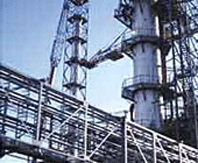 Технология производства бензола и сферы его использования 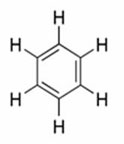 Бензол (C6H6, PhH) — ароматический углеводород. Входит в состав бензина, широко применяется в промышленности, является исходным сырьём для производства лекарств, различных пластмасс, синтетической резины, красителей. Бензол – один из наиболее распространенных химических продуктов и самое распространенное ароматическое соединение. В физическом весе пластмасс около 30%, в каучуках и резинах – 66%, в синтетических волокнах – до 80% приходится на ароматические углеводороды, родоначальником которых является бензол. Бензол входит в состав сырой нефти, но в промышленных масштабах по большей части синтезируется из других её компонентов. Свойства продукта и технические характеристики Бензол - бесцветная жидкость со своеобразным нерезким запахом. Температура плавления — 5,5 °C, температура кипения — 80,1 °C, плотность — 0.879 г/см³, молекулярная масса — 78,11г/моль. С воздухом образует взрывоопасные смеси, хорошо смешивается с эфирами, бензином и другими органическими растворителями, с водой образует смесь с температурой кипения 69,25 °C. Растворимость в воде 1.79 г/л (при 25°C). Токсичен, опасен для окружающей среды, огнеопасен. Бензол по составу относится к ненасыщенным углеводородам (гомологический ряд CnH2n-6), но в отличие от углеводородов ряда этилена C2H4, при жёстких условиях проявляет свойства присущие насыщенным углеводородам, более склонен к реакциям замещения. Свойства бензола объясняются наличием в его структуре сопряжённого π-электронного облака. Транспортировку бензола осуществляют в железнодорожных цистернах и автоцистернах, на баржах и в металлических бочках. Перекачивание из одного сосуда в другой происходит в закрытой системе, так как бензол ядовит. В зависимости от технологии производства получают различные марки бензола. Бензол нефтяной получают в процессе каталитического риформинга бензиновых фракций, каталитического гидродеалкилирования толуола и ксилола, а также при пиролизе нефтяного сырья. В зависимости от технологии производства и назначения установлены следующие марки нефтяного бензола: высшей очистки, очищенный и для синтеза. Нормы для марок регламентированы ГОСТ 9572-93. ГОСТ 8448-61 распространяется на каменноугольный и сланцевый бензол, получаемый в процессе термической переработки каменных углей и сланцев. Выпускается двух марок: для синтеза и для нитрации. Бензол сырой каменноугольный представляет собой смесь, содержащую 81-85% бензола, 10-16% толуола, 1-4% ксилола. Содержание примесей не регламентируются. ГОСТ 5955-75 соответствует бензолу как химическому реактиву, применяемому в лабораториях. Ниже приведены технические характеристики марок нефтяного и каменноугольного бензола согласно вышеперечисленным ГОСТам.
Техническая характеристика марок каменноугольного бензола Наименование нормируемых показателей | Норма для марки | Для синтеза | Для нитрации | Высший сорт | 1-й сорт | Внешний вид и цвет | Прозрачная жидкость, не содержащая взвешенных и осевших на дно посторонних примесей, в т.ч. и воды, не темнее цвета раствора 0.003 г K2Cr2O7 в 1 дм3 . | Плотность при 20С (г/см3) | 0,877-0,880 | 0,877-0,880 | 0,877-0,880 | Пределы перегонки: 95% объема от начала кипения перегоняется в интервале температур С, не более (включая температуру кипения чистого бензола 80,1С) | 0,6 | 0,6 | 0,7 | Температура кристаллизации (С, не ниже) | 5,3 | 5,3 | 5,2 | Массовая доля примесей (%, не более): | | | | Н/гептана | - | - | - | Метилциклогексана + толуола | - | - | - | Окраска серной кислоты (номер образцовой шкалы, не более) | 0,1 | 0,1 | 0,15 | Бромное число (г/100см3 бензола, не более) | - | - | 0,06 | Массовая доля (%, не более): | | | | Сероуглерода | 0,00007 | 0,0001 | 0,005 | Тиофена | 0,0002 | 0,0004 | 0,02 | Сероводорода и меркаптанов | - | - | Отсутствие | Общей серы | 0,0001 | 0,00015 | 0,015 | Испытание на медной пластинке | Выдерживает | Реакция водной вытяжки | Нейтральная |
Техническая характеристика марок нефтяного бензола
Наименование показателя | Норма для марки | | высшей очистки | очищенный | для синтеза | ОКП24 1411 0120 | ОКП24 1411 0130 | ОКП 24 1411 0200 | высшего сорта | первого сорта | ОКП24 1411 0220 | ОКП24 1411 0230 | 1. Внешний вид и цвет | Прозрачная жидкость, не содержащая посторонних примесей и воды, не темнее раствора 0,003 К2Cr2О7 в 1 дм3 воды | 2. Плотность при 20 °С, г/см3 | 0,878-0,880 | 0,878-0,880 | 0,878-0,880 | 0,878-0,880 | 3. Пределы перегонки 95 %, °С, не более (включая температуру кипения чистого бензола 80,1 °С) | - | - | 0,6 | 0,6 | 4. Температура кристаллизации, °С, не ниже: | 5,4 | 5,4 | 5,35 | 5,3 | 5. Массовая доля основного вещества, %, не менее: | 99,9 | 99,8 | 99,7 | 99,5 | 6. Массовая доля примесей, %, не более: | | | | | н-гептана | 0,01 | 0,06 | 0,06 | - | метилциклогексана и толуола | 0,05 | 0,09 | 0,13 | - | метилциклопентана | 0,02 | 0,04 | 0,08 | - | толуола | - | 0,03 | - | - | 7. Окраска серной кислоты, номер образцовой шкалы, не более: | 0,1 | 0,1 | 0,1 | 0,15 | 8. Массовая доля общей серы, %, не более: | 0,00005 | 0,0001 | 0,0001 | 0,00015 | 9. Реакция водной вытяжки | Нейтральная |
Области применения бензола Бензол – один из наиболее распространенных химических продуктов и самое распространенное ароматическое соединение. В физическом весе пластмасс около 30%, в каучуках и резинах – 66%, в синтетических волокнах – до 80% приходится на ароматические углеводороды, родоначальником которых является бензол. Основные области применения бензола - производство этилбензола, кумола и циклогексана. На долю этих продуктов приходится около 70% мирового потребления бензола. Этилбензол является важным нефтехимическим продуктом, основной объем которого используются для производства стирола. Наиболее значимыми продуктами, в производстве которых используется фенол, является бисфенол-А и фенолформальдегидные смолы. Циклогексан используется в качестве сырья для получения капролактама, растворителя. Капролактам в свою очередь применяется для производства термопластичных смол (полиамид 6), капроновых волокон и нитей. Нитробензол является полупродуктом для получения анилина. Бензол также используется для получения анилина, малеинового ангидрида, является сырьем для производства синтетических волокон, каучуков, пластмасс. Бензол применяется как компонент моторного топлива для повышения октанового числа, как растворитель и экстрагент в производстве лаков, красок, поверхностно-активных веществ. Более подробно области применения бензола рассмотрены в главе 5. ТЕХНОЛОГИЯ ПРОИЗВОДСТВА Историческая справка Впервые бензол описал немецкий химик Иоганн Глаубер, который получил это соединение в 1649 году в результате перегонки каменноугольной смолы. Но ни названия вещество не получило, ни состав его не был известен. Своё второе рождение бензол получил благодаря работам английского физика Майкла Фарадея, который в 1825 году выделил его из жидкого конденсата светильного газа. Великое открытие Фарадея было сделано случайно. В начале девятнадцатого века в Лондоне для уличного освещения стали использовать светильный газ, получаемый из каменноугольной смолы. Однако он имел ряд существенных недостатков: при его горении не только выделялось большое количество дыма, чем были весьма недовольны жители туманного Альбиона, но и со временем этот газ утрачивал свою горючесть, а на дне баллонов оседала неизвестная маслянистая жидкость. Этой проблемой, исключительно из практических соображений, и занялся Майкл Фарадей. Результатом множества разнообразных испытаний стала белая кристаллическая масса, получаемая вымораживанием остатка «светильного газа» при температуре 7 °С. В 1833 году немецкий физик и химик Эйльгард Мичерлих получил бензол при сухой перегонке кальциевой соли бензойной кислоты (именно от этого и произошло название бензол). Современное представление о свойствах и электронной природе связей в бензоле основывается на гипотезе Лайнуса Полинга, который предложил изображать молекулу бензола в виде шестиугольника с вписанной окружностью, подчёркивая тем самым отсутствие фиксированных двойных саязей и наличие единого электронного облака, охватывающего все шесть атомов углерода цикла. В XIX веке коммерческая ценность бензола была ограниченной. Он применялся в первую очередь как растворитель. В XX столетии производители бензина обнаружили у бензола ряд свойств, позволяющих использовать его в качестве компонента автомобильного топлива (высокое октановое число). Как следствие, возник экономический стимул для более полного выделения бензола, который получали как побочный продукт при коксовании в производстве стали. Начало Второй мировой войны выявило и другие – химические – области применения бензола, в основном в производстве взрывчатых веществ. В результате, в середине XX века не только бензол коксования стал направлять в химическую промышленность (а не использоваться как компонент бензина), но и сама нефтеперерабатывающая промышленность начала производить огромное количество бензола для обеспечения потребностей химической индустрии. Так, крупнейший потребитель бензола – нефтяная индустрия – стал его главным производителем. Постоянно возрастающие потребности нефтехимической промышленности в бензоле привели к появлению новых, усовершенствованных процессов его производства – каталитического риформинга, деалкилирования толуола, а также более нового – диспропорционирования толуола. Случайный вклад в развитие отрасли был сделан в 1970-е годы, когда заводы по производству олефинов начали использовать тяжелый газойль как сырье и получать бензол в качестве побочного продукта. Промышленные методы производства бензола
Производство бензола основано на переработке целого ряда сырьевых компонентов: нафты, толуола, тяжелой фракции пиролиза, смолы коксования угля, поэтому выпуск бензола ведется как на предприятиях нефтехимии, так и на металлургических заводах. В зависимости от технологии получения и назначения бензол подразделяют на бензол нефтяной и каменноугольный «высшей очистки», «для синтеза», «высшего сорта», «первого сорта», «для нитрации», «технический», «сырой». Наиболее старый метод промышленного получения бензола - выделение его из предварительно охлажденных пирогазовых продуктов коксования каменных углей абсорбцией органическими поглотителями, например маслами каменно-угольного и нефтяного происхождения; для отделения поглотителя используют перегонку с водяным паром. От примесей (например, тиофена) сырой бензол отделяют гидроочисткой. Основное количество бензола получают каталитическим риформингом (470-550°С) нефтяной фракции, выкипающей при 62-85°С. Бензол высокой чистоты получают экстрактивной перегонкой с диметилформамидом. Бензол выделяют и из жидких продуктов пиролиза нефтепродуктов, образующихся в производствах этилена и пропилена. Этот способ является более выгодным экономически, поскольку в образующейся смеси продуктов на долю бензола приходится около 40% против 3% при риформинге. Однако сырьевые ресурсы для этого способа весьма ограничены, поэтому большую часть бензола производят риформингом. Доля коксохимического бензола в общем балансе невелика. Состав смесей, образующихся в результате пиролиза и риформинга нефтяного сырья Состав смеси | Риформинг, % | Пиролиз, % | Бензол | 3 | 40 | Толуол | 13 | 20 | Ксилол | 18 | 4-5 | Этилбензол | 5 | 2-3 | Высшая ароматика | 16 | 3 | Неароматические соединения | 45 | 28-31 |
Источник: Евразийский химический рынок При избытке ресурсов толуола бензол производят также деалкилированием последнего, которое проводят термическим способом при 600-820°С в присутствии водорода и водяного пара или каталитически при 227-627°С в присутствии цеолитов или оксидных катализаторов.
Получение бензола из каменноугольного сырья Для получения кокса на металлургических предприятиях используют сухую перегонку каменного угля, который представляет собой в основном смесь полиядерных ароматических соединений с высокой молекулярной массой. В процессе сухой перегонки каменный уголь нагревают без доступа воздуха до 1200-1500ºС. Из 1 тонны угля можно получить около 680 кг кокса и 227 кг каменноугольного газа, каменноугольной смолы и каменноугольного масла. Каменноугольное масло (сырой бензол) – это смесь бензола (63%), толуола (14%) и ксилолов (7%). Для коксохимического бензола необходима более глубокая очистка от ненасыщенных углеводородов, особенно от н-гептана и метилциклогексана. Коксохимический бензол подвергается ректификации трижды: при отборе сероуглеродной фракции, перегонке очищенной фракции БТК – получение бензола «для нитрации» - и окончательном выделении бензола после дополнительной очистки – получение бензола высших марок. Получение бензола коксованием угля является традиционным и наиболее старым способом, однако в 1950-е годы он стал терять актуальность, так как рынок бензола стал расти существенно быстрее, чем рынок стали и проявилось производство бензола на основе переработки нефти. Так, США - в силу особенностей природных условий быстро переориентировались на производство бензола из нефтяного сырья, как более дешевого. И когда в 1960 году в Западной Европе даже не задумывались о получении ароматических соединений из сырой нефти, в США уже 83% этих веществ получали именно из нее. К 1990 году США полностью отказались от использования каменноугольного сырья в производстве ароматики, а в Западной Европе к этому времени из нефти получали 93% бензола и его гомологов. В настоящее время в Европе существует только четыре производства бензола, работающих на каменноугольном сырье: в Германии, Польше, Чехии и Бельгии. Производство бензола в России еще тесно связано с конъюнктурой рынка металлов, основная часть которых перерабатывается на 10 имеющихся предприятиях.
Получение бензола каталитическом риформингом нефтяных фракций Содержание бензола в сырой нефти составляет обычно не более 0,5-1,0%. Этого недостаточно, для того чтобы оправдать затраты на оборудование необходимое для выделения бензола из сырой нефти. Гораздо более важным и коммерчески выгодным источником получения бензола является процесс каталитического риформинга, на долю которого приходится большая часть производимого в мире бензола. Каталитический риформинг предназначен для повышения октанового числа прямогонных бензиновых фракций путём химического превращения углеводородов, входящих в их состав, до 92-100 пунктов. Процесс ведётся в присутствии алюмо-платино-рениевого катализатора. Повышение октанового числа происходит за счёт увеличения доли ароматических углеводородов. Продукты, полученные в результате риформинга узких бензиновых фракций, подвергаются разгонке с получением бензола, толуола и смеси ксилолов. Сырьем для каталитического риформинга служит тяжелая бензиновая фракция (нафта, или лигроин) – смесь парафинов, нафтенов и ароматических углеводородов фракции С6-С9. В ходе каталитического риформинга состав нафты меняется следующим образом: - парафины превращаются в изопарафины, - парафины превращаются в нафтены, - нафтены превращаются в ароматические углеводороды, включая бензол. Также образуются побочные продукты: - парафины и нафтены могут распадаться с образование бутана и более легких газов, - боковые звенья ароматических соединений и нафтенов могут отщепляться и также давать бутан и более легкие газы. Оба побочных процесса приводят к понижению октанового числа и снижению экономических показателей. Мощность установок риформинга составляет от 300 до 1000 тыс. тонн и более в год по сырью. Оптимальным сырьём является тяжёлая бензиновая фракция с интервалами кипения 85-180°С. Сырьё подвергается предварительной гидроочистке - удалению сернистых и азотистых соединений, даже в незначительных количествах необратимо отравляющих катализатор риформинга. Установки риформинга существуют 2-х основных типов - с периодической и непрерывной регенерацией катализатора - восстановлением его первоначальной активности, которая снижается в процессе эксплуатации. В России для повышения октанового числа в основном применяются установки с периодической регенерацией, но в 2000-х гг. в Кстово и Ярославле введены установки и с непрерывной регенерацией, которые эффективнее технологически, однако, стоимость их строительства выше. Процесс осуществляется при температуре 500-530°С и давлении 18-35 атм (2-3 атм на установках с непрерывной регенерацией). Основные реакции риформинга поглощают существенные количества тепла, поэтому процесс ведется последовательно в 3-4 отдельных реакторах, объёмом от 40 до 140 м3, перед каждым из которых продукты подвергаются нагреву в трубчатых печах. Наличие нескольких реакторов позволяет поддерживать различные рабочие условия. В каждом из реакторов проходит одна из реакций, перечисленных выше. Выходящая из последнего реактора смесь отделяется от водорода, углеводородных газов и стабилизируется. Полученный продукт – стабильный риформат – охлаждается и выводится с установки. При регенерации осуществляется выжиг образующегося в ходе эксплуатации катализатора кокса с поверхности катализатора с последующим восстановлением водородом и ряд других технологических операций. На установках с непрерывной регенерацией катализатор движется по реакторам, расположенным друг над другом, затем подаётся на блок регенерации, после чего возвращается в процесс. Продукты, полученные в результате риформинга узких бензиновых фракций, подвергаются разгонке с получением бензола, толуола и смеси ксилолов - центральную фракцию, кипящую в узком интервале температур. Для итогового выделения бензола используют один из двух процессов: извлечение растворителем или экстрактивную перегонку. Выход бензола на установках каталитического риформинга зависит от состава сырья. Нафта различается по содержанию парафинов, нафтенов и ароматики (углеводороды группы ПНА). Высокое содержание нафтенов и ароматических веществ – признак хорошего сырья для риформинга, а высокое содержание парафинов означает, что это сырье лучше использовать для промышленного получения олефинов. Выход бензола также зависит условий проведения процесса, которые определяются экономическими соображениями.
Получение бензола из смолы пиролиза Наиболее экономически выгодным является метод выделения бензола из жидких продуктов пиролиза нефтепродуктов, образующихся в производстве этилена и пропилена. Производство бензола по данной технологии напрямую зависит от производства олефинов, сырья для производства олефинов и рынка смолы пиролиза (пироконденсата), который является весьма ограниченным. Выделение бензола из пироконденсата заключается в гидроочистке соответствующей фракции продуктов пиролиза от непредельных и сернистых соединений, последующем гидродеалкилировании полученной смеси, содержащей бензол, толуол и ксилолы и последующей доочистке полученного бензола. Разделение БТК-фракции с получением бензола проводят экстракцией растворителем или экстрактивной перегонкой. Наиболее часто применяется экстракция смесью N-метилпирролидона с этиленгликолем. Также в качестве экстрагентов применяют гликоли, сульфолан, диметилсульфоксид и др. растворители.
Получение бензола гидродеалкилированием толуола В процессе гидродеалкилирования (дезалкилирования) толуол смешивают с потоком водорода, нагревают и подают в реактор. Метильная группа отщепляется при прохождении толуола через слой катализатора с образованием бензола. Поток, выходящий из реактора, фракционируют на водород, метан и другие легкие газы и бензол. Бензол, как правило, очищают контактно-земляным методом. Полученный продукт представляет собой чистый бензол (марки «для нитрования»). Выход бензола на установке гидродеалкилирования толуола достигает 96-98%.
Материальный баланс процесса гидродеалкилирования толуола Сырье | Масса, кг | Продукты | Масса, кг | Толуол | 545 | Бензол | 454 | Водород | 12 | Метан и пр. газы | 103 |
Получение бензола диспропорционированием толуола В течение последних 15 лет спрос на бензол и ксилолы начал значительно опережать спрос на толуол. В результате был разработан технологический процесс диспропорционирования толуола, позволяющий повысить объем производства этих продуктов. При диспропорционировании толуола происходит восстановаление до бензола с потерей метильной группы (т.е. гидродеалкилирование) и окисление до ксилола, так как метильная группа присоединяется к другой молекуле толуола (переалкилирование). Катализаторами процесса служат платина и палладий, редкоземельные металлы и неодим, нанесенные на оксид алюминия, а также хром, нанесенный на алюмосиликат. Толуол подается в реактор, где находится неподвижный слой катализатора. В реактор также вводят некоторое количество водорода для подавления осаждения углеводородов на поверхности катализатора. Режим работы реактора – температура 650-950ºС и давление 10,5-35 атм. Поток, выходящий из реактора, охлаждают, из него извлекают водород на рецикл. Остальную смесь трижды перегоняют с выделением на первой стадии неароматических соединений, на второй – бензола, на третьей – ксилолов. Материальный баланс процесса диспропорционирования толуола
Сырье | Масса, кг | Продукты | Масса, кг | Толуол | 544 | Бензол | 454 | Водород | 3 | Ксилолы | 606 | Метан и пр. газы | 28 |
Как показывает материальный баланс процесса, выход продуктов за одну стадию довольно высок. При экономической обоснованности получения бензола из толуола, выбор между процессами гидродеалкилирования и диспропорционирования зависит от других экономических соображений, в частности от необходимого конечного состава продуктов. Области применения бензола Спрос на бензол определяется развитием потребляющих его отраслей. Основные области применения бензола - производство этилбензола, кумола и циклогексана и анилина. Этилбензол является важным нефтехимическим продуктом, основной объем которого используются для производства стирола. Более 65 % производимого стирола в свою очередь используется для производства полистирола. Оставшаяся часть используется в производстве акрилонитрил-бутадиен-стирола (АБС) и стирол-акрилонитрила (САН), ненасыщенных полиэфиров и стирол-бутадиенового каучука. Основной сферой применения фенола является химическая промышленность. Наиболее значимыми продуктами, в производстве которых используется фенол, является бисфенол-А и фенолформальдегидные смолы. Фенол также используется в производстве синтетического волокна капрона, красителей, пестицидов, лекарственных препаратов (аспирин, салол). Разбавленные водные растворы фенола (карболка, 5%) применяют для дезинфекции помещений, белья. Циклогексан используется в качестве сырья для получения капролактама, растворителя. Капролактам в свою очередь применяется для производства термопластичных смол (полиамид 6), капроновых волокон и нитей. Нитробензол является полупродуктом для получения анилина, который используется для производства метилдиизоцианатов, из которых получают полиуретаны. Анилин также используется при производстве искусственных каучуков, гербицидов и красителей. Бензол также используется для получения малеинового ангидрида, является сырьем для производства синтетических волокон, каучуков, пластмасс. Применяется как компонент моторного топлива для повышения октанового числа, как растворитель и экстрагент в производстве лаков, красок, поверхностно-активных веществ. Схематично основные синтезы на основе бензола можно представить следующим образом:
Схема основных синтезов на основе бензола 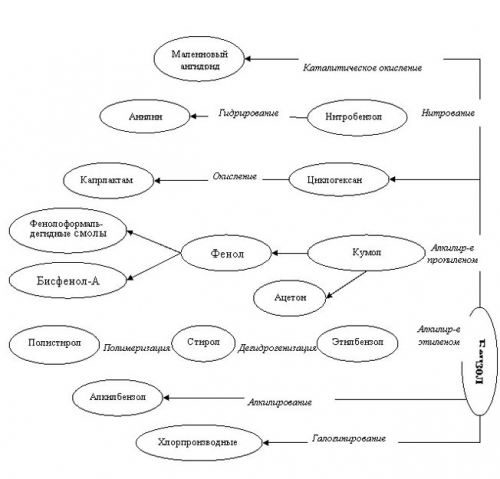
Применение продуктов переработки бензола Продукт | Химическая формула | Применение | Стирол |  | Основная сфера применения – производство полистирола. | Фенол | 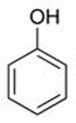 | Применяют в производстве бисфенола-А, фенолформальдегидных пластмасс, синтетического волокна капрона, красителей, пестицидов, лекарственных препаратов (аспирин, салол). Разбавленные водные растворы фенола (карболка, 5%) применяют для дезинфекции помещений, белья. | Капролактам | 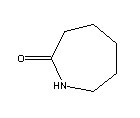 | Является основным сырьем для получения полиамида-6 (нейлон, капрон, ультрамид). | Анилин | 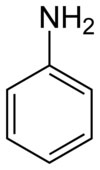 | Применяется в качестве полупродукта в производстве полиуретанов, красителей, взрывчатых веществ и лекарственных средств (сульфаниламидные препараты). | Малеиновый ангидрид | 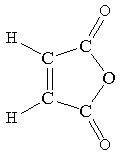 | Применяется для получения полимерных материалов, алкидных и полимерных смол, в производстве синтетических волокон, моющих средств, фармацевтических препаратов, присадок и стабилизаторов топлива, фумаровой и яблочных кислот, сельскохозяйственных препаратов | Алкилбензолы | 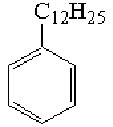 | Используются как поверхностно-активные вещества. |
C текущей ситуацией и прогнозом развития российского рынка бензола можно познакомиться в отчете Академии Конъюнктуры Промышленных Рынков «Рынок бензола в России». Об авторе: Академия Конъюнктуры Промышленных Рынков оказывает три вида услуг, связанных с анализом рынков, технологий и проектов в промышленных отраслях - проведение маркетинговых исследований, разработка ТЭО и бизнес-планов инвестиционных проектов. • Маркетинговые исследования • Технико-экономическое обоснование • Бизнес-планирование
Академия Конъюнктуры Промышленных Рынков Тел.: (495) 918-13-12, (495) 911-58-70 E-mail: mail@akpr.ru WWW: www.akpr.ru |