МЕДЬ (лат. Cuprum-от
назв. о. Кипр, где в древности добывали медную руду) Сu, хим. элемент I гр.
периодич. системы, ат. н. 29, ат. м. 63,546. Прир. М. состоит из смеси двух
стабильных изотопов 63Сu (69,09%) и 65Сu (30,91%). Поперечное
сечение захвата тепловых нейтронов для прир. смеси 3,77.10-28
м2. Конфигурация внеш. электронной оболочки атома 3d104s1;
степени окисления + 1, +2, редко +3, + 4; энергии ионизации Сu0 Сu+ Сu2
+ Сu3+
соотв. равны 7,7264, 20,2921, 36,83 эВ; сродство к электрону 1,8 эВ; электроотрицательность
по Полингу 1,9; атомный радиус 0,128 нм, ионные радиусы (в скобках указаны координац.
числа) Сu+ 0,060 нм (2), 0,074 нм (4), 0,091 нм (6), Сu2+ 0,071
нм (2), 0,079 нм (5), 0,087 нм (6); работа выхода электрона 4,36 эВ.
Содержание М. в земной
коре (4,7.5,5).10-3% по массе. Для М. характерны
месторождения гидротермального происхождения. В морской воде содержание М. 3.10-7%
по массе, в речной —1.10-7%; ионы М., поступающие в бассейны
морей и океанов, сорбируются донными отложениями, поэтому содержание М. в них
достигает 5,7.10-3%. Ионы М. участвуют во многих физиол.
процессах, среднее содержание М. в живых организмах 2.10-4%
по массе, в крови человека ок. 0,001 мг/л.
В земной коре М. встречается
в осн. в виде соед. с S (св. 90% мировых запасов и добычи М.) и в виде кислородсодержащих
соединений. Среди многочисл. минералов М. (более 250) наиб. важны: халькопирит
CuFeS2, ковеллин CuS, халькозин Cu2S, борнит Cu5FeS4,
куприт Сu2О, малахит CuCO3.Cu(OH)2,
хризоколла CuSiO3.2H2O др. Редко встречается
самородная М. Медные руды по минера-логич. составу м. б. подразделены на сульфидные,
оксидные и смешанные (30-40% Си в форме оксидных минералов). По текстурным особенностям
различают медные руды массивные, или сплошные (колчеданные, медно-никелевые,
по-лиметаллич.), и прожилково-вкрапленные (медистые песчаники и сланцы). Медные
руды полиметаллич., помимо М., они содержат Fe, Zn, Pb, Ni, Au, Ag, Mo, Re,
Se, Fe, платиновые металлы и др. Осн. мировые запасы М. (кроме СССР) сосредоточены
в Сев. Америке (США, Канада, Мексика)-32%, Юж. Америке (Чили, Перу)-30%, Африке
(Замбия, Заир)-15%. Мировые запасы медных руд (без СССР) составляют 847,6 млн.
т, в т. ч. доказанные 447,4 млн. т.
Свойства. М.-пластичный,
розовато-красный металл с характерным металлич. блеском, тонкие пленки М. при
просвечивании-зеленовато-голубого цвета. Кристаллич. решетка
гранецентрированная кубич., а = 0,36150 нм, 2 = 4, пространств. группа
FтЗт. Т. пл. 1083,4 0С, т. кип. 2567 °С; плотн.
8,92 г/см3, жидкой при 1100 0С-8,36 г/см3,
при 200°С-8,32 г/см3, рентгеновская плотн. 8,9331 г/см3;
C0р 24,44 ДжДмоль • К), ур-ние температурной
зависимости в интервале 248-1356,9 К: С0р =
4,187(5,41 + 1,4.7.10-3 Т)ДжДмоль.К);
DH0пл 13,02 кДж/моль, скрытая DHпл
205 кДж/молъ, DH0исп 304,8 кДж/моль; S0298
33,15 ДжДмоль.К); ур-ние температурной зависимости давления пара
над жидкой М.: lgp(Па) = -17650/T + 1 l,27.l,273lg
Т (1356,9-2870 К). Даже при 1900 К давление пара над М. не превышает
133,32 Па. Температурный коэф. линейного расширения 1,7.10-5
К-1 (273-323 К), ур-ние температурной зависимости линейного расширения:
lt = l0(1 + 1,67.10-5t
+ + 3,8.10-9t2 + 1,5.10-12t3)
м, где l0-длина образца при 25 °С; объемная усадка при
кристаллизации-4,1%. Наиб. важные и широко используемые св-ва М.-ее высокая
теплопроводность и малое электрич. сопротивление:

Температурный коэф. r 4,3-10~3
К-1 (273-373 К). М. диамагнитна, уд. магн. восприимчивость -0,66.10-6.
Для жидкой М. у (в мН/м): 1120 (1413 К), 1160 (1473 К), 1226 (1573 К); h (в
мПа.с): 4,0 (1356,9 К), 8,6 (1373 К), 3,41 (1418 К).
М.-мягкий, ковкий металл;
твердость по Моосу 3,0; твердость по Бринеллю 370-420 МПа; sраст
220 МПа; относит. удлинение 60%, относит. уменьшение поперечного сечения 70%;
модуль продольной упругости 112 ГПа; модуль сдвига 49,25 ГПа; коэф. Пуассона
0,34. После обработки давлением в связи с наклепом предел прочности М. возрастает
до 400-450 МПа, уменьшаются на 1-3% удлинение и электрич. проводимость; последствия
наклепа устраняются после отжига металла при 900-1000 К. Под действием нейтронного
облучения (373 К, поток 5.1019 n/см2)
предел текучести М. возрастает почти в 2,7 раза, сопротивление разрыву-в 1,26
раза, удлинение уменьшается в 1,35 раза. Небольшие примеси Bi, Pb вызывают красноломкость
М., S, О2 - хладноломкость, примеси Р, As, Al, Fe заметно уменьшают
электрич. проводимость М.
М. растворяет Н2,
к-рый существенно ухудшает ее мех. св-ва ("водородная болезнь").
Р-римость Н2 при 0,1 МПа (в см3 на 1 кг М.):

Стандартный электродный
потенциал для р-ции Сu2+ + + 2е Сu
равен 0,339 В, для р-ции Cu+ + e Сu
0,515 В. Хим. активность М. невелика. В сухом воздухе при комнатной т-ре М.
почти не окисляется. При нагр. тускнеет из-за образования пленки меди оксидов.
Заметное взаимод. с О2 воздуха
начинается ок. 200 °С по схеме: Сu Сu2О СuО.
Сначала при т-ре до 377 °С образуется Сu2О, а выше 377 °С-
двухслойная окалина, внутр. слой к-рой состоит из Сu2О, внешний-из
СuО. Во влажном воздухе в присут. СО2 на пов-сти М. образуется зеленоватая
пленка Cu(OH)2 x х СuСО3, в присут. SO2-пленка
CuSO4 • 3Cu(OH)2, в среде H2S-черная пленка
сульфида CuS.
М. не реагирует с Н2,
N2, С, Si. При пропускании NH3 над раскаленной М. образуется
Cu3N, в аналогичных условиях при контакте с парами S, Se, H2S,
оксидами азота на пов-сти М. образуются соотв. сульфиды, селениды, оксиды. При
сплавлении с S М. дает Cu2S, с Se и Те -соотв. селениды и теллуриды.
М. активно реагирует с галогенами, образуя соответствующие соли (см. Меди
хлориды). С соляной к-той, разб. H2SO4, СН3СООН
M. взаимод. только в присут. окислителей, образуя соответствующие соли Cu(II).
В HNO3
М. раств. с образованием
Cu(NO3)2 и оксидов азота, в горячей конц. H2SO4-c
образованием CuSO4 и SO2 ,в конц. р-рах цианидов - давая
комплекс состава [Cu(CN)2]-.
Соли Cu(I) бесцв., практически
не раств. в воде, легко окисляются; Cu(I) склонна к диспропорционированию: 2Cu+
Cu2+
+ Сu0. Соли Cu(II), напротив, хорошо раств. в воде, в разб. р-рах
полностью диссоциированы. Аквака-тионы [Сu(Н2О)4]2
+ придают водному р-ру голубой цвет. При введении NaOH в р-ры солей
Cu(II) сначала выпадает Сu(ОН)2 (см. Меди гидроксиды), а
в очень конц. р-рах NaOH образуется Na2[Cu(OH)4].
В р-рах соед. Cu(II) при действии Na2CO3 или К2СО3
осаждаются основные карбонаты mCuCO3.Cu(OH)2
(см. Меди карбонаты), при избытке оса-дителя они раств. с образованием
комплексов, напр. К2[Сu(СО3)2].ЗН2О.
При обработке аммиачных р-ров солей М. ацетиленом получают карбид СuС2.
Ионы М. количественно восстанавливаются до металла др. более электроотрицат.
металлами.
Соли Cu(I) и Cu(II) с рядом
молекул и ионов (NH3, CN-, Сl- и др.) образуют
устойчивые комплексные соед., напр. (NH4)2[CuBr3],
K3[Cu(CN)4], K2[CuCl4], аммиакаты;
коор-динац. числа для Сu(I)-2, 3, 4, для Сu(II)-3, 4, 6. Путем образования комплексных
соед. можно перевести в р-р многие нерастворимые соли М. Известны соед. Cu(III)-
неустойчивые, сильные окислители, примеры-KCuO2, K3[CuF6].
Наиб. важным соед. М. посвящены отдельные статьи, см., напр., Меди ацетаты,
Меди нитрат, Меди сульфат, Медь-органические соединения.
Получение. Осн.
сырье для получения М.-сульфидные, реже-смешанные руды. Большое значение приобретает
переработка вторичного сырья, из к-рого в ряде развитых стран получают до 30-60%
производимой М. В связи с невысоким содержанием М. в рудах (0,5-1,2%) и их много-компонентностью
руды подвергают флотационному обогащению, получая попутно, помимо медного, и
др. концентраты, напр. цинковый, никелевый, молибденовый, пиритный, свинцовый.
Содержание М. в медных концентратах достигает 18-45%.
Осн. кол-во М. (85-88%)
получают по пирометаллургич. схемам, к-рые, как правило, включают след. последовательные
стадии: обжиг концентрата, плавку, конвертирование, рафинирование. Обжиг проводят
при переработке высокосернистых и полиметаллич. концентратов. При обжиге удаляют
избыточное кол-во S в форме газов, содержащих 5-8% SO2 и используемых
для произ-ва H2SO4, и переводят часть примесей (Fe, Zn,
As, Pb и др.) в формы, переходящие при послед. плавке в шлак. Обжиг проводят
в печах "кипящего слоя" с применением дутья, обогащенного О2
(24-26% О2), без затрат углеродистого топлива. Продукт обжига - огарок
-плавят в печах отражательного типа, реже - электропечах. Богатые М. руды плавили
в шахтных печах, в настоящее время этот способ имеет подчиненное значение. Перечисл.
способы плавки связаны с расходом (10-18% от массы шихты) углеродистого топлива
(прир. газ, мазут, кокс) или электроэнергии (350-450 кВт.ч на 1 т
шихты).
В процессе плавки образуются
2 жидкие фазы-сплав сульфидов М., Fe, цветных металлов (штейн; 22-45% Сu) и
сплав оксидов металлов и силикатов (шлак; 0,4-0,7% Сu), к-рые не смешиваются
друг с другом. Шлаки складируют или используют при произ-ве строит. материалов.
Осваиваются автогенные процессы плавки, использующие тепло экзотермич. р-ций
окисления сульфидов; концентраты обрабатывают в атмосфере О2, воздуха,
обогащенного О2, или подогретого воздуха. Высокая производительность,
получение богатых М. штейнов (до 75% Сu) и концентрированных по SO2
газов, миним. расход углеродистого топлива-достоинства, определяющие автогенные
процессы как перспективное направление в развитии пирометаллургии М. Важнейшие
способы автогенной плавки-кислородно-факельная, взвешенная, отражательная, электроплавка,
плавка в жидкой ванне, процессы "Норанда", "Мицубиси".
Расплав штейна (в осн.
Cu2S • FeS) направляют на кон-вертирование - продувку сжатым воздухом
с целью количеств.
окисления FeS и его ошлакования в присут. кварцевого флюса (первая стадия процесса),
окисления Cu2S и макс. удаления S и большинства примесей (вторая
стадия):
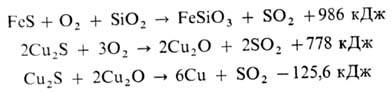
При конвертировании используют
тепло экзотермических р-ций окисления, конечный продукт-черновая М. (98,5-99,3%
Сu).
Черновую М. рафинируют
огневым, а затем электрохим. способом. Огневое рафинирование основано на большем,
чем у М., сродстве большинства металлов-примесей к кислороду, что позволяет
при продувке расплава воздухом окислить и ошлаковать количественно Fe, S, Zn,
Pb и, частично, Ni, As, Sb, Bi. Для удаления кислорода расплав М. обрабатывают
восстановителем (прир. конверсир. газ, сырая древесина). Готовый металл (>=99,5%
Сu) разливают в формы, удобные для проведения электролиза. Полученные отливки
служат анодами. Электролитич. рафинирование проводят в сернокислых р-рах при
наложении постоянного тока; в процессе электролиза осуществляется непрерывная
циркуляция подогреваемого (57-67°С) р-ра, М. осаждают на катодных основах,
получаемых также электролизом в спец. матричных ваннах при условиях, обеспечивающих
осаждение чистого металла. Для получения ровного катодного осадка требуемой
текстуры в электролит вводят ПАВ. Катодную М. (>=99,94% Сu) переплавляют
и разливают в формы, удобные для послед. обработки прокаткой, волочением. При
растворении анодов ряд примесей (As, Fe, Ni, Sb) накапливается в электролите,
поэтому часть его выводят из циркуляц. цикла (заменяя равным объемом р-ра H2SO4)
и направляют на переработку для получения техн. сортов медного и никелевого
купоросов. Нерастворимые включения анода образуют дисперсный продукт - шлам,
в к-ром концентрируются благородные и редкие металлы. Этот продукт специально
перерабатывают в шламовом цикле. Анодные остатки (выход их 15-18% от массы анода)
возвращают на переплавку в цикл огневого рафинирования.
При пирометаллургич. переработке
медного концентрата извлекают до 96-98% М. и благородных металлов, однако степень
извлечения сопутствующих элементов (S, Zn, Ni, Pb) гораздо ниже, a Fe полностью
теряется со шлаком.
Многие проблемы пирометаллургич.
произ-ва М. (экологическая из-за повыш. тепло-, пыле- и газовыделения, взры-воопасность
в случае контакта расплава штейна с водой и др.) устраняются при использовании
гидрометаллургич. технологии. Она включает: селективное выщелачивание М. из
сырья, чаще всего р-ром H2SO4 или NH3; очистку
р-ра от примесей и извлечение сопутствующих ценных элементов (Zn, Co, Ni, Cd
и др.); выделение М. При переработке бедных р-ров (0,5-12,0 г/л М.) используют
цементацию на железном скрапе и экстракцию с послед. электрохим. осаждением
М. Из богатых р-ров (30-40 г/л М.) М. извлекают чаще электролизом или автоклавным
осаждением водородом (127-197 °С, давление Н2 1,5-2,5 МПа). В
последнем случае М. получают в форме порошка (>=99,6% М.). Гидрометаллургич.
схемы эффективны при извлечении М. из бедных руд методами подземного, кучного,
чанового выщелачивания, в т. ч. с использованием биохим. окисления сульфидов;
остатки от выщелачивания смешанных руд обогащают флотацией. Рациональна переработка
полиметаллич. концентратов, вторичного сырья, особенно при небольшом объеме
произ-ва. В этом случае весьма перспективно автоклавное выщелачивание при повыш.
т-рах (137-197 °С) и давлении кислородсодержащего газа-окислителя (давление
О2 0,2-1,0 МПа), обеспечивающее значит. интенсификацию процесса,
получение более чистых р-ров и элементной S при окислении сульфидов. Гидрометаллургич.
схемы позволяют более комплексно использовать сырье, проще обеспечить экологич.
и пром. санитарию. Внедрение их сдерживается из-за
недостаточной интенсивности, повыш. эксплуатац. затрат и др.
Определение. Соед.
М. в смеси с содой и углем в пламени горелки образуют красный металлич. королек,
р-римый в HNO3. Р-ры, содержащие ионы Сu2+ , при добавлении
NH3 приобретают синюю окраску (чувствительность 0,007 мг/л); при
добавлении K4[Fe(CN)6] выпадает красно-коричневый осадок
(чувствительность 0,0001 мг/л); при взаимод. с Na2S или (NH4)2S
образуется черный осадок CuS. Для количеств. определения М. используют гравиметрич.,
объемный, комплексонометрич., амперометрич., кондуктометрич., по-лярографич.,
потенциометрич., радиоактивац., эмиссионный, спектральный методы анализа. При
повыш. содержании М. ее определяют объемным иодометрич. или более точным электрогравиметрич.
методом. Для определения малых кол-в М. используют фотометрич. метод с дити-зоном,
купфероном, диэтилдитиокарбаматом Na (чувствительность 0,02-0,002 мг/л), атомно-абсорбционный
(кислородно-водородное пламя, l = 324,7 нм, чувствительность 0,01-0,0015 мг/л).
При определении содержания М. в сточных водах дополнительно используют флуоресцентный
(чувствительность 0,002 мг/л), спектральный (0,002-0,003 мг/л), хроматографич.
(0,07 мг/л) методы анализа.
Применение. Широкое
применение М. в пром-сти обусловлено рядом ее ценных св-в и прежде всего высокой
электрич. проводимостью, пластичностью, теплопроводностью. Более 50% М. используется
для изготовления проводов, кабелей, шин, токопроводящих частей электрич. установок.
Из М. изготовляют теплообменную аппаратуру (вакуум-испарители, подогреватели,
холодильники). Более 30% М. применяют в виде сплавов, важнейшие из к-рых - бронзы,
латуни, мельхиор и др. (см. Меди сплавы). М. и ее сплавы используют
также для изготовления художеств. изделий. В виде фольги М. применяют в радиоэлектронике.
Значит. кол-во М. (10-12%) применяют в виде разл. соед. в медицине (антисептич.
и вяжущие ср-ва), для изготовления инсектофунгицидов, в качестве медных удобрений,
пигментов, катализаторов, в гальванотехнике и т.д.
Мировое произ-во М. (без
СССР) ок. 7,5 млн. т, в т.ч. из вторичного сырья-1,15 млн. т/год (1985). Осн.
страны-производители рафинированной М. (1985): США (1,7 млн. т), Япония (1,1),
Чили (0,9), Канада (0,8), Замбия (0,53), Заир (0,5).
Все соли М. ядовиты; раздражают
слизистые, поражают желудочно-кишечный тракт, вызывают тошноту, рвоту, заболевание
печени и др. При вдыхании пыли М. развивается хронич. отравление. ПДК для аэрозолей
М. 1 мг/м3, питьевой воды 1,0 мг/л, для рыбных водоемов 0,01 мг/л,
в сточных водах до биол. очистки 0,5 мг/л.
М. известна человечеству
с глубокой древности. М. и ее сплавы сыграли заметную роль в развитии цивилизации.
=== Исп. литература для статьи «МЕДЬ»: Набойченко
С. С., Смирнов В. И., Гидрометаллургия меди, М., 1974; Металлургия меди, никеля,
кобальта, 2 изд., ч. 1, М., 1977; Онаев И. А., Жакибаев Б. К., Медь в истории
цивилизации, А.-А., 1983; Ванюков А. В., Уткин Н. И., Комплексная переработка
медного и никелевого сырья, М., 1988; Ванюков А. В. [и др.], Плавка в жидкой
ванне, М., 1988; Подчайно-ва В.Н., Симонова Л.Н., Медь, М., 1990. С. С. Набойченко.
Страница «МЕДЬ» подготовлена по материалам химической энциклопедии.
|