Эти вопросы, а также достижения в области мониторинга температуры формования и давления и новая концепция формования без использования печи, были в центре внимания на недавней 31-й ежегодной встрече Ассоциации работников центробежного формования, состоявшейся в Вашингтоне, округ Колумбия. Использование смолы для ускорения цикла A. Schulman разработала новую модификацию смолы, которая, по имеющимся данным, дает оптимальные параметры отверждения расплава за более короткий срок, нежели тот, которого можно достигнуть за счет изменения формы или установок. Сообщается, что, давая оптимальные параметры отверждения, патентованная технология создания компаунда от Schulman Better Parts Faster (BPF) дает и самые лучшие физические свойства, сокращая, в то же время, продолжительность цикла нахождения в печи на 25% и уменьшая срок охлаждения до 10% по сравнению с традиционными методами. BPF была разработана для того, чтобы помочь формовщикам увеличить пропускную способность без дополнительных трудозатрат или оборудования. Технологию можно использовать, когда формовщик изготавливает несколько деталей различной толщины с помощью одного звена манипулятора. BPF улучшает процесс за счет более быстрого отверждения более толстых деталей для того, чтобы приблизить их по параметрам к срокам отверждения более тонких деталей. Также расхождения в пропускной способности могут быть сглажены формованием деталей с разной окраской. Технология BPF может реализоваться с использованием компаундов на основе любого полиэтилена независимо от индекса плавления или плотности. Не появляется практически никаких изменений физических свойств смолы—“только цикл осуществляется быстрее”, - говорит Томас Вышински, технический менеджер по смолам центробежного формования. Проведенные Schulman испытания показали, что технология BPF снижает продолжительность 18-минутного цикла для одной детали до 15 минут, достигая, в то же время, тех же значений прочности на разрыв. Новости в области мониторинга формования Новое низкозатратное устройство регистрации данных о температуре формования начального уровня было представлено 493K, поставщиком устройств для измерения температуры и давления для центробежного формования. Представителями этой английской компании здесь являются Ferry Industries, Mity-Lite, и STP. Устройство K-Log представляет собой одноразовое одноканальное устройство измерения и регистрации температуры. Переносное устройство размером с камеру обладает теплоизоляцией, так что его можно прикреплять к форме простым креплением с помощью кабеля. Данные относительно одного полного цикла формования собираются термопарой и хранится в памяти устройства измерения и регистрации. Устройство затем удаляется из формы и подсоединяется к персональному компьютеру для загрузки данных. K-Log эксплуатируется при температуре до 5720 F, и, по имеющимся данным, его точность составляет до ±2° F. Компания также сообщила о модернизации своей системы мониторинга температуры и давления в реальном времени K-paq для того, чтобы обслуживать до 12 звеньев манипулятора с многоместными пресс-формами. Система монтируется на форму и измеряет температуру формования с помощью термопар в стенке формы и давление в форме с помощью датчика в вентиляционной трубе. Данные относительно цикла формования отсылаются беспроводным способом в режиме реального времени на приемное устройство K-paq, а также на компьютер для отображения. Система работает при температурах до 6620 F. В компании говорят, что мониторинг формования позволяет оптимизировать использование обогревающего газа на 8 - 10% и уменьшить количества лома до 20%. Тем временем, Datapaq представила программное обеспечение Insight для своей системы профилирования температуры печи в реальном времени Rotopaq. В систему входят устройство регистрации данных, температурный барьер, а также термопары. Оно подсоединяется непосредственно к пресс-форме и отсылает информацию в беспроводном режиме на приемник, подсоединенный к персональному компьютеру. ПО Windows обеспечивает, по имеющимся данным, быструю загрузку, анализ, хранение и распечатку отчетов, которые можно также экспортировать в Microsoft Excel. Система “подсказок” программного обеспечения направляет пользователя в ходе процедуры установки профиля печи и введения рецептур продуктов, а также шаблонов продуктов. Система позволяет осуществлять сопоставление различных циклов. При наличии нового водонепроницаемого температурного барьера, теперь можно собирать и анализировать информацию из пресс-форм с помощью охлаждения разбрызгиванием воды или охлаждения туманом. RotoPaq может выдерживать температуру до 5750 F на протяжении 3 часов. Пресс-формы без печи Новая концепция формования без печи, при котором пресс-форма нагревается электричеством с помощью проводящего покрытия, была представлена Innovex Systems (ранее reSource, Inc.), поставщиком адаптированных под заказ клиента оборудования и автоматизированных устройств для предварительного нагревания и распределения материала, зажима пресс-формы, а также извлечения деталей. Новая система HeatPaint Rotomolding нагревает и охлаждает деталь без использования печи или камеры охлаждения. Пресс-форма покрыта новым проводящим покрытием с наночастицами, к которому поступает ток через токосъемные контактные кольца, которые доставляют питание на форму. Дирк Йериан, коммерческий директор, рассказывает, что покрытие можно нагреть до 4000 F в течение 30 секунд. Сообщается также, что покрытие может непрерывно использоваться при температуре 6500 F, а при коротких циклах при температуре 8500 F. Нагревается только пресс-форма, поэтому центральная спица дорнодержателя может удерживать электронное устройство управления, которое отсылает оператору информацию в режиме реального времени. Innovex изготовила в форме для образцов детали с толщиной стенок 0.220 дюйма с использованием 5.5-минутного цикла нагревания и предварительно нагретого порошка LLDPE и 6.5-минутного и холодного порошка. Эти результаты надо сравнить с продолжительностью цикла 12 минут для той же детали, изготовленной на обыкновенной установке. Затраты на энергию для нагревания установки составляют примерно 1.08¢ по сравнению с примерно 11.5¢ при традиционном нагреве с использованием газа. Innovex разрабатывает полностью автоматизированную систему, которая осуществляет автоматическую загрузку формы предварительно нагретым материалом. Программное обеспечение персонального компьютера обеспечивает зонированное управление температурой в пресс-форме и получение данных. Лабораторная установка будет стоить примерно $10,000 за базовую установку без пресс-форм. 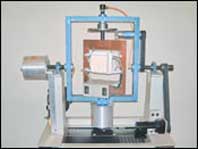
С новой компактной технологией формования без использования печи от компании Innovex используется специальное нанопокрытие, которое проводит электрический ток для непосредственного нагревания пресс-формы. Сообщается, что это может ускорить формовании при использовании меньшего количества энергии. Здесь показана лабораторная модель Еще некоторые новинки оборудования Серия с рукой с поворотными движениями TRM от компании STP Rotomachinery была модернизирована добавлением камеры сгорания новой конструкции, печи для обжига и вентиляторов, которые улучшают распределение горячего воздуха и повышают эффективность нагревания. Серия также модернизировалась для повышения простоты материально-технического обслуживания. Также компания перемещает свое производство на более крупное предприятие в Шербруке, Квебек. Работа на новой площадке позволит сократить срок до начала реализации проекта с 12 до 16 недель. Более крупные детали можно теперь производить с использованием линии XT компании Rotoline Industrial Equipment Ltda из Бразилии, интересы которой представлены здесь Reduction Engineering. Уникальная цилиндрическая печь установки сейчас примерно на 10% длиннее, что, как сообщается, повышает производительность и эффективность энергопотребления за счет исключения мертвого и холодного пространства. По имеющимся данным, система обеспечивает на 30% большую производительность, чем одинарная карусельная установка, и может затрачивать на 20 - 25% меньше газа, чем конкурирующее с ней оборудование, обеспечивая при этом рабочие циклы на 20% короче. Измельчитель материала высокой мощности Mega-Mill был представлен компанией Powder King. Новая модель компании PK-DD Mega может обрабатывать от 1700 до 2100 фунтов полиэтилена в час. Прямой привод установки делает ненужным использование плит настила, ограждения ремённой передачи, а также корпуса подшипника, которые используются для моделей с ременным приводом. Она также дает на 10 лошадиных сил больше энергии, чем установка с ременным приводом.
Микелль Найтс, старший редактор Источник: Plastics Technology
|