От ПП блок-сополимеры отличаются более высокой ударной прочностью при низких температурах и более высокой эластичностью. За прошедшие 30 лет технология синтеза ПП и БС значительно усовершенствована. Использование катализаторов Циглера-Натта, обладающих необычайно высокой активностью, позволило упростить производство и сократить стадии промывки полимера от катализатора. Однако основные стадии синтеза сохранили свою главную функцию - формирование оптимальной структуры БС. Сложившаяся к настоящему времени технологическая схема синтеза включает несколько основных узлов (рисунок). Реакторный узел 1 предназначен для синтеза ПП или сополимера пропилена м этиленом (1-5% звеньев этилена). Синтез ПП может проводиться в одном или нескольких реакторах [1-4], в среде газообразного [5] или жидкого пропилена [6-10], либо инертного растворителя [11]. Конструкция реакторов также разнообразна: аппарат с псевдоожиженным слоем порошка [5], емкостный реактор идеального перемешивания с мешалкой [1-4], петлевой реактор. Несмотря на разнообразие конструкций, главная их функция - получение в единицу времени заданного количества ПП определенной молекулярной массы. Молекулярная массы, как правило, регулируется водородом [12]. Смесь порошкообразного ПП с пропиленом непрерывно поступает из реакторного узла 1 в узел удаления избыточного пропилена 2, где часть пропилена отделяется от реакционной массы и возвращается в рецикл. Некоторые технологические решения не предусматривают узла 2 [6, 13, 14], и весь пропилен поступает в следующий реакторный узел 3, где производится сополимеризация этилена с пропиленом. Узел 3 может состоять из одного или нескольких последовательно расположенных реакторов [1-4]. В Узел 3 не вводят катализатор, поступающий из узла 1 вместе с ПП. Для сополимеризации подают этилен и в необходимых случаях различные добавки. В узле 4 полимер полностью отделяется от мономера и поступает на дальнейшую обработку: сушку, разложение катализатора, промывку (при необходимости), введение добавок, грануляцию. Сополимеризация чаще всего проводится в среде газообразных мономеров [5, 9, 10] или инертного растворителя [11], значительно реже - в среде жидкого пропилена [6, 14], так как в последнем случае ограничивается диапазон вариаций состава сополимера (СЭП) из-за высокого парциального давления пропилена. 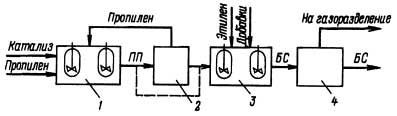
Рис. Принципиальная блок-схема получения блок-сополимера пропилена и этилена по непрерывной технологии. 1 - реакторный узел для синтеза ПП; 2 - узел удаления избыточного пропилена; 3 - реакторный узел синтеза СЭП; 4 - узел дегазации БС. Если узел 1 имеет один реактор идеального перемешивания, то время пребывания в нем различных частиц катализатора может изменяться от нескольких минут до десятков часов при среднем значении, равном нескольким часам [15]. В связи с этим частицы катализатора на выходе из реактора имеют на своей поверхности различное количество ПП. После длительного пребывания в реакторе 1 количество ПП на них велико и, соответственно, активность таких частиц меньше, чем частиц с небольшим количеством ПП. В ректоре 3 на наиболее активных частицах образуется больше СЭП, чем на менее активных. В итоге получается композиция из частиц БС разного состава, и эта неоднородность влияет на качество продукта. В готовый продукт попадают частицы БС, содержащие фазу СЭП в значительно большем количестве, чем среднее содержание СЭП. Например, если в БС обычно содержится 5-20% фазы СЭП, то в отдельных частицах содержание СЭП может достигать 60-90%. Эти крупные включения размером до 30 мкм создают в изделиях из БС напряжения, провоцирующие разрушение, и ударная прочность снижается. Если эти включения имеют молекулярную массу существенно выше, чем ПП, то в пленках БС образуются дефекты типа "рыбий глаз". Методы борьбы с этим нежелательным явлением разнообразны. Вместо одного реактора используют каскад реакторов [1-4], это уменьшает разброс по времени пребывания частиц катализатора и обеспечивает более полное их использование. Кроме того, каскад реакторов позволяет полнее использовать пропилен и обходиться без узла дегазации 2. Однако каскад реакторов удорожает стоимость оборудования и требует обеспечения определенного перепада давления между реакторами для перетока реакционной массы, что не всегда выполнимо без установки насосов.
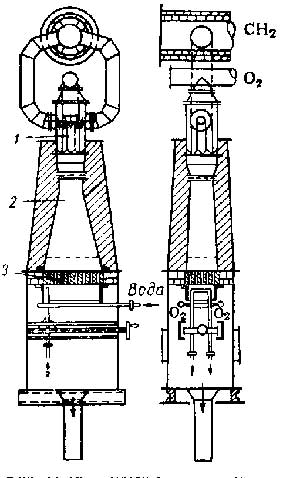
Для того чтобы не увеличивать количество реакторов и исключить попадание крупных частиц СЭП в готовый продукт, процесс ведут так, чтобы СЭП по молекулярной массе незначительно отличался от ПП. В этом случае крупные частицы СЭП при грануляции диспергируют до нужного размера. Снижение молекулярной массы СЭП осуществляется введением водорода в реакторный узел 3 [16]. Однако уменьшение молекулярной массы СЭП отрицательно сказывается на ударной прочности [17]. Оптимальной для ударной прочности БС является структура, где достаточно высокомолекулярные частицы СЭП размером 0.5 - 2 мкм диспергированы в матрице ПП [18]. Добиться этого можно путем сепарирования частиц полимера на выходе из узла 1 и возврата мелких частиц на доработку обратно в реактор. Известны способы решения этой задачи посредством введения добавок в катализатор перед реактором 3 или прямо в реактор. Вводимые агенты частично дезактивируют катализатор, причем в первую очередь его мелкие и самые активные частицы, так как они почти не покрыты слоем ПП и более доступны для дезактиватора. В результате уменьшается вероятность образования крупных включений СЭП в БС. При таком воздействии снижается и средняя активность реакционной массы, однако это может быть скомпенсировано повышением давления мономеров, увеличением времени пребывания в реакторе и т.п. С указанной целью в реактор 3 добавляют воду, спирты, фенолы, кислоты, CO, CO2, NO2, SO2, CS2, H2S [19], диэтиловый эфир этиленгликоля [20, 21], амины, кетоны, амиды кислот [22], четыреххлористый титан [23], алкоксититан [24], галогены [25]. Не все перечисленные добавки являются дезактиваторами, некоторые модифицируют каталитическую систему с целью изменения констант сополимеризации и ММР.
В патентах на способ получения БС часто указывают содержание фазы СЭП в пределах 2-50%, однако на практике оно не превышает 25% [5-14, 16-39]. Это связано с трудностями, возникающими при синтезе СЭП, который набухает в растворителях, растворяется, затрудняет теплосъем и перекачку пульпы. Если сополимеризация протекает в газовой фазе, то при содержании СЭП свыше 20% наблюдается увеличение липкости порошка, комкование, налипание на оборудование [5]. Положение усугубляется, если СЭП имеет низкую молекулярную массу, так как в этом случае увеличивается его растворимость и липкость [40]. При повышении БС необходимо регулировать не только общее содержание СЭП, но и его состав. Для достижения максимальной ударной прочности содержание пропиленовых звеньев в СЭП варьируют в пределах 20-40%, поддерживая определенное соотношение пропилен : этилен в ректорах. Большая часть пропилена поступает в узел 3 с потоком порошка ПП. Если этот поток избыточен, то часть пропилена удаляют в узле 2 в дегазационных камерах или в системе шлюзов. Если ПП получают в среде жидкого пропилена, то его излишки испаряют, подводя тепло. Для того, чтобы меньше сдувать полипропилен, сополимеризацию проводят в каскаде реакторов [1-4]. При этом в каждый реактор сополимеризации дозируют определенное количество этилена таким образом, чтобы его концентрация от реактора к реактору увеличивалась, а концентрация пропилена уменьшалась. В результате такой технологии фаза СЭП складывается из двух частей: аморфного СЭП (20-70% звеньев пропилена) и кристаллического СЭП (2-15% звеньев пропилена). Такое сочетание фаз позволяет достигнуть высокой ударной прочности с минимальными потерями жесткости и прочности при разрыве [41-58]. Лучше всего, когда доля аморфного СЭП составляет 10-20% от общего содержания СЭП [41, 43, 45-48, 51, 52]. В зависимости от способа получения БС его свойства могут изменяться. Если процесс ведут в газовой фазе без растворителя, то в полимере остаются все продукты синтеза, атактический ПП и растворимый СЭП, что приводит к снижению модуля упругости и прочности при разрыве. Если процесс проходит в среде растворителя, то часть атактического ПП и аморфного СЭП переходят в раствор и отделяются от целевого продукта, поэтому БС будет более жестким [40]. Каждый из этих вариантов имеет свои плюсы и минусы, но в настоящее время наибольшее распространение получили технологические решения фирм "Хаймонт" (Италия) и "Юнион Карбайд" (Англия). В обоих случаях СЭП получают в одном газофазном реакторе на титан-магниевом катализаторе без промывок. Синтез ПП ведут в одном реакторе в газовой фазе ("Юнион Карбайд") и в петлевом реакторе в среде жидкого пропилена ("Хаймонт"). Менее распространены процессы, в которых на каждой стадии синтеза получают СЭП с разным содержанием пропиленовых звеньев [34, 58]. Такие БС по свойствам близки к термопластам. Литература 1. Англ. патент 1530827. 2. Фр. патент 2328003. 3. Пат. США 4066718. 4. Пат. ЕПВ 0225099. 5. Пат. США 4259461. 6. Пат. США 4576994. 7. Яп. пат. 60-34963. 8. Яп. пат. 62-396603. 9. Яп. пат. 72-26113. 10. Яп. пат. 61-38928. 11. Англ. пат. 1058263. 12. Пат. США 4365045. 13. Яп. пат. 40-17988. 14. Яп. пат. 61-50086. 15. Попов В.П. и др. Пласт. массы, 1982, № 1, с. 60. 16. Пат. США 3401212. 17. Авт. свид. 732302; опубл. в Б.И., 1980, № 17, с. 413. 18. Попов В.П. и др. Высокомол. соед., 1980, т. А23, № 4, с. 750. 19. Пат. ЕПВ 0174863. 20. Пат. ЕПВ 0225099. 21. Пат. ЕПВ 0225094. 22. Яп. пат. 63-41929. 23. Яп. пат. 47-55594. 24. Пат. ЕПВ 0261962. 25. Яп. пат. 56-60227. 26. Пат. США 3937758. 27. Пат. США 4365045. 28. Пат. США 3929232. 29. Англ. пат. 1342647. 30. Англ. пат. 2157302А. 31. Англ. пат. 2152067А. 32. Фр. патент 2078327. 33. Фр. патент 2221476. 34. Яп. пат. 62-23768. 35. Яп. пат. 61-218615. 36. Яп. пат. 61-264012. 37. Яп. пат. 61-25221. 38. Яп. пат. 63-58165. 39. Попов В.П. и др. Тезисы докладов региональной конференции "Проблемы и перспективы развития производственного объединения Томский нефтехим. комб.". Томск, 1991, с. 15. 40. Пат. США 4521566. 41. Пат. США 4316966. 42. Пат. США 4128606. 43. Пат. США 3937758. 44. Англ. пат. 2132624. 45. Англ. пат. 1497822. 46. Англ. пат. 2925994. 47. Англ. пат. 1566391. 48. Яп. пат. 49-45308. 49. Яп. пат. 61-50088. 50. Яп. пат. 62-39164. 51. Яп. пат. 62-39165. 52. Яп. пат. 49-45308. 53. Фр. патент 2262054. 54. Фр. патент 2291220. 55. Пат ФРГ 2417093. 56. Пат ФРГ 2700774. 57. Англ. пат. 1328102
В.П. Попов Источник: Пластические массы
|