Сам процесс смешивания производится при помощи насосов, требует обвязки установки длинными рециркуляционными трубопроводными линиями и зачастую характеризуется неоправданным завышением качественных показателей готовой продукции и повышенными трудозатратами. В настоящем докладе приводится информация о современной смесительной технологии и оборудования. Основное внимание будет уделено вопросам соблюдения качественных спецификаций готовой продукции в соответствии с требованиями внутренних и/или зарубежных заказчиков в свете специальных условий новых ЕВРО стандартов в отношении бензинов и дизельного топлива. Предлагаемая технология в случае ее правильного использования обеспечит более рациональное использование рецептурных компонентов, повышение качества готовой продукции, сокращение использования резервуарного парка и значительную экономию в плане себестоимости выпускаемой продукции. Современные поточные смесительные установки в комбинации с поточными анализаторами и программным обеспечением для оптимизации рабочих процессов в режиме реального времени зарекомендовали себя в промышленной эксплуатации в качестве экономичных, точных и стабильных средств производства высококачественных моторных топлив с оптимальной себестоимостью. Достигаемая экономия средств и повышения рентабельности производства по сравнению с традиционной технологией смешивания компонентов в смесительных емкостях может ускорить темпы возврата капиталовложений до 60% а год и обеспечить окупаемость проекта за срок до одного года и менее. ТРАДИЦИОННАЯ СМЕСИТЕЛЬНАЯ ТЕХНОЛОГИЯ
Процесс смешивания компонентов в смесительных емкостях отдельными замесами (партиями готового продукта) требует применения большого объема ручных операций, связанных с последовательными загрузками рецептурных компонентов, и производится при помощи насосов. Кроме того, традиционные смесительные установки обвязываются длинными рециркуляционными трубопроводными линиями и зачастую характеризуются неоправданным завышением качественных показателей готовой продукции и повышенными трудозатратами. Если говорить конкретно, то при традиционной технологии каждый рецептурный компонент подается при помощи насоса из своего хранилищного резервуара в смесительную (хранилищную) емкость готового продукта через систему трубопроводов. В этом случае важно соблюдать последовательность подачи компонентов, а именно: сначала подаются наиболее тяжелые компоненты (с высоким удельным весом), а затем более легкие компоненты (с низким удельным весом). Подача в резервуар сначала тяжелых компонентов обеспечивает создание в его нижней части достаточного давления с тем, чтобы последующая подача в него легких компонентов не вызывала образования паров. Дозирование каждого подаваемого на смешение компонента выполняется при помощи расходомерных приборов, установленных на их хранилищных резервуарах. После подачи всех компонентов при помощи рециркуляцинного насоса, которым оснащается резервуар готового продукта, производится смесительный цикл. Точность такой технологии смешения зависит на точности дозирующего приборного обеспечения резервуарного парка, системы управления подающими насосами (обычно ручной режим) и времени, которое требуется для рециркуляции смеси с целью получения гомогенизированного конечного продукта. Наш опыт работы с несколькими НПЗ в Российской Федерации показывает, что именно такая технология в основном применяется сегодня на многих предприятиях. Однако исходя из требований сегодняшнего и будущего рынка сбыта готовой продукции в отношении ужесточившихся стандартов по охране окружающей среды, а также рентабельности производства, такая технология все чаще и чаще рассматривается как устаревшая, и в этой связи большинство нефтеперерабатывающих компаний в мире переводят свои производства моторных топлив на автоматизированные поточные смесительные установки. Переоснащение российских НПЗ такими установками позволит поднять их конкурентоспособность как на внутреннем, так и на международном рынках. ТИПОВАЯ СХЕМА СОВРЕМЕННОЙ СМЕСИТЕЛЬНОЙ ПОТОЧНОЙ УСТАНОВКИ
Типовая схема автоматизированной поточной смесительной установки включает в себя следующие участки: 1. Поточный смеситель; 2. Автоматические поточные анализаторы; 3. Интегрированная система управления с программным обеспечением для оптимизации рабочих процессов в режимах «вне реального времени» и «в реальном времени»; 4. Модернизация резервуарного парка. 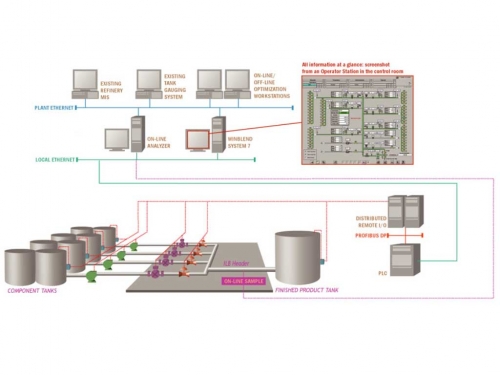 Такие поточные смесительные установки могут применяться для производства бензинов, дизельных и авиационных топлив и мазутов с использованием полностью автоматизированной системы управления, специального программного обеспечения и поточных анализаторов, обеспечивающих наибольшую экономичность производства и стабильные качественные показатели готовой продукции в соответствии с требованиями современных международных стандартов. Поточный смеситель для производства бензинов обычно имеет большее число контуров для подачи компонентов по сравнению с поточным смесителем для дизельного топлива. СОСТАВНЫЕ ЭЛЕМЕНТЫ СОВРЕМЕННОЙ СМЕСИТЕЛЬНОЙ ПОТОЧНОЙ УСТАНОВКИ В состав полностью автоматизированной смесительной поточной установки входят следующие элементы: * Поточный смеситель; * Автоматические поточные анализаторы; * Интегрированная система управления; * Средства автоматизации резервуарного парка.
ПОТОЧНЫЙ СМЕСИТЕЛЬ В поточном смесителе используется смесительный процесс, позволяющий одновременно подавать все компоненты в заданном рецептурном соотношении в общий смесительный коллектор, по которому готовый продукт подается в хранилищный резервуар. Преимуществами такой технологии являются точный контроль дозирования каждого компонента, значительное сокращение продолжительности смесительного цикла и отказ от использования смесительных емкостей для обеспечения гомогенизации готового продукта. В ходе процесса смешения в поточном смесителе расход каждого компонента постоянно регулируется с целью обеспечения на выходе из смесительного коллектора готового продукта со стабильными качественными показателями согласно заданной рецептуре. Получаемый с поточного смесителя готовый продукт имеет гомогенизированную структуру и компонентный состав в точном соответствии заданной рецептуре. 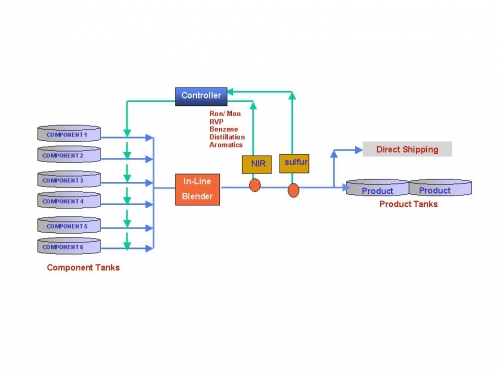
Рисунок 1. Поточный смеситель бензинов. 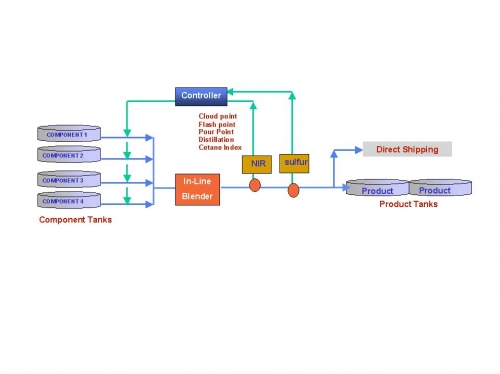
Рис. 2. Поточный смеситель дизельного топлива АНАЛИЗАТОРЫ
Автоматические поточные анализаторы позволяют в постоянном режиме периодически отбирать и проводить анализ проб из смесительного коллектора, в котором готовится бензин, дизельное или любое иное топливо. Результате таких анализов программное обеспечение системы анализаторов заносит в файл «истории замеса», регистрируя в нем фактические свойства рецептурных компонентов, подаваемых в смеситель на протяжении всего цикла замеса. Кроме того, через обратную связь данные о результатах анализов отобранных проб постоянно поступают с анализаторов в интегрированную систему управления смесительной установкой. Поточные анализаторы в комбинации с оптимизационным программным обеспечением позволяют контролировать и регулировать в режиме реального времени качественные показатели готового продукта на выходе из смесительной установки. Может также, в случае необходимости, автоматически проводиться небольшая коррекция рабочих рецептур на основании сравнения получаемых с поточных анализаторов данных с заложенными в программу задачами оптимизационных моделей. На поточных смесительных установках могут устанавливаться два типа анализторов: NIR – анализатор около-инфракрасного спектра и MRA – магнитно-резонансный анализатор. Принцип действия этих типов анализаторов имеет фундаментальные различия, но оба из них успешно эксплуатируются на многих промышленных установках. В обеих случаях результаты проведенных анализов обрабатываются в сравнении с математическими моделями, заложенными для каждого типа готового продукта в программное обеспечение, и передаются в систему управления. 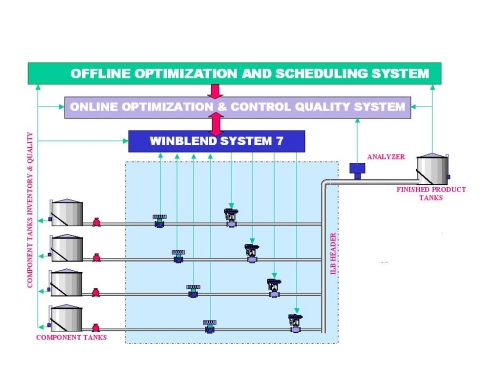 Рисунок 3. Интегрированная система управления и оптимизации.
ИНТЕГРИРОВАННАЯ СИСТЕМА УПРАВЛЕНИЯ И ОПТИМИЗАЦИИ
Интегрированная система управления включает в себя систему управления смесительным циклом (WINBLEND® System Seven) и систему оптимизации технологического процесса. Система управления (WINBLEND® System Seven) представляет из себя распределенную систему управления смесительным процессом, используя закладываемые в нее рецептуры готовых продуктов для регулирования потоков подаваемых в смеситель компонентов. В комбинации с оптимизационным программным обеспечением система управления производит в режиме реального времени необходимые корректировки рецептурной смеси компонентов с целью обеспечения заданных параметров качества готового продукта на выходе из смесителя. Система оптимизации технологического процесса включает в себя программное обеспечение для работы в режимах «вне реального времени» и «в реальном времени». Оптимизация в режиме «вне реального времени» дает плановикам НПЗ возможность заранее разработать наиболее оптимальные в отношении себестоимости рецептуры на базе имеющихся в их распоряжении компонентов с тем, чтобы в полном масштабе использовать их подачу с технологических установок. Система оптимизации в режиме «реального времени» обрабатывает данные от поточных анализаторов с целью определения, насколько готовый продукт соответствует заданным качественным показателям. Если она определяет необходимость введения корректировок, то через интерфейс с системой управления она регулирует расход подачи компонентов таким образом, чтобы вернуть качественные показатели готового продукта в заданный рецептурой диапазон. Такой режим постоянного анализа, обратной связи и автоматических корректировок продолжается в течение всего рабочего цикла смесительной установки и позволяет гарантировать стабильное соответствие готовой продукции заданным спецификациям качества.
МОДЕРНИЗАЦИЯ РЕЗЕРВУАРНОГО ПАРКА До сих пор многие нефтеперерабатывающие предприятия используют систему управления своими резервуарными парками в ручном режиме. В случае приобретения современной поточной смесительной установки желательна автоматизация всех функций управления резервуарным парком для того, чтобы полностью реализовать весь технологический потенциал такой установки и получить максимальную отдачу за счет экономии на оплате труда, которую позволяет ее эксплуатация в автоматическом режиме. Модернизация резервуарного парка в таком случае обычно сводится к приобретению новых насосов и клапанной арматуры с автоматическими приводами и реконструкции трубопроводного хозяйства с целью обеспечения стабильно надежной подачи рецептурных компонентов в коллекторы смесительной установки, а также к автоматизации приборного обеспечения резервуарного парка для выдачи в форме сигналов необходимой информации в систему управления смесительной установкой о каждом рецептурном компоненте, а именно: его плотности, уровне и объеме в хранилищном резервуаре. Автоматизированная система управления резервуарным парком через интерфейс с центральной информационной системой НПЗ обычно имеет также доступ к данным о материальном балансе и качестве компонентов.
ОЖИДАЕМЫЙ РОСТ ЭКОНОМИЧЕСКИХ ПОКАЗАТЕЛЕЙ По нашему опыту применение только одной автоматизированной поточной смесительной установки для производства бензинов за счет экономии может принести НПЗ 3-5 миллионов долларов США в год при годовых объемах выпуска бензинов в одни миллион тонн. Ниже приводятся наиболее характерные преимущества предлагаемой нами технологии.
СОКРАЩЕНИЕ ОБЪЕМОВ ИНВЕНТАРИЗАЦИИ Значительное сокращение продолжительности смесительного цикла и стабильный выход готовой продукции (отсутствие необходимости в повторных замесах) позволяет говорить о возможности сокращения объемов инвентаризации материального баланса. В частности, время хранения компонентов и готовых продуктов уменьшается на 25%. По нашему опыту экономия средств только в результате сокращения затрат на инвентаризацию может составить 500 тысяч долларов в год.
СНИЖЕНИЕ СТЕПЕНИ ЭКСПЛУАТАЦИИ РЕЗЕРВУАРНОГО ПАРКА Предлагаемая технология обеспечивает снижение степени эксплуатации резервуарного парка в силу сокращения потребности в резервуарных емкостях за счет ускорения технологического процесса. Если при традиционной схеме смешения продуктов партиями продолжительность изготовления одного замеса в среднем составляет более 40 часов, то такое же количество готового бензина может быть изготовлено на поточной смесительной установке не более, чем за 14 часов. Кроме того, благодаря проведению анализов продукта в потоке отпадает необходимость длительных ожиданий результатов лабораторных анализов для сертификации качества готового продукта либо дополнительных смесительных операций для приведения его качественных показателей в соответствие с требованиями стандарта. Все это может обеспечить экономию средств порядка 1-2 миллионов долларов за счет отказа от строительства новых хранилищных резервуаров. ОТКАЗ ОТ ПРАКТИКИ ЗАВЫШЕНИЯ КАЧЕСТВЕННЫХ ПОКАЗАТЕЛЕЙ ГОТОВОЙ ПРОДУКЦИИ Высокая точность результатов анализов, получаемых с поточных анализаторов, в комбинации с оптимизационным программным обеспечением позволяет добиться снижения себестоимости готовой продукции без риска нарушения заданных качественных показателей и в то же время отказаться от практики завышения на всякий случай таких ее параметров, как октановое число и упругость паров по Рейду. В зависимости от объемов производства достигаемая за счет этого экономия по нашему опыту может составить 1-2 миллиона долларов в год. Приводимые ниже графики иллюстрируют этот вывод. 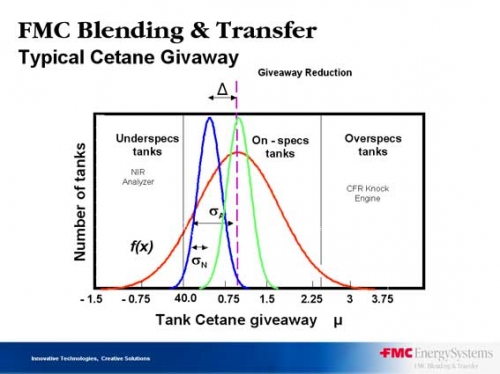
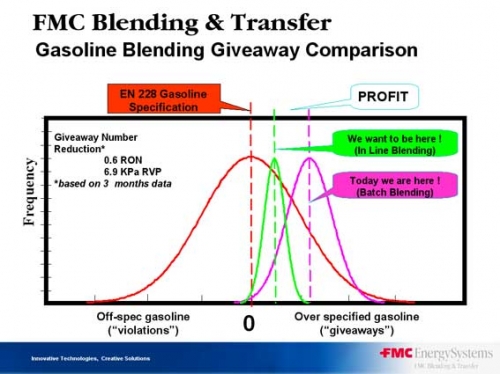
ПОВЫШЕНИЕ РЕНТАБЕЛЬНОСТИ ПРОИЗВОДСТВА ОПТИМАЛЬНОЕ ИСПОЛЬЗОВАНИЕ КОМПОНЕНТОВ
Система оптимизации производства в режиме «вне реального времени» позволяет добиться оптимального использования имеющихся на НПЗ компонентов, повысив долю компонентов с низкой себестоимостью в рецептурных формулах смесительных процессов, а также сбалансировать инвентаризацию исходных материалов и их расход для широкого диапазона смесительных операций. Характерная экономия в этом плане по нашему опыту может составить 0,04–0,18 долларов на баррель произведенного бензина.
СОКРАЩЕНИЕ ТРУДОЗАТРАТ И ОБСЛУЖИВАЮЩЕГО ПЕРСОНАЛА Использование поточных смесительных установок с встроенными анализаторами и системой автоматизации позволяет сократить продолжительность замесов и количество необходимого персонала, занятого в смесительном цикле и в выполнении лабораторных анализов. Автоматизация управления резервуарным парком позволит отказаться от большого числа операторов, необходимых для управления клапанной арматурой и насосами в ручном режиме. За счет этого ожидаемая экономия может принести НПЗ еще 500 тысяч долларов. ДРУГИЕ ПРЕИМУЩЕСТВА • Увеличение производительности; • Эффективное и оптимальное использование оборудования; • Автоматизация смесительных процессов; • Сведение к минимуму влияния изменений в процессах переработки сырья на технологических установках НПЗ на качество готовой продукции, получаемой со смесительных установок; • Сертификация готовой продукции в процессе смесительного цикла; • Сведение к минимума простоев транспорта при отгрузке готовой продукции; • Контроль за уровнем продуктов в резервуарах позволяет использовать их емкости в максимальной степени; • Улучшение планирования смесительных операций; • Сокращение ручного труда, повышение квалификации и интереса к работе операторов. ИНФОРМАЦИЯ О КОМПАНИИ FMC Blending & Transfer имеет более чем 40-летний опыт в области проектирования, изготовления и ввода в эксплуатацию смесительных установок с полной автоматизацией технологических процессов. Штаб квартира FMC Blending & Transfer находится в г. Чикаго, США. Основными нашими заказчиками являются компании, занимающиеся производство бензинов, дизельных, авиационных, судовых и печных топлив. Наша компания является также признанным лидером на мировом рынке в поставке комплектного оборудования для изготовителей моторных и смазочных масел. Выступая в качестве исполнителя интегрированных проектов, FMC Blending & Transfer предлагаем своим клиентам апробированные технические решения для стоящих перед ними задачами. Огромный опыт и установившиеся партнерские отношения с поставщиками ключевых компонентов современных технологических линий позволяет нашей компании создавать для своих заказчиков уникальные и оптимальные производственные системы.
А. Джозефсон, «FMC Blending & Transfer», Чикаго, США Источник: ГСМ
C текущей ситуацией и прогнозом развития российского рынка горюче-смазочных материалов можно познакомиться в отчетах Академии Конъюнктуры Промышленных Рынков: «Рынок автомобильных бензинов в России»«Рынок нефтяных битумов в России».«Рынок дизельных топлив в России» «Рынок смазочных масел в России». |