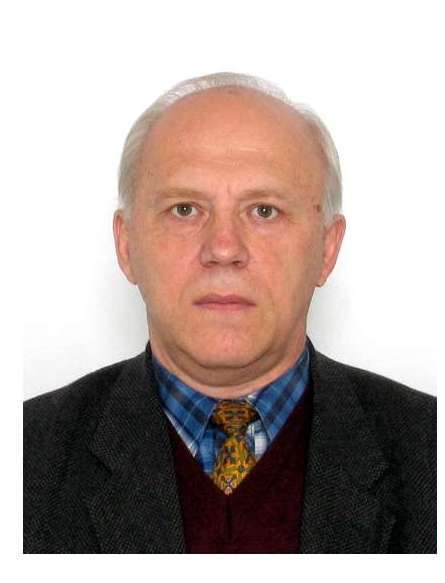
Валерий Шарыкин, кандидат химических наук, эксперт Сегодня на производство метанола в России ориентировано несколько крупных предприятий. Крупнейшее из них – ОАО «Метафракс» в Пермской области, достигшее ежегодного выпуска этого продукта в миллион тонн. Таких объемов достаточно для реализации его стратегии развития переработки метанола в КФК и другие продукты, необходимые внутреннему рынку, но не для того, чтобы поставлять чистый продукт малым и средним потребителям России. Это менее прибыльно; и экспорт по-прежнему будет оставаться важнейшим источником валютных поступлений «Метафракса». Кроме того, создание новых мощностей по производству концентрированного безметанольного формальдегида по технологии "Пернер" позволит предприятию остановить старые формальдегидные установки в Губахе и Орехово-Зуеве, что фактически перекроет существующие поставки продукта производителям формальдегидных смол. Еще одно предприятие – томский «Метанол», с годовым производством 750 тыс. т. Значительная часть продукции здесь также отправляется за границу. В числе его потребителей – Томский нефтехимический завод, где из метанола производят формалин; а также «Газпром», но это скорее вынужденная мера, так как ОАО «Метанол» принадлежит одной из его дочерних компаний. В целом продавать свой продукт на внутреннем рынке предприятие не стремится. У менеджмента предприятия существуют разные идеи использования метанола: от создания производства пентаэритрита для последующего производства пластификаторов-стабилизаторов до использования метанола для производства и переработки полипропилена. Они вряд ли «откроют врата» к продукту мелким потребителям. Одно из крупнейших в отрасли ОАО "Тольяттиазот" в июне 2006 г. достигло мощности производства метанола 1 млн. т. Ориентация предприятия на экспорт привела к созданию на Черноморском побережье метанольного терминала, которому для ввода в эксплуатацию осталось решить лишь организационные проблемы. Если учитывать абсолютную готовность регионов Черного и Средиземного морей потреблять метанол "Тольяттиазота", то разрешение вопроса на уровне местной администрации, скорее всего, не заставит себя ждать. В качестве потенциальных потребителей, вероятно, окажутся также предприятия, производящие каучуки по методу Фаворского, – "Тольяттикаучук", «Нижнекамскнефтехим» и Волжский завод каучуков. Кроме того, "Тольяттиазот" осуществляет свои планы в области производства формальдегидных смол и других продуктов на основе формальдегида. В свою очередь, "Щекиноазот", известный производитель этого продукта (мощность 390 тыс. т в год), реализует свои новые производства формальдегида и КФК. Сегодня здесь их уже производят по технологии ЗАО "Безопасные Технологии" мощностью 80 тыс. т в год в расчете на 37%-й водный раствор формальдегида. "Щекиноазот" ориентирован на экспорт метанола, однако запас в себестоимости, особенно на старой установке, невелик. На предприятии используются две технологические линии: старая, высокого давления (мощностью 220 тыс. т в год), и М-100 (достижимая мощность 170 тыс. т в год). При определенном снижении цен на метанол, что и происходит в настоящее время, эта установка может быть остановлена, хотя причиной вполне может стать и банальный износ техники. В такой ситуации поставки метанола мелким и средним потребителям внутри страны ОАО "Щекиноазот" вряд ли станет планировать даже на перспективу. Новомосковская акционерная компания "Азот", входящая в состав корпорации "ЕвроХим", – еще один производитель метанола в России с мощностью производства 550 тыс. т в год, использующий три технологические линии: - старую, высокого давления, мощностью 150 тыс. т в год; - М-100 мощностью 100 тыс. т в год; - М-300 мощностью 300 тыс. т в год.
Все три производственные нитки не являются современными; разве что по времени пуска М-300 еще относительно новая. Производство метанола для НАК «Азот» не является профильным и работает на экспорт и продажи внутри России. Экономика компании привязана к выпуску аммиака и минеральных удобрений. Рост цен на газ в стране будет снижать экспортные возможности продукта, что может поставить вопрос о целесообразности дальнейшего его производства. Существующая ныне устаревшая технология производства метанола еще одной компании – новочеркасского ЗСП (мощность 300 тыс. т в год) может также не выдержать роста цен на природный газ. В перспективе завод должен будет либо полностью модернизировать это производство, что весьма затруднительно, учитывая использование старых способов производства по технологии высокого давления, либо остановить его в недалеком будущем. Сегодня завод находится в стадии приватизации, которая проходит очень неспокойно. Но в г. Азове продолжается строительство метанольного терминала, который, как предполагается, будет использован и для перевалки новочеркасского метанола.Один из немногих производителей, чья продукция ориентирована исключительно на российский рынок, а именно на производство мочевиноформальдегидных смол, – это ОАО "Акрон", с мощностью 100 тыс. т. Хотя очевидно, что производство формальдегида на старой производственной линии будет постепенно уступать место современным установкам по технологии фирмы "Хальдор Топсе". Второе ориентированное на внутреннего потребителя предприятие – ОАО «Невинномысский Азот», производящее 150 тыс. т метанола в год для производства уксусной кислоты. Небольшое количество метанола продается прежде всего в Черкесск, где есть производство формальдегида. Прорабатывался проект реконструкции производства метанола с наращиванием мощности до 400 тыс. т в год. Однако в компании "ЕвроХим", в состав которой оно входит, метанольный бизнес не является основным, и вполне возможно, что эта реконструкция останется нереализованной. Посмотрим теперь основные направления использования метанола в России в 2004-2005 гг.
Направление использования | Объем использования метанола, тыс. т | Изменение за 2004/05 гг.,% | 2004 г. | 2005 г. | Формалин | 385 | 362 | –5,97 | КФК | 97 | 170 | 75,26 | Изопрен (из изобутана) | 236 | 249 | 5,51 | М-ТБЭ | 186 | 190 | 2,15 | Уксусная кислота | 94 | 97 | 3,19 | Ингибиторы гидратообразования и осушающие агенты в газовой промышленности | 312 | 316 | 1,28 | Прочие направленияиспользования | 75,9 | 77 | 1,45 |
Несложно заметить, что производство изопрена по методу Фаворского в настоящее время стабилизировано прежде всего дефицитом на изобутилен, и в ближайшие годы расход метанола на это направление вряд ли изменится и будет составлять 240-250 тыс. т. Аналогичная ситуация – с метилтретбутиловым эфиром (МТБЭ). Здесь также используется изобутилен, и рост потребления метанола, как и возможный спад, в этом направлении вряд ли будет наблюдаться. Производство уксусной кислоты, единственным производителем которой в России является ОАО "Невинномысский Азот", переживает дефицит. Это достаточно затратное производство, и, мало того, в ближайшее время других производителей этого продукта в России не намечается. Однако планы корпорации "ЕвроХим" нарастить мощность по производству уксусной кислоты в Невинномысске пока остаются нереализованными. Использование метанола в качестве ингибитора гидратообразования и осушающего агента в газовой промышленности, по оценкам специалистов, будет характеризоваться незначительным ежегодным ростом. И его уровень в 300-330 тыс. т сохранится, как минимум, на ближайшие 3-5 лет. Остается сектор применения метанола для производства формальдегида и карбамидоформальдегидного концентрата (КФК), являющегося стабилизированным мочевиной водным раствором формальдегида. Всего в 2005 г. на формальдегид, включая формалин и КФК, пошло 532 тыс. т метанола. Учитывая производство пентаэритрита, число следует сократить примерно на 32 тыс. т. Таким образом, рынок потребителей метанола в производстве формальдегидных смол можно оценить в 500 тыс. т в год. Дальнейший «расклад» продукта трудно отследить, так как мощностями производства смол располагают 83 российские компании; однако только 40 из них в настоящее время занимаются выпуском продукции. При этом около 8-ми предприятий относятся непосредственно к химической промышленности, остальные – производители карбамидных смол – входят в состав деревоперерабатывающей отрасли. Должен заметить, в мировой практике производство формальдегида и КФК концентрируют именно в этой отрасли, образуя так называемый интегрированный цикл, который в России практически отсутствует. В результате десять крупных компаний обеспечивают выпуск почти 75% всего выпуска карбамидных смол, а 43 предприятия вообще выключены из этого производства. Аналогичная картина складывается и в сегменте фенолформальдегидных смол. Их в России могут выпускать на 53-х предприятиях, но на постоянной основе производят только 30. Эта ситуация связана с тем, что в бывшем Советском Союзе формальдегид производили на неэффективных и экологически грязных установках, отгружая большую часть продукта примерно 150-ти предприятиям. В начале 90-х годов, под давлением общественности, такие производства в большей части были закрыты, и только в 2001 г., когда "Метафракс" закупил первую установку по производству КФК у фирмы "Персторп АБ", начался новый период в развитии формальдегидного бизнеса. Вслед за ОАО "Метафракс" его начали развивать другие производители метанола, и в России один за другим стали появляться современные производства очень важной продукции. Вместе с тем по мере развития этого бизнеса существующая сегодня практика производства и продажи стандартного КФК и универсальных смол начала вступать в противоречие с многообразием задач, стоящих перед потребителями при их применении. И потребитель вынужден тратить значительные средства, чтобы приспособить их для нужд своего производства. Выход в такой ситуации многие специалисты ищут в двух направлениях. Новые производители смол, например, приспосабливают свои производства под каждого потребителя, что при частой переналадке масштабных установок под параметры разных смол не очень выгодно. А потребители стараются найти выход в создании интегрированных предприятий, когда производство формальдегида, формальдегидных смол и их применение (прежде всего в производстве ДСП, МДФ, мебели) объединены в рамках одного хозяйственного комплекса – так, чтобы его подразделения, с учетом достаточно короткого срока жизни смол, находились на близких расстояниях и транспортировка тех же смол не занимала длительное время. Однако в современном производстве интегрированные комплексы наиболее выгодны при мощности установок деревоперерабатывающих предприятий по производству ДСП, МДФ от 450 до 900 тыс. м3 продукции. Их в России практически нет. Но западные компании, приходящие на российский рынок, стараются соблюдать это условие. Например, "Кроноспан", обустраивая свой бизнес по лучшим мировым образцам, приобрела у фирмы "Персторп АБ" две установки по производству формальдегида мощностью около 200 тыс. т в год. Скорее всего, метанол для этих установок она будет приобретать в счет экспорта российского продукта в Европу. А как быть более мелким российским производителям? Выходом для них может стать предложение использовать альтернативные мини-установки по переработке метанола мощностью 25, 45, 90 тыс. т в год. Выгодной стоимости таких установок можно добиться упрощением технологической схемы, возможно без возврата рецикловых газов. Стоимость природного газа в России и его доступность в большинстве регионов – хорошая предпосылка для реализации этой идеи. Россия – крупнейшая лесная держава в мире, и такие установки могут послужить делу безотходной и глубокой переработки древесины и ее дальнейшему экспорту. Они же дадут толчок к более широкому использованию метанола на внутреннем рынке, что укрепит позиции его основных производителей и снизит их зависимость от конъюнктуры внешнего рынка. Материал был опубликован в журнале "Химия и бизнес" (№1, 2007) |