Топливно-энергетическая отрасль является ключевой как для всего мирового хозяйства, так и для каждой национальной экономики в отдельности. Для Росси ТЭК играет еще более значимую роль, нежели для других стран мира, особенно на современном этапе развития. ТЭК определяющим образом влияет на состояние и перспективы развития национальной экономики, обеспечивая около четверти производства ВВП и треть объема промышленного производства. Принимая во внимание разнообразие направлений ТЭК, следует особенно выделить его газовую составляющую. На долю России приходится 30,7% объемов мировых запасов газа. Для сохранения добычи на современном уровне необходимо осваивать новые месторождения мощностью 60 – 70% от нынешнего объема запасов. Газодобыча уже сейчас демонстрирует высокие темпы развития. Ожидается, что до 2025 г. объемы добычи газа удвоятся. При этом более 60% всей добычи газа в РФ будет сосредоточено в районах Крайнего Севера, что ставит перед разработчиками газовых месторождений ряд задач. Одна из них касается предотвращения закупорки магистральных газопроводов и подземных газохранилищ кристаллогидратами при низких температурах воздуха. Для этого в перекачиваемый газ необходимо вводить метанол. С развитием масштабов добычи газа в районах Крайнего севера в зонах вечной мерзлоты потребление метанола будет только возрастать. Уже на сегодня потребность в метаноле только ОАО «Газпром» достигает 250 тыс. т/год. Рост потребления метанола сопровождается и увеличением его стоимости. В настоящее время метанол на российском рынке предлагается по цене более 10000 руб./т. Для сравнения в 2003 г. метанол продавался по цене 5000 – 6000 руб./т, а год назад по цене 7000 – 8000 руб./т. Доставка метанола на промыслы Крайнего Севера как минимум удваивает его стоимость, а для некоторых месторождений, в частности Ямала, вообще существует возможность только сезонной его доставки, что приводит к удорожанию доставки в три раза. На рисунке 1 представлена тенденция увеличения стоимости метанола по годам, где нижняя составляющая – базовая стоимость метанола, а верхняя – расходы, связанные с его транспортировкой и хранением. 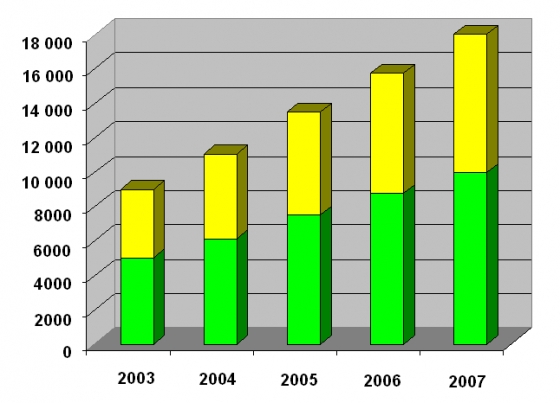 Рис. 1. Тенденция увеличения стоимости метанола
Оптимальным решением проблемы снижения стоимости метанола может стать размещение производств метанола в непосредственной близости от потребителей, т.е. в районах газодобычи. Осуществить это возможно при строительстве легко транспортируемых малотоннажных установок, производительностью 5000 – 20000 т/г. Однако здесь возникает ряд вопросов, касающихся технологии производства метанола, которая в своей основе подразумевает сложный технологический процесс. Существующие технологии, как правило, базируются на двух и более стадийных процессах, при которых на первой стадии, наиболее сложной и дорогостоящей, осуществляется паровая, парокислородная или углекислотная конверсия метана в присутствии катализатора при температурах 700 - 900°C и давлении 2-3 МПа. Процесс проходит с высоким потреблением тепла. Если добавить к этому энергозатраты на производство пара, то уже первая стадия получается весьма энергоемкой. На второй стадии осуществляется конверсия полученного синтез-газа в метанол, при этом необходимо обеспечить равномерное распределение температур во всем объеме реактора. Это требование необходимо для достижения высокой степени селективности конверсии с целью получения чистого продукта. Исходя, из этого можно прийти к заключению, что подобные технологии применимы только в случае очень крупных комбинированных производств, где становится оправданной утилизация тепловых потерь для покрытия высоких энергозатрат и снижения себестоимости получаемых продуктов. Все методики расчета экономической эффективности, отраслевые коэффициенты, нормативы создавались именно для таких предприятий и попытки рассчитывать по ним сравнительные характеристики малотоннажных производств встречают большие затруднения. И связано это с тем, что практически по всем показателям мы имеем дело с совершенно другим типом производства. Однако, всевозрастающий интерес в России и во всем мире к децентрализованному производству метанола, а также ужесточение экологических требований при добыче газа, подвигло многих разработчиков к созданию новых высокоэффективных технологий. Немаловажную роль в развитии таких технологий играет и то, что в настоящий момент основным сырьем для производства метанола служит природный газ, это приводит к необходимости локализации метанольных производств в районах газовых разработок. Истощение или наоборот, открытие крупных газовых месторождений способствует к существенному перераспределению метанольных мощностей. Именно поэтому в некоторых регионах мира, например, в Северной Америке продолжается сокращение мощностей в связи с повышением локальных цен на газ, оказывающих значительное влияние на себестоимость производства метанола. Себестоимость метанола в США в настоящее время является самой высокой в мире и на 40% превышает среднюю себестоимость в остальных странах мира. Таким образом, расположение производств метанола в районах газодобычи не только упрощает вопросы доставки метанола к потребителям, но и повышает экономическую эффективность производства метанола, снижая себестоимость целевого продукта. Возвращаясь к вопросу о возможности строительства малотоннажных производств метанола в районах Крайнего севера, необходимо отметить, что в настоящее время все газодобывающие компании, так или иначе, проявляют интерес к такого рода производствам. Принимаются решения о проектировании и строительстве. Одним из пионеров в этом направлении является ОАО «НОВАТЭК». Являясь крупнейшей газодобывающей компанией годовая добыча природного газа которой составляет более 25 млрд м3/год, ОАО «НОВАТЭК» вынуждено было обеспечивать завоз на газодобывающие подразделения, расположенные в районах Крайнего севера, более 25 тыс. т/год метанола. Что в связи с сезонными возможностями этого завоза, создавало целый ряд проблем и приводило к удорожанию метанола в 2 – 3 раза. Для решения этой проблемы было принято решение, о строительстве на территории Юрхаровского ГКМ малотоннажного производства метанола производительностью 12,5 тыс. т/г, с использованием в качестве сырья природного газа. В основу проектирования было заложено создание малотоннажного производства метанола в составе установки комплексной подготовки газа (УКПГ) с использованием существующей инфраструктуры: источников сырья и энергоресурсов, вспомогательных материалов, инженерных коммуникаций, сооружений, административно-бытовых сооружений. Исполнение производства, осуществляется в виде блок-боксов с высокой заводской готовностью, установка которых, на площадке потребителя не требует масштабных строительных работ. Разработанный в конце 60-х годов, блочно-модульный метод строительства до сих пор остается основополагающим в решении задач ускорения строительства объектов в районах Крайнего севера со сложными природно-климатическими условиями. Суть его состоит в том, что объекты строительства проектируются в виде блочных устройств различного назначения и комплектных зданий. Эти блоки и здания изготавливаются на специальных заводах в индустриальных центрах, перевозятся на площадки строительства, где в короткие сроки монтируются на подготовленные фундаменты. При этом непосредственно на площадках работает минимальное число людей, что позволяет значительно экономить время и материальные средства, необходимые для обустройства строителей в необжитых районах. Блоки в основном применяются там, где необходимо выполнить строительство в короткие сроки, ускорить инвестиционный процесс, сэкономить затраты на обустройство работников монтажных специальностей за счет уменьшения их численности, сократить транспортные расходы, так как доставка грузов осуществляется крупными блоками, а не ''россыпью''. Эффективность блочного метода строительства особенно проявляется в условиях малообъемного, рассредоточенного строительства. Поэтому блочное сооружение малотоннажных производств метанола, в настоящий момент, является самым перспективным направлением. Набор а, следовательно, и мощность этих сооружений могут увеличиваться в зависимости от реальных потребностей в метаноле. При этом себестоимость продукции и ее качество в значительной степени зависят от выбора технологического процесса. Выбранный ОАО «НОВАТЭК» в случае малотоннажного производства процесс получения метанола не является революционным. Также как в случае крупнотоннажного производства предусматривается двухстадийный процесс: получение синтез-газа и собственно синтез конечного продукта. Однако применительно к месторождению получение синтез-газа оказывается наиболее оптимальным в процессе паровой конверсии метана. Это наиболее простой и экономичный способ, который позволяет исключить подачу кислорода на конверсию природного газа. Данный момент является немаловажным, т.к. отказ от использования кислорода значительно повышает безопасность процесса. Кроме того, из технологической схемы исключается блок выделения кислорода, что значительно снижает капитальные затраты. Технологическая схема производства представлена на рисунке 2.
Рис. 2. Принципиальная технологическая схема малотоннажной установки по производству метанола Смесь водяного пара и природного газа подогревается в теплообменниках-утилизаторах тепла дымовых газов печи риформинга до температуры 537°С и с давлением 2,2 МПа поступает в реакционные трубы реактора риформинга, где на никелевом катализаторе при температуре 850°С протекают реакции конверсии природного газа с водяным паром. Утилизация тепла контактного газа происходит в целом ряде теплообменников рекуператоров, одним из которых является кипятильник колонны разделения воды и метанола. После утилизации тепла контактный газ поступает на прием компрессора, с нагнетания которого под давлением 5МПа направляется в реактор синтеза метанола, где на пяти полках в присутствии медного катализатора происходит синтез метанола. Выбор медного катализатора позволяет проводить технологический процесс при сравнительно мягких условиях – температуре 220°С. На практике это выразится не только в энергосбережении но и в значительном снижении капитальных затрат на оборудование. Полученная в результате синтеза, смесь метанол – водяной конденсат направляется на разгонку в колонну разделения воды и метанола, откуда полученный в качестве дистиллята метанол с концентрацией до 95%, направляется на склад. Существенное снижение капитальных затрат и себестоимости метанола обеспечивает также интегрирование производства метанола в установку комплексной подготовки газа (УКПГ), основного объекта газовых и газоконденсатных промыслов. Отличительная особенность интегрированной технологии по сравнению с традиционной состоит в исключении из технологической схемы ряда технологических узлов: - отпадает необходимость в блоке подготовки сырья, т.к. подготовленный на УКПГ товарный газ месторождений Крайнего севера РФ не содержит соединений серы, отравляющих катализаторы конверсии парогазовой смеси и синтеза метанола; - упрощается блок ректификации метанола-сырца, т.к. его концентрация 80 – 88% достаточна для непосредственного использования в качестве ингибитора гидратообразования; - упрощается блок подготовки химически очищенной воды, т.к. блок первичной очистки воды уже, как правило, имеется в составе УКПГ. При этом максимально используются вспомогательные производства, имеющиеся в составе УКПГ (факельное хозяйство, очистные сооружения, источники электрической энергии, воздуха КИПиА, операторной). Технико-экономические оценки показывают, что за счет интеграции малотоннажной установки получения метанола в состав УКПГ достигается почти трехкратное снижение капитальных затрат, что собственно и делает строительство производств метанола в районах газодобычи рентабельным. Экономические показатели установки производства метанола: 1. Затраты на содержание персонала установки – 19424408 руб.; 1.1. Фонд оплаты труда – 16730660 руб.; 1.2. Отчисления на социальные нужды – 2618748 руб.; 1.3. Льготный отпуск – 75000 руб.; 2. Электроэнергия – 4704833 руб.; 3. Амортизация – 23726124 руб.; 4. Ремонт ОС – 461369 руб.; 5. Всего затрат – 48316734 руб.; 6. Объем произведенного метанола – 12500 т; 7. Себестоимость произведенного метанола – 3865 руб./т; 8. Себестоимость произведенного метанола без аммортизации – 1967 руб./т; 9. Окупаемость проекта с момента ввода в эксплуатацию установки – 30 месяцев (простая) или 39 месяцев (с дисконтом).
В заключении хотелось бы отметить, что, несмотря на значительный срок добычи газа, данная отрасль ТЭК, как и все остальные отрасли, ставила и будет ставить все новые и новые задачи, решение которых часто требуют нестандартного подхода. Главной целью при этом является повышение рентабельности и безопасности процесса, как для человека, так и для окружающей среды. Специалистам ТЭК приходится разрабатывать свои идеи, что-то заимствовать у других отраслей промышленности, превращая рационализацию в бесконечный процесс, требующий в первую очередь комплексного рассмотрения проблемы. При этом общий эффект складывается из деталей, некоторые из которых и были затронуты в данной статье. Директор Департамента добычи и переработки газа и конденсата ОАО «НОВАТЭК» Юнусов Рауф Раисович Заместитель начальника управления по переработке ОАО «НОВАТЭК» Шевкунов Станислав Николаевич |