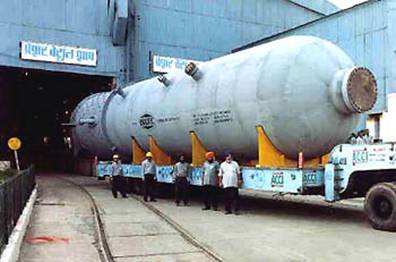
Чтобы ни происходило на финансовых рынках, промышленность должна работать и производить необходимую для народного хозяйства продукцию. Пусть обороты будут меньше, чем в стабильный период, но все же они должны быть. Иначе коллапса экономики не избежать. Отрадно, что петербургские производители, несмотря на все сложности текущего момента, берутся за новые проекты, требующие конструкторской и технической смекалки. 
Итак, на «Ижорских заводах» построили необычный агрегат – огромный цилиндрический сосуд длиной 30 метров, наружным диаметром более 6 метров и весом 800 тонн. В сентябре 2009 агрегат отправился в город Кстово Нижегородской области на тамошний нефтеперерабатывающий завод. С его помощью будут производить высококачественное дизельное топливо по стандарту «Евро-5». Подобные габариты осваиваются российским предприятием впервые после длительного перерыва. В середине 1990-х годов ижорцы уже изготавливали крупное и тяжеловесное изделие – реактор гидрокрекинга для «ЛУКОЙЛ-Пермнефтеоргсинтеза». Но кстовский сосуд все-таки превзошел пермский по наружному диаметру. Для того чтобы произвести на свет подобное чудо, его сначала собрали виртуально на компьютере – с использованием специального программного обеспечения. Важно еще одно отличие нового реактора от предыдущих аналогичных изделий – его корпус изготовлен не из кованых деталей (так называемых обечаек), а из листового проката. Металлургические заготовки были отлиты специалистами «ОМЗ-Спецсталь», они же осуществили прокат 5 тыс. листов. Здесь также было использовано новаторство – применена хромомолибденованадиевая сталь (эта марка была создана еще в 1960-е годы ленинградскими металлургами в содружестве с ЦНИИ конструкционных материалов «Прометей» и использовалась для корпусов атомных реакторов и ядерных установок подводных лодок). Особенность работы с этой сверхпрочной сталью состоит в том, что сварку ее надо вести «нагоряче», разогревая заготовки до 250 – 300 градусов и строго соблюдая режим термической обработки. Для изготовления реактора пришла помощь и из-за рубежа. К примеру, листы для днища реактора были отштампованы в Германии. Каждое днище состоит из восьми «лепестков» и «шапочки», их сварка производилась на новой установке фирмы Siemens. Конструкторы утверждают, что прежде в России никто не сваривал полусферы подобного диаметра из листа такой толщины. Особую сложность представляла и термическая обработка кольцевого шва. Дело в том, что на ижорской промышленной площадке нет печей, в которые могло бы поместиться такое огромное изделие, самая крупная шахтная печь имеет глубину 26 метров. Спасла технология МТО – местная термическая обработка: с помощью двух систем электронагревателей, наружной и внутренней, по особому режиму прогревали каждый сварной шов. По ходу дела пришлось решать множество технических вопросов. Последний из них возник уже при выходе реактора из цеха. Выезжал он, погруженный на специальный итальянский транспортер, снабженный более 200 колесами, управляемыми дистанционным пультом. И вот неожиданно оказалось, что на пути стоит железный столб – опора заводской электролинии. Для собравшихся на торжественное событие журналистов так и осталось непонятным, почему препятствие нельзя было обнаружить и удалить заранее, но они с любопытством наблюдали сам технологический процесс устранения. Сначала фундамент опоры был освобожден от излишнего количества земли. Затем сварочным аппаратом специалисты отрезали столб от основания и повалили. Именно в этот момент и выяснилось, что внутри него находится электропроводка. Но, к счастью, она не была под напряжением. После этого место, на котором находился злополучный столб, было утрамбовано с помощью больших металлических плит. Специальным механизмом подняли свисающие провода осветительной линии. И лишь после этого гигантская «гусеница на колесах» наконец-то двинулась в путь к причалу на реке Ижоре. Остается надеяться, что на пути следования подобного рода непредвиденных препятствий больше не окажется По материалам www.spbvedomosti.ru |