Локальный перегрев Термодинамические и кинетические характеристики процесса парового риформинга, в котором метан реагирует с паром на катализаторе для получения угарного газа и водорода, таковы, что для его проведения требуется большое количество энергии в виде высокой температуры, и поэтому риформинг чаще проводится в трубной печи, чем в реакторе с неподвижным слоем (катализатора). Необходимость работы при высокой температуре усугубляется высоким давлением, которое повышает теплоперенос, но нарушает равновесие реакции. В то же время, чем выше давление в трубах, тем больше механическое напряжение в них, а это может критически повлиять на предельные рабочие температуры материала труб. В результате большинство паровых печей для риформинга работает при таких температурах, что средняя продолжительность службы труб составляет 100 тыс. часов (12 или больше лет). Но если температура части трубы на некоторое время окажется выше нормальной рабочей температуры всего на несколько градусов, то можно с уверенностью сказать, что этот участок трубы разрушится намного раньше. Независимо от конструкции печи и точности контроля температуры, локальный перегрев может быть результатом действия незначительных факторов, которые нарушают нормальную передачу тепла через стенки трубы. К таким факторам относятся: неравномерная плотность набивки катализатора, частичная дезактивизация катализатора соединениями серы или отложениями углерода. Действие этих факторов нельзя компенсировать добавлением режимов обжига, поэтому очень важно не допускать возникновения первичных условий, при которых появляются эти нарушения. Рабочие характеристики катализатора и метод его загрузки в трубы очень важны не только для эффективности процесса, но и для обеспечения долговечности труб. Резкие изменения рабочих условий, такие как аварийное выключение или быстрый запуск также могут иметь разрушительные последствия, не только из-за их влияния на трубы, но и потому, что они могут повредить огнеупорную облицовку печи. Катастрофическое повреждение труб Поскольку грань между нормальными рабочими условиями и состоянием неисправности очень тонка, то потеря контроля может привести к разрушениям за считанные минуты. Подобный случай произошел на аммиачном заводе Terra Industries (Канада) в апреле 2001 г. во время запуска, после временной остановки из-за неполадок с электричеством. Во время пуска в печь начали постепенно подавать технологический газ, но печь стало невозможно контролировать, и через 30 минут она снова выключилась. При этом температура технологического газа на выходе из печи достигла 927°C, а внутри превышала 1000°C. Вследствие этого 11 из 168 труб распались на две или более части, 129 – треснули или раскололись вдоль аустенитовых границ, что случается при температурах свыше 1200°C. Расчетное температурное ограничение для данных труб равнялось 880°C. Экспертиза записей рабочих условий показала, что температура в туннеле технологического газа понизилась в течение 25 минут после нового введения пара (до введения технологического газа), возможно, что некоторые трубы уже были треснуты в некоторых местах. При возобновлении потока технологического газа, может произойти воспламенение просочившегося газа. Но остается неясным, был ли перегрев, вызван воспламенением в разрушенных трубах, которое затем перекинулось на соседние трубы, или нехваткой пара/газа в разрушенных трубах. После этого инцидента, из-за которого завод был в простое 59 дней, были добавлены два дополнительных переключателя. Один на выходе газа из, а другой на входе в подогреватель сырья, кроме того, было встроено оборудование для визуального контроля во время пуска. Другая авария с разрушением труб произошла в январе2005 г. на заводе по производству водорода Syncrude Canada's (провинция Альберта, Канада). В печи риформинга шесть труб вышли из строя, они расширились и накренились. Печь была остановлена для удаления этих труб до того, как они повредят смежные трубы и каналы топочного газа. Так как остановка произошла в середине зимы, паровая система была под давлением. Во время последующего поспешного запуска в том месте, где пар был снова введен в систему, давление стало сверхвысоким и пять труб взорвались с такой силой, что их фрагменты пробили крышу. Еще 41 труба была разрушена взрывной волной. Стенки топки были местами расплавлены. Ущерб был такой, что все трубы печи надо было полностью заменить. Причиной взрыва считалось попадание воды в горячие трубы печи. Было подсчитано, что испарения всего лишь 0,4 л воды достаточно для разрушения пяти труб, а этот риск не был адекватно оценен. Источником воды послужило устройство для предварительного нагрева смешанного сырья в секции конвекции, которое не было оборудовано осушителем. Это не было известно во время ремонта. В свете этого опыта процедура пуска была дополнена более длительным периодом предварительного нагрева, повышенным контролем уровня влажности и системой отключения; а инженерный персонал был дополнительно проинструктирован. Производство труб Трубы установки риформинга нельзя обработать под давлением как обычные стальные трубы, использующиеся в химической промышленности, так как жаропрочные сплавы, необходимые при работе в жестких условиях, недостаточно пластичны для обработки по такой методике. Вместо этого они изготовлены методом центробежного литья, при котором определенное количество расплавленной примеси наносится на вращающуюся форму на большой скорости. Компании Kubota Metal Corporation и Saskferco Products Inc. подготовили совместный отчет о производстве труб для печей риформинга и специальных условиях, требующих пристального внимания и контроля, некоторые из этих условий являются личным опытом операторов печи риформинга. Равномерность состава труб – самый важный фактор, а метод центробежного литья позволяет его повысить. Например, при обычном литье труб самый плотный материал (непосредственно метал) находится на наружной стороне трубы, а более легкие частицы, такие как остатки шлака и захваченный газ мигрируют на внутреннюю поверхность. Из-за этой тенденции внутренняя поверхность получается пористой и неоднородной, что способствует их деформации, и поэтому в настоящее время такие трубы рассверливают, чтобы удалить эти примеси. С другой стороны, неровность наружной поверхности трубы способствует поглощению и передачи теплоты. Жаропрочные сплавы на основе никеля и хрома обычно содержат 25%Cr, 35% Ni, 0,4-0,6% углерода и следовые количества легирующих добавок. Обычными аналитическими методами контроля состава сплавов являются рентгено-флуоресцентная и эмиссионная спектроскопия. Момент добавления легирующих добавок, обычно титана, циркония и ниобия, очень важен. Чтобы уменьшить окисление, которое снижает их эффективность, нужно ввести эти добавки как можно ближе к моменту разливки, но при этом необходимо добиться равномерного распределения во всем расплаве. Хотя толщина труб, изготовленных методом центробежного литья, равномерна, они имеют тенденцию изгибаться при охлаждении до комнатной температуры, поэтому, при применении любого метода рассверливания трубы, разница в толщине на 15 метровом отрезке может достичь 5 мм. Это может стать причиной преждевременного разрушения труб, как случилось на заводе Saskferco в 1999 г., когда труба разрушилась после семи лет работы. В том месте, где произошел разрыв трубы, толщина стенки варьировалась от 10,9 до 13,6 мм. После этого случая на заводе Saskferco внесли изменение в технические условия применения таких труб, теперь разница в толщине не должна превышать 10% при 0°C, 90°C, 180°C и 270°C. Всего этого можно избежать при использовании метода тягового сверления, при котором направляющая втулка находится перед головкой фрезы и таким образом получается линия соответствующая внутренней поверхности до обработки. А при обычном методе сверления под давлением направляющая втулка следует за линией уже обработанной поверхности (рис. 1), которая не соответствует сгибу трубы, поэтому некоторые части получаются более тонкими, а некоторые толстыми. Специалисты Saskferco считают, что трубы разрушаются в тех местах, где есть наибольшие перепады в толщинах стенок, так как происходит неравномерное распределение тепла. 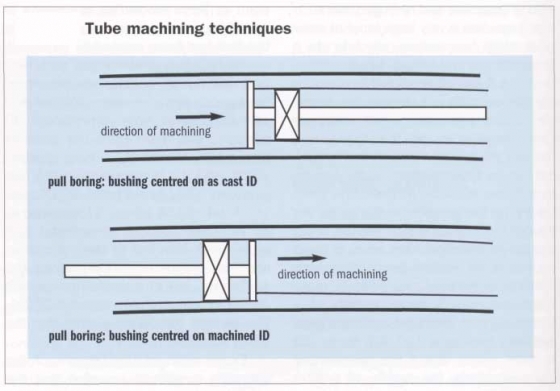
Рис. 1. Методы обработки внутренних поверхностей труб печей рифогрминга.
В общем, при сварке труб важно добиться однородного распределения легирующих добавок. Сварные швы следует тщательно проверять рентгеновскими методами. Перед запуском печи следует проверить все сварные швы и провести гидравлическое и пневматическое испытание труб. Особые проблемы могут возникнуть со сварными швами между разнородными материалами, например, если трубу из легированного сплава приваривают к детали из углеродистой стали. Авария на заводе Saskferco является ярким примером преждевременного разрушения целого ряда разнородных сварных швов в установке, которая эксплуатировалась в суровых зимних условиях, и в это время сварные швы были незащищены от кислотного конденсата. О причинах подобных разрушений шла речь на симпозиуме по безопасности на аммиачных производствах AlChE (Safety in Ammonia Plants and Related Facilities symposium). Трещины возникают в местах образования тонкой прослойки мартенсита, который формируется во время сварки. Этого можно избежать, если предварительно подогревать свариваемую зону до 150°C, однако такие рекомендации не были учтены при монтаже печи. Катализаторы Продолжительность службы труб также во многом зависит от структуры и химического состава катализатора процесса риформинга. Если реакция риформинга не будет идти с ожидаемой скоростью на некотором участке трубы, то есть не будет вовремя расходоваться подводимое тепло, то возникнет локальный перегрев. Структура - это верное слово, потому что от формы и размера частиц носителя, а также от распределения активных центров (атомов никеля) зависят свойства катализатора: активность, характеристики теплопередачи, устойчивость к перепадам давления и к закоксовыванию. Усовершенствование катализатора может принести значительное повышение мощности печи для риформинга без дорогостоящих модификаций самой печи. Компания Sud-Chemie, Inc. представляет серию катализаторов процесса риформинга Reformax. Глинозем (алюминат кальция), использованный в качестве материала носителя в катализаторе Reformax 330 имеет наибольшее количество активных центров на поверхности, благодаря большему объему пор является более прочным по сравнению с обычно применяемым в качестве носителя оксидом алюминия. К тому же глинозем менее кислый, чем оксида алюминия, поэтому в меньшей степени способствует прохождению побочных реакций крекинга, повышая экономическую эффективность процесса риформинга. Отложения углерода на катализаторе не только снижают активность катализатора, но также препятствует прохождению потоков газа, оба эти фактора повышают риск перегрева труб. Уже давно известно, что щелочные металлы, особенно калий, хорошо использовать в качестве активаторов каталитической реакции. Введение этих элементов в состав катализатора позволяет сдерживать реакции образования углерода. Но вследствие большой летучести этих металлов эффективность их воздействия падает со временем. Sud-Chemie уменьшил эту тенденцию путем введения связанного калия в материал-основу своего катализатора Reformax 210 в виде смешанного алюмината кальция и калия (CaK2Al22O34). Также были исследованы катализаторы с нещелочными активаторами, такими как титан, цирконий, иттрий и ниобий, которые способны окислить углерод, осевший на катализаторе. Такие элементы обладают превосходными характеристиками по отношению к процессам риформинга. Один экземпляр (Reformax 340) будет в скором времени протестирован на заводе. Наряду с этими новинками Sud-Chemie представила новый тип катализаторов, устойчивых к большим перепадам давления и имеющих лучшие характеристики поверхности. По сравнению с простыми катализаторами, их применение позволит повысить пропускную способность печи на 22%. На рынке катализаторов в настоящее время существует множество разработок конкурентоспособных сложных каталитических систем, но их производительность ниже. Даже самый лучший катализатор процесса риформинга не будет работать, если он загрязнен каталитическими «ядами», особенно серой. Компания Kaltim (Индонезия) делится своим опытом по регенерации отравленного серой катализатора. Во время изменения состава поступающего природного газа серу не удалось полностью уловить на установке десульфирования, и катализатор процесса риформинга был отравлен. Это привело к отложению углерода, повышению перепада давления и температуры стенок труб. Для регенерации катализатора во время остановки печи были предприняты следующие меры: поддержание температуры стенок труб на уровне 700°C, пропускание потока газа содержащего небольшое количество воздуха, доля которого постепенно увеличивалась, но не превышала того предела, когда температура могла бы стать выше 700°C. В начале процедуры количество кислорода в смеси составляло 0,1-0,2% от всего объема; с течением времени оно выросло до 2,5-2,7%. Под воздействием этого пара основная часть сульфида никеля превратилась в сероводород и оксид никеля, в то время как осевший на катализаторе углерод превратился в оксид углерода, а остальные следы сульфида превратились в диоксид серы. При запуске реактора через катализатор сначала был пропущен пар обогащенный водородом (гидроочистка), после чего нормальные рабочие условия восстановились, а на трубах не образовались зоны локального перегрева. Огнеупорные материалы Топка простой печи риформинга обложена огнеупорным материалом для защиты стальной конструкции от экстремальных условий во время функционирования. Компания Karrena GmbH (Германия) исследует различные типы, огнеупорных материалов применяемых на заводах в процессе риформинга, методы их проверки и ремонта. Стены печи облицовывают либо теплоизоляционными кирпичами, либо блоками из керамического волокна. Верхнюю часть топки обычно покрывают волокном. Особое внимание следует уделить расширению и сужению материалов во время запуска и остановки процесса, которое происходит вследствие огромного перепада температур. Температурные швы шире 10 мм заполняют керамическим волокном, швы меньшей ширины оставляют незаполненными, так как они сами смыкаются при нагревании печи. Любой облицовочный материал вследствие низкой эластичности и небольшой теплопроводности очень чувствителен к резким перепадам температуры, и может разрушиться при слишком быстром охлаждении или нагревании во время остановки или запуска. Огнеупорная облицовка некоторых деталей установки риформинга, подвергается нагреванию под большим давлением технологическим газом, содержащим водород. Для предотвращения проникновения водорода к металлическим стенкам, что может стать причиной хрупкости, применяют огнеупорные материалы с плотной непористой поверхностью. Также как и температуру, давление следует повышать и сбрасывать медленно, чтобы не повредить огнеупорное покрытие. Свежеуложенное огнестойкое покрытие содержит воду, поэтому его следует тщательно высушить. Если по тем или иным причинам произойдет резкий сброс давления, то оставшаяся вода начнет быстро испаряться, что неминуемо приведет к разрушению огнеупорного покрытия печи. На заводе Fafen-SE Petroleo Brasileiro компании Kellogg подвергнутый обработке газ обычно охлаждается в паре бойлеров с вертикальной байонетной трубой, заключенной в водяную рубашку, с внутренней огнеупорной облицовкой. При нормальных условиях работы не было никаких проблем с этим покрытием, но во время технического обслуживания часть облицовки деформировалась, и ее пришлось заменить на новую. Этот ремонт занял много времени. Но во время следующего цикла работы установки, вода, содержащаяся во вновь уложенном облицовочном материале, начала испаряться, что привело к его разрушению. Дальнейшее безопасное функционирование было возможно при повышении циркуляции воды в охлаждающем контуре. Таким образом, удалось снизить температуру незащищенных облицовочным материалом частей до 118°C, хотя температура при неповрежденном огнеупоре ниже 100°C. Этот режим функционирования позволил продлить время эксплуатации установки до очередного ремонта. Компания приобрела еще одну подобную установку, чтобы можно было производить ремонтные работы без остановки всего производства. Горелки Одна из важных задач при разработке и эксплуатации печей для риформинга – это добиться равномерных температурных условий для всех труб. Данное требование актуально также и для пламени на всех горелках, не только при нормальных рабочих условиях, но также и при всех экстренных условиях, в которых может работать печь. Если поток топочного газа будет неправильно отрегулирован, то может снизиться эффективность процесса риформинга и даже разрушение труб печи. Большие печи для риформинга являются главным источником оксидов азота (NOx), которые образуются при взаимодействии кислорода и азота воздуха в самой высокотемпературной зоне пламени. Во многих странах мира приняты специальные инструкции по максимально допустимым выбросам оксидов азота, и даже в тех странах, где такие ограничения не наложены, добросовестные промышленники пользуются специальными горелками, различные модели которых представлены на рынке. Их работа основана на принципе постепенного сгорания для предотвращения возникновения высокотемпературных зон пламени и/или создании мягких условий на периферии пламени, что препятствует образованию NOx или даже разрушает уже образовавшиеся молекулы NOx. Компании Air Products и John Zink Co. сообщили об успешных испытаниях собственной модели горелки (LSV™) в процессе парового риформинга на заводе по производству водорода West-lake компании Air Products, расположенного в северной части Мексиканского залива США, который поставляет водород целому ряду заказчиков через распределительную магистральную линию. Печь с нижним подогревом снабжена 126 горелками, расположенными в 9 рядов, и 368 трубами в 8 рядов. Она топится смесью газов поступающих с нефтеперерабатывающего завода и газом, прошедшим систему очистки. Эта печь функционирует с апреля 2004 г. В отличие от большинства горелок, использующихся для снижения образования NOx, в процессе изготовления которых применяют металлические или керамические стабилизаторы пламени, горелка LSV™ (рис. 2.) динамично стабилизирует пламя посредством создания бурного вихревого потока топливного газа и воздуха, необходимого для поддержания процесса горения. Очищенный газ после подается через форсунки расположенные вокруг основного пламени на уровне внешней поверхности огнеупора.
Рис. 2. Устройство горелки LSV™ (Air Products). При первом запуске установки риформинга циркуляция газа была неравномерной, из-за чего некоторые горелки функционировали при значительно более высокой температуре, чем другие; также наибольшая температура пламени в два раза превышала расчетную. Попытки группы специалистов настроить отдельные горелки потерпели неудачу. С помощью тестов проведенных при использовании впрыскивания гидрокарбоната натрия была обнаружена нежелательная циркуляция газа от основания печи к вершине. Комплексное исследование, основанное на экспериментах и моделировании, показало, что пламя каждой отдельной горелки было слишком широким, и это приводило к их интерференции. Был принят ряд мер, включающий доработку наконечника сопла, изменение угла впрыскивания обоих типов газа, для того чтобы разбавить олефины и более тяжелые углеводороды в газе, поступающем с нефтеперерабатывающего завода. Эффект был поразителен. До проведения доработки разница температур между самыми горячими и самыми холодными трубами достигала 111°C, после модификации разница составляла всего 44°C – это намного ниже показателя 100°C, который является обычным для промышленности. Без печи? Идея проведение процесса первичного риформинга в теплообменнике за чет высокой температуры газа процесса вовсе не нова. Компания, которая раньше называлась ICI (сейчас Terra), была первой организацией применившей подобный процесс на заводе по производству аммиака в Великобритании в 80-х годах прошлого века, но сама идея возникла намного раньше. Несмотря на очевидные преимущества, особенно маленькую площадь основания по сравнению с обычной печью для риформинга, развитие этой технологии шло постепенно, по крайней мере, в аммиачной промышленности. Имелись некоторые технические проблемы с металлическим напылением в первых установках. Неотъемлемым минусом этого автотермического риформинга является то, что при работе с количеством воздуха, необходимым для получения синтез-газа, содержащего водород и азот в стехиометрическом отношении 3:1, он не производит достаточного количества теплоты для протекания первичной реакции риформинга на том уровне, при котором содержание метана в технологическом газе достаточно для осуществления вторичного риформинга. Это означает, что необходимо, чтобы установка вторичного риформинга функционировала с большим количеством воздуха, и затем нужно удалять газообразный азот из синтез-газа, или добавлять дополнительные порции кислорода в технологический газ во время проведения процесса вторичного риформинга. Имеются различные альтернативные пути, когда теплообменный риформинг можно использовать вместе с обычной печью для риформинга в качестве дополнения, для повышения производительности процесса не прибегая к дорогостоящим модификациям печи. Также хорошим способом является использование тепла, выделяющегося в процессах связанных с синтез-газом. Примером применения такого подхода является большой комплекс Sasol в Южной Африке, производящий синтетическое топливо из угля. Он включает в себя шестнадцать автотермических установок риформинга (autothermal reformer – ATR), которые преобразовывают газ, содержащий метан, полученный методом газификации угля. Этот завод – место первого коммерческого применения процесса теплообменного риформинга (high-temperature Exchange Reformer – HTER) компании Haldor Topsǿe. HTER был запущен в эксплуатацию параллельно с одним из ATR (рис. 3.), он обогревается выходящим из ATR технологическим газом. Установки автотермического риформинга были частью завода, они производили технологический газ слишком высокой температуры, охлаждающие установки не справлялись, и требовалось дополнительное охлаждение. Использование HTER не только снизило необходимость дополнительного охлаждения, но и повысило производительность на 33%, снизило потребление кислорода на 20%, улучшило соотношение компонентов синтез-газа, что важно для синтеза легких углеводородов в процессе Фишера-Тропша, и понизило выработку пара на 45%, снизив необходимость его отвода.
Рис. 3. Параллельное функционирование процесса теплообменного риформинга и автотермической установки риформинга. В будущем ожидается, что комбинации ATR/HTER достигнет двухлетней неприрывной работы, как и автотермические установки риформинга. На установке Sasol преобразованный газ из HTER и технологический газ автотермического риформинга, используемый в качестве обогревающей среды смешиваются перед охлаждением. На аммиачном заводе, где изменение количества метана необходимо уменьшить, можно охлаждать отдельно два потока газа и потом смешивать их. Сторонники технологии Topsǿe, использующие HTER или их модифицированные модели на заводах по производству аммиака, утверждают, что мощность производства аммиака возрастает на 25%; или позволяет уменьшить размер первичной печи для риформинга. Выход пара из охлаждающего контура процесса риформинга уменьшился на 10%, хотя общее образование пара на всем заводе в целом (включая цикл синтеза) изменилось незначительно. |