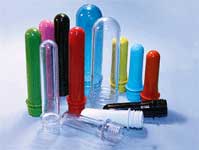
Технологии производства гранулята ПЭТ упаковочного назначения трдиционно состоят из непрерывной поликонденсации (СР), в ходе которой производятся исходные гранулы с характеристической вязкостью от 0,55 до 0,62 и содержанием ацетальдегида от 40 до 100 ррm. Для производства ПЭТ с вязкостью 0,76 - 0,85 и содержанием ацетальдегида менее 1 ррm, что удовлетворяет требования к материалам для упаковки пищевых продуктов, например, преформам и экструзионной пленке, за традиционной поликонденсацией должна последовать поликонденсация в твердой фазе (SSP). Сравнение двухреакторной технологии (2R) «расплав в смолу» (MTR) с четырехреакторной технологией (4R) и поликонденсацией в твердой фазе (SSP) Во время поликонденсации в твердой фазе происходит сушка, кристаллизация и темперирование гранул инертным газом при температуре около 200°С. Этот процесс, который увеличивает производственные затраты примерно на 100 Евро/тонну, оказывается весьма дорогостоящим и чувствительным. Когда несколько лет назад ценовая конкуренция в области ПЭТ-гранулята усиливалась, Uhde Inventa-Fischer, одна из лидирующих инжиниринговых компаний с опытом более 40 лет в области производства полиэфиров, начала разработку новой технологии MTR®, которая позволяет сэкономить как минимум 80 Евро/тонну ПЭТ. Это предоставляет производителям значительные выгоды без ущерба качеству по сравнению с предыдущими технологиями. 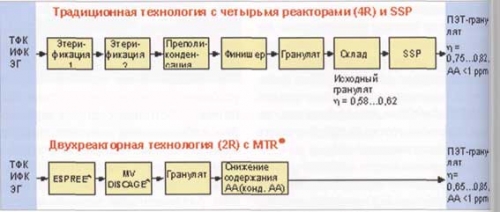
На первом этапе имеющаяся четырех-реакторная технология непрерывной поликонден-сации была замещена новой двухреакторной технологией (2R), рассчитанной на мини-мальное время пребывания и низкие температуры реакции, чтобы ограничить возможность деструкции ПЭТ. Эта технология была представлена общественности в начале 2003 года после успешного запуска прототипа установки в 2002 г. Процесс 2R состоит из принципиально нового реактора башенного типа ESPREE и финишера DISCAGE. Помимо таких преимуществ, как высокое качество продуктов и низкая потребность в техобслуживании, предоставляется возможность экономить 30-40 Евро/тонну ПЭТ производственных затрат по сравнению с предыдущими технологиями непрерывной поликонденсации. На втором этапе необходимо было обеспечить требования к высокому уровню качества при проведении поликонденсации ПЭТ в расплаве с получением характеристической вязкости гранул 0,85, чтобы избежать дорогостоящих промежуточных стадий, особенно поликонденсации в твердой фазе и сопутствующих процессов. Уже несколько лет реактор UIF DISCAGE используется для окончательной поликонденсации полимеров высокой вязкости в расплаве (финишинг) при производстве полибутилентерефталата (ПБТ), поликарбоната (ПК) и модифицированных полиэфиров. До настоящего времени его конструктивные принципы послужили прочным базисом для недавно созданного низкотемпературного реактора MV-DISCAGE (MV = средняя характеристическая вязкость) для процесса MTR, который особенно рекомендуется для пищевой упаковки. Предложенные решения вначале апробировались на пилотном финишере, связанном с системой MTR, a затем в течение нескольких лет проверялись и совершенствовались в научно-исследовательских центрах UIF в Швейцарии и Берлине. В результате удалось добиться качества продукта, превосходящее получаемое по технологии поликонденсации в твердой фазе (SSP). Это было успешно подтверждено в условиях промышленного производства бутылок без использования добавки для поглощения ацетальдегида. Качество ПЭТ-гранул: Сравнение технологий MTR и SSP 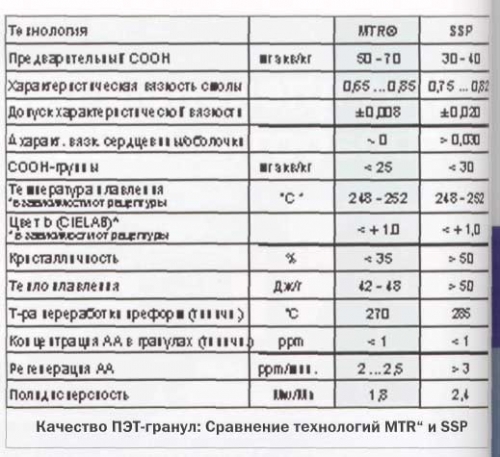
Третий этап заключался в разработке процесса дальнейшей максимально мягкой обработки для получения смолы с низким содержанием ацетальдегида, готовой для производства преформ. В результате всех предшествующих шагов была создана технология, получившая название «Расплав в смолу» (MTR). Необходимо было пересмотреть процесс непрерывной поликонденсации с тем, чтобы снизить содержание ацетальдегида до величины менее 10 ppm в системе гранулирования продавливанием через перфорированную плиту, где требуется еще более низкое содержание ацетальдегида в расплаве после финишинга. Для этого потребовалось улучшить условия протекания процесса, установить дополнительные встройки в реакторе ESPREE, обеспечить невозможность протекания реакции в кубе реактора MV-DISCAGE, внести изменения в процесс разгрузки полимера, в расплавопровод и процесс фильтрации, разработать специальную конструкцию гранулятора, предусмотреть темперирование гранул до уровня кристаллизации менее, чем 25%, и, в заключение, дегазацию гранул и удаление следов разного рода летучих компонентов, в т.ч. и ацетальдегида. Обнаружено, что можно достичь уровней содержания ацетальдегида в грануляте менее 1 ррm и даже 0,5 ррm в зависимости от рецептуры, что сопоставимо с общепринятыми методами. Содержание ацетальдегида во время обработки Благодаря уменьшенной кристалличности по сравнению с продуктами, полученными методом SSP, требуется меньше энергии для плавления при экструзии на машине по производству преформ. Следовательно, минимизируется дальнейшее выделение ацетальдегида. 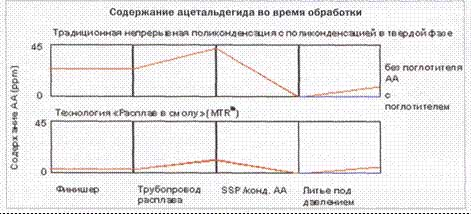
Замечания к продукции Таблица сравнения гранулята ПЭТ по технологии MTR и SSP демонстрирует, что все типичные параметры качества продукта при производстве по технологии MTR выгодно отличаются, что стало возможным благодаря мягкой обработке на протяжении всего процесса, от стадии этерификации до стадии дегазации. Обнаружено, что продавливаемые через перфорированную плиту сферические гранулы, содержащие в среднем более 75% аморфной фазы и приобретавшие в процессе резки определенную ориентацию крайних молекул и транс-кристаллическую структуру, теряют склонность к слипанию в ходе следующих затем темперирования или сушки. Поскольку этот управляемый феномен типичен для продавливаемых через перфорированную плиту гранул и уже известен при производстве других полимеров, они значительно отличаются от цилиндрических ПЭТ-гранул, кристалличность которых должна составлять более чем 35% для последующих! процессов темперирования, и более 45% для поликонденсации в твердой фазе. Конечно, гранулы сферической формы меньше склеиваются, ибо поверхность контакта меньше, чем при цилиндрической форме. Другим преимуществом таких гранул является поверхность, напоминающая апельсиновую корку, которую можно рассмотреть в микроскоп, что объясняется макроэффектами местного выпаривания и кавитации от потока воды, уносившего гранулы после резки. Такая структура поверхности совместно с другими вышеупомянутыми эффектами позволяет поддерживать общую кристалличность на самом! низком уровне для обеспечения кратковременной последующей дегазации. Замечания к переработке Процесс дегазации для удаления ацетальдегида и других летучих компонентов из гранул в принципе подобен другим методам сушки ПЭТ, осуществлявмым небольшим потоком газа, обычно воздуха, при температурах от 150°С до 180°С, чтобы избежать деградации за время пребывания в емкости дегазации в течение нескольких часов. Изначальная характеристическая вязкость расплава полимера 0,82-0,85 сохраняется на протяжении всего процесса MTR и обеспечивает низкую скорость кристаллизации, поэтому время пребывания не оказывается критическим фактором. Для дальнейшей переработки сферических гранул с высоким уровнем характеристической вязкости нет необходимости в большей кристалличности, в отличие от технологии поликонденсации в твердой фазе (SSP). Однако при кристаллизации расплава при температурах, обеспечивающих низкую скорость кристаллизации, необходим строгий контроль температуры воды и времени пребывания в системе резки и обезвоживания, чтобы поддерживать среднюю кристаллизацию на уровне не более 25%. В то же время, тепло расплава, остающееся в гранулах, максимально используется для последующей сушки и дегазации. Стало очевидно, что первичное темперирование и дегазация гранул протекает легче при низкой кристалличности, что обеспечивает краткое время пребывания в аппарате при содержании ацетальдегида ниже 1 ррm. Разумеется, на данном этапе потребуется подача некоторого количества тепла, чтобы содействовать удалению ацетальдегида и обеспечить управление производительностью за счет регулировки скорости кристаллизации. Это можно осуществить псевдоожижением гранул низкоскоростным потоком нагретого воздуха, поступающего в микроотверстия перфорированных виброконвейеров и протекающего через слой гранулята. В циркулирующем воздухе поддерживается определенная влажность, которая содействует извлечению оставшегося ацетальдегида, содержание которого на данном этапе составляет от 3 до 5 ррm. Дальнейшая дегазация осуществляется в емкости выдерживания в адиабатических условиях за счет уноса ацетальдегида низкоскоростным потоком нагретого воздуха, т. е. методом, использованным для осушки ПЭТ в течение десятилетий. При этом содержание оставшегося в гранулах ацетальдегида снижается до 0,5 - 0,9 ррm без увеличения вязкости. Гранулы впоследствии охлаждаются до температуры расфасовки в кожухотрубчатом теплообменнике, встроенном в нижнюю часть упомянутой емкости. Экономия сырья - технологии MTR и SSP Сравнение с технико-экономической точки зрения предыдущих систем про¬изводства ПЭТ с новой технологией 2R-MTR наглядно демонстрирует, что при применении последней, значительная экономия достигается уже при мощности установки 200 - 300 тонн/сутки. Для установки, работающей по технологии СР с SSR потребуется, для того, подобную выгоду можно извлечь лишь при мощности 609 тонн/сутки. Это позволит небольшим производителям быть конкурентоспособными на мировом рынке ПЭТ - гранулята. 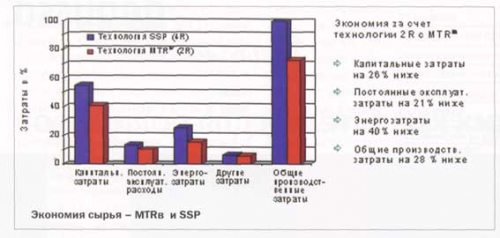
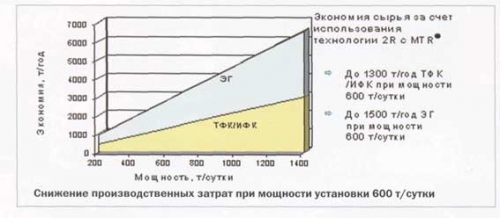
Заключение Новая технология 2R-MTR предоставляет возможность производить ПЭТ гранулят выгодным способом и экономить около 80 Евро производственных затрат на тонну продукции. Она отличается высокой гибкостью при переходе на другие марки и мощности, поскольку представляет из себя кратковременный процесс, при котором оконча тельная вязкость уже достигается на стадии пребывания ПЭТ в расплаве. Процесс характеризуется простым, не критическим режимом работы. Каче¬ство продукта превосходит полученный по предыдущим технологиям и полностью удовлетворяет производи¬телей преформ и бутылок. Смола отве¬чает стандартам FDA и ЕС, поскольку для технологии MTR не требуется применение недопустимых реагентов или добавок. MTR - это высокоэффектив¬ное решение и шаг в будущее производства ПЭТ-гранулята. А. ван Эндерт, вице-президент по инжинирингу, директор по полиэфирной продукции компании Uhde Inventa-Fischer Uhde Inventa-Fischer AG Reichenauerstr. , CH-7013 Domat/Ems Швейцария Тел.: +41 81 632 63 11, факс: +4181 632 7403 или: Holzhauserstr. 157-159, D-13509 Berlin Германия Тел.: +49 30 435 67 5, факс: +49 30 435 67 699
|