Смолы из поливинилиден фторида (PVDF) уже на протяжении пятидесяти лет широко применяются для изготовления отделочных пленок наружного применения и красок, устойчивого к коррозии оборудования, и огнеупорной изоляции электронных устройств. Тем не менее, их применение в формовании из расплава было ограниченным. Материал обладает долговременной устойчивостью к воздействию ультрафиолетовых лучей; отличной устойчивостью к воздействию агрессивных химикатов, таких как кислоты, хлор и бром; а также высокой термической стабильностью для увеличения огне- и дымостойкости. Чередование атомов водорода и фтора в молекулярной цепи придает дополнительные свойства, такие как: устойчивость к истиранию, радиационную стабильность, а также более низкую температуру плавления, чем у большинства фторполимеров, что позволяет использовать более низкие температуры обработки, близкие к тем, что используются для полиолефинов. Другими преимуществами являются более низкая плотность, чем у большинства фторполимеров, и хорошая прочность на разрыв при температуре до 1500 C/302 F. Несмотря на этот впечатляющий набор свойств, PVDF всегда вели борьбу за то, чтобы сбросить с себя ярлык материала, применяемого для особых ниш. Arkema Inc. проделала немалый объем исследовательской работы для того, чтобы изменить гомополимер PVDF с целью повышения эффективности обработки и соответственного расширения области применения. Новые марки PVDF компании Kynar с высокой прочностью расплава (HMS) являются смолами с разветвленными цепями, которые обладают высокой прочностью расплава и устойчивостью против провисания и натеков в ходе экструзии, что делает их идеальными кандидатами для экструзионного выдувного формования, горячего формования и производства плёнки, получаемой экструзией с раздувом. Хотя для этих технологий доминирующими всегда были товарные смолы, такие как полиолефины, PET, и ABS, в настоящее время существует растущий интерес к конструкционным смолам. Способность видоизменять архитектуру полимера для того, чтобы уравновесить вязкость расплава с помощью эластичности, позволяет этим смолам из PVDF быть конкурентоспособными в области затрат, сохраняя, в то же время, эксплуатационные характеристики материала. Марки HMS компании Kynar обладает сбалансированными реологическими свойствами, что позволяет использовать их при реализации многих технологий и получении многих применений по сравнению с традиционными смолами PVDF. Они сочетают хорошую прочность расплава и коэффициент вытяжки с устойчивостью против провисания и натеков и деформационным упрочнением. Их особенно рекомендуют для использования при экструзионно-выдувном формовании, горячем формовании и получении пленки экструзией с раздувом. Их также можно использовать при экструзии жёстких пенополиуретанов и потенциально при пряжении волкон. Кроме того, их механические и физические свойства остаются сопоставимыми со свойствами традиционных смол Kynar. Arkema производит смолы HMS на экспериментальной опытно-промышленной установке, и проверяет материалы на мощностях основных заказчиков. Новые возможности Какую выгоду могут получить от этих новых материалов, предприниматели, занимающиеся обработкой пластмасс? Выдувное формование позволяет производить полые детали, такие как бутылки и крупные емкости для хранения химических веществ. Химические прокладки и поддоны являются основными рынками для изделий, производимых горячим формованием, в то время как экструдированные защитные покрытия предназначены для пленок. Присутствие на рынке материалов конструкционных марок, которые можно использовать для этих применений, ограничено. Большинство таких материалов разрабатывалось для литьевого формования, экструзии профиля и покрытия провода. Они обладают технологическими параметрами (вязкостью расплава, эластичностью расплава, температурой плавления и термической стабильностью), которые лучше приспособлены к использованию данных технологий. Они не очень хорошо приспособлены для использования технологий, при которых имеет место сильное растяжение по одной или двум осям. Хотя использование модифицированных шнеков с более низкой степенью сжатия при экструзии и более длинной переходной зоной может помочь избежать тормозящего течения, из-за которого происходит деградация смолы, основным препятствием в области выдувного формования остается формирование заготовки для выдувания. Ранее использованию конструкционных смол препятствовала избыточная осадка, то есть, неспособность расплава противостоять силе тяжести и силам выдувания до и во время формования. Различные решения, такие как аккумуляторы, которые можно использовать для того, чтобы снизить воздействие скорости экструзии на формирование заготовки, а также черновое выдувание и выдувное формование с растяжкой, являются дорогостоящими альтернативами, которые требуют постоянной регулировки для достижения оптимального режима. Горячее формование широко использовалось для производства крупных и сложных компонентов. Если раньше его использование ограничивалось применениями, для которых не требовалось исключительной размерной стабильности и жестких допусков, то в наши дни современные технологии и усовершенствованные смолы позволяют формовать сложные детали с жесткими допусками. Горячее формование продолжает отвоевывать территорию у других технологий, включая компрессионное и литьевое формование. При использовании горячего формования основными параметрами являются реологические свойства, которые должны быть хорошо сбалансированы для того, чтобы соответствовать требованиям формования листа, а также вакуумной растяжки и формования. К числу самых существенных свойств смол относятся контроль вязкости и прочность расплава. В частности, высокая прочность расплава признается существенной для использования данной технологии для того, чтобы обеспечить более широкое технологическое окно и более высокую устойчивость против провисания и натеков. Благодаря своим повышенным показателям прочности расплава и устойчивости против провисания и натеков, HMS компании Kynar обладают большим потенциалом для вакуумного формования тонких листов во вкладыши, открытые поддоны и теплоизолированные детали емкостей для хранения химических веществ. Высокая стабильность рукава 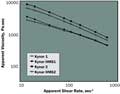 Рис. 1—Новые разветвленные смолы с высокой прочностью расплава (HMS) компании Kynar обладают той же или меньшей вязкостью, что и сопоставимые стандартные PVDF компании Kynar при 2100 C, даже при том, что у марок HMS ниже MFR (скорость течения расплава). При получении пленки экструзией с раздувом сбалансированные реологические свойства также важны, поскольку они позволяют обеспечивать высокую степень раздува, превосходную стабильность рукава, и улучшенные оптические свойства при малой толщине. Данная технология требует относительной низкой вязкости для достижения простоты обработки и исключения появления дефектов поверхности, таких как «акулья шкура», в то время как здесь необходимы достаточная прочность расплава и устойчивость к провисанию и натекам для того, чтобы выдерживать массу рукава и выдерживать контролируемое двухосное растяжение, позволяющее производить тонкие пленки. В области выдувной пленки смолы с высокой прочностью расплава от Kynar расширяют технологическое окно и сохраняют свойства смолы PVDF, такие как прочность на разрыв, стойкость к ударным нагрузкам, а также устойчивость к воздействию химических веществ. Они обладают превосходным соотношением прочности расплава и удлинения, высокой устойчивостью к провисанию и натекам при низкой вязкости, а также высокой продольной усадкой экструдируемого потока. Эти улучшенные свойства были получены благодаря введению разветвления с образованием длинной боковой цепи. Одним из основных применений является производство огнестойких покрытий для внутренней отдели самолетов, получаемых с помощью экструзии.
Сопоставимость новых PVDF В исследовании Arkema сопоставляются реологические свойства двух пар образцов PVDF с различными молекулярными структурами. Первая пара состоит из двух существующих промышленных марок, Kynar 1 и Kynar 2 с двумя различными молекулярными весами и скоростями течения расплава 23.6 и 4.8 г/10 мин при 2300 C, соответственно. Во вторую пару вошли вновь разработанные Kynar HMS 1 и Kynar HMS 2 с двумя различными молекулярными весами и скоростями течения расплава 15.5 и 2.5 г/10 мин при 2300 C. На Рисунке 1 представлены кривые соотношения вязкости и скорости сдвига для образцов Kynar и Kynar HMS при 2100 C. Образцы с более высокой текучестью (Kynar 1 и Kynar HMS 1) дали практически одинаковые профили вязкости по всему диапазону скорости сдвига, что показывает, что эти две смолы можно обрабатывать при одинаковых условиях, несмотря на различия в значениях MFR (которые получены в условиях низкой скорости сдвига). 
Рис. 2—Новые PVDF с высокой прочностью расплава имеют более высокую прочность расплава при сохранении достаточных параметров коэффициента вытяжки заготовки (DDR) при 2300 C. Кривые для образцов с более низкой MFR (Kynar 2 и Kynar HMS 2) показывают, что промышленные образцы обладают более высокой вязкостью расплава, чем Kynar HMS 2 на протяжении всего диапазона скорости сдвига. В обоих случаях данные по вязкости расплава противоречат данным по MFR, поскольку образцы HMS оба имеют более высокую вязкость (в соответствии с испытанием MFR) по сравнению с промышленными образцами (Kynar 1 и 2). Это несоответствие возникает из-за различий в эластичности расплава новых смол, которая намного выше для образцов HMS, чем для образцов Kynar 1 и 2. Прочность расплава и коэффициент вытяжки (DDR) для образцов при 2300 C даны на Рис. 2. Kynar HMS 1 дает прочность расплава, в четыре раза превышающую прочность расплава Kynar 1, несмотря на одинаковую вязкость в условиях сдвига. Точно так же, прочность расплава Kynar HMS 2 в два раза превышает прочность расплава Kynar 2. Увеличенная прочность расплава говорит об улучшении рабочих параметров при горячем формовании и лучшей устойчивости к провисанию и натекам при экструзионно-выдувном формовании и получении пленки экструзией с раздувом. Различия в коэффициенте вытяжки показаны на Рис. 2. Образцы Kynar HMS сохраняют довольно высокую способность к вытяжке (хотя и меньшую, чем у промышленных образцов), а также высокую прочность расплава, что делает их хорошо приспособленными для экструзии моноволокон, волокон и плёнок, получаемых экструзией с раздувом, где обычно необходим коэффициент вытяжки заготовки 10:1 или выше. Максимальные значения, получаемые при 2300 C, намного выше, чем коэффициенты вытяжки заготовки, которые обычно наблюдаются при горячем формовании или выдувном формовании.
Лучшая устойчивость к провисанию и натекам 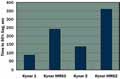
Рис. 3— Лучшая устойчивость PVDF с высокой прочностью расплава к провисанию и натекам при 2270 C указывает на их лучшую пригодность для горячего формования и выдувного формования. Устойчивость к провисанию и натекам является самым важным свойством при использовании горячего формования. Она также может быть существенной при экструзионно-выдувном формовании. Устойчивость к провисанию и натекам является параметром, зависящим от температуры, и ее измерение предполагает оценку формы устойчивости расплава к ползучести при отсутствии нагрузки. Тем не менее, определить количественные показатели нелегко из-за обилия используемых методов испытаний, условий и геометрий объекта. В данном исследовании листы помещались над концом стеклянной трубы в шесть дюймом шириной и оставлялись до уравновешивания температуры. Используя градуировку, нанесенную на трубу, снимались показания осадки нагретой смолы как функции от прошедшего времени. Моментом окончания испытания стало оседание листа на 50% глубины стеклянной трубы, условно это значение названо “50% осадкой” на Рис. 3. Диаграмма показывает относительную устойчивость к провисанию и натекам для стандартного образца Kynar и нового образца Kynar HMS при 2150 C для пары с низкой вязкостью и при 2280 C для пары с высокой вязкостью. Для каждой пары новые разветвленные образцы намного менее подвержены осадке, чем их неразветвленные аналоги, на что указывает больший срок достижения 50% осадки. Для пары с низкой вязкостью необходимо всего 80 сек., чтобы Kynar 1 достигла 50% осадки, против 240 секунд, которые потребуются Kynar HMS 1. Устойчивость к провисанию и натекам для пары с высокой вязкостью дает время 50% осадки 130 сек. и 350 сек. для Kynar 2 и Kynar HMS 2, соответственно. Измерение объемной вязкости расплавленных полимеров не слишком распространено в отрасли производства пластмасс из-за сложности процедуры испытания и сложности его проведения. Тем не менее, это практически самая чувствительная технология для определения последствий изменений в молекулярной структуре полимеров в области реологических свойств. Разветвление цепи можно определить только с использованием объемной вязкости, хотя осцилляционные измерения могли бы дать ценную информацию в случаях, когда распределение молекулярных масс одно и то же. Принцип измерения объемной вязкости основан на растяжении полимера в расплавленном состоянии с различной скоростью. Когда полимер признается линейным, а это означает, что все цепи полимера свободны от каких-либо узлов разветвления, растяжение образца будет однородным, и не будет наблюдаться никакого деформационного упрочнения, поскольку цепям ничто не мешает проскальзывать поверх друг друга. В результате сила растяжения, или усилие, достигают устойчивого состояния. В полимерах с разветвленными цепями проскальзыванию цепей препятствует наличие разветвлений, которые перепутаны с основными цепями. Из-за этого и возникает деформационное упрочнение. Из-за этого сила растяжения или усилие достигают псевдо-устойчивого состояния, а затем снова возрастает, благодаря сопротивлению, вызванному присутствием разветвлений, перепутанных с основными цепями полимера. Эффект деформационного упрочнения усиливается по мере роста скорости растяжения, поскольку время, необходимое для реакции на усилие вытягивания, меньше для более высоких скоростей расширения.
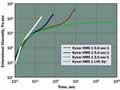 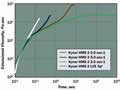
Рис. 4 и 5— Объемная вязкость для образцов с высокой прочностью расплава от Kynar при 1800 C дает деформационное упрочнение, которое улучшает контроль выдувного формования и получения пленки экструзией с раздувом. Объемная вязкость образцов PVDF была измерена специально созданным реометром растяжения. На Рисунках 4 и 5 показана объемная вязкость для образцов с высокой прочностью расплава от Kynar при 1800 C относительно времени достижения деформационного упрочнения. Измерение следует за обработкой при постоянном коэффициенте вытяжки. Измерения производились при различных скоростях растяжения, и сопоставлялись с линейной вязко-упругой оболочкой (LVE), которая определялась с помощью эксперимента ступенчатого изменения растяжения. LVE является основной точкой отсчета для объемной вязкости при нулевой скорости сдвига, она определяется с помощью плоско-параллельного реометра. Оба образца Kynar HMS дают деформационное упрочнение, тем самым, подтверждая наличие разветвленных цепей и указывая на наличие взаимосвязи между скоростью растяжения и степенью упрочнения, т. е. можно сказать, что деформационное упрочнение происходит быстрее при более высоких скоростях растяжения. Это соотношение считается основным при пневмоформовании с экструзией и получении плёнки экструзией с раздувкой, поскольку оно дает возможность лучше контролировать выдувание заготовки или стабильность рукава. В результате при использовании обеих технологий можно получить более однородную толщину готового продукта. На этих двух фотографиях показаны примеры испытания пленки, полученной экструзией с раздувом при 2400 C с использованием лабораторной линии для получения экструзионно-раздувной пленки. Используя образец стандартной Kynar 2 можно было получить рукав с максимальным коэффициентом раздува 2.2 и толщиной пленки 10 микронов. Плоский размер составил 55 мм при использовании кольцевой выходной части оформляющего канала головки экструдера в 0.5 дюйма. При увеличении потока воздуха, рукав дал искаженный “эффект сосиски”, и порвался в разных местах. Также, поскольку полученная толщина была невелика, механическая целостность пленки не была устойчивой, и появились повреждения по направлению к машине. 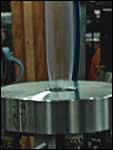
При испытании пленки, полученной экструзией с раздувом, новые HMS PVDF (слева) позволяют получать в два раза больший коэффициент раздува по сравнению со стандартным PVDF (справа). Для разветвленного образца, Kynar HMS 2, оказалось возможным получить рукав с коэффициентом раздува до 4.4, плоское измерение 110 мм, а также толщину пленки 5 микронов. Рукав продемонстрировал превосходную стабильность, не порвавшись в ходе тридцатиметрового цикла. Способность достигать высокого коэффициента раздува напрямую связана с разветвлением цепей, но также и с соотношением вязкости смолы и ее деформационного упрочнения, которые создают оптимальные условия для данного процесса.
Д-р Нафаа Мекхилеф – старший научный сотрудник с глубокими знаниями в области структур полимеров и реологии, а также того, как они взаимосвязаны с формованием из расплава. С ним можно связаться по телефону (610) 878-6977 или на сайте nafih.mekhilef@arkema.com. Д-р Лотфи Хедхли – старший научный сотрудник и эксперт в области синтеза фторполимеров и конденсационной полимеризации. С ним можно связаться по телефону (610) 878-6623 или на сайте lotfi.hedhli@arkema.com. Дэвид Сейлер – глобальный коммерческий директор компании Kynar. С ним можно связаться по телефону (215) 419-7396 или на сайте david.seiler@arkema.com
Arkema Inc.
|