Основные преимущества данной системы заключаются в следующем: • сведение к минимуму энергопотребления холодильным компрессором, гак как синтез-газ может направляться непосредственно в колонну синтеза; • сведение к минимуму энергопотребления циркулятором, так как температура на всасывающей линии становится очень низкой; • получение выигрыша в давлении синтез-газа для выделения аммиака. Конвертор синтеза аммиака (рис 4) также базируется на технологии аксиально-радиального распределения потока Казале. Степень конверсии за проход, таким образом, максимально увеличивается, при этом минимизируется энергопотребление к копире синтеза и размер его оборудования. Важной чертой в проектировании контура синтеза аммиака является современная конструкция котла-утилизатора фирмы «Казале» после колонны синтеза. Котелутилизатор Казале пред¬ставляет собой теплообменник с U-образными трубками, в котором кипит вода со стороны трубного пространства, а со стороны межтрубного пространства проходит технологический газ. Корпус высокого давления охлаждается более холодным потоком газа на выходе. Единственные ферритные части, которые находятся в контакте с го¬рячим газом, — трубы, охлаждающиеся кипящей водой. С, такой специальной конструкцией становится возможным избежать риска нитрирования. Стандартная технология производства аммиака Казале имеет высокоэффективные характеристики: • соотношение пар/углерод (относится только к потоку ПГ): от 2.9 до 1; • остаточная концентрация СО с НТК: менее 0,3 об. % (в пересчете на сухой); • СО2 из абсорбера: менее 300 об. ррm; • давление в контуре синтеза аммиака: 140-160 бар; • степень конверсии аммиака: около 20%. 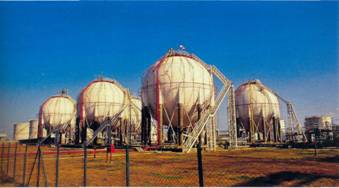
А также очень низкие показатели энергопотребления (оцениваемые как сырьевые потоки + топливо + импорт пара от пускового котла и экспорт пара на агрегат карбамида): около 6,7 Гкал/МТ аммиака. Высокая эффективность стандартной технологии производства аммиака Казале делает возможным при данной мощности уменьшить размеры оборудования и, следовательно, сократить инвестиционные затраты на постройку завода по сравнению с другими технологиями. Стандартная технология производства аммиака Казале разработана таким способом, чтобы свести к минимуму влияние на окружающую среду. Фактически единственными жидкими стоками являются компоненты продувки котла и конденсат межступенчатых холодильников компрессора. Компоненты продувки котла после вскипания и охлаждения используются как подпиточная вода для пополнения ВОЦ. То же самое справедливо и для конденсата межступенчатых холо¬дильников компрессора, который возвращается в коллектор оборотной воды. Единственным газообразным выбросом является отходящий газ из первичного риформинга, содержащий 110 мг/нм3 NOx. Га-рантийный показатель по NOx составляет величину менее требуемой Евросоюзом для новых агрегатов {140 мг/нм.куб., рассчитанный при 3%, избытка кислорода). Технология MEGAMMONIA Технология MEGAMMONIA® разработана Казале вместе с компанией Lurgi для проектирования агрегатов аммиака на природном газе в одну нитку с очень большой мощностью. Основная концепция технологии MEGAMMONIA заключается в использовании автотермического риформинга для производства синтез-газа при более высоком давле-нии по сравнению со стандартным процессом, использовании технологии очистки от диоксида углерода, основанной на физической абсорбции CO2, которая более эффективна при повышенном давлении по сравнению со стандартными химическими процессами, а также в высокоэффективной конструкции конверторов СО и конверторов синтеза аммиака, что позволяет в комбинации с узлом промывки азотом сохранить размеры конверторов СО и колонн синтеза аммиака, равно как и всего контура синтеза в конструкционных рамках даже при очень высокой и производительности.
|