2.3 Описание топлива Качество топлива является критичным в производстве цемента. Топливо — не только источник энергии, необходимый для нагрева материала до температуры спекания, обычно 1350 °C, но и источник сырьевого материала, поскольку топливо в реальном процессе смешивается с сырьевым материалом. Поэтому химический состав золы также важен. Для каждого вида топлива в модель вводится новым компонент. Один топливный компонент описывается химической формулой, рассчитанной путем химического анализа, а его молекулярная масса принимается за 1000 г сухого вещества на моль. Энтальпия образования каждого топлива затем рассчитывается как энтальпия продуктов минус энтальпия реагентов. Энтальпия реагентов аппроксимируется с калориметрической теплотворностью сухого образца топлива. 2.4 Встречный процесс Процесс производства цемента основан на встречном движении газа и потока твердого вещества. Сырьевой материал загружается в начале системы и в конце на выходе получается клинкер. Газ проноситься через всю систему, начиная от угольной мельницы и клинкерного холодильника до вентиляторов отработанного газа в направлении противоположном потоку сырьевой муки. В реальном процессе в газовой фазе еще присутствует пыль, которая движется тоже в направлении, противоположном сырьевому материалу. Циркуляция пыли и образование аэрозолей не учитываются в модели. Калийные, натриевые, сульфатные хлоридные испарения циркулируют в системе, путешествуя вместе с газом от горячей зоны, где они испаряются, к холодным зонам, где они вновь конденсируются и превращаются в жидкости. Циркуляция испарений происходит совместно с потоком сырьевой муки. Моделирование процесса теплопереноса в данной модели решено через энергообмен между газом и материалом и через потери энергии в окружающую среду. Тепловую энергию поставляют нагретый газ, подаваемый в систему из теплообменника, горение топлива и экзотермические химические реакции. 2.5 Расчет равновесия. Для нахождения химического равновесия были произведены расчеты. Химическим равновесием называется состояние, когда концентрации реагентов и продуктов не подвергаются нетто-изменениям в течение продолжительного времени. В некоторых реакциях состояние равновесия достигается очень быстро, в некоторых медленно, а в ряде реакций этого состояния достичь невозможно. В исследовании этот аспект не учитывался, т. е. в модель не вводились переменные, зависимые от времени. Существует возможность создать неравновесные части модели, однако это требует знаний соответствующих процессов, которых мы пока не имеем. При расчетах модели сделано допущение, что в процессе происходит идеальное смешивание всех газов, твердых материалов и жидкостей. 3 Проверка модели Для обоснования модели результаты моделирования сравниваются с параметрами стандартного реального процесса. Параметры процесса либо замеряются, либо рассчитываются стандартными методами. Кроме того, результаты моделирования сравниваются с данными из литературы. Массовый выход (т/ч) произведенного клинкера и пыли, удержанной рукавными фильтрами, а также расход газа в одной нитке после верхних циклонов, показан на рис. 4. Согласно модели производится больше клинкерной пыли, по сравнению с реальным процессом, благодаря тому, что в модели приняты идеальные условия процесса. Реально измеренное в процессе количество газа в верхних циклонах превышает показатель в моделированном процессе. Это свидетельствует о недостаточном учете подсоса воздуха в модели. Рис. 5 иллюстрирует сравнение измеренных и моделированных показателей температуры в циклонной башне и в обжиговой печи. В реальном процессе температура на входе печи, в зоне кальцинации и в зоне горения не отслеживается. В процессе управления температура в зоне горения устанавливается равной 1450 °C. 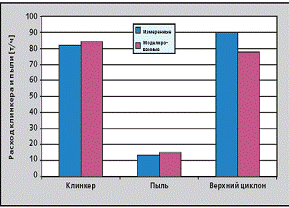
4 Измеренные и моделированные показатели расхода газа и материалов 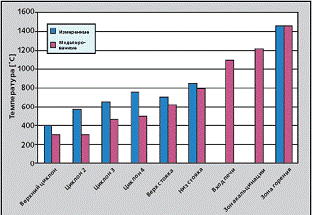
5 Измеренные и моделированные параметры температуры процесса 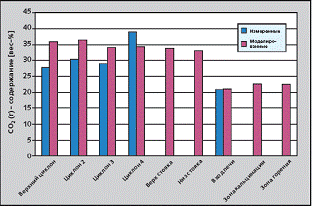
6 Измеренные и моделированныее параметры содержания C02 в газовых потоках процесса 
7 Измеренные и моделированные параметры содержания О2 в газовых потоках процесса 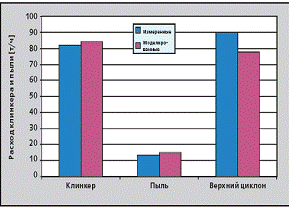
|