В 1999 году Западная Европа переработала 32% всех потребительских пластиковых отходов – на этом статистические данные Европейской ассоциации производителей пластмасс пока заканчиваются. Столь значительным успехам способствовало, в первую очередь, законодательство. Система Duales, или «Зеленая точка», действующая в Германии, предписывает перерабатывать как минимум 60% потребительских упаковочных материалов. В Италии обязательным является переработка использованных бутылок для машинного масла. В настоящее время Еврокомиссия разрабатывает стандарты для автотранспортных средств и электроники. 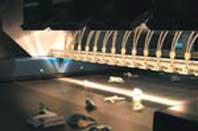 Но законы, как правило, ничего не говорят о дальнейшей судьбе восстановленных пластмасс. По словам Нейла Майне, главы технического центра Европейской ассоциации производителей пластмасс в Брюсселе, лишь малая доля их – 11% - поступает в повторную переработку. 14% восстановленного пластика экспортируется за рубеж,. 21% сжигается в ТЭЦ. Выступая на конференции по технологиям рециклинга Identiplast, регулярно проводимой в Брюсселе, г-н Майне отметил, что на самом деле европейский бизнес по переработке использованных материалов переживает не лучшие времена. Однако некоторые тенденции внушают оптимизм: новые технологии, запускаемые в производство, обещают обеспечить значительно более высокую долю вторично использованного пластика, выйдя за пределы его классического использования в котельном топливе. Эти технологии включают разделение ПВХ с помощью растворителя, расслоение и сортировка материалов, из которых изготовлены приборные панели автомобилей, высокоскоростная автоматическая идентификация смол в потребительских упаковочных материалах.
Восстановление ПВХ с помощью растворителей Две недавно разработанных технологии разделения с помощью растворителей, использующихся в коммерческом производстве в Европе, позволяют восстановить компаунды ПВХ по цене, значительно ниже цены производства первичных аналогов. Технология «Vinyloop» компании Solvay SA и нескольких ее партнеров по производству восстанавливает ПВХ из размолотой проволоки после удаления из нее меди. Материал содержит равные доли ПВХ и резины, таким образом, сначала они разделяются электростатическим сепаратором Hamos GmbH для того, чтобы затем получить материал, состоящий из 85% ПВХ и 15% резины. За этим следует растворение ПВХ в растворе метиэтиленкетона. Специальная фильтрация позволяет удалить натуральные и синтетически волокна, сшитый полиэтилен, вулканизированную резину, полипропилен, полиуретан, бумагу, метал и другие примеси. В раствор пускается пар, приводя к оседанию ПВХ в форме небольших шариков. Растворитель дисстилируется, конденсируется и затем вторично используется. После высыхания шарики ПВХ приобретают текучесть и удельный вес, сходные с аналогичными показателями первичного компаунда. 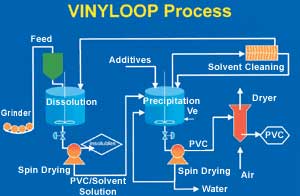 Восстановленный ПВХ обычно бывает серого цвета - из-за неоднородности проволочного размола - и сохраняет все добавки и стабилизаторы, содержавшиеся в изначальных компаундах. Свойства смол не ослабляются, поскольку процесс проходит без воздействия высоких температур: максимальный уровень – 240 градусов по Фаренгейту. Но самое главное преимущество технологии в том, что ПВХ не должен проходить специальной подготовки. «Vinyloop – это прибыльный бизнес, поскольку у нас нет необходимости гранулировать материал», говорит Бернард Ванденхэнде, инженер по переработке использованных материалов компании Solvay, участвовавший в разработке технологии. 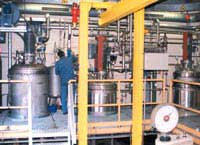 Технология Vinyloop подходит для всех видов ПВХ-отходов, в частности кабелей и настилов полов, и создает компаунд, который потенциально может иметь такое же использование, что и его первичный аналог. Однако Vinyloop не позволяет смешивать несколько видов сырья, к примеру, проволочный размол или измельченный настил. Свинцовые стабилизаторы в кабеле и оловянные в ПВХ-покрытии совместимы с себе подобными, но несовместимы друг с другом – они придают материалу коричневый цвет. Крупный опытный завод переработки пластмасс по технологии Vinyloop в Брюсселе работает с 1999-го года. В итальянской Феррере начато строительство первого завода промышленного масштаба. Ожидается, что он будет открыт к декабрю текущего года. По словам представителей компании Solvay, стоимость предприятия оценивается в $7,2 миллиона, а его производственная мощность - 22 миллиона фунтов ПВХ в год по цене 13 евро за фунт. Второй завод мощностью 20 миллионов ПВХ в год планирует построить производитель брезента компания Ferrari SA из французского Пиж ан Руссийон. На нем будут восстанавливаться ПВХ и ПЭТ волокна из брезента, используемого для палаток, покрытия грузовиков и уличных плакатов. Завод начнет работу к 2004 году. Восстановленный ПВХ может быть использован в производстве настилов и других промышленных товаров. Представители Solvay сообщили, что в планах компании добиться еще около 10 лицензий на строительство новых заводов и основать несколько совместных предприятий. Будущее проектов зависит от результатов, которые покажет итальянский завод. Чтобы быть рентабельным, завод должен производить, по меньшей мере, 22 миллиона фунтов ПВХ в год. Другая технология переработки с помощью растворителя позволяет удалить ПВХ с системы автомобильных проводов. Эта технология разрабатывалась немецкой Delphi Automotive Systems в сотрудничестве с Университетом Вутертала. На рынок ее вывела 3 года назад Wietek GmbH, немецкий автопереработчик. По словам Вольфганга Дигманна, директора Delphi по экотехнологиям и переработке материалов, технология компании позволяет получить вторичные ПВХ компаунды, себестоимость которых на 20% ниже аналогичных показателей первичных материалов. В технологии Delphi используются растворители из сложных эфиров и кетона в значительно меньших количествах, чем требуется для технологии Vinyloop. Он не растворяют ПВХ, но размягчают его до консистенции йогурта, облегчая его отделение от медного провода. Восстановление последнего с лихвой окупается. Wietek получила патент на технологию отделения пластмассы от растворителя в центрифуге. Поскольку провод не размолот, процесс проходит без образования пыли, отсутствует необходимость фильтрации и отделения металла. Технология позволяет ежегодно восстанавливать из проволочного лома около 500 000 фунтов компаундов ПВХ, пригодных для дальнейшего использования. Как утверждается, данная технология применима и к другим материалам. Wietek также запатентовала процесс переработки с помощью растворителей АБС-пластика и смеси АБС и акрила, восстановленных из раздробленных решеток радиатора и металлизированных свинцом деталей.
Центрифужное разделение Суть еще одной новой европейской технологии - в комбинированном применении теплового воздействия и быстрого вращения для разделения слитых пластиков, как из разбитых на мелкие куски формованных автомобильных деталей. Этот процесс, также разработанный Delphi совместно с Университетом Вупертала, начинается с закладывания целых деталей в корзину центрифуги и подогревания их горячим азотом, при этом для того, чтобы предотвратить расщепление веществ выкачивается кислород. Температура не должна выходить за рамки плюс-минус 5 градусов, так чтобы более легкоплавкие материалы плавились и таким образом, отделялись. 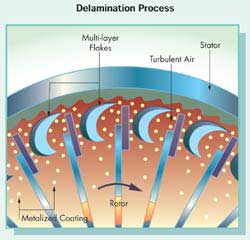 Процесс был протестирован на партии сырья весом в несколько килограммов и, как отмечают представители компании Delphi, тестирование показало: данный процесс требует в пять раз меньше энергии, чем производство первичного нейлона – 2,7 Квт-ч на фунт против 13.6 Квт-ч на фунт. Delphi также восстанавливает полипропилен из отделки внутренней вертикальной опоры автомобилей, состоящей из нейлонового материала, укрепленного полипропиленом. Этот материал не плавится, поэтому он остается в центрифуге, когда из нее вынимается расплавленный полипропилен. Технология также позволяет выделить поликарбонат из металлизированных покрытий на CD-дисках, оставляя металл в центрифуге и производя чистый, пригодный к вторичному использованию поликарбонат. Поскольку технология не требует добавления каких-либо компонентов (единственное непременное условие – высокая температура), процесс проходит без образования вредных веществ, таким образом, избавляя от необходимости их утилизации. Еще одна европейская технология, объединяющая температурное воздействие и центрифужную силу – это процесс отслоения во время вращения, предложенный Result Technology AG. В нем используется высокоскоростной ротор, вращающийся со скоростью 600 футов в секунду внутри ребристого барабана, создавая на поверхности ротора (статора) поперечную силу в 3500 гауссов. Эта сила разрывает хлопья заранее разрубленного многослойного пластика. Металлические слои преобразуются в небольшие шарики, в то время как твердый пластик сохраняет форму, а гибкий растягивается и удлиняется. Различие форм облегчает механическое разделение материалов. Технология Result Technology на настоящий момент используется 14 компаниями в Европе и на Дальнем Востоке. Производства различаются по выработке - от 2.200 до 11000 фунтов вещества в час - и применяют вышеназванную технологию, главным образом, для разделения металлопластиковых композитов, таких как покрытый алюминием полипропилен или полиэтиленовые пленки, или металлизированные ПВХ блистерные упаковки. Некоторые виды использования технологии Result Technology отличаются от стандартных: комплекс мощностью 50000 фунтов в час, принадлежащий германской Retec Recycling und Umwelttechnic GmbH, занимается разделением - среди прочих отходов - материалов из разобранных потребительских компьютеров. Шведская компания восстанавливает металл из скрапа, порубленного в автоматическом измельчителе. Третья компания, использующая технологию Result Technology, разделяет измельченные материалы из деталей приборных панелей на заводе недалеко от Ганновера. Приборные панели состоят из твердых компонентов - АБС, слоя полиуретановой пены и мягкого покрытия, часто из ПВХ. Смесь представляет собой 15-миллиметровые кусочки материалов. После отслоения в акселераторе при скорости кромки ротора в 280 футов в секунду, частицы пены полиуретана становятся диаметром 3.5 мм, куски АБС- 1,2 мм и хлопья ПВХ – 0,25 мм. Затем их разделяют на 99% чистый АБС и 97% чистый ПВХ. Дополнительное механическое разделение может обеспечить 100% чистоту материалов. Эксплуатационные расходы составляют 5 евро за фунт. Последняя разработка Result Technology позволяет совместить центрифужное отслаивание и разделение по плотности. Прошлой осенью компания разработала блок, монтирующийся сверху деламинатора. В нем имеется воздухоотражатель, разделяющий легкие и тяжелые фракции, в частности алюминий от пластика. Смесь представляет собой 95% полиэтилен в шестислойном композиционном материале из целлюлозы, полиэтилена и нейлона. Акселератор расслаивает их при скорости кромки ротора в 360 футов в секунду. Хлопья полиэтилена не меняются в размере, оставаясь от 5 до 25 мм, в то время как целлюлоза и нейлон растягиваются до 40 мм и более и могут быть извлечены с потоком воздуха через крышку деламинатора. Полиэтиленовые хлопья 99% чистоты выпадают снизу. В апреле немецкая компания Polyamid 2000 AG установила на новом заводе систему из 12 сенсорных центрифуг производства Baker Process, США (ранее известной как Bird Machine Co.).Центрифужная технология применяется для восстановления нейлона из потребительского покрытия. Планируется, что завод будет перерабатывать 240 миллионов фунтов использованного покрытия в год, производя 20 миллионов фунтов первичного нейлона 6 и 26 миллионов фунтов нейлона 66 и других технических пластмасс. Polyamid 2000 работает с загрязненными использованными покрытиями. На первой стадии шерсть, полиэтилен, полипропилен и другие ненейлонные покрытия идентифицируются раман-спектроскопом и удаляются из смеси. Ненейлонные покрытия сжигаются, чтобы высвободить энергию для работы завода. Тем временем нейлонные покрытия измельчаются, и полученный материал проходит через двухступенчатую центрифужную систему. Все 12 центрифуг имеют диаметр 35 дюймов и пропускную способность 260 фунтов в час. Восемь задействованы на первой ступени разделения, 4 - на второй. Сначала от нейлона отделяется основа из наполненной карбонатом кальция резины. Она продается для производства компаундов или сжигается для выделения энергии. На второй стадии продолжается удаление примесей из нейлона 7, который затем деполимеризуется, дистиллируется и реполимеризуется в новый нейлон. Ожидается, что в этом производстве себестоимость первичного нейлона будет такой же, как и у обыкновенного
Новые возможности распознавания Новая система идентификации веществ в пластиковых отходах в ближнем инфракрасном диапазоне, представленная LLA Laser Labor Adlershof является, по словам разработчиков, первым инфракрасным устройством, способным правильно идентифицировать смолы в черной пластиковой стружке. Данные исследований, обнародованные немецкой DaimlerChrysler AG на Identiplast показывают, что устройство может быть использовано для отделения хлопьев от раздробленных автомобильных деталей. По запатентованной технологии волны длиной от 1,5 до 2, 2 микронов идентифицируют АБС, смесь ацетилсалициловой кислоты и поликарбоната, акриловую смолу, полипропилен, полистирол, полиуритановую пену, ПВХ и нейлон. Мультиплексированная система LLA соединяет 32 датчика к одному спектрометру и сканирует хлопья на конвейерной ленте шириной 1 метр, движущейся со скоростью до 2-х метров в секунду. Хлопья отделяются воздушными потоками. LLA также работает с системой датчиков, предоставленных токийской Hamamatsu Co. В системе используются волны длиной до 2,5 микронов и специальная смесь из индия, галлия и арсенида в качестве фотодетектора. В Берлине небольшой конвейер работает на заводе Steremat Montageautomatisierung. Более крупный будет запущен в сентябре. Хлопья на нем будут сортироваться на восемь фракций со скоростью 2200 фунтов в час, перемещаясь на конвейерной ленте 10 x 15 метров. Линия в Steremat - это первая система Laser Labor Adlershof, способная идентифицировать и сортировать хлопья. На настоящий момент система может работать только с огрубленными хлопьями, чтобы провести идентификацию черных полимеров, однако компания ищет новый светлый источник, который избавит от необходимости огрубления пластика. Американская National Recovery Technologies объявила на Identiplast о технологии идентификации, разработанной ею совместно с Dow Chemical Co. Технология позволяет разделить стандартные полиэтилентерефталатовые бутылки и бутылки из ПЭТ, содержащие защитные материалы, такие как нейлон. Технология работает на высокой скорости и применима как к целым бутылкам, так и к хлопьям. До получения патента NRT отказывается раскрывать детали процесса. SORTEChnology 3.0 – название немецкого завода в Гановере, производящего сортировку в системе DSD и переработку материалов. Основанный 18 месяцев назад, это первый в мире полностью автоматизированный завод такого профиля (для краткости его называют «Sortec»). Владельцем является Der Gruene Punkt–Gesellschaft fur System Technologie mbH. Завод осуществляет сортировку упаковок по типам: жестяные, алюминиевые банки, картонные коробки для напитков, емкости из ПЭТ, ПЭ, полистирола и смесей. Затем проводит автоматическое гранулирование ПЭ и полистирола и образует агломерат из полиолефинов, используемый в доменных печах. Более сложная автоматическая сортировка смол производится на заводе A.R.T. GmbH в Триере, Германия. Здесь автоматически разделяются картонные коробки для напитков и упаковки, изготовленные из ПЭ, ПЭТ, полипропилена и полистирола. На обоих заводах применяются конструкции идентификации смол Autosort NIR, производимые норвежской TiTech Autosort, имеющей офисы в США. Автоматическая выработка составляет 9900 фунтов в час более, чистота восстановленных ПЭ, полипропилена и полистирола превышает 95%, полиэтилентерефталата – 98%. В настоящее время на разделительном заводе COREPLA в Монтелле устанавливается новейшая NIR система TiTech. Она позволдяет разделять светло-голубые и прозрапчные бутылки из ПЭТ. Шесть блоков Autosort на двух параллельных конвейерах сначала убирают весь ПЭТ из разных бутылок, затем разделяют цветной и прозрачный и на последней стадии отделяют светло-голубые бутылки для воды от бутылок других цветов. Ожидается, что производительность системы составит 22000 фунтов в час.
Автор: Ian H.Shut Источник: Plastics Technology |