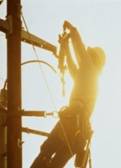
Трудности энергосбережения для предприятий бывшего СССР особо актуальны по сегодняшний день, поскольку рыночные механизмы в экономике отсутствовали, то это привело к тому, что энергоемкость их производств значительно выше промышленно развитых стран. Поэтому, в России на производство продукции в химической и нефтехимической промышленности используется энергии на 30-60% выше, чем в аналогичных зарубежных производствах. А в азотной промышленности энергозатраты выше зарубежных на приблизительно 35%. Сегодня уделяется достаточно большое внимание теории и практике химической энерготехнологии с детальным анализом отдельных производств и процессов, методы энергосбережения постепенно внедряются в практику промышленных предприятий. Также, трудности энергосбережения и пути их разрешения имеют примерно одинаковый характер для предприятий со схожей структурой производств. На больших предприятиях, занимающихся азотной промышленностью, в большинстве случаев, имеется избыточный пар низких параметров, образующийся в технологических процессах, отработанный низкопотенциальный пар с турбоприводов, потоки конденсата и органических продуктов, имеющих высокую температуру, уничтожение тепла которых затруднена из-за невозможности его использования напрямую в технологии. Достаточно большое количество тепла количество тепла уходит с отходящими дымовыми газами печей риформинга природного газа, при дросселировании пара до технологически необходимых параметров и так далее. Благодаря этому крайне интересно рассмотрение нескольких общих подходов при решении проблем энергосбережения, не требующих значительных перемен в технологии и больших капитальных вложений. По результатам проведения опыта многолетней совместной работы одной купной компании по переработке азота с ОАО ГИАП (г. Москва), лабораторией термодинамики органических веществ НИИ физико-химических проблем Белгосуниверситета (г.Минск), НПО ЦКТИ (г. С.Петербург) можно заметить наиболее эффективные с точки зрения сроков окупаемости затрат направления: 1. Применение паро-струйных компрессоров для утилизации низкопотенциального пара Для решения проблемы утилизации низкопотенциального пара самым простым и эффективным способом является повышение его давления до технологически приемлемых параметров с помощью паро-струйных компрессоров, методы расчета ко¬торых разработаны хорошими специалистами. При завершении процесса инжекции за счет энергии пара более высоких параметров повышается давление инжектируемого пара и также есть возможность повысить его температуру до требуемого значения, что очень важно если утилизируемый пар является насыщенным. Используемый нами метод утилизации низкопотенциального пара имеет ряд преимуществ перед остальными способами из-за низких затрат и очень простой конструкции применяемого оборудования, которое можно изготовить при помощи сил ремонтно-механических цехов предприятий. Мы решили проблемы утилизации благодаря применению пара-струйных компрессоров низко-потенциального пара с турбоприводов компрессоров в аммиачных производствах, избыточного технологического пара в производствах карбамида. Таким образом видим реализацию схемы использования тепла горячего конденсата с предварительным получением пара повторного вскипания, его следующим компремированием и выдачей в заводскую сеть, а также насыщенного низкопотенциального пара от теплоутилизационных установок. 2. Комбинированная выработка электроэнергии и теплоты на теплоэнергетическом оборудовании Развитая система редукционно-охладительных установок, как правило, существует в энергоемких химических производствах, потребляющих в больших количествах пар. Пар высокого давления редуцируется до технологически необходимых параметров, а также для собственных нужд котельной, отопления и так далее с большими теплопотерями. Основная экономия энергоресурсов происходит при установке паровых турбин с максимально возможной выработкой электроэнергии, при этом питание главных потребителей пара осуществляется из отборов турбины, в минимальной степени предусматривая работу РОУ. |