ЭФФЕКТИВНАЯ ОБРАБОТКА ДОМЕННЫХ ШЛАКОВ GBFS И GGBFS |
Компания Aumun – известный проектировщик цементных производств. В данной статье рассматривается продукция и услуги компании Aumund.
|
В последние годы цементная промышленность переживает существенный рост операционных издержек, который был вызван, в частности, непрерывно растущими ценами на энергию и давлением экологических лоббистов, направленным на снижение зависимости от ископаемого топлива и сокращение выбросов СО2 в мире. Если учесть, что во время производства одной тонны традиционного портландцемента генерируется почти тонна СО2, то получается, что по объему выбросов парниковых газов цементная промышленность занимает второе место в мире среди отраслей промышленности, уступая в рейтинге мировых загрязнителей лишь энергетике. Ввиду этих факторов нарастает осознание того, что существуют виды топлива альтернативные сгоранию в печи, а также другие сырьевые материалы, которые можно использовать в производстве цемента. Помимо этого нарастает спрос на цемент с добавками, особенно на сорта, включающие в себя гранулированный доменный шлак (GGBFS). С каждой тонной GGBFS, включенного в готовый цемент с добавками, общая выработка СО2 уменьшается приблизительно на 1 тонну… Несмотря на то, что процессы, стоящие за использованием гранулированного доменного шлака (GGBFS) в качестве замещающего сырьевого материала, хорошо изучены, применение этого материала представляет собой серьезную проблему для проектировщиков заводов, начиная с подвода гранулированного шлака и заканчивая внедрением молотого материала в цемент с добавками. В целом, вести надежную обработку данных материалов очень сложно, поскольку они существуют в различных разновидностях, от чрезвычайно мелкосыпучих (GGBFS) до очень вязких, склонных к скоплению и засорению, а также слипанию при хранении (GBFS). Гранулированный доменный шлак также чрезвычайно абразивен, его скорость износа примерно в пять раз больше, чем у цементного клинкера в аналогичных сборках. Компания Aumund Group, в которую входят B&W и Schade, понимает эти сложности. Она разработала инновационные решения для многих из этих проблем обработки, при этом особой регулировке подвергаются имеющиеся конструкции, специально созданные для того, чтобы соответствовать конкретным требованиям этих новых областей применения. Сочетая традиционные преимущества своей продукции с новыми концепциями, и повышая тем самым уровень гибкости конструкций и сокращая расходы на осуществление проекта, Aumund Group предлагает быстрые и эффективные решения, которые позволяют клиентам извлекать прибыль из краткосрочной рыночной позиции и максимизировать прибыльность предприятия.
Производство Гранулированный доменный шлак является побочным продуктом сталелитейного производства, в частности, производным резкой закалки расплавленного шлака, извлеченного из доменной печи, в холодной воде. В результате этого процесса создается гранулированный, стекловидный, однородный и некристаллический материал, обладающий цементирующими свойствами. В зависимости от вида процесса, около 25% или более сырьевого материала, использованного в доменной печи, превращается в шлак. Таким образом, по всему миру производится огромное количество материала, и рынок по-настоящему ограничен лишь количеством гранулирующего оборудования на сталелитейных заводах, а также наличием транспорта до цементных заводов. После этого гранулированный материал высушивается и измельчается в дробилке. Полученный порошок, известный как гранулированный доменный шлак (GGBFS), можно внедрять в цементные материалы. Уже много лет GGBFS используется в качестве дополнительного цементирующего материала в портландцементе, в качестве минеральной примеси или компонента цемента с добавками. GGBFS может заменить 35-85 процентов портландцемента в составе цементной смеси. При этом соответствующим образом сокращаются выбросы СО2, что сказывается на экологии очевидно благоприятным образом. 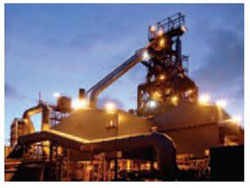 Используя GGBFS для частичной замены портландцемента, можно извлекать выгоду из энергии, потраченной в производстве шлака, а также из возникающих в результате этого преимуществ, связанных с повышенными цементирующими свойствами шлака. Для измельчения шлака с целью замены им цемента требуется лишь около 25% энергии, расходуемой в производстве обычного портландцемента. Если бы гранулированный материал не использовался, то весь производимый шлак невозможно было бы эффективно или экономически оправданно использовать в других процессах, например в качестве наполнителя, и он неизбежно бы оказывался среди мусора.
Поэтому, максимальным образом используя GGBFS в составе цемента, промышленность не только значительно сокращает выработку парниковых газов и энергопотребление, но также и уменьшает размеры мусорных свалок, что приводит к существенному снижению общего уровня загрязнения окружающей среды в соответствии с общими целями Инициативы Устойчивого Развития Компаний-производителей цемента. |
Рыночные условия В условиях современного быстро меняющегося международного рынка способность быстро реагировать на изменчивость рынка и использовать преимущества краткосрочной рыночной позиции приобретает большое значение, если операторы хотят получать максимальную прибыль и возвращать вложенный капитал. В этом свете использование замещающего сырьевого материала, такого как гранулированный доменный шлак, должно считаться частью общего плана по сокращению расходов и улучшению окружающей среды. Достаточно часто эти требования становятся взаимоисключающими. Тем не менее, в цементной промышленности сочетание замещающих сырьевых материалов и альтернативных видов топлива делает ситуацию выигрышной для всех участников. Использование этих материалов также в значительной степени зависит от цен на топливо и доступности сырьевых материалов на территории конкретного региона, а также спроса на конкретные свойства готового цемента с добавками. Это может оказать существенное влияние на экономический состав, при этом в любом случае требуя гибкости и быстрых темпов строительства новых заводов. Аналогичным образом в цементной и иных отраслях промышленности широко используются другие материалы, например гипс, полученный в результате десульфуризации дымовых газов (FGD), который также известен как синтетический гипс. Ценообразование подчиняется воздействию рынка, поэтому соответствующим образом меняется и связанная с этим экономика. В тех случаях, когда все эти условия объединяются в одно общее уравнение, изменчивость рынка может серьезно и быстро изменить связанную экономику конкретных решений. При таких условиях производителю цемента приходится производить сложные расчеты, оценивая срок возврата инвестиций в новый завод, предназначенный для обработки альтернативного топлива или замещающих материалов. Таким образом, сокращенные издержки на установку и гибкость становятся основными факторами, влияющими на принятие таких решений. Точно так же, после решения этих вопросов, огромное значение для извлечения максимальной финансовой выгоды в пределах четко определенного уровня расходов и срока работы приобретает период запуска нового завода в эксплуатацию. 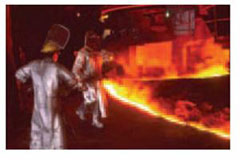 В данной статье рассматриваются требования, которым необходимо соответствовать при обработке гранулированных и измельченных материалов в цементной промышленности. Однако подобные решения можно использовать и в автономных помолочных станциях или на участках измельчения, установленных прямо на сталелитейном заводе. Основные вопросы проектирования завода
Помимо пригодности нового завода к основным операциям существуют и другие вопросы, которые могут повлиять на принимаемое решение. В случае, когда необходимо получить максимальную финансовую выгоду, вытекающую из использования замещающего сырьевого материала или альтернативных видов топлива, критерии проектирования завода и бюджетные ограничения будут существенно отличаться от требований к основному процессу. К тому же, различные способы размещения оборудования и пригодность для работы с другими материалами и в других областях являются привлекательным сочетанием, благодаря которому связанная экономика предполагаемого проекта претерпит значительное изменение. Хорошо, когда завод можно использовать в других целях. Таким образом, снижается рискованность инвестиций. Несомненно, важным фактором строительства нового завода является стоимость общестроительных работ. Это не только серьезные расходы, но также, разумеется, невозможность повторения этого этапа и задержки при строительстве объектов, для которых требуется уделять серьезное внимание проектированию, планированию и экскаваторным работам. За некоторыми исключениями расходы, связанные с доставкой альтернативных материалов по железной дороге, слишком велики, поэтому единственным общепринятым вариантом является доставка автотранспортом. Подвод материала на самосвалах становится причиной легкого пылевого загрязнения, поэтому для минимизации воздействия на окружающую среду необходимо вводить меры контроля. Для успешной и рентабельной установки нового завода необходимо заниматься этими ключевыми вопросами, чтобы оказывать благоприятное воздействие на окружающую среду и соответствовать требованиям технологического процесса. |
Опыт компании Aumund Group Aumund Group более 80 лет занимается проектированием специализированных систем для обработки сыпучих материалов, предназначенных к использованию в сталелитейной и цементной отраслях промышленности. Компания уникальна тем, что может уверенно предлагать механические транспортные системы для работы с гранулированным доменным шлаком, представленным как в виде сырья, так и в измельченном состоянии. Данный опыт включает в себя и работу с очень горячими материалами на заводах по обработке цемента, шлака и окатышей. При этом используется общепринятая концепция ячейкового конвейера Aumund, характеризующаяся конструкциями высокого уровня разработки, которые были специально созданы для работы в этих агрессивных и требовательных условиях. Для демонстрации высокого профессионализма в инженерной области Aumund установила самый крупный в истории ковшовый конвейер для работы с железом горячего прессования. Высота подъема – 110 м (расстояние между центрами – 150 м), скорость работы – 210 тонн в час. Конвейеры такого типа спроектированы для работы с материалом при температуре 900 оС в инертной среде для сохранения качества продукта. Транспорты для клинкера и вертикальные ковшовые элеваторы производства Aumund лидируют в данной отрасли промышленности, обладая заметными технологическими преимуществами, в основе которых непрерывное и всестороннее развитие. Отталкиваясь от концепции ячейкового конвейера, Aumund разработала специализированные конвейеры для охлаждения отливок на заводах окатышей со встроенными перфорированными лотками, через которые пропускается окружающий воздух и после этого выводится посредством широкой системы трубопроводов. Данная система способствует охлаждению окатышей с температуры 250 оС до 100 оС. Помимо лоточных конвейеров и вертикальных элеваторов Aumund также поставляет оборудование для питателей, работающих в тяжелых условиях, и механизмы выгрузки из силоса, а в 2001 году к Schade Group был добавлен обширный ассортимент отвалообразователей и реклаймеров в виде цепных скреперов, привнеся на этот рынок 125 лет непрерывной работы в данной области. Также в 2002 году компания Aumund приобрела английскую B&W Mechanical Handling Ltd., благодаря чему уже имеющееся обширное портфолио группы компаний пополнилось питателем Samson Surface Feeder и более гибкими решениями на основе оборудования для мобильного складирования и загрузки кораблей. В стандартном ассортименте Aumund можно найти различные предложения, от питателей для подачи сырого или гранулированного шлака на склад методом отсыпки, вывоза со склада и подачи материала на дробилку и поднятие готового измельченного материала к конечному силосному хранилищу: изготовленное на заказ решение, невозможное без длительного опыта.
Выше: питатель Samson подает материал прямо на ленточный конвейер, установленный под углом 90 градусов. Подвод и поднятие Серия B&W, входящая в ассортимент питателей Samson, предлагает идеальное решение по подводу как сырого, так и гранулированного шлака. Питатель Samson принимает сырой шлак прямо из сталелитейного завода для последующей его обработки на сторонней дробилке. Samson подает материал непосредственно на ленточный конвейер, установленный под углом 90 градусов, что позволяет идеально осуществлять передачу материала на ленту конвейера, минимизируя при этом риск засорения, поскольку существует значительный риск содержания в материале слишком крупных и посторонних элементов. На ленточном конвейере шлак в первую очередь просеивается с целью удаления инородного материала, а затем дробится до размера частицы, пригодной для использования в качестве заполнителя в дорожном строительстве. Ниже: Самосвалы подвозят импортируемый гранулированный шлак к новой установке на испанском заводе Holcim Carboneras 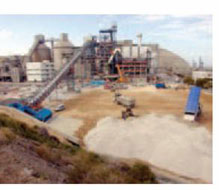
Свойства шлака могут быть самыми различными, и, чтобы система была максимально производительной при любых условиях, производительность механизма Samson автоматически регулируется относительно фактической скорости обработки (оценивается конвейерными весами) и текущими потребностями дробилки. Система Samson аналогичной конструкции может использоваться для подвода гранулированного шлака на цементном заводе или измельчающей установке напрямую от самосвалов или ковшового погрузчика. Самосвалы подвозят импортируемый гранулированный шлак к новой установке на испанском заводе Holcim Carboneras, после чего материал выгружается на складе. Оттуда его забирает ковшовый погрузчик, использующий машину Samson в качестве промежуточного хранилища с механизмом регулирования подачи (при помощи планировочного отвала), и подает на следующий наклонный ленточный конвейер, который поднимает шлак к высоко расположенному бункеру дробилки. |
Поскольку гранулированный шлак склонен к спеканию во время хранения, создавая крупные и жесткие комки, Samson должен быть оборудован сортировочной решеткой на входе (как показано выше) или на выходе, чтобы эти крупные комки не попали в бункер дробилки и не создавали риск серьезного повреждения дробилки. В качестве альтернативы решению, в котором используется хранилище, на некоторых заводах, где недостаточно пространства для хранения больших объемов материала, подвод гранулированного шлака осуществляется при помощи самосвалов. В подобной ситуации питатель Samson является идеальным вариантом, обеспечивая подвод материала, промежуточное хранение и контроль за скоростью подачи в пределах одного механизма, при этом устраняется необходимость в глубоких котлованах и накопителях. Таким образом, сокращаются расходы на общестроительные работы, и повышается степень гибкости системы. 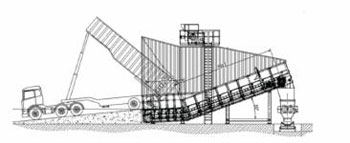
Решение проблемы слишком крупных комков изображается на вышеуказанном чертеже, где показан механизм Samson установленным на выходе несъемным двухосным поворотным рассевом, установленный на выходе. Поворотный рассев компактен и может быть установлен между машиной Samson и последующим конвейером, как показано на чертеже ниже. 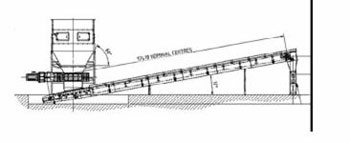
С последующего конвейера материал можно поднять к силосу дробилки при помощи ковшового элеватора Aumund BW-Z, который будет рассмотрен далее. Сочетание механизма Samson и рассева нельзя назвать новой конструкцией. На следующем рисунке изображается довольно нестандартный пример, где рассев выгружает материал прямо на магистральный поверхностный конвейер, обрабатывающий добытый известняк. На самом деле существует два альтернативных решения, например Samson может быть совмещен с вертикальной конвейерной системой «Лента на боковой стене», которая используется на новой установке для обработки гранулированного шлака в компании Holcim Germany. В этой конструкции Samson используется для приема гранулированного шлака прямо от самосвалов обычным образом. Производительность регулируется при помощи стандартного планировочного отвала, однако материал выгружается непосредственно на горизонтальный подающий участок ленточного конвейера, установленного на боковую стену и имеющего форму буквы «S». Размещенный на данной странице рисунок (справа) отображает схему расположения оборудования для данного проекта, где горизонтальная разгрузочная станция подает гранулированный шлак прямо на силос, установленный на большой высоте. Рисунок ниже показывает стандартную ленту вертикального участка, установленную вдоль внешней стены и закрепленную только в верхней части.
Стандартная лента вертикального участка, установленная вдоль внешней стены и закрепленная только в верхней части Однако подобные конвейеры печально известны тем, что их сложно прочищать. Также приходится использовать конвейеры по возврату просыпанного материала, предназначенные для сбора и переноски такого материала к подающему механизму главного конвейера. Aumund Group также предлагает альтернативный вариант – ковшовый элеватор Aumund BW-Z, обеспечивающий поднятие гранулированного шлака прямо к силосу и представляющий собой полностью закрытую и защищенную от просыпания материала систему. Вертикальный ковшовый элеватор можно совмещать с любым транспортным или подающим конвейером. Однако при совмещении с питателем Samson, всю установку можно сделать компактной и чистой. Как в классической системе, работающей на поверхности… используется короткий ленточный конвейер для перемещения материала от механизма Samson к загрузочной воронке вертикального ковшового элеватора. |
Ковшовый элеватор производства Aumund – идеальное решение для транспортировки GBFS к силосу, которое может поднимать материал на высоту 10-60 м и работать со скоростью более 600 тон в час. Также возможна работа в других областях, где температура материала может составлять до 400 оС. В этих механизмах используется одна центральная кованая цепь, они идеальны для работы с агрессивными материалами. Однако для работы со шлаком добавляются специальные свойства, обеспечивающие надежную работу в течение долгого времени. • Конец и загрузочная воронка с резиновой обкладкой • Гибкие резиновые панели • Полностью облицованные ковши • Зубчатые измельчители (на каждом 10-м шаге) • Дополнительные возможности доступа с целью проверки • Цепи предварительно смазаны герметиком Все эти функции предназначены для придания механизму устойчивости против износа и продления срока службы при минимальном техническом обслуживании и максимально редких простоях. Резиновая обкладка зарекомендовала себя как решение для входного и выходного участков механизма. Однако для вертикального кожуха традиционные листы из штампованной стали были заменены сварной решеткой с гибкими резиновыми панелями, которые устойчивы против износа и не слипаются с материалом. Каждый ковш полностью облицован износостойкими стальными плитами, которые накладываются на ковш со всех сторон, а также на зубья каждого 10-го ковша, благодаря чему в остаточном материале создается отчетливая дорожка. Это позволяет минимизировать износ всей ленты конвейера. Тем не менее, главной деталью этих элеваторов является массивная кованая конвейерная цепь с запечатанными и предварительно смазанными болтами, которые формируют основную цепь механизма и являются ключевым фактором долгосрочной надежности. Лабиринтное уплотнение, внедренное в боковые элементы цепи, эффективно предотвращают проникновение материала в болты и втулки и, после эффективной смазки, продлевает срок службы цепи на целых 60% в сравнении с традиционной негерметичной конструкцией, не прошедшей предварительную смазку. В ходе эксплуатации цепи не смазываются повторно, и для них не требуется специальное повседневное обслуживание, однако выбор заранее нанесенного смазывающего материала приобретает большое значение в том случае, когда данной конструкции необходимо реализовать полностью. Нижеприведенная схема отображает повышение уровня износостойкости, которого можно достичь в этой конструкции. Фактический срок службы цепи более чем удваивается. 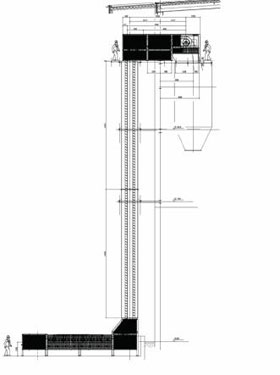
Выше: Горизонтальная разгрузочная станция подает гранулированный шлак непосредственно к высоко расположенному силосу
Повышение уровня износостойкости: голубая линия изображает стандартную цепь без герметика и предварительной смазки, красная линия – герметичная цепь со смазкой класса премиум. Линия посередине – результаты использования других сортов смазочного материала. |
Разгрузка силоса После доставки гранулированного шлака наверх к силосу или бункеру дробилки складируемый материал следует извлекать и, возможно, взвешивать для последующего дозирования, которое осуществляется весовым питателем Aumund. Данный механизм, используя весовой рельс, совмещает в себе точность, скорость и надежность. Рельс установлен на датчики нагрузки, служа тем самым опорой для пластины конвейера или валиков ячейкового конвейера и измеряя действующую нагрузку с высокой степенью точности. Если измерять давление, оказываемое материалом вдоль известного расстояния, и отслеживать скорость движения цепи, то можно в реальном времени осуществлять непрерывное регулирование скорости работы, чтобы соответствовать требованиям технологического процесса. Конструкция подобных весовых питателей основана на зарекомендовавшей себя концепции ячейкового конвейера типа KZB. Они обеспечивают надежную работу в течение долгого времени в самых тяжелых условиях. Для обработки вяжущих материалов предпочтительным решением является изогнутый пластинчатый конвейер типа BPB, который также доступен в вариантах с весовыми рельсами, предназначенными для пропорционального дозирования или систем с контролируемой скоростью подвода материала. Обладая по-настоящему массивной конструкцией, подобные питатели подходят для работы в самых сложных условиях. Эффективным решением для извлечения вяжущего материала из силоса является Aumund Centrex. Данная система предотвращает образование мостов и засорение, выбирая материал по краям силоса. При этом используются логарифмические манипуляторы, установленные на поворотном транспортере, как показано на рисунке напротив. Centrex предлагается с несколькими вариантами установки, в том числе возможность обеспечения надежной выгрузки поворотной воронкой, а также перемещение материала по принципу «первый на входе, первый на выходе». Поскольку разгружающий манипулятор работает строго по краю силоса с небольшим недобором, то разгрузке силоса ничто не мешает, и можно гарантировать надежное извлечение материала. Для более крупных силосов можно использовать «Поворотный разгрузчик», в который входит разгрузочное колесо с несколькими манипуляторами, укрепленное на поворотном транспортере. Данная установка обслуживает силосы диаметром до 4,5 м и обрабатывает самые различные вяжущие материалы. Тем не менее, она широко используется при работе с FGD или синтетическим гипсом как на электростанциях, так и на цементных заводах, поскольку гипс такого рода можно использовать в качестве непосредственного заменителя природного гипса, который необходим для изменения свойств цемента на последней стадии измельчения. Отсыпка и выгрузка Для крупных проектов, где необходимо обрабатывать значительные объемы гранулированного шлака, идеальным решением являются рельсовые отвалообразователи со стрелой серии Schade. Отвалообразователь, установленный на бельгийском заводе CCB Italcementi, принимает шлак с ленточного конвейера, переданный от самосвала и направленный к стреле передвижного отвалообразователя, со скоростью 600 тонн в час, благодаря чему можно создать отвал емкостью 35,000 м3. Выгрузка из отвала осуществляется портальным рамочным реклаймером Schade, оборудованным специальной скребковой цепью (рассмотрено ниже), которая передает материал на идущий параллельно отвалу ленточный конвейер со скоростью 300 тонн в час, чтобы соответствовать требованиям процесса. Процедуры отсыпки и выгрузки ведутся автоматически с помощью встроенных систем управления. При этом используются разветвленные полевые, контрольно-измерительные и защитные системы, благодаря которым возможна работа по безлюдной технологии. Понимая потенциальные проблемы износа, возникающие при работе с этим чрезвычайно абразивным материалом, компания Schade разработала цепь с внешними подшипниками специально для работы в подобных трудных условиях. Внешние ролики устанавливаются на удлиненные болты цепи при помощи шарикоподшипников двойной точности. Также используется лабиринтное уплотнение с пластичным смазочным материалом. Поэтому смазка на ролике может держаться в течение всего срока службы и не требовать последующего технического обслуживания. Цепи с внешними роликами также значительно понижают уровень шума в механизме, их часто используют в системах, расположенных в чувствительных районах, поблизости от городских застроек. Помимо специальных роликов на внешних подшипниках используются специальные скребковые погрузчики, оборудованные износостойкой резающей поверхностью. Schade изготовила некоторые из крупнейших в мире установок этого типа, в которых скорость выгрузки достигает 2400 тонн в час, а длина рельсового пути составляет до 65 м. Помимо продольного портального реклаймера Schade предлагает цилиндрические накопители со встроенными отвалообразователями, а стрелы реклаймеров устанавливаются на стандартные колонны. Цилиндрические накопители представляют собой экономичной решение, применимое в условиях ограниченного пространства, также они обеспечивают самые низкие издержки в пересчете на одну тонну хранящегося материала. Системы хранения и выгрузки производства Schade могут поставляться в полной сборке вместе с рельсами или оборудованием для организации подвода автомобильным транспортом на основе питателя Samson или пластинчатым конвейером типа BPB. Подобные установки – это полноценные системы обработки. Аналогичным образом систему хранения Schade можно соединить с цементным заводом, использующим, к примеру, ковшовые элеваторы Aumund, силосы и извлекающее оборудование, в результате чего создается полная комплексная установка, включающая в себя все этапы, от подвода материала до измельчения. Помимо приведенного здесь конкретного примера, имеющего отношение к обработке гранулированного шлака Schade, предлагает множество альтернативных конструкций, например изображенную ниже консольную стрелу. Полупортальная конструкция; одна сторона портала поддерживается приподнятой стеной здания, которая одновременно несет нагрузку и увеличивает эффективную вместимость хранилища в расчете на метр длины здания. Для смешивания на цементных заводах таких материалов как известняк с гарантией выпуска однородного материала Schade также предлагает мостовой реклаймер с активной бороной и возвратно-поступательным движением зубовых брусьев. Материал отбирается с лицевой поверхности отвала, поэтому смешение образцов осуществляется на всех слоях. Системы мостовых реклаймеров могут быть продольными вместо портальных, также они могут основываться на цилиндрических конструкциях (см. ниже). 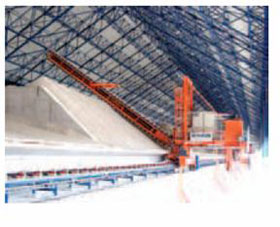
|
Поднятие измельченного шлака Ранее были подробно рассмотрены подвод и хранение гранулированного шлака, полученного от сталелитейного завода. Но этим процесс не ограничивается. После измельчения шлака, обычно в вертикальной дробилке, готовый материал, который называют GGBFS, следует поднять к силосу для последующего смешивания или прямого распределения. Технологические характеристики гранулированного шлака очень похожи на показатели готового цемента, и здесь Aumund является рыночным лидером, используя свои ленточные/ковшовые элеваторы BW-G. Механизмы устанавливаются на высоте более 140 м. скорость перемещения составляет до 1500 тонн в час, мощность двигателя – до 450 кВт. Гибкие мобильные решения Если бюджет не позволяет установить специализированную станционарную систему обработки, то экономичным решением для хранения и даже вывоза шлака могут стать мобильные решения, которые предлагает B&W.
Штабелеукладчик Stormajor принимает гранулированный шлак прямо от расположенного в Южном Уэльсе (Великобритания) сталелитейного завода. Он поставляется самосвалами для нового измельчающего завода под управлением Civil and Marine Slag Cement. Штабелеукладчик Stormajor включает в себя принимающий материал питатель Samson и радиальную стрелу для передачи материала прямо к отвалу. Вся система устанавливается на стандартные подвижные шасси. При длине стрелы 23 м механизм создает отвал высотой до 12 м, позволяя хранить большое количество материала с минимальным передвижением механизма. Данная система была поставлена в 1998 году, она обработала многие тысячи тонн шлака и зарекомендовала себя как эффективное решение. 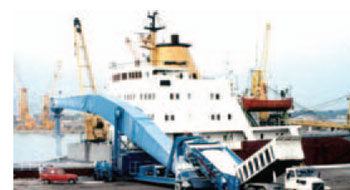 Stormajor также можно эффективно использовать для загрузки барж и вагонов, являясь в этом случае гибкой инвестицией. Помимо подвижных штабелеукладчиков B&W также предлагает передвижное оборудование для загрузки кораблей, в которое включен питатель Samson, предназначенный для прямой погрузки от самосвала на корабль.
Если использовать передвижные системы обработки, то пропадает необходимость в дорогостоящих строительных работах. Также создается максимальная гибкость, которая позволяет операторам полностью использовать преимущества краткосрочных рыночных условий. При этом финансовые ресурсы достигают своего максимума, а инвестиционные риски минимизируются без ущерба для производства или снижения уровня надежности. Модификация и модернизация Помимо проектирования и производства новых заводов и установок Aumund также предлагает уникальный сервис модернизации не только для продуктов Aumund Group, но также и для сходных машин от других поставщиков. Клиентам, использующим сервис модернизации, предоставляется возможность преобразовать имеющиеся механизмы при помощи, например, цепей, ковшей, валов, шкивов, приводов и других важнейших компонентов производства компании Aumund, которые позволят им насладиться легендарной надежностью Aumund при минимальных расходах и ущербе для завода. Aumund предлагает быструю поставку запасных частей от своих сервисных центров, расположенных по всему миру, а также гарантирует высочайший уровень послепродажного обслуживания и поддержки. 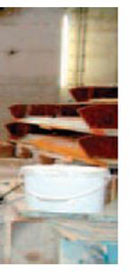 Ремонт на месте работы при помощи исключительно оригинальных запасных частей и компонентов от Aumund. |
Заключение В рамках данной статьи были подробно рассмотрены инновации Aumund, которые стали результатом приверженности компании к непрерывным НИОКР. В особенности они посвящены процессам обработки сырого, гранулированного и измельченного доменного шлака. Данные продукты можно поставлять на заводы, являющие либо автономными механизмами, либо частью интегрированной системы обработки. При этом Aumund также предлагает инженерную поддержку на стадиях проектирования и местного производства связанных конструкций, эстакад для конвейеров, перегрузочных башен и аналогичных вспомогательных систем. Aumund предлагает своим клиентам всестороннее обслуживание, от концептуальной схемы завода и проектирования до итогового пуска завода в эксплуатацию, а также непрерывную сервисную поддержку от головного офиса компании, расположенного в Германии. Помимо этого у компании имеются дочерние предприятия и представительства во Франции, Швейцарии, Польше, Индии, Китае, Бразилии, Гонконге, США и Великобритании. Помимо этих стран Aumund обладает разветвленной сетью агентов, прошедших полный цикл обучения работе с продукцией Aumund Group. Они предоставляют местную поддержку и прямой доступ к услугам сбыта на местах и сети поддержки. По-настоящему международная группа, обладающая обширным опытом и ресурсами и предоставляющая по всему миру эффективные и экономичные решения по обработке насыпных материалов, которые изготовляются специально под конкретные требования клиентов. С анализом российского рынка металлургических и топливных шлаков и с анализом оборудования для производства цемента на основе шлаков Вы можете познакомиться в отчетах Академии Конъюнктуры Промышленных Рынков «Рынок шлаков в России» и «Анализ оборудования для производства шлакощелочного вяжущего».
www.newchemistry.ru |
|
|