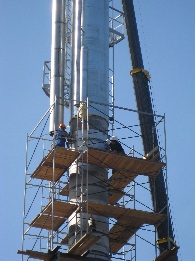
Однако, начиная с 2000-х годов эту роль взяло на себя ЗАО "Безопасные Технологии" и последние годы успешно с этим справляется. Первая промышленная установка с использованием железо-молибденового оксидного катализатора была создана в 1958 году на Новосибирском химическом заводе (ныне ОАО "Химпласт"). На ней впервые в СССР начали производить безметанольный формальдегид. Однако эта идея, которая соответствовала мировым тенденциям того времени, не была поддержана и более таких производств в СССР не строилось. В настоящее время эта установка демонтирована. На рынок эта компания вошла недавно, создав в 2002 году установку мощностью в 9000 тонн мочевиноформальдегидного концентрата (в пересчете на 37%-ный формальдегид) в Карелии на модульной установке, которую планируют предлагать для поставки деревоперерабатывающим предприятиям. В августе-сентябре 2005 года ЗАО "Безопасные Технологии" пустили в эксплуатацию на Горловском концерне "Стирол" (Украина) установку мощностью 26 тысячи тонн в год КФК-85. Каждая установка производства КФК-85, разработанная и поставленная фирмой ЗАО «Безопасные Технологии», была выполнена с учётом особенностей и требований конкретного производства. Возможны варианты, как наружного размещения установки, так и внутри производственного здания. Основными особенностям установок КФК-85 ЗАО «Безопасные Технологии» являются: - Низкая стоимость строительно-монтажных работ за счет размещения основного оборудования на нулевой отметке, без необходимости задействования металлоконструкций зданий/сооружений;
- Высокий уровень автоматизации с дублированием опасных параметров;
- Применение аппарата каталитического дожига вредных выбросов;
- Собственное производство нестандартного оборудования, позволяющее контролировать качество на всех стадиях выполнения проекта.
- Низкая металлоемкость установки и следовательно капитальные затраты.
Технологические отличия: - Длительный срок службы катализатора: 3 года и более (11-15 месяцев у других поставщиков). Причем на катализаторах любого поставщика;
- Низкий расход электроэнергии;
- Качество КФК существенно лучше, чем у других поставщиков. Буферная емкость 7-9, содержание уроновых соединенией менее 1% (у других поставщиков до 10%);
- Содежание метанола 0,1%.
Эти данные подтверждаются многолетним опытом проектирования, строительства и эксплуатации установок производства КФК-85. - КФК-85 производимый на установке в ОАО «Щекиноазот» обладает буферной емкостью менее 9 мл, что недостижимо на установках других производителей.
- Установка по производству формалина в ОАО «Уралхимпласт» работает 3 года без замены катализатора.
Основные объекты по КФК-85 и смолам выполненные ЗАО «БЕЗОПАСНЫЕ ТЕХНОЛОГИИ» - 2002 г. ОАО «Карелия ДСП» (Медвежьегорск, Карелия). Цех карбамидных смол/установка КФК-85 (проект и строительство «под ключ»).
- 2003 г. ПК «Электрогорскмебель» (Моск. обл.). Паровая котельная на термомасле. (проект и строительство «под ключ»). Первая в России технологическая котельная с использованием в качестве теплоносителя термомасла прессов цеха ДСП, производящая технологический пар для производства смол.
- 2004 г. ПК «Электрогорскмебель» (Моск. обл.). Рабочий проект технического перевооружения производства смол. Первая стадия строительства. Расширение мощности производства до 40 тыс. тонн смолы в год, с полной заменой технологического оборудования, автоматизацией и механизацией производства.
- 2005 г. ПК «Электрогорскмебель» (Моск. обл.). Техническое перевооружение производства смол. Вторая стадия строительства.
- 2004 г. - 2005 г. ОАО «Концерн Стирол» (Украина). Установка КФК-85 мощностью 40 тыс. тонн в год. Проектирование, изготовление и поставка оборудования, шеф-монтаж. Данный проект стал возможен в результате тендера, в котором, помимо ЗАО «Безопасные Технологии», принимали участие фирмы Haldor Topsoe (Дания) и Perstorp (Щвеция).
- 2006 г. ОАО «Щекиноазот» (Щекино, Тульской обл.). Установка КФК-85 мощностью 80 тыс. тонн в год. Проектирование и строительство «под ключ». Данный проект стал возможен в результате тендера, в котором, помимо ЗАО «Безопасные Технологии», принимали участие фирмы Haldor Topsoe (Дания) и Perstorp (Щвеция).
- 2008 г.-2009 г. ООО «Гексион-Щекиноазот». Проектирование и строительство цеха фенолоформальдегидных смол.
- 2009 г. – 2011 г. ООО «Krono Holding - Шарья» (Костромская обл.). Проектирование производства карбамидоформальдегидных смол мощностью 160 тыс. тонн в год. Проект в стадии реализации.
- 2010 г. – 2011 г. ООО «Сибметахим» (г. Томск). Проектирование технического перевооружения производства карбамидоформальдегидных смол мощностью 75 000 т/год и установок производства карбамидоформальдегидного концентрата (КФК-85) и малометанольного 55% формалина суммарной мощностью 120 000 т/год (по 37% формалину). Объект в стадии проектирования.
- 2010 г. – 2011 г. ЗАО «ПДК «Апшеронск» (Краснодарский край). Проектирование производства карбамидоформальдегидных смол мощностью 58 000 т/год, установки производства карбамидоформальдегидного концентрата КФК-85 мощностью 40 000 т/год (по 37% формалину) c возможностью форсирования до 50 000 т/год, для производства МДФ. Объект в стадии проектирования.
Шарыкин В.Г. www.newchemistry.ru |