Многообразие видов разрушения деталей при трении связано физико-химическими и механическими процессами в зоне контакта, главным образом, от окружающей среды, условий трения и применяемых конструкционных и смазочных материалов. Длительное время главными направлениями борьбы с изнашиванием и уменьшением сил трения было повышение твердости поверхностей трения деталей машин. При повышении твердости материала уменьшается взаимное внедрение одной поверхности в другую, снижаются пластические деформации и окислительные процессы, а также действия абразива. Однако существует и другой путь решения этих вопросов. Так последние десятилетия появился значительный интерес к использованию противоизносных, антикоррозионных и восстановительных технологий в узлах трения, в том числе в двигателях внутреннего сгорания. Эти технологии позволяют в процессе эксплуатации, без разборки узлов и агрегатов, снижать износ и частично восстанавливать изношенные поверхности трения. Противоизносная антифрикционная технология ремонтно-восстановительными составами (РВС) по своей физической природе и по характеру воздействия на поверхности трения является одной из разновидностей методов повышения износостойкости деталей машин, основанных на эффекте безызносности при осуществлении избирательного переноса. Избирательный перенос это особый вид трения, который обусловлен самопроизвольным образованием в зоне контакта тонкой, не окисляющейся металлической пленки с низким сопротивлением сдвигу и неспособной наклепываться. Такую защитную пленку толщиной 1-4 мкм называют сервовитной. Образование сервовитной пленки в процессе трения обусловлено его созидательным характером, определенным интенсивностью обмена узла трения с внешней средой энергией и веществом, а также коллективным поведением ионов металла. Свойства защитной сервовитной пленки, образующейся в процессе трения, иные, чем у исходного металла. Следует отметить, что при трении детали контактируют на очень маленькой площади, составляющей 0,01-0,001% номинальной площади сопряженных поверхностей. В результате чего участки фактического контакта испытывают весьма высокие напряжения, что приводит к их взаимному внедрению, пластической деформации и, следовательно, к интенсивному изнашиванию. В случае избирательного переноса, контакт сопряженных поверхностей осуществляется через площадь фактического контакта и возрастает в десятки раз. После обработки деталей ремонтно-восстановительными составами коэффициент трения снижается в 3-5 раз. Перед нанесением ремонтно-восстановительных составов (РВС) необходимо подготовить защищаемые поверхности и масло либо топливо. При этом наибольшую сложность представляет подготовка деталей двигателей внутреннего сгорания (ДВС) находящихся в эксплуатации. Известно, что современные двигатели внутреннего сгорания имеют в зоне верхнего поршневого кольца, при работе на форсированных режимах, температуру выше 250°С. Еще более высокие температуры отмечены в зоне тюльпанов клапанов, продувочных и выхлопных окон, на днище поршня и некоторых поверхностях камеры сгорания. Минеральные масла, состоящие из высокомолекулярных нафтеновых, ароматических, парафиновых углеводородов и небольшого количества соединений, содержащих серу, кислород и азот, подвергаются при этих температурах окислению, разложению, полимеризации, конденсации и коксованию. Продукты окисления, разложения, окислительной полимеризации и конденсации, образующиеся в процессе работы, накапливаются в масле и откладываются на деталях двигателя. Образование твердых нерастворимых в масле продуктов его окисления и уплотнения (карбенов, карбоидов, асфальтенов, некоторых смол) в зоне поршневых колец и канавок поршня приводит к защемлению и пригоранию поршневых колец, снижению мощности двигателя, повышенным износам и задирам. Значительные отложения твердых углеродистых частиц на внутренней стенке канавок поршневых колец могут вызвать «распирание» колец и, как следствие, повышенные износы и задиры на гильзах цилиндров. Продукты окисления, коксования и озоления масла покрывают днище поршня. Нагар, образующийся на днище поршня, существенно изменяет степень сжатия двигателя и так же, как и образование лака и нагара на боковой и внутренней поверхностях поршня, ухудшает теплоотвод в масло. Твердые углеродистые частицы и другие продукты конденсации и окислительной полимеризации масла забивают дренажные отверстия поршня и приводят к резкому увеличению проникновения масла в камеру сгорания. Растет угар масла. Обильное нагарообразрвание на днище и на боковой поверхности поршня выше первого компрессионного кольца часто является причиной «натиров» на гильзе и боковой поверхности поршня вследствие нарушения масляной пленки и появления полусухого и сухого трения. Отложение нагара на тюльпанах и штоках всасывающих и выхлопных клапанов, в продувочных и выхлопных окнах двухтактных двигателей нарушает процессы смесеобразования и сгорания, приводит к неполному сгоранию топлива, повышает дымность выхлопа, снижает коэффициент наполнения и мощность двигателя. Образование продуктов окисления, конденсации и углеродистых частиц приводит к увеличению в масле механических примесей, смол и продуктов окисления. Углеродистые частицы, как правило, полностью не задерживаются фильтрами и не отделяются специально установленными центрифугами, а, циркулируя вместе с маслом по масляной системе двигателя, откладываются в клапанной коробке, в картере, в полых быстровращающихся деталях (коленчатый вал, муфты, ротор нагнетателя) забивают пути прохода масла и нарушают нормальную работу смазочной системы. Нередко основной причиной заклинивания, задира и выплавления коренных и шатунных подшипников дизелей является закупорка углеродистыми отложениями, выделившимися из масла, масляных каналов и отверстий для прохода масла на смазку подшипников. Кислые продукты, образующиеся в масле, увеличивают его коррозионную агрессивность, вызывают коррозионное разрушение подшипников из цветных металлов и коррозионный износ стальных деталей двигателя, в результате часто снижается его долговечность. Все это справедливо как для бензиновых двигателей, так и для дизелей. Но при работе масла в дизелях углеродистые частицы, откладывающиеся на деталях дизеля и загрязняющие масло, образуются в неизмеримо большем количестве и, прежде всего, за счет продуктов неполного сгорания дизельного топлива. В дизеле главным источником загрязнения масла и нагарообразования являются продукты неполного сгорания топлива (сажа), тогда как в бензиновых карбюраторных двигателях загрязнение масла и нагарообразование на деталях идет в основном за счет окисления, термоокислительной полимеризации, конденсации и коксования углеводородов и соединений, содержащих серу, кислород и азот, имеющихся в масле. Нагары, лаки и высокотемпературные отложения имеют очень хорошую адгезию к металлу и достаточно прочно связаны с поверхностью. Поэтому прежде чем наносить на поверхность РВС эту поверхность надо очистить от имеющихся загрязнений. Одним из способов очистки поверхностей камеры сгорания и газовыхлопного тракта ДВС может быть использование сервисных топлив, изготовленных с применением присадок-катализаторов горения (например, «0010» и «0011»). Катализаторы горения – присадки к топливу, задачей которых является увеличение полноты сгорания топлива, особенно на последних стадиях, характеризующихся недостатком кислорода. Применение сервисных топлив с присадками «0010» и «0011» позволяет очистить камеру сгорания и газовыхлопной тракт от лаков, нагаров и отложений, повысить КПД двигателя, снизить содержание вредных веществ в отработавших газах. Сводные результаты испытаний по снижению токсичности отработавших газов представлены в таблице 1. Таблица 1. Максимальное значение снижения содержания вредных веществ в отработавших газах при использовании присадок (%) Вредный компонент ОГ | Присадка | «0010» | «0011» | Дымность | 90 | – | Оксиды азота | 50 | 55 | Оксид углерода | 85 | 85 | Углеводороды | 65 | 80 | Бенз(a)пирен | 40 | 90 | Альдегиды | 60 | 16 | Аэрозоль | 20 | – | Масляный туман | 20 | 100 |
При использовании присадок происходит повышение механического КПД, что объясняется попаданием в зону трения меньшего количества абразивных частиц (сажи), которые выгорают под действием присадки и выносятся из камеры сгорания. Для подтверждения очистки камеры сгорания, клапанов и газовыхлопного тракта, двигатель одного из автобусов Икарус-250 был разобран на участке ремонта двигателей автопарка. После последнего капитального ремонта пробег автобуса составил 530000 км. Автобус проработал одну рабочую смену на сервисном топливе. Операция по очистке двигателя была проведена на автобусе ЛиАЗ-667. Результаты очистки приведены на рис. 1. Как видно из фото, произошла частичная очистка камеры сгорания от нагаров, применение сервисного топлива позволяет в процессе эксплуатации двигателя быстро очистить камеру сгорания, произвести раскоксовывание залегших колец.
Рис. 1. Головки блоков цилиндров двигателей ЗиЛ-375 автобусов ЛиАЗ-667 работавших на сервисном (1) и штатном (2) бензинах
Приведенные данные показывают, что применение сервисных топлив с присадками 0010 и 0011 позволяет: - очистить камеру сгорания и газовыхлопной тракт от лаков, нагаров и отложений; - повысить КПД двигателя; - снизить содержание вредных веществ в отработавших газах. Перед нанесением ремонтно-восстановительных составов (РВС) на узлы трения новых или капитально отремонтированных двигателей, машин и механизмов необходимо соответствующим образом подготовить поверхности. От степени подготовки поверхностей будет зависеть качество их обработки. Следует заметить, что хоть РВС и являются слабыми абразивами, однако использовать их для обкатки экономически вряд ли целесообразно. Обкатка заключительный технологический процесс изготовления двигателей, от которого в значительной мере зависит надежность работы двигателя и ресурс основных его сопряжений. При обкатке формируются оптимальные свойства сопрягаемых поверхностей, что позволяет деталям двигателя воспринимать номинальные нагрузки без повышенного износа и заеданий. Для ускорения приработки применяется универсальная приработочная присадка к моторным топливам «0033», представляющая собой композицию хромовых комплексов на базе СЖК С17С20 или алкилсалициловых кислот с алкенилсукцинимидом мочевины (СИМ). Универсальность приработочной присадки «0033» состоит в том, что она может применяться с бензинами и дизельными топливами; на любых режимах и при любом времени обкатки двигателя, по необходимости изменяется лишь только концентрация присадки в топливе. Присадка сгорает в камере сгорания двигателя вместе с топливом, образуя при этом мелкодисперсный оксид хрома. Часть ее выносится с продуктами сгорания, а часть вместе с масляной пленкой образует тонкую притирочную пасту. Детали прирабатываются как в процессе мягкого шлифования в масляной среде, так и путем заполнения крупных неровностей на поверхности пар трения абразивным порошком. Приработанные детали имеют более гладкие поверхности, что устраняет возможность микросхватывания. Поверхностный слой лучше держит масляную пленку, что в конечном итоге приводит к снижению износа. Кроме того, содержащиеся в присадки поверхностно-активные вещества улучшают диспергирующую способность топлива и способствуют отмывке топливной системы от скопившихся в ней отложений. В результате сгорания присадки мягкий абразив (оксид хрома) образуется только в камере сгорания и оказывает влияние на приработку деталей цилиндропоршневой группы и газовыхлопного тракта. Попадающее с маслом количество абразивной пасты достаточно мало, чтобы оказывать какое-либо влияние на износ вкладышей подшипников. Кроме того, дисперсность абразивных частиц настолько мала, что они не забивают фильтр тонкой очистки масла и масляные каналы. Все это позволяет не производить замену масла после приработки двигателя с применением присадки. Ниже приведены фотографии цилиндровых втулок двух двигателей ЗиЛ-131, прошедших обкатку после капитального ремонта. Первый двигатель проходил обкатку по штатной технологии, второй проходил обкатку на топливе с присадкой «0033», рис. 2. 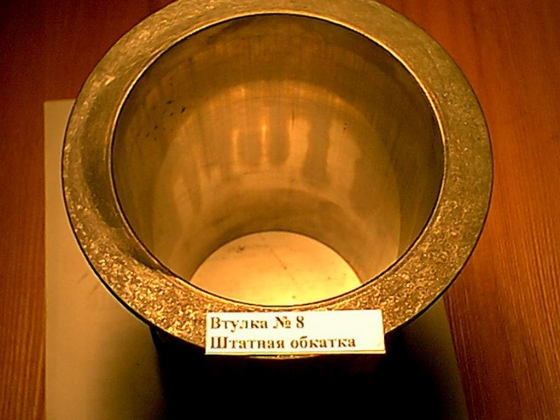 Рис. 2. 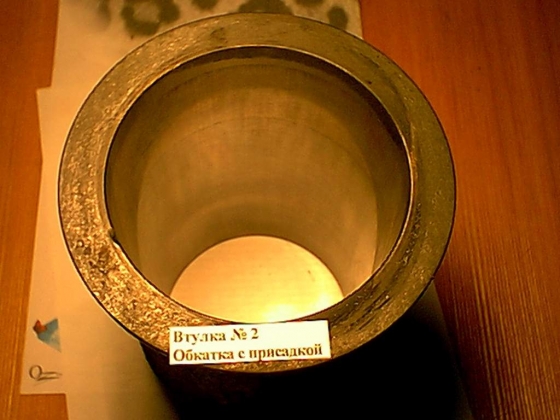 Втулка №8 двигателя ЗиЛ-131, прошедшего штатную обкатку, втулка №2 двигателя ЗиЛ-131, прошедшего обкатку на топливе с присадкой «0033»
На фотографиях четко видна разница качества приработки при использовании присадки «0033». На втулках, приработанных на штатном топливе, видны натиры, чего практически не отмечено при работе на топливе с присадкой. Площадь приработанной поверхности при обкатке двигателя на топливе с присадкой значительно больше, чем при обкатке на штатном топливе. При этом все втулки обкатанные на топливе с присадкой «0033» сохранили сетку от хонингования, в то время как на втулках, приработанных на штатном топливе, остались лишь ее фрагменты, т.е. с присадкой приработка проходит равномерно практически по всей рабочей поверхности. При дальнейшей эксплуатации хонингованная поверхность будет лучше удерживать масло, следовательно, меньше изнашиваться. Обкатка двигателей на топливе с присадкой 0033 позволяет: - приработать поверхности ЦПГ и выпускных клапанов и подготовить их к нанесению защитных покрытий; - снизить расход топлива при эксплуатации обкатанного двигателя; - промыть топливную систему двигателя. Нанесение ремонтно-восстановительных составов, в зависимости от типа обрабатываемого узла трения, производят из масла, топлива, либо СОЖ. При обработке узлов трения механизмов, машин и ДВС, находящихся в эксплуатации, следует помнить, что используемые в них горюче-смазочные материалы подвергаются естественному старению. В них накапливаются высокомолекулярные примеси смолы, асфальтены, карбены и карбоиды. Смолисто-асфальтеновые вещества могут находиться в молекулярно-растворенном, коллоидно-диспергированном состоянии или в виде макрофазы. Переход из одного состояния в другое может быть вызван действием разнообразных внешних факторов, самыми распространенными среди которых являются изменение температуры и состава растворителя, за счет испарения легких фракций топлив и масел во время хранения и эксплуатации. На основе исследования поверхностной активности асфальтенов в интервале 20-150°С была найдена критическая концентрация мицеллообразования в групповых компонентах соответствующих нефтяных остатков, и показано, что при концентрации асфальтенов 0,0050,60% по массе содержащие их нефтяные системы являются истинными растворами. С увеличением концентрации асфальтенов растворы переходят в дисперсные системы с последующим выделением асфальтенов в виде отдельной фазы. Частицы асфальтенов в коллоидных системах имеют размеры 230 нм и образуют коацерваты размером до 2 мкм. Поверхность асфальтенов, независимо от их природы, энергетически неоднородна, мозаична. В отличие от поверхности асфальтенов вторичного происхождения, характеризующейся преобладанием лиофобных участков, поверхность нативных асфальтенов по характеру менее лиофобна, что существенно влияет на структуру образуемых вокруг асфальтеновых частиц сольватных слоев. Химическая активность смолисто-асфальтеновых веществ обусловлена наличием в них реакционноспособных центров в качестве которых выступают алкильные заместители, функциональные группы, свободные радикалы и незамещенные, пространственно доступные положения ареновых, циклоалкановых и гетероциклических фрагментов. При определенных условиях суммарное действие межмолекулярных сил приводит к так называемому стэкинг-взаимодействию. В стопкообразной упаковке плоских молекул, расположенных на ван-дер-ваальсовых расстояниях друг от друга, имеет место стэкинг-взаимодействие, известное для биомолекул типа ДНК. По-видимому, стэкинг-взаимодействие в асфальтенах, возникающее между содержащимися в их составе ареновыми фрагментами, карбоксильными и аминогруппами, ответственно за формирование их пачечной кристаллоподобной структуры. Молекулярная масса нативных асфальтенов составляет от 1600 до 6000 а.е., нативных смол от 460 до 1600 а.е. Гораздо меньшими молекулярными массами характеризуются асфальтены и смолы вторичного происхождения. Для смолисто-асфальтеновых веществ наиболее характерны обменные, диполь-дипольные взаимодействия, водородные связи, взаимодействия между нефтяными основаниями и соединениями кислотного характера, приводящие к стэкингу-взаимодействию. Асфальтеновые частицы состоят из двумерных, почти планарных слоев со средним диаметром 0,851,5 нм, образующих пачечную структуру из 46 слоев общей толщиной 1,62,0 нм при расстоянии между слоями 0,350,37 нм (рис. 3). Такая модель строения асфальтеновых частиц имеет наибольшее признание. 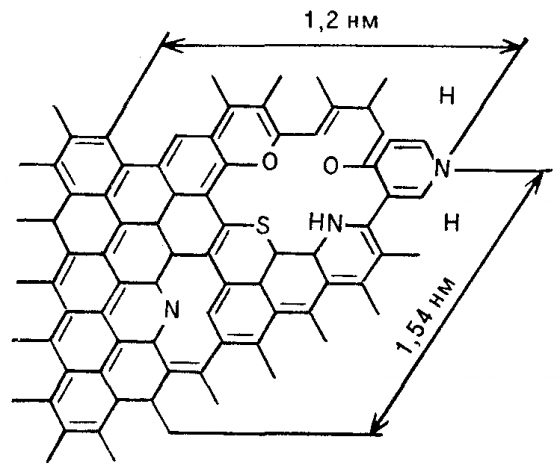
Рис. 3. Модель полиядерной структуры монослоя асфальтена
Эти структуры обладают способностью адсорбировать на свои поверхности микрочастицы РВС и препятствовать их контакту с поверхностями трения. Поэтому перед обработкой узлов трения, находящихся в длительной эксплуатации, необходимо очистить применяемый в качестве смазки материал (ГСМ) от имеющихся продуктов его старения. Проблема предварительной комплексной очистки ГСМ наиболее эффективно может быть решена использованием в качестве фильтрматериала пористых полимерных композиций. В течение нескольких лет проводились исследования эффективности очистки ГСМ от воды и механических примесей путем фильтрации его через различные материалы. В результате многочисленных опытов был создан и получил широкое внедрение полимерный материал, получивший название «АПРИСОРБ», схема работы фильтра приведена на рис. 4. Этот материал способен не только эффективно поглощать из топлива воду и механические примеси, рис. 5, но и непрерывно самоочищаться в процессе работы от накопившейся воды. В результате очистки получается прозрачное дизельное топливо, а загрязнения и вода удаляются, рис. 6. В процессе работы фильтра на основе «АПРИСОРБА» вместе с водой и механическими примесями удаляются из топлива в отстойник и микроорганизмы, а затем выводятся из корпуса фильтра при сливе отстоя.
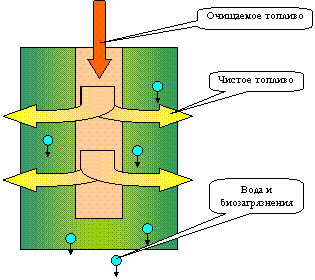 Рис. 4. Схема работы фильтрэлемента АПРИС®
Рис. 5. Разрез фильтрэлемента АПРИС® с задержанными механическими примесями 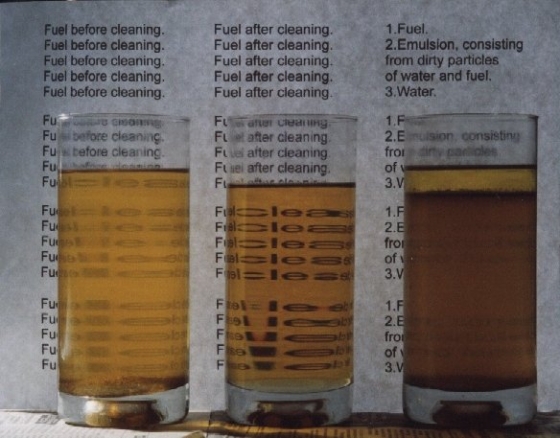
Рис. 6. Результаты очистки дизельного топлива фильтрэлементом АПРИС® 1 - Загрязненное дизельное топливо. 2 - Дизельное топливо после очистки материалом «АПРИСОРБ». 3 - Загрязнения и вода, удаленные из топлива. Из топлива, также, удаляется часть (до 75%) смолисто-асфальтеновых веществ. Все это ведет к более полному сгоранию топлива в двигателе, снижению его расхода до 5%, увеличению срока службы фильтров, топливных насосов высокого давления, форсунок и двигателя в целом на 30-40%, а также к существенному снижению объемов, дымности и токсичности отработавших газов. Совместные работы с НИИ медицины труда РАМН и НИИ канцерогенеза ОНЦ РАН, показали, что как в самом топливе, так и в отработавших газах двигателя содержание канцерогенных полициклических ароматических углеводородов после фильтрации снижается в среднем в 2,2-2,5 раза. При этом установлено, что, несмотря на незначительное снижение концентрации оксидов азота в отработавших газах, количество канцерогенных азотсодержащих соединений снижается на различных режимах работы двигателя от 2 до 20 раз. Мутагенная активность отработавших газов при использовании фильтрованного топлива, значительно ниже, чем при использовании стандартного топлива практически на всех режимах работы. Аналогично загрязнения удаляются и из масла. На рис. 7, как пример возможности данной технологии, представлены результаты очистки трансформаторного масла, взятого из сгоревшего трансформатора, которое содержало как большое количество продуктов окисления масла, так и мелкодисперсную сажу. Фильтрэлементы АПРИС справляются и с такими сильнозагрязненными масляными системами.
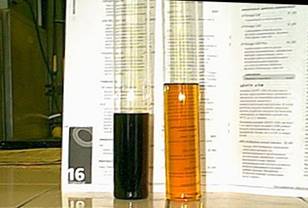
Рис. 7. Результаты очистки трансформаторного масла фильтрэлементом АПРИС® При нанесении ремонтно-восстановительных составов (РВС) на поверхности трения новых механизмом, машин и ДВС следует обратить внимание на то, что современные масла для ДВС содержат моюще-диспергирующие присадки. Они способствуют снижению образования отложений на поверхностях металлических деталей двигателя. Принцип действия присадок двоякий. Во-первых, они сорбируются на поверхности металла, создавая прочный слой, препятствующий образованию отложений; во-вторых, они солюбилизируют частицы нагара, смол и различных твердых продуктов. Моюще-диспергирующие присадки бывают двух типов: зольные щелочные и беззольные. Зольные присадки в качестве активных компонентов содержат алкилсульфонаты, алкилсалицилаты и алкилфеноляты металлов (бария, кальция, магния). Благодаря наличию щелочноземельных металлов зольные присадки характеризуются некоторой щелочностью. Поэтому они нейтрализуют кислотные продукты окисления масла. Щелочность присадок может быть искусственно повышена. Для этого в них добавляют высокодиспергированные карбонаты, оксиды и гидроксиды металлов. Наиболее распространены сульфонатные присадки, которые вводят в большинство моторных масел. Еще более эффективны алкилсалицилаты, стойкие в пресной и морской воде и придающие маслам дополнительные антиокислительные свойства. Однако алкилсалицилаты сравнительно дороги и применяются реже. Различают нейтральные, среднещелочные и высокошелочные алкилсульфонаты и алкилсалицилаты. Определение адсорбционной способности присадок методом контактной разности потенциалов показало, что присадки АСК и MACK образуют на металле электроотрицательные слои, причем АСК в большей степени, чем MACK. Композиции сукцинимида с диалкилдитиофосфатом цинка образуют на металле электроположительные адсорбционные слои, которые не повышают солюбилизирующей способности композиций. Необходимо отметить, что наиболее распространенные отечественные масла содержат зольные присадки, а импортные беззольные сукцинимидные. Т.е., отечественные и импортные масла создают на поверхностях трения заряды различной полярности. Это обстоятельство надо учитывать при подборе РВС. Беззольные моюще-диспергирующие присадки характеризуются меньшей щелочностью (около 20 мг КОН/г), но зато обладают лучшими солюбилизирующими свойствами. Наиболее распространены присадки С-5А и Днепрол. С-5А 40-50%-й раствор алкенилсукцинимидов в масле. В силу особенностей технологии содержит также некоторое количество полиизобутилена. Днепрол основание Манниха алкилфенола, модифицированное борной кислотой. Он более термостабилен, чем С-5А, и применяется в маслах, работающих при повышенной температуре. Рабочие концентрации моюше-диспергирующих присадок в масле составляют 25%, но в некоторых случаях могут достигать 20% и более. Поэтому при использовании свежих масел необходимо учитывать их способность образовывать на поверхности металла заряженные слои различной полярности и экранировать частицы РВС. Учитывая это, для получения максимального эффекта от обработки, необходимо соответствующим образом увеличить концентрацию РВС. Установки АПРИС для очистки ГСМ выпускаются серийно различной производительности и под различные задачи. Одна из них приведена на рисунке 8.
Рис. 8. Один из вариантов фильтрационных установок АПРИС®
Применение фильтров АПРИС® позволяет: - очистить горюче-смазочные материалы от механических примесей, воды и биозагрязнений; - понизить кислотность топлива и масла; - частично убрать смолистые вещества. Таким образом, нанесение ремонтно-восстановительных составов требует предварительной подготовки как поверхностей трения, на которые они будут наноситься, так и горюче-смазочных материалов, из которых они будут осаждаться. Разработанные методы очистки поверхностей, перед использованием РВС технологий, позволяют качественно и быстро без разборки двигателя подготовить поверхности к обработке. В.С. Перекалов, В.В. Сердюк, А.А. Кудян, С.Б. Панов, А.В. Климов, Д.В. Сердюк, Л.А. Ашкинази, Академия прикладных исследований, Санкт-Петербург. |