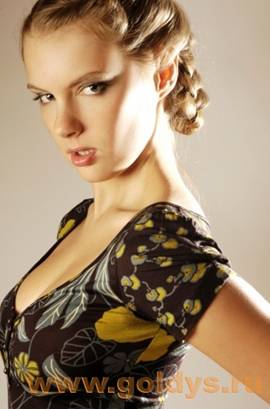
Вискозный процесс. Получение текстильных материалов по вискозному методу проводится в несколько стадий: 1) подготовка целлюлозы (дробление и получение пульпы, т.е. суспензии целлюлозы в воде); 2) добавление к пульпе каустической соды с последующим созреванием вискозного раствора (конечный раствор называется вискозой); 3) формование вискозного волокна через коагуляцию (осаждение) вискозного раствора в осадительную ванну; 4) обработка готового волокна (окраска и сушка).1 К достоинствам процесса и полученных в результате его проведения материалов относятся: 1) доступность сырья (любая древесина); 2) сравнительно низкая себестоимость (производство обычного вискозного штапельного волокна по трудоемкости примерно эквивалентно производству синтетических волокон и 6,5-7 раз ниже, чем соответствующий показатель хлопковолокна); 3) широкие ассортиментные возможности (трикотаж, гардинно-тюлевые изделия, обивочно-декоративные ткани); 4) хорошие результаты смеси с природными волокнами (снижение количества отходов в 2-3 раза и увеличение производительности на 10-15%); 5) готовый материал обладает высокими санитарно-гигиеническими качествами. В числе недостатков: 1) длительный срок подготовки и созревания технологических растворов; 2) экологический риск техпроцесса (в ходе его проведения выделяется целый ряд опасных компонентов, многие из которых по свойствам подобны военным отравляющим веществам высшей категории вредности); 3) готовое волокно нестойко в жестких условиях отварки, отбелки и мерсеризации, в силу чего может быть использовано в смесях с хлопком в количестве, не превышающем 10-15% общего объема; 4) резкое снижение прочности готовых изделий во влажном состоянии. Коротко о рынке. Прирост потребления вискозных (гидратцеллюлозных) текстильных волокон на мировом рынке наблюдался только в период с 1950 г. по 1960 г., после чего его уровень «застыл» независимо от изменений цен на другие полимерные продукты.1 В период между 1970 и 1984 гг. цена вискозных волокон составляла 70% от стоимости хлопка, а в 1985 г. - уже 130-140%. Основными причинами роста цен, по мнению западных экспертов, стали ужесточение требований к экологической безопасности производства, рост выпуска хлопковолокна и затраты, связанные с переводом производственных мощностей в развивающиеся страны, прежде всего, государства Юго-Восточной Азии. В настоящее время стоимость одной тонны готового материала на основе вискозного волокна, исходя из цены хлопка, составляет 1800-2200 USD.4 Вискозные волокна в основном используются в качестве технологической добавки при производстве смесовых тканей на основе хлопка и синтетических волокон. Добавки вискозы могут достигать 25% при производстве рубашек и сорочек. В других изделиях присутствие вискозы обычно ограничивается 10%. Основные типы вискозных волокон. К ним относятся: 1) вискоза (regular rayon или viscose), для которой характерна невысокая прочность во влажном состоянии; 2) вискозное модальное волокно (High Wet Modulus (HWM) rayon, polynosic rayon или ModalTM), отличающееся более высокой прочностью во влажном состоянии; 3) высокомодульное вискозное волокно (High Tenacity Rayon), у которого этот показатель выше, чем у модального волокна; 4) штапельное вискозное волокно (Microfibers Rayon), для которого характерны многие свойства хлопковых волокон. Смотрите, кто пришел! Это традиционное семейство пополнилось вискозным волокном нового типа, полученным по ММО-процессу. Последний получил свое название по основному компоненту - метилморфолиноксиду (ММО), добавляемому к пульпе или порошку целлюлозы в ходе техпроцесса. Производство по этому методу в промышленном масштабе началось в 1992 году в США. Готовая гидратцеллюлоза вышла на рынок под разными именами, присвоенными ей компаниями - владельцами брэндов: лиоцелл (lyocell) или лайоцелл в английском произнесении, ньюцел (newcell), тенсел (tencel), орцелл (orcell). Ниже все эти волокна мы будем называть лиоцеллом. Существуют промышленные модификации вышеприведенных торговых марок в зависимости от потребностей текстильного производства (волокна разной плотности, степени фибрилляции и др.). ММО-процесс. Получение текстильных материалов в этом случае проводится по следующим этапам: 1) подготовка целлюлозы (дробление и получение пульпы или порошка в зависимости от технологии); 2) добавление к пульпе или порошку целлюлозы метилморфолиноксида (ММО); 3) смешение в экструдере с подогревом до 100оС; 3) подача раствора в осадительную ванну с последующей окраской и сушкой.2 Отметим достоинства этого процесса и полученного материала: 1) повышение прочности во влажном состоянии; 2) совместимость со всем спектром натуральных и синтетических волокон; 3) хорошая и стабильная окрашиваемость волокна, особый блеск в результате окраски; 4) экологически безопасная технология производства; 5) надежность в носке материалов на основе этого волокна; 6) в равной степени эффективное использование при производстве тканых и нетканых материалов; 7) высокие потребительские свойства, аналогичные свойствам хлопковолокна, и даже превышающие их по прочности, качеству прокраса и поверхностным эффектам; 8) тактильный эффект натурального шелка, притом, что это волокно более гигроскопично, чем натуральный шелк. |