Компания Krauss-Maffei произвела поставку первой линии для производства армированных термопластичных труб (RTR Reinforced Thermoplastic Pipes) в Китай. Линия рассчитана на производство труб диаметром от 75 до 180 мм, состоящих из трех слоев (Фото 1). Внутренний слой экструдируется из ПЭ-100. Средний слой образуется намоткой ленточного каркаса, усиленного арамидным волокном, в направлении максимальных напряжений. Как средний, так и внешний защитный слой изготавливаются из одномодального ПЭ- 80. В результате усиления высокопрочным арамидным волокном RTP-трубы способны выдерживать давление разрыва до 100 бар. В Китае их применяют в нефтепроводах для перекачки нефтегазоводной смеси из устья скважины на нефтеперерабатывающее предприятие. 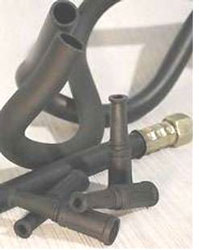
Фото 1: структура RTP-труб. а: внутренний слой из ПЭ 100, b: армированные ленты, с: внешний слой из ПЭ 80
Ранее трубы для этих целей изготавливались из стали. Сегодня предпочтение отдаётся армированным трубам из термопластичных материалов, т.к. они намного легче стальных, что упрощает их транспортировку и монтаж. Кроме того, RTP-трубы коррозионноустойчивы и выдерживают сильные колебания температуры, что позволяет применять их в регионах с экстремальными климатическими условиями. Помимо транспортировки сырой нефти, RTP-трубы используются также в газопроводах и высоконапорных водопроводах. Первые RTP-трубы были изготовлены в конце 80-х годов XX века компанией Wavin, а их промышленное использование началось с 1996 г. В 2003 г. компания Krauss-Maffei приобрела ноу-хау компании Kuhne Anlagenbau (Санкт-Августин, Германия), которая занималась производством RTP-труб с 1998 г. Сегодня компания Krauss-Maffei предлагает технологические линии для рентабельного производства RTP-труб в диапазоне диаметров от 75 до 400 мм. 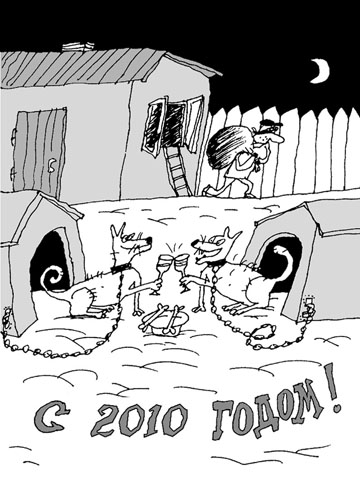 RTP-трубы на оборудовании Krauss-Maffei производятся в два этапа. Сначала изготавливается лента, пронизанная филаментными нитями (Фото 2). При этом нити подаются с раздаточного устройства, вмещающего до 90 отдельных катушек, сортируются и натягиваются посредством т.н. - валка. Затем они проходят через сушильную печь станции армирования, где удаляются остаточная влажность и технологические добавки, остающиеся на нитях после изготовления. Тормозной механизм отводит нити и одновременно, совместно с оттяжным приспособлением, придает натяжение, необходимое для прохождения через ленточную станцию. На ленточной станции (Фото 3) нити вводятся в термопластичную матрицу. Экструдер КМЕ 45-30 B/R компании Krauss-Maffei загружает расплав в специально разработанную форму для нанесения армирующего слоя.
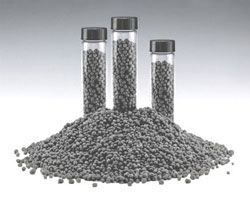
Фото 4: перед обмоткой армированной лентой внутренний слой трубы проходит станцию нагрева. После погружения в расплав рассортированных и отделенных друг от друга нитей армированная лента попадает в охлаждающую ванну со встроенным полировочным каландром. Ширина и толщина ленты контролируется лазером. На данном этапе оттяжное приспособление дополняется вспомогательным оттяжителем. Оттуда лента попадает в полуавтоматическое двойное намоточное устройство со встроенным режущим механизмом. Перед намоточным устройством расположен накопитель, рассчитанный на 30 м ленты. В зависимости от назначения, ленты могут быть толщиной до 3 и шириной до 160 мм и содержать до 90 одиночных нитей. Для усиления может применяться как ПЭТ-волокно, так и арамидное волокно. Матрица может изготавливаться из ПЭСП, ПЭВП или ПЭНП. Внутренний слой трубы из термопластичного материала изготавливается на экструдере типа КМЕ 90-30 B/R, трубная экструзионная головка со спиральным распределителем RKW 34 для труб диаметром до 250 мм. Перед обмоткой армированной лентой труба проходит станцию нагрева (Фото 4), после чего лента с помощью соответствующего устройства наматывается на трубу (Фото 5). Вокруг подвижной трубы со скоростью 36 мин-1 вращаются 2 катушки с максимальным диаметром 2 м и весом 650 кг каждая. Лента накладывается по диагонали вплотную. Для повышения прочности второй слой ленты накладывается под прямым углом к первому, закрывая все стыки. Для этого производственная линия должна быть оснащена, по меньшей мере, двумя обмоточными машинами. Скорость линии составляет до 5 м/мин. В завершении с помощью трубооблицовочной головки KM D ST G 250 компании Krauss-Maffei, совместимой с экструдером KNE 75-30 B/R Krauss-Maffei, накладывается внешний защитный слой из ПЭ-80. Затем труба проходит калибровку и охлаждение. Фото 5: трубообмоточная станция
Из труб, изготовленных таким образом, на стройплощадках монтируются трубопроводы. При этом многослойная структура трубы требует специфической техники соединения. Для этой цели фирма Friatec разработала простой и надежный в применении способ на основе электрофузионной сварки. Концы трубы, которые необходимо соединить, сначала снабжаются специальными сварочными муфтами, а затем соединяются с армированной электромуфтой с закладным нагревательным элементом. Система производства RTP-труб позволяет воспользоваться преимуществами термопластичных труб и в тех областях применения, где требуется высокое давление. С точки зрения стоимости, RTP-трубы уже могут конкурировать со стальными трубами в диапазоне диаметров до 160 мм. Последние разработки нацелены на замену органических волокон стекловолокном. Это позволит еще больше сократить расходы на производство RTP-труб. ________________________________________________ Krauss-Maffei Kunststofftechnik GmbH Krauss-Maffei-Str. 2, D-80997 Munchen (Germany) Tel.: +49 89 8899-4194, Fax:+49 89 8899-3092 www.krauss-maffei.com |