Две из основных наград в области экологии достались утилизации коврового покрытия. CARE (Американская программа по регенерации ковровых покрытий), четырехлетняя программа ковровой отрасли, предназначенная для увеличения объемов утилизации для повторного использования отходов ковровых покрытий, создаваемых использованными продуктами и изделиями, получила мемориальную награду экологической службы Dan Eberhardt Memorial Environmental Stewardship award. Но в индустрии ковровых покрытий начали заниматься утилизацией задолго до запуска CARE в 2002 г. В этой отрасли существует длительная традиция переработки материалов для повторного использования при изготовлении своей собственной продукции, и в середине девяностых годов она начала свое сотрудничество с Агентством США по защите окружающей среды и группами штатов в рамках Рабочих групп Среднего Запада по утилизации ковровых покрытий. Производители ковров вложили сотни миллионов в создание инфраструктуры рециклинга. 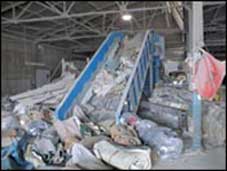
| Отрасль по производству ковровых покрытий ставит перед собой задачу восстановить для повторного использования 40% коврового покрытия, использованного потребителем, к 2012 г. В настоящее время восстанавливается примерно 4.5%, но эта цифра растет на 100% в год. (Фото: CARE) |
В 2002 г. CARE поставила казавшуюся недостижимой цель получения 40% -го восстановления для повторного применения использованных потребителем ковров к 2012 г. Полученные на данный момент результаты впечатляют. В 2005 г. в отрасли было регенерировано 225 миллионов фунтов использованного коврового покрытия, а это прирост по сравнению с 2004 г. на 108%. В этом месяце будут опубликованы цифры за этот год. Тем не менее, в прошлом году в Северной Америке было захоронено почти 5 миллиардов фунтов коврового покрытия, поэтому доля утилизированного покрытия составляет всего около 4.5%, а это еще очень далеко до 40%. Но уверенность участников CARE возросла по мере того, как увеличился объем собираемых отходов. Стоимость утилизированного коврового волокна, примерно 75% которого составляет найлон, была снижена за счет использования более экономичных сухих технологий и оставления этапа гранулирования расплава создателям компаундов и формовщикам, которые осуществляют повторное использование волокна. К числу успешных применений утилизированного коврового волокна можно отнести полипропиленовые дренажные камеры для подземных септических резервуаров и систем для ливневой воды, которые производятся Infiltrator Systems Inc. из Винчестера, Кентукки. Подразделение компании Champion Polymer Recycling Div. уже скоро начнет использование третьего полипропиленового сырьевого материала материнской компании, изготовленного из использованного коврового покрытия. Champion фильтрует расплав и гранулирует полипропиленовое волокно, а затем смешивает его с другим утилизированным полипропиленом. Компания InterfaceFLOR, LLC, Лагрэндж, Джорджия, производитель ковровой плитки на виниловой основе, осуществляет перемалывание использованных ковровых плиток для создания основы для новых ковров. В прошлом году InterfaceFLOR регенерировала более 16 миллионов фунтов и смогла утилизировать 84% от этого количества. Компания Entec Engineered Resins, производитель компаундов из Манчестера, Теннеси, обладает своей собственной технологией переработки для повторного применения использованного коврового волокна из найлона 66 в компаундах, изготавливаемых по индивидуальным заказам. Даже старое предприятие по повторной полимеризации утилизированного найлона 6, которое было закрыто уже на протяжении последних пяти лет, снова заработало. Работе созданных с самого начала предприятий по де- и реполимеризации Honeywell/DSM на Evergreen Nylon Recycling в Огасте, Джорджия, препятствовали низкие цены на капролактам и неэффективность технологии. Evergreen теперь принадлежит ковровому гиганту Shaw Industries из Дэлтона, Джорджия, который в феврале возобновил производство на регенерационной установке. DSM эксплуатирует установку для Shaw, и уже повысила эффективность эксплуатации. В настоящее время цены на капролактам высокие, и Shaw повторно использует найлон при производстве своего собственного коврового покрытия, а не продает пряжу на товарном рынке так, как это делала Honeywell.
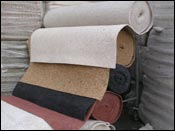
| 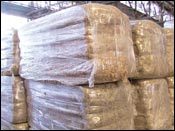 | Los Angeles Fiber, крупнейшая в мире компания по утилизации ковровых покрытий, производит волокно, упакованное в тюки по отдельным типам смолы, а также изготавливает нижний слой для коврового покрытия из утилизированного материала. |
Ожидается, что более мощная система сбора, имеющаяся у Shaw, соберет 100 миллионов фунтов использованного потребителями найлона 6 для Evergreen, а также еще 200 миллионов фунтов других типов коврового покрытия для прочих применений. На этот раз за счет этих усилий успеху Evergreen будет оказана поддержка.
|
Возобновление рециклинга текстильных материалов Вторую большую экологическую награду за рециклинг ковровых покрытий получил главный исполнитель программы CARE, компания Los Angeles Fiber Co. из Вернона, Калифорния, крупнейшая в мире компания, занимающаяся утилизацией ковровых покрытий. Компания регенерирует почти 100 миллионов фунтов в год использованного коврового покрытия. Основанная в 1983 г. компания L.A. Fiber сначала занималась рециклингом промышленных текстильных отходов, создавая из них волокно, известное как регенерированный хлопок. Но с появлением NAFTA, крупнейшие североамериканские текстильные предприятия начали закрываться, и у L.A. Fiber стало не хватать сырьевых материалов. Поскольку недостатка в использованном ковровом покрытии не было, предприятие приспособило свое разработанное внутри компании оборудование для работы с текстильным волокном под утилизацию коврового покрытия для повторного использования. Сейчас в компании L.A. Fiber используют переносные датчики ближней инфракрасной области (NIR) для того, чтобы рассортировывать поступающее ковровое покрытие в зависимости от волокна, использованного для верхнего слоя; затем формируются тюки в зависимости от типа полимера: найлона 66, найлона 6, полипропилена или же чего-либо еще. Часть полученных материалов реализуется прямо в тюках. Компания также обрабатывает отдельные материалы по одному, иногда неделями, на своем предприятии в Верноне. Используемая сухая технология включает сначала измельчение ковра, затем отделение волокон и удаление основы. Из волокон формируют новые тюки и продают создателям компаундов и прочим потребителям готовой продукции, как внутри страны, так и за рубежом. Из оставшихся материалов – натуральных волокон, полиэфирных волокон, более мелких фрагментов коврового покрытия и материалов, состав которых даже трудно определить - L.A. Fiber производит свой собственный продукт, который называется Reliance Carpet Cushion. Выявление огнеупорных материалов Две компании представили на GPEC новые автоматизированные модули для сортировки хлопьев, предназначенные для отделения фракций нежелательных электронных отходов (“e-отходов”), а именно, пластмасс, содержащих бромированные и хлорированные огнеупорные материалы. Компания S+S Separation and Sorting Technology GmbH из Германии (новый офис в США в Льюистоне, Нью-Йорк) представила свой новый рентгеновский датчик для е-отходов, который называется Varisort X. Он выявляет пластмассы, содержащие бромированные и хлорированные огнеупорные материалы, а также PVC, которые являются “нежелательными элементами” в потоке е-отходов. Как сообщают в S+S, для того, чтобы пластмассовые е-отходы могли иметь промышленное применение, содержание таких загрязняющих веществ не должно превышать 50 промилле. 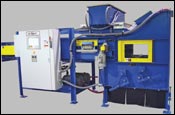
|  | Новые рентгеновские модули от S+S (справа) и MSS (слева) идентифицируют бромированные и хлорированные огнеупорные материалы, содержание которых не должно превышать 50 промилле для того, чтобы е-отходы можно было утилизировать для повторного использования. |
Компания MSS Inc из Нэшвилла, Теннеси, также недавно внедрила новый модуль рентгеновского датчика для выявления пластмассы с бромированными огнеупорными материалами. В настоящее время новый модуль является частью используемой MSS автоматизированной сортировочной системы e-Sort для сортировки электронных отходов. В MSS считают, что использовать рентгеновские лучи для того, чтобы выявлять PVC, будет проблематично: “Тонкий фрагмент PVC будет для рентгеновского луча выглядеть как толстый фрагмент ABS”, - говорит представитель компании. Компания Powdertech International является дистрибьютором переносных и автоматизированных устройств идентификации смол от IoSys из Ратингена, Германия. Переносная модель SSS3-FR и настольные модели Slidespec-S2 и mlRoSpark могут выявлять галогенизированные огнеупорные вещества. А лабораторные модели, Slidespec и mlRoSpark, могут также идентифицировать типы полимеров и добавки из тяжелых металлов. В модели sIRoLine для автоматизированных сортировочных линий используется NIR для идентификации полимеров, включая PVC и текстильные материалы.
Микровспенивание пленки из PET Компания MicroGreen Polymers и Университет Вашингтона, Сиэттл, представили на GPEC необычный подход к микроячеистому вспениванию отходов пленки из РЕТ с помощью ее насыщения углекислым газом при высоком давлении (патенты США 5182307 и 5684055). Рулон пленки из РЕТ (индекс вязкости 0.7) сначала перематывают со слоем пористого нетканого материала для того, чтобы отделить слои пленки из РЕТ друг от друга и позволить газу проникнуть в рулон. Затем рулон обрабатывают под высоким давлением углекислым газом в автоклаве периодического действия. Время обработки для пленки с толщиной 0.02 дюйма составляет от 4 до 20 часов в зависимости от необходимой степени насыщения углекислым газом. 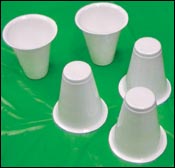
| Компания MicroGreen насыщает рулон пленки из РЕТ углекислым газом, затем нагревает и вспенивает пленку, осуществляя затем из нее горячее формование блестящих и термостойких стаканчиков для кофе. |
Насыщенную пленку разматывают и пропускают через печь с горячим воздухом за 15 - 30 секунд, что позволяет содержащемуся в пленке газу расшириться, но не порвать твердую поверхность пленки, которая затем охлаждается. В результате получается пленка с гладкой поверхностью и однородным микроразмерным (<10-микрон), замкнутым вспененным ядром и общим снижением плотности 80 - 90%. По оценкам MicroGreen, обработка обходится примерно 42¢ за фунт при пропускной способности 20,000 фунтов в день. Микроячеистую пленку из РЕТ можно использовать для горячего формования поддонов и изготавливаемых глубокой вытяжкой стаканчиков. Детали с толщиной стенок 1 мм термостабильны до температуры 3500 F, они также обладают высокими эстетическими свойствами. MicroGreen также провела испытания своей технологии с обработкой углекислым газом под давлением с пленками из PEN, PS, ABS, PVC, PC, акрилов, TPU, и PLA.
Йен Х. Шут, старший редактор Источник: Plastics Technology |