В области формования с множеством литьевых отверстий конструкционных пенопластов низкого давления по-прежнему распространена практика ручного извлечения деталей из пресс-формы. Но эта ситуация быстро меняется по мере того, как детали из пенопласта становятся все больше и все тяжелее. “На протяжении последних шести лет автоматизация была редкостью на нашем предприятии. Но изменения в области физической размерности, массы и формы деталей требуют применения автоматизации для того, чтобы не допускать телесных повреждений операторов”, - говорит Стюарт Хейден, менеджер предприятия в Джорджтауне, Кентукки, принадлежащего Orbis Corp. До недавнего времени предприятие было частью компании Linpac Materials Handling, крупного поставщика устройств для погрузки/разгрузки пластмассовых утилизированных сырьевых материалов, которая была приобретена Orbis. “Несколько лет тому назад наши самые тяжелые детали весили в среднем 70 фунтов, но сейчас чаще всего производят детали с массой 120 фунтов”, - поясняет Хэйден. “Также в настоящее время мы производим больше деталей, которые весят 140 или даже 150 фунтов”. 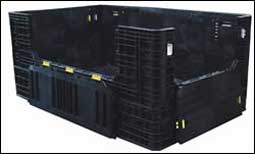
| Формованные детали из конструкционных пенопластов с большей массой, такие как ящики из HDPE с компонентами весом до 150 фунтов, заставляют предприятия переходить на автоматизированную погрузку/разгрузку деталей. |
При большом количестве тяжелых деталей, которые выходят из установки после каждого цикла, можно обойтись погрузкой/разгрузкой сложных деталей с помощью ручного труда. Но все становится намного сложнее, когда в формы нужно также помещать вставки для каждого последующего цикла. “Ручные операции не только создают эргономические проблемы и проблемы в области обеспечения безопасности для работника, они могут также влиять на продолжительность цикла обработки детали”, - говорит Хейден. Пресс должен простаивать, пока рабочий не покинет участок формования, а из-за этого материал может дольше удерживаться в цилиндре, чем это необходимо. Количество деталей, формуемых одновременно, может даже сокращаться для того, чтобы ускорить ручное извлечение деталей.
Пришествие автоматизации “Формовщики стремятся получить более стабильный производственный цикл, повысить производительность и оптимизировать каждый этап осуществляемых операций. Вот почему в области формования конструкционных пенопластов наблюдается устойчивая тенденция к внедрению автоматизации, особенно, на более крупных установках”, - говорит Эд Хьюнерберг, директор по формованию конструкционных пенопластов и промышленному выдувному формованию компании Uniloy Milacron, которая создала прессы, использующиеся на предприятиях Orbis. Хьюнерберг рассказывает, что компании, занимающиеся собственным формованием, которые работают на специально выделенных линиях для определенных продуктов, первыми начали использовать робототехнические устройства, особенно, по мере того, как детали у них начали становиться все тяжелее. Тем не менее, даже компании, осуществляющие формование по индивидуальным заказам на одной-двух установках, находят практические причины для того, чтобы рассмотреть вопрос об использовании робототехнических устройств. “У формовщика, работающего по индивидуальным заказам, как правило, эксплуатируются различные сочетания множеств пресс-форм на одной установке, гнезда для каждой серии устанавливаются в различное положение на установках с широкой плитой. У типичной 750-тонной установки SF с широкой плитой расстояние между поперечными планками 137 дюймов”, – говорит Хьюнерберг. Он также добавляет, что наличие робототехнического устройства позволяет формовщику создавать, сохранять и считывать программу, которая предназначена для того, чтобы доставать и подбирать детали, что позволяет сделать погрузку/разгрузку деталей более воспроизводимыми.
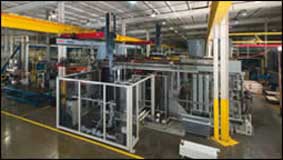
| Два больших робототехнических устройства на одной балке позволяют Orbis оптимизировать работу на прессе, уменьшить продолжительность циклов, количество лома, а также продолжительность простоев, которые возникают из-за поломки деталей. |
Хьюнерберг говорит, что Uniloy разработала специальный разъем устройства связи с робототехническим устройством, который позволяет более эффективно осуществлять связь между роботом и прессом. “Еще несколько лет тому назад нельзя было и представить себе использования многоштырькового соединения для наших машин, а сейчас такое соединительное устройство установлено как стандартный элемент. Более половины всех прессов для конструкционных пенопластов, которые реализует Uniloy, подготавливается под использование средств автоматизации для извлечения деталей”, - говорит Хьюнерберг. Интерфейс настроен для конфигураций SPI или Euromap. Компания Linpac начала автоматизацию несколько лет тому назад с внедрения боковых робототехнических устройств. По словам Хейдена, боковые робототехнические устройства подходят для некоторых более простых применений, но более крупные детали лучше перемещать с использованием моделей с подвеской сверху.
|
Погрузка/разгрузка крупных деталей Предприятие в Georgetown является одним из пяти предприятий Orbis, занимающихся конструкционными пенопластами. Это предприятие производит крупные решетчатые ящики из HDPE, которые состоят из основания и четырех боковых стенок. По словам Чака Бонда, менеджера по производственному инжинирингу предприятия в Джорджтауне, у контейнеров, которые можно складывать для того, чтобы сократить затраты на обратную транспортировку, также имеются откидные дверцы для облегчения доступа. По словам Хейдена, ящик может создаваться с одной, двумя или четырьмя откидными дверцами, причем заказы на ящики с двумя дверцами составляют более 90% от всего объема заказов. Занимаемая ящиком площадь составляет от 30 x 32 дюйма до 45 на 78 дюймов, а высота составляет от 25 до 50 дюймов. В пресс-форме может быть шесть гнезд, расположенных рядами, для производства четырех боковых стенок и двух съемных откидных дверец. “Масса боковых стенок может быть в диапазоне от 70 до 80 фунтов на каждую единицу, и большие размеры могут затруднять погрузку/разгрузку деталей”, - говорит Бонд. Основание, которое может весить от 120 до 150 фунтов, производится на отдельном прессе, где также основное внимание уделяется исключению ручных погрузки и разгрузки. Для компании Orbis размер деталей не является единственной проблемой. У крупного основания некоторых ящиков имеются также четыре арматурных стержня из композита, которые вставляются в гнездо с формованием поверх. Стержни подаются в пресс на специальном вращающемся револьверном устройстве. Кроме того, для производства крупных деталей необходима специальная последовательность извлечения стержней в инструменте, что, по словам Хейдена, значительно увеличивает сложность извлечения. Компания Orbis ранее ставила трех рабочих возле пресса для введения стержней, извлечения деталей и очистки деталей (такой как удаление ниток пластмассы толщиной с волос), а также сборки и штабелирования ящиков. Полученная производительность “Из-за всевозрастающего размера деталей здесь не может эксплуатироваться робот с боковой подвеской”, - говорит Хейден. Для того, чтобы найти альтернативное решение, Orbis сотрудничала с производителем вспомогательного оборудования Wittmann, Inc. при разработке специального полностью сервоприводного робототехнического устройства с монтажом сверху. Установленное примерно год тому назад устройство состоит из двух трехкоординатных роботов горизонтального хода с монтажом сверху от Wittmann W673, у которых оба манипулятора монтируются на один удлиненный брус. Брус монтируется над плитой на высоте более 10 футов над полом. У каждого робота грузоподъемность 275 фунтов, и этого, по мнению Хейдена, более, чем достаточно для того, чтобы осуществлять погрузку/разгрузку деталей. 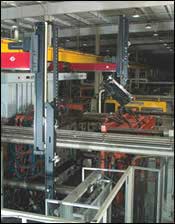
| Самая крупная в Северной Америке робототехническая система для конструкционного пенопласта компании Wittmann имеет две системы с подходом сверху модели W673 на одной балке. Они вводятся в форму и выводятся из нее за 15 секунд. |
Для робота с монтажом сверху требуется меньше производственной площади и защитного ограждения, чем для предшествующей модели с монтажом сбоку. Конфигурация бруса в виде буквы T позволяет двум роботам функционировать попеременно для осуществления введения вставки и извлечения детали или же осуществлять одновременное извлечение деталей из различных пресс-форм или же погрузку/разгрузку одной очень крупной детали. Добавление запястного шарнира к манипулятору робота позволяет осуществлять поворот на 180°, и помогает перемещать вставки и готовые изделия. При формовании основания ящика роботы программируются для того, чтобы сначала размещать вставку в одну половину пресс-формы, а затем работать совместно для извлечения готового изделия из другой половины пресс-формы. Как рассказывает Бонд, при производстве более маленьких боковых стенок оба робототехнических устройства вводятся в участок формования одновременно, и каждый робот извлекает до трех деталей каждый. Роботы программируются с помощью контроллера от Wittmann R7, который использует подпрограммы, специальные для каждой пресс-формы и каждого рабочего органа инструмента (EOAT). Подпрограммы сохраняются для последующей установки. Контроллер снабжен программным обеспечением для предупреждения столкновения в качестве стандартного. Он также программирован для защитной блокировки, которая препятствует взаимодействию с мостовым краном, когда последний работает в непосредственной близости от пресса. При смене пресс-формы с помощью крана, робот переводится в безопасное положение, и не может эксплуатироваться до тех пор, пока кран не покинет защищаемый участок. Конфигурация двойного робота на одной балке использует самый большой устанавливаемый Wittmann в Северной Америке робот для формования конструкционных пенопластов. Wittmann также спроектировала блочное установочное устройство EOAT, которое позволяет Orbis легко осуществлять переключение с погрузки/разгрузки отдельного основания на извлечение из формы множества боковых стенок из пресс-форм с количеством гнезд от четырех до шести.
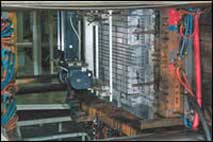
| 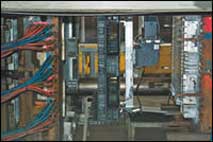 | Orbis использует устройство с двумя роботами, работающими по очереди, для размещения вставок (слева), и последующего извлечения отдельной крупной детали (справа). Их также программируют для одновременного извлечения нескольких деталей из множества гнезд. |
За счет использования робототехнических устройств Orbis смогла оптимизировать количество рабочих, работающих у пресса, сократив его с трех до двух. Роботу необходимо всего 15 секунд для того, чтобы войти в зону формования сверху, выполнить свои функции и покинуть зону, хотя для осуществления некоторых операций роботы должны выполнять специальные движения по переориентации деталей для очистки поперечных планок. “Мы можем повысить производительность наших установок на 29% для изготовления боковых стенок, и на 8% для изготовления оснований”, - говорит Бонд. “Установка функционирует с сокращением продолжительности цикла на 65%, и нам удалось решить все проблемы с обеспечением безопасности оператора”, - добавляет он. Кроме того, создается экономия за счет 1% уменьшения количества лома за счет более устойчивого цикла и снижения продолжительности простоя установок на 2%, поскольку детали извлекаются без повреждения. Компания Orbis установила, что робототехнические устройства от Wittmann окупили себя менее, чем за год, и в настоящее время собирается установить роботы и на другие прессы для производства деталей еще большего размера.
Микелл Найтс, старший редактор, Источник: Plastics Technology |