Основной ротационный тип вибросварки, был создан для того, чтобы заполнить имевшуюся на рынке нишу для машин среднего размера, которые могут обрабатывать детали размером до 305 мм в диаметре, а также, чтобы обрабатывать некоторые детали, которые нельзя обрабатывать с помощью обыкновенной вибросварки. При использовании данной технологии две пластины вращаются круговым движением относительно друг друга, как показано на Рисунке 1. В отличие от линейной вибросварки, при которой скорость сварки не одинакова, поскольку она должна начинаться и прекращаться в конце каждого цикла, круговая сварка непрерывна. Это уменьшает время, необходимое для создания сварного шва, а это, в свою очередь уменьшает объем потребляемой энергии. Для этого также нужна меньшая амплитуда сварки, таким образом, уменьшается расстояние, необходимое для сварного движения и улучшается контроль вспышки. Сварка оказывает меньшее воздействие на эластичные тонкие стенки, и она может обеспечивать более прочное соединение. К сожалению, круговая вибрация очень чувствительна к параметрам применения, и ее нельзя использовать для производства многих продуктов. 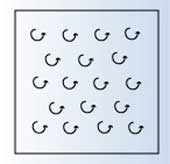 Рисунок 1: Движение при круговой сварке
Линейная вибросварка Вибрацию можно также применять к созданию линейного или кругового процесса. Линейная сварка это самый старый и наиболее распространенный вид сварки, в этом режиме работают тысячи машин. Ее использование обеспечивает наилучший результат и обработку широкого диапазона размеров. В то время, как круговая вибросварка лучше всего осуществляется при нерезонансной частоте, линейная вибросварка используется при резонансной частоте. Способ перемещения деталей зависит от их формы и жесткости. Тяговое усилие прикладывается к внешним заплечикам на Рисунке 2a. Тем не менее, оно также может прикладываться к углублению в детали, как показано на Рисунке 2b. Когда необходимо сварить внутренние ребра или промежуточные перегородки, может понадобиться сварочное приспособление, такое, как на Рисунке 2c. в том месте, где к внутреннему соединению прикладывается сила.  Рисунок 2: Сварочные приспособления для линейной вибросварки: а. Внешнее сварочное приспособление к заплечикам, b. Сварочное приспособление к углублению и c. Многокомпонентное внутреннее сварочное приспособление для ребер
Оборудование для линейной вибросварки состоит из вибратора, размешенного в верхней части рамы машины, и состоящего из вибрирующей пластины, подвешенной на пружинах и работающей от электромагнита, и находящейся в нижней части корпуса машины зажимной доски, управляемой с помощью гидравлического цилиндра, который поднимает ее для соединения с вибрирующей плитой, и обеспечивает давление, необходимое для сварки. Сварочные приспособления, которые специально создаются для того, чтобы соответствовать контурам каждого применения, присоединяются к вибрирующей пластине и зажимной доске. 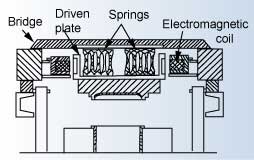 Рисунок 3: Основные компоненты установки для линейной вибросварки
Цикл начинается с загрузки одной из деталей, которые будут присоединяться с помощью вибросварки, в гнездо или к сварочному приспособлению нижней зажимной доски машины, как показано на Рис. 3. Привариваемая часть затем размещается в нужном положении на нижней детали. Затем нижняя зажимная доска поднимается к вибрирующей пластине, в которой находится верхнее сварочное приспособление. Она точно подходит к сопрягаемой детали и фиксирует ее положение. Обе детали зажимаются вместе под контролируемой нагрузкой, и деталь, которая находится на вибрирующей пластине, обрабатывается вибрацией при диапазоне амплитуды от 0.75 до 5.0 мм и при частоте от 120 до 300 Гц для того, чтобы создать теплоту рассеяния при трении на интерфейсе между ними. Давление является важным фактором, поскольку без давления, не происходит выделения тепла. Низкое давление при сварке приводит к увеличению продолжительности цикла. Усовершенствованные системы могут оптимизировать управление процессом за счет изменения давления прямо в ходе рабочего цикла. В целом, вибрасварка состоит из четырех этапов. На первом этапе вибрация жестких компонентов создает кулоновское трение, которое создает тепло на месте сопряжения деталей. На этом этапе не происходит никакого проплавления (движения деталей навстречу друг другу). Когда достигается температура перехода в стеклообразное состояние и появляется вязкий поток, начинается второй этап, в ходе которого тепло генерируется за счет вязкого рассеяния в расплавленном полимере. Растекание потока полимера в радиальном направлении позволяет осуществиться проплавлению. В ходе третьего этапа расплав и поток уже достигли устойчивого состояния, при котором потери тепла через стенки из-за вспышки равны количеству выделяемого тепла. На этом этапе расплав растекается в радиальном направлении, и с течением времени увеличивается линейное проплавления сварного соединения. Эта часть цикла осуществляется в зависимости от применения, и на нее потребуется от 0.5 до 10 секунд, т. е. примерно две трети от продолжительности цикла сварки. Проплавление, которое необходимо для того, чтобы достигнуть стабилизированного режима, увеличивается с увеличением толщины стенок детали, и уменьшается с повышением давления сварки. Когда выделяется количество тепла, достаточное для того, чтобы расплавить материал в месте соединения, вибрация прекращается и наступает четвертый этап. Глубина проплавления продолжает увеличиваться, поскольку давление замыкания формы заставляет расплавленный полимер течь до тех пор, пока он не отвердеет. Детали держат прижатыми в нужном окончательном положении, пока они не остынут достаточно долго для того, чтобы выдержать разгрузку, этот период длится от 0.5 до 5.0 секунд. Это имеет решающее значение, поскольку не существует другого способа контроля горизонтального расположения двух деталей относительно друг друга кроме окончательного положения вибрирующей пластины. После того, как это произойдет, нижняя зажимная доска отводится вниз в свое исходное положение, а готовая сборка удаляется из установки. После этого оборудование готово к началу нового цикла. Преимущества вибросварки 1. НЕ НУЖНЫ НИКАКИЕ ДОПОЛНИТЕЛЬНЫЕ МАТЕРИАЛЫ – При вибросварке не используются никакие дополнительные материалы, такие как крепеж, вкладыши, электромагнитные преформы, клеящие вещества или растворители. Благодаря этому данный метод по определению менее затратный, чем другие методы, при использовании которых применяются дополнительные материалы, этот метод также дешевле с точки зрения демонтажа для утилизации. 2. МЕНЬШЕ РАБОТ ПО ПОДГОТОВКЕ ПОВЕХНОСТИ – Вибросварка относительно нечувствительна к плохой подготовленности поверхности. 3. ПРОСТОТА СБОРКИ – Для вибросварки нужно только разместить две детали в сварочное приспособление установки для вибросварки. 4. ЗАХВАТ ДРУГИХ ДЕТАЛЕЙ – Можно удерживать дополнительные детали между двумя деталями, подвергающимися вибросварке, при условии, что они размещены так, что не создают помех для сварки. 5. УСТОЙЧИВОСТЬ – При вибросварке создаются постоянные сборки, которые нельзя вскрыть, не повредив сами детали. Из-за ограничений, которые накладывают материалы, различия в линейном термическом расширении и влагопоглощении редко создают проблемы после того, как детали сварены. 6. ВНУТРЕННИЕ СОЕДИНЕНИЯ – В некоторых случаях можно осуществлять вибросварку внутренних стенок при условии, что они сходятся в плоскости сварки. 7. СВОБОДА СОЗДАНИЯ ФОРМ – Вибросваркой может осуществляться соединение деталей практически любой формы, при условии возможности создания горизонтальной соединяемой поверхности в соответствии с требуемыми параметрами. Вибросварка не зависит от способности пластмассы передавать вибрацию, поэтому с ее помощью можно сваривать детали, которые плохо подходят для ультразвуковой сварки из-за того, что они слишком тонкие, имеют сложный контур, а также отверстия в стенках, или же не обладают поверхностью, хорошо подходящей для ультразвуковых консолей. 8. ГЕРМЕТИЧНЫЙ СПАЙ – С помощью вибросварки можно создавать герметичные спаи. 9. ЭФФЕКТИВНОСТЬ ИСПОЛЬЗОВАНИЯ ЭНЕРГИИ – По сравнению с другими технологиями сварки, вибросварка позволяет очень эффективно использовать энергию. Это также означает, что не выделяется избыточного тепла, которое надо удалять из производственного помещения. 10. ЧИСТОТА АТМОСФЕРЫ – В отличие от ситуаций с применением клеящих систем и систем соединения с помощью растворителя, здесь не требуется вентиляционного оборудования для отвода ядовитых дымов. 11. НЕМЕДЛЕННАЯ РАЗГРУЗКА – Собранные детали могут сразу же поступать для осуществления других операций, не дожидаясь, пока деталь остынет, и клеящие вещества или растворители схватятся. 12. ВЫСОКАЯ СКОРОСТЬ ПРОИЗВОДСТВА – В зависимости от применения, при вибросварке можно получить скорость производства от 4 до 30 деталей в минуту на основе одной сварки на цикл, не учитывая времени погрузки/разгрузки детали, которое различно для каждого применения. Возможно получение и более высокой скорости при обработке множества деталей в ходе каждого цикла. 13. ТЕХНОЛОГИЧЕСКАЯ СВОБОДА – Подвергаться вибросварке могут детали, произведенные с помощью практически всех технологий получения термопластов. 14. ВОЗМОЖНОСТЬ ОБРАБОТКИ КРУПНЫХ ДЕТАЛЕЙ – Имеется оборудование, которое позволяет сваривать детали, достигающие до 1016 мм на 2032. С помощью вибросварки можно изготовить автомобильный бампер размером 1524 мм. 15. КОНТРОЛЬ ТОЧНОСТИ – Вибросварка позволяет осуществлять контроль точности технологических переменных. 16. ВОЗМОЖНОСТЬ БЫСТРОГО ПЕРЕХОДА ОТ ОДНОЙ РАБОТЫ К ДРУГОЙ – Оборудование для вибросварки можно быстро переналадить для перехода от выполнения одной работы к другой. 17. ВОЗМОЖНОСТЬ ОСУЩЕСТВЛЕНИЯ КОНТРОЛЯ – Эту технологию легко контролировать, здесь едва ли возможна деформация поверхности из-за пережога. Недостатки вибросварки 1. ОГРАНИЧЕНИЯ ФОРМЫ – Должна быть плоская горизонтальная поверхность сварки. 2. ПОВРЕЖДЕНИЕ ЭЛЕКТРОННЫХ КОМПОНЕНТОВ – Вибрация может повреждать некоторые электронные компоненты или их сборки. 3. ПОДГОНКА - В деталь нельзя формовать фиксирующие штифты или иные устройства. Регулировка расположения частей относительно друг друга осуществляется по окончательному положению двух деталей. 4. ОГРАНИЧЕНИЯ ИСПОЛЬЗУЕМОГО МАТЕРИАЛА – Для вибросварки можно использовать только совместимые термопласты. 5. ШУМОВЫЕ ПРОБЛЕМЫ – Похожие на вой сирены звуки, возникающие при вибросварке (от 90 до 95 дБ), приводят к повсеместному использованию звукозащитных камер. Они снижают уровень шума до примерно 80 дБ. 6. ЗАТРАТЫ НА ОБОРУДОВАНИЕ – Установки для вибросварки дороже, чем установки для сварки нагретым инструментом, и стоят значительно дороже, чем установки для ультразвуковой сварки или сварки трением. Это соображение ограничивает их использование обработкой деталей слишком крупного размера или же слишком плохо сконфигурированных для использования вышеупомянутых технологий. Материалы для вибросварки Практически все термопласты можно подвергать вибросварке. В этом плане данный процесс аналогичен сварке нагретым инструментом или сварке трением. Эта технология особенно полезна при работе с кристаллическими термопластами, которые трудно соединять с помощью ультразвуковой сварки. Как и в случае с ультразвуковой сваркой, аморфные смолы лучше поддаются сварке, чем кристаллические смолы. Тем не менее, кристаллические термопласты значительно лучше поддаются вибросварке, нежели ультразвуковой сварке. Для материалов с низкими коэффициентами трения, могут потребоваться большие частоты вибрации для получения оптимального качества сварки. Сообщается об успешном применении технологии при обработке термопластичных каучуков и эластомеров. Успешно соединяются с помощью вибросварки и высокотемпературные конструкционные термопласты. Хорошо поддаются вибросварке также наполненные и армированные смолы. Тем не менее, сварке подвергается только полимер, поэтому прочность соединения это прочность самой смолы, и прочность соединения уменьшается с учетом процентного соотношения наполнителя. В частности, стекловолокно может выступать сквозь поверхность сварного шва прямо посередине. С другой стороны, при использовании данной технологии меньше воздействие антиадгезионной смазки для пресс-формы и прочих веществ, загрязняющих поверхность, чем при сварке нагретым инструментом или ультразвуковой сварке, здесь также несколько меньше воздействие влаги, хотя высоко гигроскопичные полимеры, такие как нейлон, все же следует подвергать сварке с осторожностью. Из-за влаги могут появиться раковины в швах из-за образования водяного пара. Уменьшить образование раковин и время сварки можно с помощью предварительного высушивания деталей. Высокое давление при соединении может предотвратить образование раковин в сварных швах. При 50 процентной относительной влажности прочность сварных швов из нейлона 6 может уменьшиться вдвое по сравнению с прочность сухих швов. Для нейлона 66 показатели несколько лучше: здесь прочность снижается только на треть. Сопоставление со сверхзвуковой сваркой и сваркой нагретым инструментом Вибросварку можно охарактеризовать как технологию, которая начинает использоваться там, где перестает использоваться ультразвуковая сварка, особенно в том, что касается размеров детали. Справедливо, что эти технологии, в целом, схожи. Соответственно, у этих технологий много общих черт. Кроме того, оборудование для вибросварки производится теми же производителями, которые делают оборудование для ультразвуковой сварки, так что эти технологии прекрасно дополняют друг друга. Тем не менее, из-за значительной стоимости оборудования, вибросварку обычно используют только для применений, для которых нельзя использовать ультразвуковую сварку. Но между этими технологиями существуют и некоторые существенные различия. Хотя при обеих технологиях используют высокочастотную вибрацию, она применяется по-разному и с использованием различных частот. При ультразвуковой сварке вибрации вертикальные, в диапазоне от 15000 Гц до 72000 Гц, здесь тепло создается за счет молекулярного трения. Вибросварка горизональный процесс, протекающий при частотах от 120 Гц до 300 ГЦ, а тепло здесь создается за счет поверхностного терния, когда происходит физическое движение всей детали. В результате при вибросвакре можно обрабатывать значительно более крупные детали, чем при ультразвуковой сварке, и здесь не нужны направляющие энергии, из-за которых ультразвуковая сварка ограничивается использованием только тех деталей, которые были изготовлены литьевым формованием. В то время, как детали из термоотверждающихся смол нельзя обрабатывать вибросваркой, детали, получаемые в результате использования практически всех термопластических технологий, можно соединять вибросваркой. Сварка нагретым инструментом или сварка плавлением также может рассматриваться в качестве конкурента вибросварки, поскольку прочность сварных швов и параметры совместимости материалов здесь практически одинаковы. Тем не менее, хотя стоимость оборудования значительно ниже, а диапазон форм и размеров больше, у нее более продолжительный рабочий цикл; стоимость оборудования, сварочных приспособлений, энергии, и материально-технического обслуживания у этой технологии выше, чем у вибосварки. У линейной вибросварки множество применений в автомобильной промышленности, включая выхлопные трубы, приборные доски, бамперы и задние фары. К числу применений относятся такие устройства, как: вентиляторные и насосные установки, лотки для холодильников и чехлы для бензопил. Примерами использования круговой вибросварки являются задние габаритные огни и электрические оболочки. Джордан Ротхайзер, http://www.omnexus.com |