Ультрафиолетовые покрытия, не содержащие мономеров на водяной основе Можно улучшить устойчивость к воздействию многих термопластических дисперсионных полимеров с помощью добавления акрилатных разбавителей с ультрафиолетовым отверждением, таких как триметилолпропантриакрилат, перед нанесением, с последующим ультрафиолетовым отверждением. Тем не менее, это не дает сшивания первичного связывающего вещества, и существует определенный риск, что акрилатный мономер вызовет раздражение кожи или повышение чувствительности во время или после нанесения. Значительно более удобным походом является включение мономера с ультрафиолетовым отверждением непосредственно в сам эмульсионный полимер. К числу известных способов реализации такого включения относятся: - образование изоцианат-функционального преполимера и проведение реакции преполимера с, например, гидроксиэтилакрилатом до эмульгации; - производство кислотно-функционального акрильного полимера с помощью нормальной технологии эмульсионной полимеризации, придавая растворимость за счет добавления основания, а затем добавление и осуществление реакции в каком-либо материале, таком как глицидилметакрилат для придания функциональности ультрафиолетового отверждения. Преимуществом использования более твердого акрилового полимера поверх полиуретанов является то, что основные покрытия достаточно твердые для того, чтобы быть достаточно очищенными в состоянии физической сухости, и их надо только подвергнуть ультрафиолетовому отверждению после нанесения поверхностного покрытия. ПОЛИУРЕТАНЫ Исключение NMP На протяжении длительного времени N-метилпирролидон (NMP) использовался для производства практически всех дисперсий полиуретана на водяной основе (ПУД). При таком применении у них прекрасная растворяющая способность, они не вступают в реакцию с изоцианатами, обладают слабым запахом и полностью смешиваются с водой. Тем не менее, в настоящее время существует постоянно возрастающая озабоченность их токсичностью, и производители ПУД вынуждены были искать другие способы управления вязкостью во время реализации начальной стадии безводной полимеризации. К числу способов, которые были использованы для исключения использования NMP, относится использование ацетон- или метилэтилкетона в качестве растворителя при полимеризации. Оба эти материала огнестойки с низкими температурами воспламенения, но это означает, что можно отгонять большую часть растворителя, у которого довольно хороший профиль токсичности. После того, как их заставили отказаться от их любимого растворителя, многие поставщики ПУД стали утверждать, что необходимая разработка новых рецептур дала в результате новые марки, у которых более высокие эксплуатационные характеристики по сравнению со старыми марками, и что теперь могут потребоваться более низкие концентрации сорастворителя для обеспечения коалесценции пленок. В некоторых случаях этого достигали за счет использования поликарбонатной главной цепи вместо главных цепей уже известных (более дешевых) сложного полиэфира или простого полиэфира. В области полиуретанов на водяной основе другим решением является включение полиолов, которые способствуют растворению широко используемого гидрофильного диола – диметилолпропионовой кислоты, при этом снижается необходимое количество растворителя. Этот способ позволяет производить чистый полиуретан с высокой молекулярной массой, модифицированный жирными кислотами или обладающий самосшиванием дисперсии полиуретана с очень низкими минимальными температурами образования пленки, так что можно действительно производить покрытия, не содержащие летучих органических соединений. Гибридные растворы Существует широко распространенная практика смешивания дисперсий полиуретана с акриловыми (или иными) эмульсионными смолами для производства покрытий с меньшей стоимостью, чем стоимость ПУД, но, зачастую, с лучшими свойствами. Оказалось возможным использовать акриловые мономеры в качестве растворителей для полиуретанов. После того, как будет закончена полимеризация уретана на основе растворителя и образуется дисперсия на водяной основе, акриловые мономеры полимеризуют. Получаемые в результате гибридные частицы имеют внешнюю оболочку, которая обогащается более гидрофильным уретановым материалом. Такая структура очень хороша, поскольку полиуретан, в целом, является более мягким компонентом, и с использованием точного состава рецептуры можно производить покрытия с низкими или нулевыми значениями требований коалесценции. Похожий подход включает использование вышеописанных действий в обратном порядке. Акриловые дисперсии обычно производят с помощью эмульсионной полимеризации, получая смолы с высокой молекулярной массой с быстрым физическим высушиванием. Так называемые «вторичные дисперсии» можно также производить с помощью технологии на основе растворителя, при которой получают смолы с более низкой молекулярной массой, очень малым размером частиц и сильным глянцем, но относительно высоким содержанием растворителя. Гидрокси-функциональные диолы, которые поддаются сшиванию с изоцианатами, использовались с этой технологией вместо растворителей. Это дало существенные изменения значений молекулярной массы и размера частиц полиакрилата, и наложило ограничения на состав полиуретанового компонента покрытия, но сообщается, что можно производить покрытия с твердостью и устойчивостью к воздействию химических веществ, аналогичными тем, которыми обладают полиуретаны с растворителем 2K. Концентрация ЛОС снижается с примерно 350 г/л (с высоким содержанием сухого остатка) или 150 г/л (для нормальных WB 2K PU) до примерно 20 г/л. Полиуретаны, не содержащие изоцианата, и родственные им покрытия Хотя термины «изоцианат» и «полиуретан» часто используются как взаимозаменяемые, на самом деле возможно производство полиуретановых полимеров без использования вредных изоцианатов на любом этапе производства. Заявляется, что полиуретаны, которые производятся с помощью реакции между циклокарбонатами и первичными амин олигомерами, обладают свойствами, превосходящими свойства традиционных полиуретанов. Несколько продуктов, изготавливаемые на основе этой технологии, предлагаются на рынке, некоторые можно отверждать при температурах окружающей среды. Полиуретаны, созданные подобным способом, обладают внутримолекулярными водородными связями, которые значительно повышают их устойчивость к воздействию химических веществ при сохранении аналогичных физических свойств. Тем не менее, циклокарбонаты производят из эпоксидных смол (с помощью реакции с двуокисью углерода), и многие такие материалы подвержены пожелтению под воздействием ультрафиолетовых лучей. Сообщается, что циклокарбонаты, произведенные из акриловой эпоксидной смолы и отвержденные при 110°C, имеют значительно более высокую светостойкость. Использование аминосиланов в качестве аминовых компонентов повышает устойчивость к воздействию высоких температур, и может быть распространено на производство гибридных покрытий с кремниевыми наночастицами, которые формируются прямо на месте с помощью золь-гелевой реакции. Материалы с ультрафиолетовым отверждением можно приготовить за счет включения, например, циклического карбоната глицидилметакрилата в полиуретановом преполимере. Некоторые исследователи также изучали возможность использования энзимов для катализа подходящих реакций уретанового сшивания. В Университете Центрального Ланкашира (Великобритания) продемонстрировали, что таким способом можно осуществить переэтерификацию карбаматдиолов и полиэфирных полиолов. Enichem запатентовала технологию создания ароматических уретанов с помощью переэтерификации между диолами и метил карбаматами. В области радиационного отверждения были разработаны новые двухступенчатые технологии с тем, чтобы избежать использования изоцианатов. В качестве примера можно приготовить монофункциональные уретанметакрилаты за счет реакции монофункционального или вторичного амина с монофункцинальным циклическим карбонатом. Затем продукт реакции гидроскиалкилкарбамат превращается в метакрилат за счет переэтерификации с алкилметакрилатом. Необходимо свести к минимуму некоторые побочные реакции на втором этапе. Возможно приготовление новых форм уретанметакрилата, которые невозможно произвести с использованием изоцианата. У этих продуктов заметно ниже вязкость, по сравнению с теми, которые приготовлены с помощью изоцианатных реакций, и поэтому можно уменьшить содержание реактивного разбавителя в составе вещества. Электростатические покрытия, не содержащие изоцианатов Хроматы уже удалены из большинства катодных электростатических рецептур, которые используются при нанесении грунтового покрытия на транспортные средства. Хотя это наиболее очевидно вредные для окружающей среды ингредиенты, которые используются в данной технологии, в большинстве рецептур продолжают использовать блокированные изоцианаты в качестве агентов сшивания для эпоксидных смол. Это приводит к появлению трех потенциальных проблем при отверждении: высвобождение самих изоцианатов, осаждение блокирующих агентов или продуктов их реакции, и осаждение олова (из оловоорганических веществ, которые широко применяются в качестве катализаторов полиуретана). 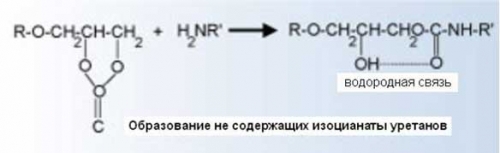 Общая схема реакции образования уретана с водородной связью из циклокарбоната и первичного алифатического амина Но существует много способов отверждения эпоксидных смол. Решением, которое исследовалось для данного конкретного применения, является изготовление смол с самосшиванием, в которых имеются как эпоксидные группы, так и группы третичного амина. Добавление подходящей кислоты [в рассматриваемой работе это муравьиная кислота] делает смолу растворимой в воде. Отверждение происходит при температурах, превышающих 180°C, а исходные испытания позволяют предположить, что эти покрытия могут обеспечивать хорошую устойчивость к коррозии и высокие физические свойства. НЕ СОДЕРЖАЩИЕ ЯДОВИТЫХ ВЕЩЕСТВ БИОЦИДНЫЕ ПОКРЫТИЯ При наличии действующего строго запрета на использование оловоорганических противообрастающих веществ, ограничений использования других биоцидных материалов и озабоченности относительно долговременного воздействия меди на морские живые организмы, существуют мощные стимулы для разработки нетоксичных противообрастающих покрытий. В целом существует два основных подхода: создание очень скользкой поверхности, к которой не могут прикрепиться обрастающие организмы (здесь также имеется преимущество снижения трения с водой), или же обеспечение использования поддающихся биологическому разложению материалов, которые будут медленно выщелачиваться из покрытий. Скользкие клиенты Фторированные или кремниевые добавки широко используются в качестве средств снижения поверхностного или межфазного натяжения в покрытиях при низких количествах введения, поскольку они легко мигрируют на поверхность во время отверждения. Покрытия этого типа очень эффективны для использования в качестве противообрастающих веществ на быстро передвигающихся судах, где поток воды позволяет выселять нежелательных постояльцев. Общее правило заключается в том, что для того, чтобы сделать эти покрытия эффективными, нужна скорость, превышающая 18 узлов, именно поэтому они используются на морских судах и быстроходных паромах. Были разработаны материалы, известные как полиэлектролитные фторотензидные комплексы (PEFT) с исключительно низким поверхностным натяжением, ниже, чем у PTFE, а некоторые компании исследуют покрытия, которые медленно выщелачивают силоксановые компаунды для того, чтобы содержать поверхность всегда свежей и активной. К числу трудностей, которые встречаются при производстве покрытий данного типа, относится способность поверхности покрытия со временем восстанавливаться. Это выражается в том, что данные измерения поверхностного натяжения, которое было произведено на только что смоченной чистой водой поверхности, могут существенно отличаться от значений, получаемых на поверхности, которая была в течение нескольких дней погружена в морскую воду. Такое изменение свойств поверхности выражается в снижении межфазового натяжения, что, в свою очередь, позволяет микроорганизмам легче прикрепляться к покрытию. Масштабы и скорость такого изменения зависят от состава покрытия, и эти параметры ниже у твердых высокосшитых покрытий. Один из вариантов подхода со снижением трения был представлен на рынок бельгийской компанией Subsea Industries, в противообрастающих покрытиях которой Ecospeed используются стеклянные чешуйки для того, чтобы обеспечить очень гладкое, жесткое и долговечное поверхностное покрытие со сроком эксплуатации до 25 лет. Коррозийную стойкость усиливает наличие множества слоев стеклянных чешуек, которые дают исключительно низкий уровень проницаемости водяных паров. Если все же будет иметь место обрастание, его можно удалить в сухом доке водяной струей высокого давления. В настоящее время покрытие используется на кораблях от быстроходных судов береговой охраны до танкеров, контейнеровозов и круизных лайнеров. 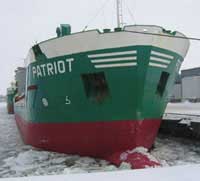 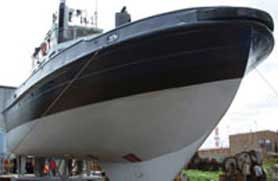
Природные биоциды Многие организмы производят природные биоциды (пенициллин был первым из открытых), и многие морские растения изучались в качестве источников полезных токсических веществ, поскольку они стремятся защитить себя от обрастания морскими организмами. Эти исследования начались еще в 1985 г. Австралийская компания Biosignal разработала линию продуктов на основе фуранонов, соединений, которые производят из австралийских красных водорослей. Фураноны препятствуют работе внутренних регулирующих систем бактерий, не допуская образования организованных биопленок на поверхностях. Компаунды способны подвергаться биологическому разложению, и у некоторых очень низкий уровень токсичности. Последний отчет об использовании данной технологии содержит подробное исследование большого количества бактерий, собранных с поверхностей водорослей, губок и других морских организмов. Было установлено, что небольшое количество таких бактерий может создавать противобактериальные компаунды, которые эффективны в борьбе с другими морскими организмами. Было установлено, что самые эффективные из этих экстрактов и биоцидов растительного происхождения, которые продаются как Tophelex, обладают сильным противообрастающим воздействием, хотя его и недостаточно для производства краски только из этих материалов. Точно так же, оказалось, что зостерическая кислота, природный компаунд, который содержится в морской траве зостере, снижает способность пресноводных бактерий к прилипанию к силоксановым покрытиям почти на 80%. Потребовался всего 1% зостерической кислоты, но повышение концентрации не сделало воздействие более эффективным, тем самым снова показывая, что это многообещающий компаунд для дальнейших исследований, но не исчерпывающее решение проблемы обрастания. Шведские исследователи рассмотрели целый ряд стандартных фармацевтических продуктов для использования их в качестве противообрастающих агентов. Они отметили, что совсем необязательно убивать морские организмы; достаточно не давать им садится на поверхность покрытия. Оказалось, что группа продуктов, которую исследователи называют катеминами, и о которых известно, что они обладают низкой токсичностью благодаря своему фармацевтическому использованию, может не давать ракообразным обездвиживать себя. Медетомидин особенно эффективен, и была разработана система медленного выпуска лекарственного вещества, действие которой основано просто на адсорбции медетомидина на поверхности наночастиц оксидов металла. Рассмотренные здесь примеры являются только иллюстрацией имеющихся и предстоящих в будущем достижений на пути к созданию покрытий, не представляющих опасности для окружающей среды и не содержащих токсичных веществ. Это одна из тех областей, в которых всегда будет возможность совершенствоваться, но, возможно, мы сейчас только начинаем осознавать, как многого можно добиться в случаях, когда производители красок и производители сырья вынуждены все более старательно работать над своими рецептурами. Сэнди Моррисон, http://www.specialchem4coatings.com |