В настоящее время весьма жестко и придирчиво выбираются материалы для изготовления изделий, работающих в условиях трения. Для того чтобы максимально удовлетворить эксплуатационные требования используют в основном полимерные композиционные материалы, состоящие из полимерной матрицы, модифицирующих добавок и упрочняющих наполнителей. Следует сказать, что одному и тому же полимеру, используемому в качестве матрицы, в зависимости от добавок, составляющих окончательную композицию, можно придавать как фрикционные, так и антификционные свойства. Пластмассы обладают комбинациями физико-механических свойств, которые часто наиболее полно отвечают эксплуатационным условиям узлов и деталей машин. К числу таких свойств относятся: • Малый удельный вес при достаточной прочности. Известно, что пластмассы в 2–3 раза легче алюминия и в 5–8 раз легче стали. Это свойство особенно ценно для создания конструкций летательных аппаратов, транспортных систем, машин и аппаратов специального назначения. Машины становятся значительно легче, уменьшается «мертвый» вес конструкции и возрастает полезная нагрузка. • Способность воспринимать и выдерживать нагрузки — механические, термические и электроэнергетические — определяется физико-механическими свойствами материала. У некоторых видов пластмасс удельная прочность, то есть нагрузка, воспринимаемая на единицу площади, значительно превышает удельную прочность металлов. Например, некоторые пластики, армированные волокнами, по прочностным свойствам превосходят прочность углеродистой стали в два раза. Кроме того, эти пластики удовлетворительно работают на сжатие и изгиб, тогда как углеродистая сталь таких нагрузок не выдерживает. • Вибростойкость. Пластмассы — прекрасные амортизаторы вибраций. Они поглощают колебания в 20 раз лучше, чем алюминий, и в 100 раз лучше, чем сталь. Детали, изготовленные из пластмасс, хорошо работают при больших динамических и ударных нагрузках. • Способность поглощать шумы и звуконепроницаемость — особенно ценные свойства пластмасс как конструкционных материалов. Детали из пластмасс в машинах не только не создают дополнительных шумов, но и сами в какой-то мере поглощают их. Например, при замене металлических быстроходных шестерен на пластмассовые в редукторах почти полностью устраняются шумы. • Антифрикционные пластмассы обладают низким коэффициентом трения, мало изнашиваются, хорошо выдерживают температуры, возникающие в процессе трения. Кроме того, они способны работать без смазки. Полиамидные материалы Наиболее распространенными термопластичными антифрикционными материалами являются полиамиды, как алифатические, так и ароматические. Алифатические полиамиды обладают низким коэффициентом трения (коэффициент трения полиамидов по стали без смазки 0,1–0,2, со смазкой маслом — в пределах 0,05–0,10), достаточно износостойкие, способны работать в интервале температур от –40 до +80°С. К недостаткам полиамидов можно отнести невысокую теплопроводность, низкую несущую способность. Полиамиды не обладают стойкостью по отношению к маслу и влаге. Для улучшения физико-механических характеристик полиамиды армируют волокнистыми материалами (например, стекловолокном, углеродным волокном и т. д.), для улучшения антифрикционных свойств в полимер вводят твердые смазки (графит, дисульфид молибдена, и т. д.). Они могут применяться как в чистом виде, так и модифицированные добавками и наполнителями. Ароматические полиамиды относятся к термореактивным материалам. Их применяют для изготовления узлов трения, как в чистом виде, так и с наполнителями: фторопластом, дисульфидом молибдена, графитом и другими смазками. Благодаря высокой механической прочности армировать ароматические полиамиды не нужно, поэтому в них вводят лишь добавки, снижающие коэффициент трения и износ. Детали из этих материалов не только прочные, но и термостойкие. Типичным представителем ароматических полиамидов является фенилон. Детали из фенилона эксплуатируются при температурах от –50 до +200°С. Этот материал химически стоек, может работать в агрессивных средах. Полиолефины Другими распространенными материалами для узлов трения являются полиолефины — полиэтилен и полипропилен. Они используются как в чистом виде, так и в композициях с различными наполнителями. Полиолефины в чистом виде обладают хорошими эксплуатационными свойствами в пределах температурных нагрузок до +60°С. Свыше этой температуры из-за невысокой теплопроводности они в нагруженном режиме работать не могут. Это ограничивает область их применения в качестве антифрикционных материалов. Для повышения работоспособности будущих изделий в полимер вводят армирующие наполнители, повышающие его прочность, а также добавки, снижающие коэффициент трения, износ и температуру в зоне трения. При этом коэффициент трения у модифицированных полиолефинов может быть ниже 0,1. Компоненты, добавляемые к такой композиции, стандартны, однако существенно повысить температурную работоспособность материала крайне трудно (максимум на 20%), а подчас невозможно. Поэтому полиолефины применяют в слабонагруженных узлах, работающих в относительно мягких условиях эксплуатации. Таблица 1. Физико-химические свойства полиамидов и полиолефинов | Материал | Плотность, г/см3 | Прочность при сжатии, МПа | Ударная вязкость, кДж/м2 | Твердость по Бринеллю | Полиамид 6 | 1,10 | 85 | 120 | 110 | Полиамид 610 | 1,10 | 90 | 100 | 130 | П-12А | 1,02 | 60 | 90 | 75 | Капролон-В | 1,15 | 110 | 140 | 140 | Фенилон П | 1,33 | 320 | 20 | 180 | Фенилон С1 | 1,33 | 220 | 20 | 180 | Фенилон С2 | 1,33 | 220 | 35 | 220 | Полиэтилен высокого давления | 1,40–2,50 | 12 | – | 14–25 | Полиэтилен низкого давления | 4,50–5,80 | 27 | 2–150 | 45–60 | Полиэтилен среднего давления | 5,60–6,50 | – | 7–120 | 60–80 | Полипропилен | | 60 | 33–88 | 40–70 |
|
Узлы трения из поликарбоната Поликарбонат используется не только для производства листов и тары, но и для изготовления антифрикционных изделий. Он идеально подходит для работы в условиях низких и сверхнизких температур, вплоть до криогенных. Изделия из поликарбоната эксплуатируются в среде жидкого азота, водорода и гелия при температурах до –253°С. Поликарбонат, как известно, обладает высокой ударной прочностью и стабильностью размеров деталей, малой ползучестью. Эти свойства являются одними из определяющих для его применения в узлах трения, работающих при ударных нагрузках. Однако следует заметить, что поликарбонат плохо сопротивляется циклическим воздействиям нагрузки и имеет низкую усталостную прочность. Материал устойчив к ультрафиолетовому излучению и резким перепадам температур, но не стабилен по отношению к действию ионизирующего излучения. Для снижения коэффициента трения и повышения износостойкости в поликарбонат вводят специальные наполнители и твердые смазки. Введение дисульфида молибдена (Эстеран-29, Эстеран-51), графита (ДАК-УП5Д) или 15–20% фторопласта (ДАК-8) снижает коэффициент трения в 2–3 раза, наполнение поликарбоната стекловолокном и фторопластом (Дифлон) придает изделиям из такой композиции высокие физико-механические и диэлектрические свойства. Таблица 2. Свойства наполненного поликарбоната | Марка материала | Плотность, г/см3 | Прочность при сжатии, МПа | Ударная вязкость, кДж/м2 | Предельная рабочая температура, °С | Коэффициент трения | Эстеран-29 | 1,30 | – | 6 | 110 | 0,25 | Эстеран-51 | 1,25 | 60 | 150 | 110 | 0,24 | ДАК-УП5Д | 1,25 | 90 | - | - | 0,23 | ДАК-8 | 1,24 | 55 | 87 | 115 | 0,20 | Дифлон | 1,20 | 90 | - | - | 0,30 |
Термопластичные материалы на основе полиарилатов Полиарилаты также относятся к антифрикционным термопластам. Они способны стабильно работать при высоких температурах — 160–180°С, а кратковременную работу выдерживают при 230°С. Такие диапазоны для термопластов весьма высоки. Наряду с теплостойкостью полиарилат обладает высокой сопротивляемостью ионизирующим излучениям, хорошими диэлектрическими свойствами, химической и морозостойкостью (может эксплуатироваться при температуре до –100°С). В чистом виде полиарилаты имеют нестабильные триботехнические характеристики, для их стабилизации в материал вводят такие добавки как фосфор, дисульфид молибдена, медь. Это приводит к уменьшению коэффициента трения (у чистых полиарилатов коэффициент трения высокий, примерно 0,4) и снижению износа.
Пентапласт Этот полимер гораздо реже используется в качестве антифрикционного материала для узлов трения. Он химически стоек и применяется для изготовления деталей, работающих в агрессивных средах. Из пентапласта можно получать различного рода уплотнители, так как он обладает небольшой усадкой. Работоспособность материала стабильно сохраняется в интервалах температур 120–130°С. По этому показателю пентапласт превосходит полиолефины. Его используют как в чистом виде, так и в комбинации с наполнителями: стекловолокном, слюдой, окисью хрома, графитом. Коэффициент трения чистого материала составляет 0,12. Таблица 3. Свойства пентапласта в комбинации с наполнителем | Наполнители | Плотность, г/см3 | Прочность при растяжении, МПа | Модуль упругости, кПа | Твердость по Бринеллю | Слюда (15%) | 1,52 | 63 | 2,42 | 139 | Стекловолокно (10%) | 1,45 | 67 | 2,11 | 123 | Окись хрома (15%) | 1,60 | 56 | 1,34 | 98 | Графит (10%) | 1,50 | 53 | 2,20 | 100 |
Полимерный материал, стоящий отдельно от термопластов и реактопластов Фторопласт имеет самый низкий коэффициент трения (коэффициент трения фторопласта-4 составляет 0,03–0,05). Он обладает высокой химической стойкостью, способен работать в диапазоне температур от –250°С до 300°С. Несмотря на это, фторопласт в чистом виде применяют весьма ограниченно. Это объясняется его низкой прочностью и небольшой твердостью, что в свою очередь приводит при трении к деформированию его поверхностных слоев. В результате деталь изнашивается достаточно быстро.
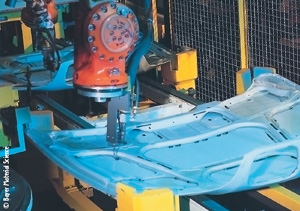
| Использование полимеров в машиностроении демонстрирует универсальность и преимущества этих материалов для деталей машин и механизмов |
В машиностроении используются в основном композиционные материалы на основе фторопласта. Для увеличения несущей способности изделий в фторопласт вводятся армирующие волокнистые наполнители, металлический порошок, кокс, и т. д. Кроме того, введение наполнителей позволяет значительно снизить интенсивность изнашивания фторопласта. Широко практикуется нанесение фторопласта в виде покрытий на более твердые и прочные поверхности.
Антифрикционные композиционные материалы на основе полиимидов Эти материалы обладают высокой радиационной и химической стойкостью, хорошими триботехническими свойствами и могут длительно эксплуатироваться при температуре 220–260°С. Материалы на основе полиимидов удовлетворительно работают в условиях высокого вакуума (до 10-4 Па). Детали узлов трения из полиимидов получают горячим прессованием. Они имеют малую усадку (0,7–1,0%), что дает возможность использовать полиимиды для изготовления деталей высокой точности. Недостатком этих материалов является большая скорость газовыделения и хрупкость, что несколько ограничивает их применение. Для изготовления пористых изделий, например, подшипников, к полиимиду добавляют полиформальдегид. Добавление внутренних смазок позволяет снизить коэффициент трения композиции до 0,1 при допустимом контактном давлении 350 МПа. Таблица 4. Свойства композитов на основе фенолоформальдегидных смол | Армирующие наполнители | Плотность, г/см3 | Прочность при изгибе,МПа | Ударная вязкость, кДж/м2 | Коэффициент трения | Базальтовые волокна | 1,71 | 93 | 40 | 0,15 | Стеклянные волокна | 1,90 | 60 | 10 | 0,35 | Углеродные волокна | 1,45 | 70 | 44 | - | Древесные волокна | - | 78 | 9 | 0,22 |
Фенолоформальдегдные смолы Как правило, такую полимерную матрицу упрочняют волокнистыми наполнителями, а также вводят внутренние смазки. Изделия на основе фенолоформальдегидов обладают химической стойкостью, высокой жесткостью, стабильностью размеров, высокой износостойкостью. Как и большинство реактопластов, изделия на основе этих смол способны стабильно эксплуатироваться при температурах до 180°С. Смолы в чистом виде практически не используются. Из них готовят композиты, состоящие из армирующих наполнителей и внутренних смазок. Содержание добавок в композите может составлять до 70%. Таблица 5. Свойства антифрикционных материалов на основе полиимидов | Марка материала | Плотность, г/см3 | Прочность при сжатии, МПа | Ударная вязкость, кДж/м2 | Твердость по Бринеллю | Предельные рабочие температуры, °С | Полиар-2 | 1,30 | – | 50 | 140 | -196, +300 | Тесан-38 | 1,30 | – | 30 | 140 | -196, +250 | ПМ-69-Г5 | 1,47 | 80 | 30 | 320 | -196, +250 | ПАМ 50-69 | 1,55 | 38 | 5 | 300 | -196, +250 |
На основе вышеизложенного можно сказать, что полимерная матрица для узлов трения может быть изготовлена из различных материалов. Все зависит от требований, которые предъявляют к ним, и условий эксплуатации. Автор: Артем Третьяков Источник: Полимеры-Деньги |