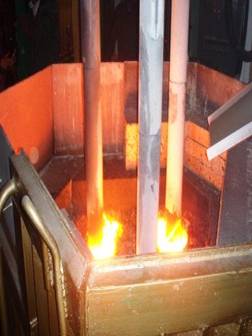
Известно, что базальтовые волокна имеют достаточно высокие характеристики по прочности, химической стойкости, обладают высокой стойкостью к воздействию кислот и особенно щелочей, термической стойкостью, негорючестью [1]. По своим характеристикам НБВ занимают промежуточное положение между стекловолокнами и углеродными волокнами. Сравнительные характеристики волокон представлены в таблице 1. Таблица 1.
Capability | CBF (continuesbasalt fiber) | E-glass fiber | S-glass fiber | Carbon fiber | Aramidfiber | Tensilestrength, mPa | 3000 ~ 4840 | 3100 ~ 3800 | 4020 ~ 4650 | 3500 ~ 6000 | 2900~ 3400 | Elastic modulus, gPa | 79.3 ~ 93.1 | 72.5 ~ 75.5 | 83 ~ 86 | 230 ~ 600 | 70 ~ 140 | Elongation at break, % | 3.1 | 4.7 | 5.3 | 1.5~2.0 | 2.8 ~ 3.6 | Diameter of filament, mµ | 6 ~ 21 | 6 ~ 21 | 6 ~ 21 | 5 ~ 15 | 6 ~ 15 | Tex | 60 ~ 4200 | 40 ~ 4200 | 400 ~ 4200 | 600 - 2400 | 600 - 1800 | Temperature of application, 0C | -260 ~ +500 | -50 ~ +380 | -50 +300 | -50 ~ +700 | -50 ~ +290 | Price, USD/kg | 2,5 – 3.0 | 1,1 – 1.4 | 2,5 – 3.5 | 25 - 50 | 25 |
Наибольше распространение для производства композиционных материалов получило стекловолокно. История промышленного производства стекловолокна составляет 60 лет. Производство стекловолокна начиналось с 50–ти фильерных питателей, затем применяли 200, 400, 600, 800, 1200 и 2000 фильерные питатели. Применяли двухстадийную технологию производства (шихта – шарики – волокно) и одностадийную технологию (шихта – волокно). По мере освоения производства происходил существенный рост объемов производства стекловолокна, а соответственно снижалась себестоимость производства. Объемы производства современных заводов по производству стекловолокна составляют до 100 тонн в сутки. В настоящее время объемы производства стекловолокна достигли 2200 - 2500 тысяч тонн в год. Ежегодный рост объемов производства стекловолокна за последние 10 – 15 лет составляет 8 – 10%. Факторы, определяющие рост объемов производства и применения стекловолокна: снижение себестоимости производства; широкое применение композиционных материалов во всех отраслях промышленности; замена традиционных материалов из металла на композиционные. Углеродные волокна до недавнего времени считались экзотическими из-за своих уникально высоких прочностных характеристик и стоимости. Поэтому находили применение при производстве военной техники, где традиционно применяются и в настоящее время. Углеродные волокна входят в перечень стратегических товаров. Однако материалы из углеродных волокон (углепластики) начали широко и активно применяться при производстве товаров широкого применения. Например, спортивного инвентаря (ракетки, лыжные палки, детали для спортивных автомобилей и мотоциклов и т.д.), но и при производстве рыболовных удочек, зонтиков и других массовых товаров. История освоения промышленного производства НБВ составляет 20 лет. Первые исследования возможностей производства базальтовых волокон были начаты в Советском Союзе, в начале 60-х годов были получены первые образцы НБВ. Затем последовали длительные исследования характеристик базальтовых волокон и материалов, разработанных на их основе. Промышленные технологии и оборудование для производства НБВ были запушены к средине 80-х годов. Промышленное производство начато в 1985 году на Украине. В 90-х годах НБВ производилось уже на двух предприятиях: Беличанском заводе «Теплозвукоизоляция» и ОАО «Судогодское стекловолокно». Однако, эти технологии очень энергоемкие, а оборудование достаточно сложное и дорогое. Себестоимость производства НБВ относительно высока, даже при условиях низкой стоимости энергоносителей. В конце 90-х годов были разработаны новая технология и принципиально новое технологическое оборудование для производства НБВ, позволившие значительно в 2 - 2.5 раза снизить расходы энергоносителей и соответственно снизить себестоимость производства НБВ. Себестоимость производства НБВ стала сопоставимой с себестоимостью производства стекловолокна. Эти разработки дали новый импульс в развитии производства базальтовых волокон и позволили существенно расширить потенциальный рынок их применения. На основе новых технологий в 2000 году построено самое крупное в мире предприятие по производству НБВ. Вся продукция предприятия используется для производства материалов для автомобильной компании «TOYOTA». Строятся и уже запущены еще несколько заводов по производству НБВ. Следующим шагом стали разработки промышленных установок НБВ серии BCF. Установки BCF -1G, BCF-1GМ, BCF-2G, BCF-2GМ с пониженным потреблением энергоносителей были построены и запущены в Китае специалистами «BF&CM TD» при выполнении программы Министерства технологии и науки КНР «Непрерывные базальтовые волокна и композиционные материалы на их основе» [1]. Сравнительные характеристики технологий и технологического оборудования для производства НБВ представлены в таблице 2. Тип технологии и оборудования Диаметр элементарных нитей НБВ, d (мкм). | Удельный расход на производство 1 kg НБВ, | Природный газ, m3 | Э/энергияkWt h | Масса бобины первичной нити (g) | Масса ФП (g),К-во фильер | Фидерная печь (d = 9 - 13 мкм) | 3.1 – 3.2 | 9.3 | 700 - 900 | 3200, (200 ф) | Модульная НБВ – 10 (d = 15 - 17 мкм) | 1.0 – 1.1 | 6.0 | 1000 - 1300 | 1800, (200 ф) | Модульная BCF-1G (d = 10 - 12 мкм) | 0.9 | 2.8 | 2500 - 3500 | 1650, (200 ф) | Модульная BCF-1GМ (d = 10 - 13 мкм) | 0.65 | 1.5 | 2500 - 3500 | 1680, (266 ф) | Модульная BCF-2GМ (d = 10 - 13 мкм) | 0.6 | 1.2 | 3000 - 3500 | 1680, (266 ф) |
|