Были определены гарантийные сроки хранения различных жидкостей в ПЭТ-бутылках. Без ущерба эксплуатационных качеств бутылок в них можно хранить: ацетон в течение 3 лет, моторное масло 5, воду 3-5 лет и т.п. Приведенные данные верны только в том случае, когда используется высококачественная бутылка. При этом доказано, что при производстве бутылки из преформы материал, из которого преформа изготовлена, не претерпевает никаких химических изменений. Итак, все дело в качестве преформы. С формальных позиций это полуфабрикат, и поэтому на преформу не существует государственного стандарта. Достаточно утверждения фирмы-производителя о соответствии преформы техническим условиям, которые производитель сам себе разрабатывает и сам себе утверждает. Существуют к счастью, международные стандарты, и, для того, чтобы понять, что такое высококачественная преформа, рассмотрим более подробно процесс ее получения. Преформы производят методом литья под давлением. Температура переработки 280 - 300 оС. При таких температурах возможна термодеструкция полиэтилентерефталата. Это значит, что ПЭТ теряет свои замечательные механические свойства. Это уже не специальный полимер для производства бутылок. Говоря научным языком, это сырье с пониженной молекулярной массой. Бутылка, изготовленная из деструктированного ПЭТ, имеет желтоватый оттенок и повышенную хрупкость. Особенно это сказывается при транспортировке: при тряске по российским дорогам у таких бутылок иногда отваливаются и лопаются донышки. Значительно увеличивается склонность изделий к деструктивному старению под действием кислорода и ультрафиолета - гарантийные сроки хранения сокращаются в десятки раз. Мало того, при термодеструкции возможно выделение весьма вредных веществ, которые мигрируют в жидкость, налитую в бутылку, а также отравляют рабочих и близко живущих жителей при производстве преформ. Допустимые концентрации вредных веществ, выделяющихся при производстве преформ, представлены в таблице. Таблица №1: Допустимые концентрации вредных веществ, выделяющихся при переработке полиэтилентерефталата Вредное вещество по ГОСТ 12.3.030 | Миграция в модельные среды в готовых изделиях, мг/л | В воздухе рабочей зоны, мг/м3 | В атмосферном воздухе населенных мест (максимально разовая), мг/м3 | В атмосферном воздухе населенных мест (среднесуточная), мг/м3 | Ацетальдегид | 0,2 | 5 | 0,01 | 0,01 | Диметилтерефталат | 0,5 | 0,1 | 0,05 | 0,01 | Кислота терефталевая | - | 0,1 | 0,01 | 0,001 | Кислота уксусная | - | 5 | 0,2 | 0,06 | Углерода оксид | - | 20 | 5 | 3 |
Катализатором термодеструкции является вода. Причем при деструкции ПЭТ снова выделяется вода. Доказано, что, для того, чтобы избежать термодеструкции, ПЭТ необходимо высушивать до содержания влаги, меньшего 0.003 - 0.004 мас.%. Такое низкое содержание влаги недостижимо при обычных приемах сушки полимеров, например в сушильных шкафах. В России, однако, уже сейчас существует множество действующих предприятий по производству ПЭТ-преформ, где сырье сушат именно в шкафах (догадайтесь, как они получили разрешение на производство и гигиенические сертификаты на готовые изделия). Оборудование на этих предприятиях, как правило китайского производства, и продают его в Россию фирмы-посредники, которых множество. Как же нужно себя не уважать, чтобы травить своих детей и окружающих! Устройство агрегатов для сушки ПЭТ показано на рисунке. Сырье засасывается из мешка вакуумным загрузчиком (на рисунке не показан). Загрузчик имеет собственное дозирующее устройство, с помощью которого гранулы ПЭТ порционно подаются в бункер таким образом, чтобы он был всегда заполнен сырьем. Сырье перемещается в бункере сверху вниз так, чтобы во время пребывания каждой порции в бункере было не менее четырех часов. Снизу в бункер через выходное сопло подается подогретый нагревателем воздух. Отобрав влагу от сырья, воздух через фильтр и холодильник попадает в адсорбер-осушитель и затем снова в бункер. Адсорберов два. Когда один работает, другой генерируется. В рабочем контуре датчики непрерывно измеряют степень сухости воздуха - точку росы. Превышение допустимого значения точки росы является сигналом того, что рабочий адсорбер пресыщен, заслонки автоматически переключаются, и роль адсорберов меняется. 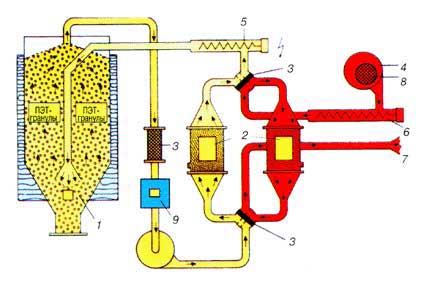 1 - выходное сопло; 2 - адсорберы; 3 - переключатели; 4 - воздуходувка; 5 - основной нагреватель; 6 - нагреватель регенератора; 7 - выходная труба 8 – микрофильтр 9 - воздухоохладитель Полиэтилентерефталат - кристаллизующийся полимер. Преформу при ее производстве следует охлаждать быстро, так, чтобы ПЭТ не успел закристаллизоваться и затвердел, т.е. перешел в стеклообразное состояние, сохранив аморфную , некристаллическую структуру, которую он имеет в расплавленном состоянии. С точки зрения физики стекло - та же жидкость, только величина его вязкости столь огромна, что и за сотни лет не удается заметить деформаций стеклообразных сред под действием напряжений. С ростом температуры вязкость падает настолько, что полимер приобретает способность деформироваться за разумные промежутки времени. На этом и основан способ получения бутылок из преформ - достаточно разогреть преформу до температуры порядка ста градусов, чтобы за секунды из нее можно было выдуть бутылку. Но в расплавленном состоянии величина вязкости ПЭТ очень низкая - подвижность очень велика и полимер может успеть частично перейти в термодинамически более выгодное - кристаллическое состояние. Визуально это видно по побелению отдельных участков преформы, особенно в области конца сферической части, у литника. Температура плавления кристаллов ПЭТ около 250 оС и при температуре производства бутылок кристаллические участки преформ деформироваться - формоваться в бутылку не могут. В составе оборудования, поставляемого нашей фирмой, - мощный холодильник. Он позволяет охлаждать пресс-формы с максимальной интенсивностью и получать минимальную величину кристалличности в изделии. Поэтому существуют международные стандарты, регламентирующие допустимую величину степени кристалличности в преформе. Диаметр пятна кристалличности в области литника не должен быть больше 6 мм. Общая степень растяжения преформы при производстве бутылок порядка десяти (произведение степени растяжения вдоль и поперек оси). Это означает, что любой дефект, который имеет преформа (пятно, царапина, облой в местах стыковки формообразующих частей и т.п.), переходят на бутылку в десятикратном масштабе. Поэтому международные стандарты строго регламентируют требования к качеству поверхности и микродефектам преформ. Не должно быть видимых глазу включений, непроплавов, царапин. Образующийся при литье облой обламывается при укладке преформ и под действием электростатических сил прилипает к поверхности преформы, а затем, подплавляясь при выдуве бутылки, уродует поверхность изделия. Поэтому величина облоя должна быть минимальной. Для того чтобы эти требования выполнить, необходимо изготавливать пресс-формы с высокими размерной точностью и качеством поверхностей.
О. Сабсай, www.plastinfo.ru |