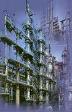
Весь цикл от начала строительства до пуска завода в эксплуатацию занял всего лишь 17 месяцев. Технология BAYQIK ® (квази-изотермический катализ), разработанная компанией Bayer Technology Services GmbH, позволяет увеличить допустимую концентрацию серной кислоты на входе на 50% по объему. В совокупности с оптимизацией процедур управления технологическим процессом, внедрение нового, инновационного метода позволяет существенно улучшить результаты конверсии, т.е. значительно снизить уровень эмиссии диоксида серы. Кроме того, с применением данной технологии производительность завода увеличивается, по меньшей мере, на 30%. Компания Berzelius провела технологические испытания и оптимизацию данного процесса под свое производство в ходе реализации пилотного проекта непосредственно на одном из своих заводов. Надежность, высокое качество и низкая стоимость стали решающими факторами для принятия руководством компании решения о присуждении контракта на планирование, поставку и строительство завода по производству серной кислоты по технологии BAYQIK® концерну Bayer. Новый завод способен производить до 450 тонн серной кислоты в день. Кроме того, благодаря тому, что BAYQIK ® применяется на периферийной основе, переход существующих мощностей компании по производству серной кислоты на новые технологии занял всего лишь несколько дней. Краткое описание современных промышленных способов получения серной кислоты Производство серной кислоты из серусодержащего сырья включает несколько химических процессов, в которых происходит изменение степени окисления сырья и промежуточных продуктов. Это может быть представлено в виде следующей схемы: где I - стадия получения печного газа (оксида серы (IV)), II - стадия каталитического окисления оксида серы (IV) до оксида серы (VI) и абсорбции его (переработка в серную кислоту). В реальном производстве к этим химическим процессам добавляются процессы подготовки сырья, очистки печного газа и другие механические и физико-химические операции. В общем случае производство серной кислоты может быть выражено в следующем виде: Сырье подготовка сырья сжигание (обжиг) сырья очистка печного газа контактирование абсорбция контактированного газа СЕРНАЯ КИСЛОТА Конкретная технологическая схема производства зависит от вида сырья, особенностей каталитического окисления оксида серы (IV), наличия или отсутствия стадии абсорбции оксида серы (VI). В зависимости от того, как осуществляется процесс окисления SО2 в SО3, различают два основных метода получения серной кислоты. В контактном методе получения серной кислоты процесс окисления SО2 в SО3 проводят на твердых катализаторах. Триоксид серы переводят в серную кислоту на последней стадии процесса - абсорбции триоксида серы, которую упрощенно можно представить уравнением реакции: SО3 + Н2О Н2SО4 При проведении процесса по нитрозному (башенному) методу в качестве переносчика кислорода используют оксиды азота. Окисление диоксида серы осуществляется в жидкой фазе и конечным продуктом является серная кислота: SО3 + N2О3 + Н2О Н2SО4 + 2NО В настоящее время в промышленности в основном применяют контактный метод получения серной кислоты, позволяющий использовать аппараты с большей интенсивностью. Рассмотрим процесс получения серной кислоты контактным методом из двух видов сырья: серного (железного) колчедана и серы. 1) Химическая схема получения серной кислоты из колчедана включает три последовательные стадии: - окисление дисульфида железа пиритного концентрата кислородом воздуха: 4FеS2 + 11О2 = 2Fе2S3 + 8SО2, - каталитическое окисление оксида серы (IV) избытком кислорода печного газа: 2SО2 + О2 2SО3 - абсорбция оксида серы (VI) с образованием серной кислоты: SО3 + Н2О Н2SО4 По технологическому оформлению производство серной кислоты из железного колчедана является наиболее сложным и состоит из нескольких последовательно проводимых стадий. Обжиг колчедана в токе воздуха представляет собой необратимый некаталитический гетерогенный процесс, протекающий с выделением тепла через стадии термической диссоциации дисульфида железа: FеS2 = 2FеS + S2 и окисления продуктов диссоциации: S2 + 2О2 = 2SО2 4FеS + 7О2 = 2Fе2S3 + 4SО2 что описывается общим уравнением 4FеS2 + 11О2 = 2Fе2S3 + 8SО2, где ?Н = 3400 кДж. Увеличение движущей силы процесса обжига достигается флотацией колчедана, повышающей содержание дисульфида железа в сырье, обогащением воздуха кислородом и применением избытка воздуха при обжиге до 30 % сверх стехиометрического количества. На практике обжиг ведут при температуре не выше 1000 оС, так как за этим пределом начинается спекание частиц обжигаемого сырья, что приводит к уменьшению поверхности их и затрудняет омывание частиц потоком воздуха. В качестве реакторов для обжига колчедана могут применяться печи различной конструкции: механические, пылевидного обжига, кипящего слоя (КС). Печи кипящего слоя отличаются высокой интенсивностью (до 10 000 кг/м2•сут), обеспечивают более полное выгорание дисульфида железа (содержание серы в огарке не превышает 0,005 мас. долей) и контроль температуры, облегчают процесс утилизации теплоты реакции обжига. К недостаткам печей КС следует отнести повышенное содержание пыли в газе обжига, что затрудняет его очистку. В настоящее время печи КС полностью вытеснили печи в других типов в производстве серной кислоты из колчедана. |