Немного компаний в мире владеют этой технологией и одной из таких компаний является фирма "ГРАНИТ" (Лозанна, Швейцария). "Мокрое Окисление" является реакцией в жидкой фазе между органическими соединениями и кислородом при повышенной температуре и давлении. Осуществимость обработки определяется концентрацией органических соединений. Содержание органических соединений, выражаемое в COD (ХПК, химическое потребление кислорода), поступающих на обработку, должно быть заключено между 70 и 120 г O2/л. Если содержание за пределами этой области, то сток должен концентрироваться или разбавляться. Содержание сухого остатка не должно быть выше 15%. Установка по мокрому окислению эксплуатируется непрерывно 24 часа в день, 330 дней в году. Процесс окисления полностью автоматизирован и, за исключением пускового периода, не требуется постоянного присутствия оператора. Принцип технологии мокрого окисления Мокрое окисление является реакцией в жидкой фазе между органическими соединениями и кислородом при повышенной температуре и давлении. Этот метод используется как для обработки городских и промышленных шлам-содержащих жидких отходов, так и промышленных стоков, содержащих высокое количество органических соединений. Химическая реакция простая: органические соединения реагируют с кислородом, образуя диоксид углерода и воду. Схема реакции: Органические соединения + Кислород à CO2 + вода + органические кислоты Принципиальная схема установки жидкофазного окисления дана ниже. Для реакции могут быть использованы сжатый воздух или чистый кислород. Газ смешивается со шлам-содержащими жидкими отходами и смесь предварительно нагревается в теплообменнике, который использует тепло жидкости после реакции. Реакция мокрого окисления протекает в вертикальном трубчатом реакторе, работающем как барботажная колонна под давлением. Поскольку мокрое окисление является экзотермической реакцией, температура среды в реакторе увеличивается. Если содержание органики в шламе или жидких отходах высокое, то избыток тепла может быть использован для производства промышленного пара, нагрева циркулирующего масляного теплоносителя или просто для производства горячей воды в больших количествах. После удаления избытка тепла жидкость используется для предварительного нагрева поступающей жидкости. После охлаждения газожидкостная смесь разделяется в сепараторе. Жидкая и газовая фазы декомпримируются, используя регулирующий клапан. Газовая фаза состоит главным образом из диоксида углерода и избытка кислорода, но может также содержать следы CO и летучих органических соединений. Чтобы гарантировать чистоту выбросов газ проходит через катализатор, и затем он выбрасывается в атмосферу. В случае существенного содержания минералов в потоке, входящем на мокрое окисление (при обработке шлам-содержащих жидких отходов), минеральная часть отделяется от жидкой фазы и отжимается от воды на пресс-фильтре. Жидкая фаза содержит только очень легко биологически разлагаемые органические молекулы (органические кислоты) и возвращается на биологическую очистку вод или в реактор ферментативного разложения. Общее описание установки Установка мокрого окисления состоит из частей: • Установка подготовки поступающего жидкостного потока • Стадии мокрого окисления • Установки выделения минерального остатка Установка подготовки поступающего жидкостного потока Оптимальная концентрация потока определяется его содержанием COD (ХПК). Концентрация COD на входе должна быть в пределах между 70 и 120 г O2/л. За пределами этой области поток должен быть концентрирован или разбавлен. Консистенция потока не должна превышать 15% сухого остатка (150 г/л TDS – общего количества растворенных твердых веществ). В случае обработки перегнившего ила, оптимальная консистенция шлама для мокрого окисления находится в пределах от 10 до 15% сухого остатка. В случае шлама с аэробной обработки, оптимальная концентрация сухого остатка ниже: 5-10%. Для того, чтобы достичь таких концентраций из неотжатого шлама, необходим обезвоживающий барабан, центрифуга или стол. Так как стадия мокрого окисления работает непрерывно, должна быть предусмотрена буферная емкость, чтобы гарантировать подачу 24 часа. Гомогенность шлама в буферной емкости гарантируется непрерывной рециркуляцией системы. Стадия мокрого окисления Типичные условия эксплуатации следующие: • степень удаления COD 70-90% (по требованию клиента) • Температура реакции 250 - 300 °C • Давление реакции 60-100 бар • Окислитель Кислород • Время пребывания в реакторе 30-60 мин Схема установки представлена ниже. 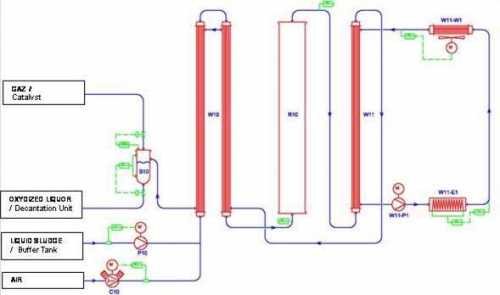 В зависимости от местных условий вместо кислорода может быть использован воздух. Установка мокрого окисления состоит из следующего основного оборудования: • Насос высокого давления P10 • Воздушный компрессор или кислородная стойка C10 • Рекуперативный теплообменник W10 • Реактор R10 • Теплообменник для выделения тепла реакции W11 • Газожидкостной сепаратор S10 В случае окисления шлама насос высокого давления P10 специально сконструирован для перекачивания шлама. Его скорость вращения может изменяться, чтобы позволить точное регулирование вводимого потока шлама. Необходимый кислород поступает с кислородной сборки и вводится в шлам перед подогревом. Кислородная сборка состоит из танка для хранения жидкого кислорода, за которым следует система питания: насос, ряд сосудов для хранения газа и автоматический клапан. В случае применения воздуха в качестве окислительного агента, необходимый для мокрого окисления воздух подается поршневыми компрессорами высокого давления. Теплообменник W10 позволяет подогреть смесь шлама и газа до температуры около 180°C, что позволяет начать экзотермическую реакцию мокрого окисления. Смесь затем вводится в нижнюю часть реактора R10, где температура возрастает до рабочей температуры. После реактора тепло смеси передается в цикл высокотемпературного теплоносителя или цикл горячей воды, используя трубчатый теплообменник W11. Выработанное тепло может быть использовано для других применений, например, нагревание реактора разложения или зданий, или тепло может быть выброшено. После удаления тепла в теплообменнике W11, окисленная смесь охлаждается в теплообменнике W10. Газовая фаза затем отделяется от жидкой в статическом сепараторе фаз S10, и оба потока, газ и жидкость, декомпримируются в специальных регулирующих клапанах. Газ после стадии жидкофазного окисления направляется через катализатор и выбрасывается в атмосферу. Нагреватель в средней части реактора позволяет запустить стадию мокрого окисления. Стадия выделения минерального остатка Жидкость после обработки мокрым окислением содержит минеральный остаток, который должен быть отделен. Это делается на пресс-фильтре или вращающемся фильтре. Отфильтрованная жидкость содержит только легко биологически разлагаемые соединения и может быть возвращена на биологическую очистку водных стоков. В зависимости от использованных технологий обезвоженный на фильтре минеральный остаток содержит 55-80% сухого вещества. Минеральный остаток может быть использован в дорожном строительстве или производстве кирпичей. Отходы и баланс производства Пример: случай перегнившего ила - 2000 тонн в расчете на сухой остаток /год - В случае перегнившего ила типичный COD потока будет: 1600 т-COD/год Выбранные условия работы: - температура реакции: 280°C - окислитель: кислород - время пребывания: 45 мин При этих условиях снижение COD будет по крайней мере 75%, и соответствующий COD поток, возвращающийся на биологическую очистку (очень легко биоразлагаемый COD): макс. 400 т/год. COD после мокрого окисления значительно увеличивает выработку метана. Прогнозируемый баланс эксплуатации установки жидкофазного окисления для обозначенного выше случая представлен в следующей таблице (при работе установки жидкофазного окисления 330 дней в году и рассматриваемом снижении COD 75%). Вход | Ед. | Кол-во | Выход | Ед. | Кол-во | Шлам 10% (перегнивший ил) | t/year | 20000 | Обработанный поток | т/год | 18140 | Кислород | т/год | 1260 | Газ (метан) | т/год | 1730 | Электричество | кВт.час | 37 | Твердый минеральный остаток | т/год | 1400 | | | | Избыточное тепло | кВт.час | 325 |
Избыток тепла в 325 квт.час может быть получен в виде пара (примерно 400 кг/час при 8 бар) или горячей воды (2000 кг/час при 80°C). Более того, если обработанный поток возвращается в реактор ферментативного разложения, температура смеси, входящей в реактор, будет выше, как это представлено в таблице ниже.
Консистенция шлама на входе в реактор | % TDS*) | 4 % TDS | 6% TDS | 8% TDS | Начальная температура входящего шлама | °C | 15 | 15 | 15 | Конечная температура входящего шлама после смешения с потоком после жидкофазного окисления | °C | 27 | 32 | 35 |
*) TDS – количество растворенных твердых веществ Выбросы: Газ с установки очищается и может быть выброшен в атмосферу в соответствии с нормами Евросоюза. Твердый остаток с окисления представляет минеральную часть шлама, входящего на стадию мокрого окисления, и содержит менее чем 5% TOC (Общее число углерода). Он может использоваться (производство кирпичей, строительство дорог) или выбрасываться на свалки. Жидкость содержит остаточную органику в виде небольших легко биологически разлагаемых молекул, главным образом карбоновых кислот (напр., уксусная кислота, жирные летучие кислоты). Она возвращается на установку биологической очистки. Возврат окисленной жидкости непосредственно в метатенк сильно увеличивает производство метана (от 10 до 30% больше по сравнению с "нормальным" производством биогаза). Внедрение При необходимости, установка может быть очень компактной. Ее размер модульный и может быть изменен в соответствии с местными ограничениями клиента. Список применений "Гранит" является одной из нескольких компаний в мире, которые имеют опыт в конструировании установок жидкостного окисления для обработки перегнившего ила. Из-за относительно высокого содержания минеральной составляющей в нем установки по переработке перегнившего ила имеют набор специальных требований. "Гранит" знает исключительно хорошо эту сферу, так как организация построила и в настоящее время эксплуатирует установку по жидкофазному окислению для обработки перегнившего ила в Orbe, Швейцария. "Гранит" имеет также большой опыт в строительстве установок по жидкофазному окислению для обработки промышленных стоков. В таблице ниже перечислены все существующие установки: Имя | Страна | Годпуска | Тип применения | Тип потока | Мощность | Окислитель | Thonon Unit | Франция | 2004 | Пульпа и бумага | Черная жидкость | 2,5 м3/ч | Воздух | Orbe Unit | Швейцария | 2000 | Городской шлам | Перегнивший городской ил | 0,5 м3/ч | Кислород | Grenzach Unit | Германия | 1991 | Химия | Хлорированные органические соединения | 15 м3/ч | Воздух | Monthey Unit | Швейцария | 1989 | Химия | Хлорированные органические соединения | 10 м3/ч | Воздух | Brunnsbüttel Unit | Германия | 1981 | Химия | Производные нафталиновой кислоты | 30 м3/ч | Воздух |
Инвестиции Инвестиции определяются количеством сухого остатка, который будет обрабатываться ежегодно и содержанием органических соединений. Необычно высокие количества соединений хлора и серы могут повлиять на цену через выбор материала, используемого для строительства высоко температурных частей установки. Поставка Конечный срок поставки 12 месяцев. Период пуска в 4 месяца гарантируется специалистами "Granit" и включается в стоимость. Эксплуатационные и капитальные затраты Для того, чтобы определить эксплуатационные и капитальные затраты установки мокрого окисления, необходимы по крайней мере следующие данные: Тип потока: - Промышленный (какая промышленность)? - Шлам с завода по обработке сточных вод? - Перегнивший ил или шлам с анаэробной обработки? - Промышленная или городская обработка сточных вод? Количество потока:т/год. Содержание сухого остатка: г/кг. Содержание органики в виде летучей органики: г/кг. Дополнительно: содержание органики как COD (ХПК), измеренное бихроматным методом: г-O2/л. Содержание хлора: мг/л. Содержание двухвалентных катионов (Ca, Mg, Si) Любая другая доступная информация.
Мнение эксперта (В.Г. Шарыкин): Оригинальная и проверенная технология позволит многим российским предприятиям решить проблемы заиливания на биологической очистке, переработки биологически не разлагаемых отходов, отходов, содержащих органический шлам, стоков с высоким содержанием токсических органических отходов и другие.
В.Г. Шарыкин, кандидат химических наук, эксперт
|