Простейший насыщенный полиэфир представляет собой продукт конденсации гликоля и терефталевой кислоты и используется в производстве полиэфирных пластиков, таких как волокно терилен.  Каждый элементарный акт поликонденсации в процессе образования смол вызывается реакцией этерификации, на которой основано получение сложных эфиров. В общем виде реакцию получения полиэфирных смол можно написать следующим образом: 
Не следует забывать и о реакции полиэтерификации, так как сополиэфирные смолы являются производными более чем двух мономеров. Этерификацию и полиэтерификацию можно ускорить добавлением сиккативов на основе металлов. Для промышленности представляют интерес три основных способа проведения поликонденсации: в расплаве, на поверхности раздела двух фаз и в растворе. Большинство полиэфирных смол получают поликонденсацией в расплаве. Линейные и разветвленные насыщенные полиэфирные смолы с низкой молекулярной массой получают в результате одностадийного процесса при повышенной температуре в атмосфере инертного газа для предотвращения побочных реакций деструкции, окисления. Для смещения равновесия в сторону образования поликонденсационной смолы (удаления побочного продукта), кроме нагревания, применяется пониженное давление. Реакция этерификации происходит в атмосфере азота при температуре 180-260 ºС. Добавляются катализаторы (дибутил олово оксид, хлорид олова, бутил хлоротин дигидрооксид или тетрабутилоксититанат) и ингибиторы окисления (фосфористая кислота, тринонилфенилфосфит или трифенилфосфит). Вода, высвобождаемая во время реакции, удаляется с помощью дистилляции. Нужная степень этерификации достигается путем применения азеотропной или вакуумной дистилляции на последней стадии реакции. Процесс контролируют по кислотному числу, которое показывает какое количество кислоты вступило в реакцию. В процессе реакции кислотное число уменьшается, вязкость увеличивается. В результате реакции получается полиэфирная смола, которая растворяется в органических растворителях или в смеси органических растворителей. Полиэфирную смолу можно добавлять в растворитель сразу после синтеза, но часто растворитель добавляют уже во время производства лакокрасочного покрытия из экономических соображений. Точные параметры процесса подбираются исходя из реагирующих веществ на основе которых получается та или иная смола. Технологический процесс получения НПС может быть следующим. В реактор загружают гликоль и после его подогрева до 100°С — ангидриды. Иногда в реактор добавляют в количестве 10% от массы основных компонентов растворитель, образующий азеотропную смесь с выделяющейся при синтезе водой, что облегчает ее удаление (в этом случае способ получения НПС - в растворе). Процесс поликонденсации проводят при 170—200 °С и работающей мешалке в токе азота. Пары гликоля конденсируются в обратном холодильнике и конденсат стекает в реактор, а пары воды и азот отводятся через прямой холодильник. Водный конденсат собирается в сборнике. Контролируют процесс по кислотному числу. Готовый полиэфир после охлаждения до 70 °С сливают в смеситель, где растворяют в растворителе. Полученный раствор после охлаждения фильтруют и сливают в тару. В зависимости от состава смолы и исходных компонентов подбирают условия проведения процесса. Рассмотрим примеры технологических процессов синтеза НПС. Ниже приведены рецептуры смол, процесс получения которых будет описан. Примеры 2-6 представляют собой патентные разработки. Примеры рецептур НПС № | Компонент | Содержание, масс. части | Пример 1 | Неопентилгликоль | 402 | Адипиновая кислота | 94 | Изофталевая кислота | 404 | Тримеллитовый ангидрид | 100 | Пример 2 | Моноэтиленгликоль | 294 | Неопентилгликоль | 510 | Фталевый ангидрид | 409 | Изофталевая кислота | 458 | Терефталевая кислота | 511 | Пример 3 | Моноэтиленгликоль | 301 | Фталевый ангидрид | 551 | Адипиновая кислота | 852 | Пример 4 | Пропиленгликоль | 787 | Триметилолпропан | 127 | Адипиновая кислота | 155 | Изофталевая кислота | 1092 | Терефталевая кислота | 465 | Пример 5 | Моноэтиленгликоль | 124 | Неопентилгликоль | 468 | Диэтиленгликоль | 213 | Триметилолпропан | 131 | Адипиновая кислота | 689 | Изофталевая кислота | 695 | Пример 6 | Неопентилгликоль | 546 | Моноэтиленгликоль | 106 | 1,6-гександиол | 50 | 1,4-циклогександиметилол | 123 | Пропиленгликоль | 65 | Изофталевая кислота | 1271 | 1,4-цилкогександикарбоновая кислота | 146 |
Пример 1 Получение смолы, состоящей из неопентилгликоля, адипиновой кислоты, изофталевой кислоты и тримеллитового ангидрида получают в два этапа. На первом, гликоль, кислоты и часть ангидридов подвергаются обработке для достижения низкого показателя кислотности при температуре 230-240 градусов по Цельсию, затем охлаждаются до температуры 170—180, добавляется остаток ангидридов и процесс продолжается при этой температуре, пока не будет достигнут показатель кислотности 45-50. Затем смолу растворяют в подходящем совместном растворителе и нейтрализуют амином.
Пример 2 Реакция этерификации начинается при температуре 188ºС с добавлением 2 м.ч. тринонилфенилфосфита и 1 м.ч. оксидибутилового эфира. Вода, образованная в ходе реакции удаляется дистиллятором. Максимальная температура, при которой идет реакция – 245ºС. Через час после того, как температура достигнет 245ºС, кислотное число доводиться до 3,5 мг КОН/гр. Гидроксильное число полученной смолы – 18,5 мг КОН/гр. Вязкость при 158ºС)–260 дПа•с. Средний молекулярный вес – 5085 г/моль. Температура стеклования данной смолы – 50 ºС. Пример 3 Получение полиэфирной смолы с высоким содержанием сухого вещества происходит также в азотной атмосфере при механическом перемешивании. В качестве инициатора выступает фосфористая кислота (2 м.ч.). Реакция этерификации начинается при температуре 157ºС. Вода, образованная в ходе реакции, отводится дистилляцией. Максимальная температура, при которой идет реакция – 235ºС. Через час после того, как температура достигнет 235ºС, осуществляется азеотропная дистилляция с использованием ксилола, до тех пор, пока не будет достигнуто кислотное число 5 мг КОН/гр. Затем достигается кислотное число 2 мг КОН/гр. После охлаждения до температуры 170 ºС добавляются 857 весовых частей Solvesso 150™, чтобы достичь 75 % содержания сухого вещества. Кислотное число полученной твердой полиэфирной смолы –2 мг КОН/гр., гидроксильное число –20 мг КОН/гр. Вязкость при температуре 23ºС - 73 дПа•с. Средний молекулярный вес –4920 г/моль. Температура стеклования данной смолы – 15ºС. Пример 4 В качестве инициатора выступают дибутилоксид олова (1,1 м.ч.) и тринонилфенилфосфит (1,1 м.ч.). Реакция этерификации начинается при температуре 177ºС. Максимальная температура, при которой идет реакция – 230ºС. Через час после того, как температура достигнет 230ºС, осуществляется азеотропная дистилляция с использованием Solvesso 150™, до тех пор, пока не будет достигнуто кислотное число 6,4 мг КОН/гр. Затем достигается кислотное число 5,3 мг КОН/гр. Кислотное число полученной твердой полиэфирной смолы – 5,3 мг КОН/гр. Средний молекулярный вес –5410 г/моль. Температура стеклования данной смолы –49ºС. Пример 5 В качестве инициаторов выступают дибутилоксид олова (1 м.ч.) и тринонилфенилфосфит (2 м.ч.). Реакция этерификации начинается при температуре 165ºС. Максимальная температура, при которой идет реакция – 230ºС. Через час после того, как температура достигнет 230ºС, осуществляется азеотропная дистилляция с использованием Solvesso 150™, до тех пор, пока не будет достигнуто кислотное число 0,8 мг КОН/гр. После охлаждения до температуры 170ºС добавляются 857 весовых частей Solvesso 150™, чтобы достичь 70% содержания сухого вещества. Кислотное число полученной твердой полиэфирной смолы –0,8 мг КОН/гр. Вязкость – 49 дПа•с. Средний молекулярный вес –4590 г/моль. Температура стеклования данной смолы –14ºС. Пример 6 В качестве инициаторов выступают хлориндигидроксид (Fascat 4101™, 1 м.ч.) и тринонилфенилфосфит (2 м.ч.). Реакция этерификации начинается при температуре 183ºС. Максимальная температура, при которой идет реакция – 230ºС. Через час после того, как температура достигнет 230ºС, кислотное число доводится до 2,4 мг КОН/гр. Кислотное число полученной полиэфирной смолы –2,4 мг КОН/гр., гидроксильное число –25 мг КОН/гр. Средний молекулярный вес –4560 г/моль. Температура стеклования данной смолы –45ºС. Примеры производства материалов на основе НПС Для лучшего понимания дальнейшего использования НПС, приведем примеры материалов, получаемых на их основе. А). Покрытия на основе насыщенных полиэфиров, полученных по рецептуре №2 и №3, приведенной в предыдущей части главы. 1. COIL COATING (первичное покрытие) 1.1. Получение лакокрасочного покрытия Полиэфир, полученный в Примере 2, растворяется в следующем растворе: Solvesso 150™, эфир двухосновной кислоты, бутил гликоль в весовом соотношении 3:6:1 до получения 50% раствора. Вязкость полученного раствора - 17 дПа•с при температуре 23ºС. К 13,3 весовым частям полученной полиэфирной смолы добавляются 2,1 части противокоррозионного пигмента (Halox CW491™), 2.1 части противокоррозионного пигмента (Zinkfosfaat ZP/M™),4.1 части вещества, препятствующего оседанию пигмента в краске (10% раствор Bentone SD2 в Solvesso 150™), 6.4 части диоксида титана (Kronos 2160™), 10.4 части растворителя (Solvesso 150™/бутил гликоль 3:1), 0.2 части противопенной добавки/активатора (50% раствор Disparlon L1984™ в Solvesso 150™) и 5 частей наполнителя - Blancfixe Micro. Затем смесь доводят до состояния пигментной пасты, при температуре не выше 70ºС. После охлаждения до комнатной температуры к 7,5 частям данного 50% раствора полиэфирной смолы, добавляются 2,7 части полиэфирной смолы, полученной в Примере 3, 2.8 частей сшивающего агента, содержащего аминогруппы (Cymel 325™), 0.4 части катализатора (Nacure 4167™), 1.2 части сшивающего линейные полимеры агента (Epikote 828™). Полученная смесь разбавляется смесью растворителей - Solvesso 150™ и бутилгликоля - в соотношении 3:1, до получения вязкости с 40-59 Па•с (при температуре 23ºС, (DIN standard 53 211). 1.2. Применение покрытия (предварительный слой - Coil coating). Оцинкованная сталь (Galfan) покрывается предварительным лакокрасочным покрытием, описанным в п. 1.1. Время отверждения в печи - 33 секунды при температуре 358ºС. Максимальная (пиковая) температура нагревания металла (ПТМ) – 210ºС. На предварительное покрытие наносится верхний слой на основе полиэфирной смолы - Uralac SN841™ (производства DSM Resins). Время отверждения в печи – 42 секунды при температуре 232ºС. 2. CAN COATING 2.1. Получение лакокрасочного покрытия Полиэфирная смола, полученная в примере 2, растворяется в следующем растворе: Solvesso 150™, сложного эфира двухосновной кислоты в весовом соотношении1:1 до получения 55% раствора. К 76.6 частям полученного раствора добавляются 18.4 части полиэфирной смолы с высоким содержанием сухого вещества, полученной в примере II и 5 частей эфира. В результате получается «смешанный полиэфир» с Тg 32ºС. К 97.5 частям полученной смеси добавляются 97,5 частей пигмента (Kronos 2310™) и 15 частей Solvesso 150™. Затем доводят до состояния пасты температуре не более 70ºС. После охлаждения до комнатной температуры к данной смеси к 18.5 частям «смешанной полиэфира», полученной выше, добавляются 14,9 частей изоцианового сшивающего агента (Uradur YB147™). Полученная смесь разбавляется Solvesso 150™ до получения вязкости с 90-110 Па•с при температуре 23ºС. 2.2. Применение покрытия (Can coating) Покрытие, описанное в п. 2.1, наносится на электролитическую белую жесть при помощи 40 µm напылительной машины. Время отверждения в печи-10 мин при температуре 180ºС. Б). Покрытия на основе насыщенных полиэфиров, полученных по рецептуре №6 и №3, приведенной в предыдущей части главы.
3. COIL COATING (лицевое покрытие, top coat) 3.1. Получение лакокрасочного покрытия. Полиэфирная смола, полученная в Примере 6 растворяется в смеси Solvesso 150™ и бутилгликоля (в соотношении 4:1) до получения 60% раствора. Вязкость полученного раствора 31 дПа•с. К 63.3 частям полученного раствора добавляются 31.5 частей полиэфирной смолы с высоким содержанием сухого вещества, полученной в примере 3 и 5.2 части Solvesso 150™. В результате получается 60% раствор «смешанной смолы» с Тg 18ºС. К 28.1 частям полученной смеси добавляются 67.4 части пигмента (Kronos 2310™) и 15.6 частей растворителя (Solvesso 150™). Затем доводят до состояния пасты при температуре не более 70ºС. После охлаждения до комнатной температуры к 18.5 весовым частям 60% раствора смешанных смол, добавляют 15.1 часть сшивающего агента (Cymel 303™, пр-ва компании Dyno Cytec), 4.9 частей катализатора (Dynapol BL1203™), 1.03 частей стабилизатора (Tinuvin 292™), 8.4 части матирующей добавки (Syloid ED 44™), 4.4 части катализатора (Nacure 2500™) и 8.4 части растворителя (Solvesso 150™/бутил гликоль 3:1). 3.2. Применение лакокрасочного покрытия (верхний слой – top coat, coil coating). Лакокрасочное покрытие, описанное выше, используется в качестве завершающего верхнего слоя поверх предварительного покрытия (койл коутинг, алюминий). Время отверждения в печи - 41 секунда при температуре 300ºС. ПТМ – 241ºС. 4. CAN COATING (лаковое покрытие) 4.1. Получение лакового покрытия Полиэфрир (№3) растворяется в смеси Solvesso 150™ и бутилгликоля (в соотношении 4:1) до получения 50% раствора. Вязкость полученного раствора 35. 68,4 части полученного раствора полиэфирной смолы смешиваются с 22,6 частями полиэфирной смолы (№3) и 9 частями смеси Solvesso 150™ и бутилгликоля ( в соотношении 4:1), в результате получается 50% раствор с Тg 24°C. К 60.9 частям полученного раствора 8,4 части сшивающего агента Uramex BF891™ и 5 частей 75% раствора сшивающего агента Epikote 834™ в бутил гликоль ацетате, а также 18,5 частей растворителя (Solvesso 150™/изопрофорон 1:1). 4.2. Применение покрытия Данное покрытие наносится на электролитическую белую жесть. Время отверждения в печи – 12 минут при температуре 185С. Технологическое оснащение производства Синтез большей части сложных полиэфиров происходит на универсальной линии (за исключением ПЭТФ и ряда других обособленных продуктов). В зависимости от состава сырья, используемого для производства той или иной смолы, настраиваются технологические режимы, подбираются химические добавки (реагенты) и дозаторы. Технологический процесс производства полиэфирных смол состоит из следующих стадий: • подготовка и загрузка в реактор исходного сырья; • поликонденсация под атмосферным давлением; • поликонденсация под вакуумом; • растворение полиэфира в реакторе - растворителе; • охлаждение и слив готового продукта. 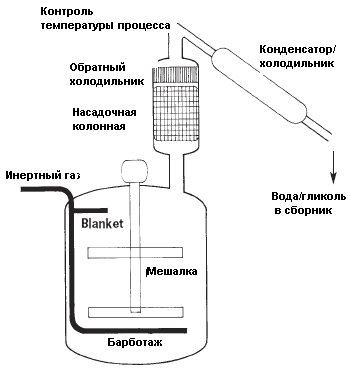
| Реактор синтеза НПС |
Реактор для производства полиэфиров представляет собой изготовленный из нержавеющей стали или биметалла вертикальный цилиндрический аппарат с эллиптическим днищем и крышкой, снабженный мешалкой обычного рамно-якорного типа и рубашкой. В реактор через крышку введена барботажная труба, по которой подают азот для вытеснения воздуха. Пары гликоля конденсируются в обратном холодильнике и конденсат стекает в реактор, а пары воды и азот отводятся через прямой холодильник. Водный конденсат собирается в сборнике. Контролируют процесс по кислотному числу. Готовый полиэфир сливают в смеситель, где растворяют в растворителе. Полученный раствор после охлаждения фильтруют и сливают в тару. Примеры технологических схем заводов по производству синтетических смол можно увидеть в Приложении, где представлены предложения поставщиков оборудования. 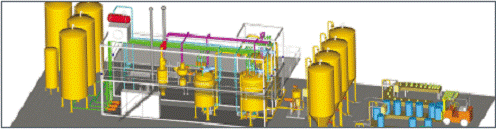
3D-модель завода по производству полиэфирных смол (EEG) Время производственного цикла на современных заводах составляет 14-16 часов в случае насыщенных полиэфиров на основе фталевого ангидрида и 18-25 часов в случае НП на основе изофталевой кислоты. В зависимости от рецептур и условий проведенияы процесса время производственного цикла на производствах различается. В частности, средний производственный цикл на оборудовании компании EEG составляет 7 часов, производительность – 10 тонн за цикл. В день проходит 3 производственных цикла, таким образом достигается производительность 30 тонн/сутки. С учетом плановых остановок, средняя годовая мощность завода составляет 7,5 тыс. тонн НПС. В отличие от производства обычных алкидов, процесс производства полиэфиров не усложняется наличием жирных кислот или масел. Одной из основных трудностей процесса синтеза является унос гликолей с водой. Для предотвращения потери гликолей используется специальная вертикальная система холодильников (конденсаторов). В то же время сам реактор аналогичен тому, который используется в производстве алкидов. Этим объясняется тот факт, что заводы по производству НПС зачастую совмещают с производством алкидных смол, а технологические линии называют производствами алкидных и полиэфирных смол(alkyd/polyester resin manufacturing plant). Несмотря на схожесть технологического оформления, под каждое определенное назначение разрабатываются рецептуры смол, в зависимости от этого разрабатывается дизайн завода, параметры процесса. Реакторы на производствах имеют различный дизайн: размер, условия смешения, нагрева, охлаждения. Для налаживания производства в каждом отдельном случае требуется изучение и подбор условий проведения процесса, которые обеспечат наилучший ход реакции, выход продукта и оптимизацию процесса производства в целом. Технологический процесс синтеза сложных полиэфиров характеризуется цикличностью операций и нестационарностью основных параметров во времени. Наряду с химической реакцией в реакторе периодического действия происходит интенсивный массообменный процесс отгона паров смеси воды и гликолей, их ректификации в установленной на реакторе насадочной колонне и возвратом гликолей в реактор. Унос гликолей оказывает существенное влияние на скорость химической реакции и качество готового продукта. В ходе синтеза наряду с изменением режимных параметров процесса (температуры, давления), происходит увеличение вязкости реакционной массы, а скорость отгона реакционной воды изменяется в десятки раз. Данные особенности процесса и наличие значительного количества компонентов реакции, обуславливают требования к оформлению и контролю процесса. На современных производствах регулировка процессов обеспечивается системой автоматизации, которая включает в себя: • автоматическое дозирование компонентов в широком диапазоне масс компонентов (от нескольких килограммов до нескольких тонн в один аппарат); • поддержание температуры с точностью ±1°С от заданной; • поддержание заданной скорости химической реакции; • автоматический расчет момента перехода на вакуумную стадию процесса; • хранение программ синтеза для различных марок смол. Можно выделить еще ряд особенностей, отличающих современные производства от производств более раннего периода. Во-первых, необходимым фактором оптимизации процесса является использование энергосберегающих технологий. Во-вторых, время производственного цикла на современных заводах на 20-50% меньше, чем на заводах конца 20 века. Это означает более высокую производительность на том же оборудовании. Более высокой производительности можно достичь, внеся некоторые изменения в производственный цикл. В частности, время загрузки сырья/выгрузки продукта можно сократить, увеличив размеры соответствующего оборудования и степень автоматизации. Более сложной задачей модернизации является увеличение скорости переноса тепла и охлаждения, так как эти параметры зависят от конструкции реактора. Увеличить скорость переноса тепла в реакторе можно в частности улучшением конструкции мешалки, с достижением лучшего горизонтального и вертикального перемешивания. Еще одним параметром, определяющим эффективность производства, является контроль за такими параметрами процесса, как вязкость продукта, кислотное и гидроксильное число. Большая часть заводов используют устаревший метод, заключающийся в отборе образца из реактора и тестировании его в лаборатории. Этот процесс занимает 15-30 минут, в течении которых химическая реакция продолжается и показатели продукта изменяются. Вмонтированные в реактор вискозиметры не решают этой проблемы. На современных реакторах для этих целей устанавливаются специальные измерительные системы, определяющие все эти параметры процесса в режиме настоящего времени. C текущей ситуацией и прогнозом развития российского рынка полиэфирных смол можно познакомиться в отчете Академии Конъюнктуры Промышленных Рынков «Рынок полиэфирных смол в России». Об авторе: Академия Конъюнктуры Промышленных Рынков оказывает три вида услуг, связанных с анализом рынков, технологий и проектов в промышленных отраслях - проведение маркетинговых исследований, разработка ТЭО и бизнес-планов инвестиционных проектов. • Маркетинговые исследования • Технико-экономическое обоснование • Бизнес-планирование Академия Конъюнктуры Промышленных Рынков Тел.: (495) 918-13-12, (495) 911-58-70 E-mail: mail@akpr.ru WWW: www.akpr.ru |