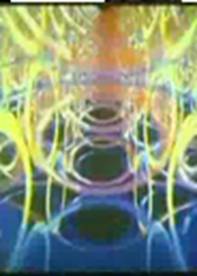
Нефть является единственным глобальным сырьем для производства моторных топлив и важнейшим - для химического синтеза. Однако постепенно ситуация изменяется. Исчерпание мировых запасов нефти вынуждает обратиться к другим источникам углеводородного сырья, наиболее значительными из которых являются уголь и природный газ. Извлекаемые запасы газа в энергетическом эквиваленте превышают нефтяные в 1,5 раза, запасы угля - более чем в 20 раз [2, 3]. По экспертным оценкам, к 2015 г. доля нефти в мировом энергетическом балансе будет составлять 38 %, природного газа - 26 %, угля - 25 % [4]. Первой стадией превращения природного газа и угля в химические продуты и жидкие топлива является их конверсия в синтез-газ -смесь СО и Н2. Далее основные направления переработки синтез-газа выглядят следующим образом: • синтез метанола; • производство аммиака; • оксо-синтез и формилирование ароматических соединений; • карбонилирование метанола в уксусную кислоту; • карбоксилирование олефинов; • синтез Фишера-Тропша (ФТ). Надо отметить, что получение синтез-газа (паровой конверсией или парциальным окислением метана, газификацией угля) является наиболее дорогой составляющей всего производства. Капитальные затраты на секцию синтез-газа в строительстве завода по получению метанола из природного газа или углеводородов по технологии ФТ из угля составляют 60-70 % [5-7]. Синтез Фишера-Тропша (ФТ) представляет собой сложную совокупность последовательных и параллельных превращений, протекающих на поверхности гетерогенного катализатора. Основными являются реакции гидрополимеризации СО с образованием парафинов и олефинов: nCO + 2nH2 CnH2n + H2O, nCO + (2n + 1)H2 н> CnH2n + 2 + H2O. В присутствии железных катализаторов образуются также значимые количества оксигенатов - спиртов, альдегидов, кетонов и карбоновых кислот. При повышенных температурах в присутствии цеолитных сокатализаторов образуются ароматические соединения. Побочные реакции - прямое гидрирование СО в метан, диспропорционирование СО (реакция Белла-Будуара) и реакция водяного газа, интенсивно протекающая на железных катализаторах: CO + 3H2 - CH4 + H2O, 2CO - C + CO2, CO + H2O - CO2 + H2. Максимальный теоретически возможный выход углеводородов из 1 нм3 синтез-газа состава СО:Н2 = 1:2 составляет 208 г. В условиях синтеза ФТ термодинамические вероятности образования продуктов выглядят следующим образом [8]: • метан > алканы > алкены > О-содержащие; • низкомолекулярные н-алканы > высокомолекулярные н-алканы; - высокомолекулярные н-олефины > низкомолекулярные н-олефины. В действительности выход метана на хороших катализаторах синтеза ФТ не превышает 8 %. Молекулярно-массовое распределение диктуется кинетикой полимеризации (см. ниже). Таким образом, синтез ФТ является кинетически контролируемым процессом, состав конечных продуктов далек от равновесного. Синтез ФТ - сильно экзотермический процесс. Тепловой эффект реакции гидрополимеризации СО составляет 165 кДж/моль СО, тепловой эффект прямого гидрирования еще выше - 215 кДж/моль. Отвод большого количества тепла в ходе синтеза представляет собой важнейшую проблему при проектировании промышленных установок синтеза ФТ. Катализаторами реакции являются металлы VIII группы. Наибольшую каталитическую активность проявляют Ru, Fe, Co, Ni. Рутений активен уже при 100 °С, в его присутствии при повышенном давлении образуются парафины очень высокой молекулярной массы (полиметилен). Однако этот металл слишком редок и дорог, чтобы рассматриваться в качестве промышленного катализатора. Никелевые контакты при атмосферном давлении обеспечивают в основном прямое гидрирование СО в метан. При повышенном же давлении легко образуется летучий Ni(CO)4, так что катализатор вымывается из реактора. В силу этих причин коммерчески использовались только железные и кобальтовые каталитические системы. Кобальтовые катализаторы были первыми катализаторами, используемыми в промышленности (в Германии, а затем во Франции и Японии в 1930-1940-е годы) [8]. Типичными для их работы являются давление 1-50 атм и температура 180-250 °С. В этих условиях образуются, главным образом, линейные парафины. Кобальт обладает значительной гидрирующей активностью, поэтому часть СО неизбежно превращается в метан. Эта реакция резко ускоряется с повышением температуры, поэтому кобальтовые катализаторы не могут использоваться в высокотемпературном процессе ФТ. По последним данным, удельная активность кобальтовых катализаторов выше, чем железных [9]. Железные катализаторы с середины 1950-х годов используются на заводах синтеза ФТ в ЮАР [8, 10]. По сравнению с кобальтовыми они гораздо более дешевы, работают в более широком интервале температур (200-360 °С), и позволяют получать более широкий спектр продуктов: парафины, низшие α-олефины, спирты. В условиях синтеза ФТ железо катализирует реакцию водяного газа, что позволяет эффективно использовать получаемый из угля синтез-газ, в котором соотношение СО:Н2 ниже стехиометрического 1:2. Железные катализаторы имеют более низкое сродство к водороду по сравнению с кобальтовыми, поэтому метанирование не является для них большой проблемой. Однако в силу той же низкой гидрирующей активности поверхность железных контактов быстро зауглероживается, и срок их службы составляет несколько недель. Кобальтовые контакты, напротив, способны работать без регенерации год и более. Еще одним недостатком железных контактов является их ингибирование водой. Поскольку вода является продуктом синтеза, кинетика процесса для железных катализаторов неблагоприятна, конверсия СО за один проход невысока. Для достижения высокой степени превращения необходимо организовывать рецикл газа [3]. И железные, и кобальтовые катализаторы крайне чувствительны к отравлению серой. Поэтому синтез-газ должен быть предварительно очищен от серы, по крайней мере, до уровня 2 мг/м3 [11]. Остаточная сера адсорбируется поверхностью катализатора, так что в итоге продукты синтеза ФТ практически ее не содержат. Это обстоятельство делает синтетическое дизтопливо, полученное по технологии ФТ, весьма привлекательным ввиду современных жестких экологических требований к транспорту. В синтезе ФТ образуется широкая углеводородная фракция (рис. 1). 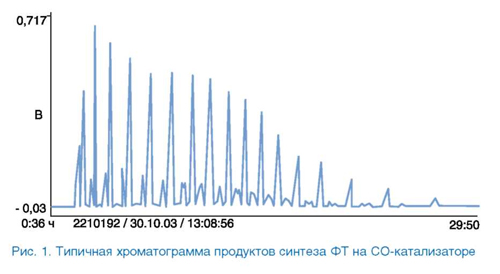
Распределение продуктов подчиняется кинетике полимеризации, и доля индивидуальных углеводородов удовлетворяет распределению Андерсона-Шульца-Флори (ASF): pn = п-(1 - α)2- α n-1, где n - углеродный номер; α - параметр распределения, имеющий физический смысл соотношения между константами скорости роста и обрыва цепи или, иными словами, вероятности роста цепи (рис. 2). Величина α определяется природой катализатора, температурой и давлением процесса. Для каждого класса продуктов, одновременно образующихся на одном и том же контакте (парафины, олефины, спирты), величина а может быть различной. Иногда наблюдается 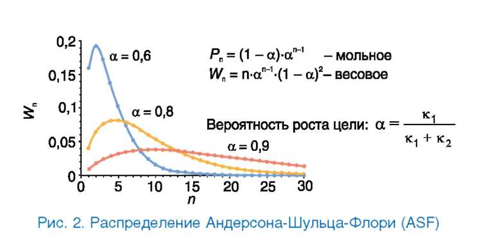
• включением низших олефинов в растущую цепь; • крекингом высших парафинов; - присутствием на поверхности двух и более видов центров полимеризации, каждый из которых обеспечивает свое значение α. Распределение ASF накладывает ограничение на селективность процесса в отношении индивидуальных углеводородов и их узких фракций. Так, выход бензиновой фракции С5-С10 не может превысить 48%, дизельной фракции С11-С18 - 30%. Однако селективность в отношении твердых парафинов монотонно растет с повышением α и асимптотически приближается к 100 % (рис. 3). Если полученные парафины подвергнуть мягкому гидрокрекингу, выход фракции газойля можно довести до 60 % на прореагировавшее сырье [12].
|