При сборе токсичных материалов (некондиционных пестицидов, вредных химических веществ) контейнеры выполняются из стали с антикор-розионным покрытием внутренней и наружной поверхностей, а для радиоактивных сыпучих отходов могут применяются контейнеры из плотного бетона с радиационно-защитным заполнителем. После заполнения таких контейнеров, они отсоединяются от воздуховодов и направляются в специальные автоклавы для термической обработки собранного материала в открытом виде при температуре 150-1800С и давлении насыщенного пара 1Мпа. При этом не происходит уноса летучих компонентов, обладающих токсичными или радиоактивными свойствами, обеспечивается стабилизация органических составляющих и полная стерилизация (уничтожение микроорганизмов), а также осуществляется гидротермальный синтез силикатов и алюмоси-ликатов металлов. После термической обработки контейнеры герметизируются заглушками или бетонным раствором (в случае бетонных контейнеров) и отправляются в хранилища. При этом не происходит разложения органики, отсутствует выделение газов, которые могут привести к повышению давления внутри контейнера и его разгерметизации. Загрязненный фильтр тонкой очистки также утилизируется вместе с контейнером. Установка может быть переоборудована для первичной переработки распадающихся металлургических шлаков воздушно-сухим способом В настоящее время на большинстве металлургических предприятий используется мокрая технология первичной переработки шлаков, в том числе и на ОАО "Оскольский электрометаллургический комбинат", которая которая сопровождается выбросами пара и образующихся сернистых соединений. Так количество образующегося сероводорода при мокрой переработке шлака в 13 раз больше, чем при сухой технологии переработки [3]. 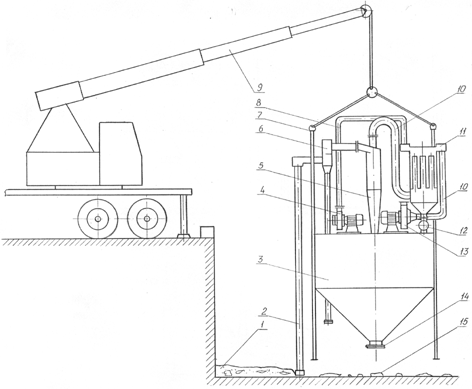
Рис. 2. Схема полупромышленной установки 1 — шлаковый порошок; 2 — заборный воздуховод; 3 — бункер готового про-дукта; 4 — нагнетательный вентилятор; 5 — циклон; 6 — пневмоклассификатор; 7 —устройство для стыковки с подъемным краном; 8 — нагнетательный воздуховод; 9 —автокран; 10 — вытяжные воздуховоды; 11 — рукавный фильтр, 12 — шлюзовой затвор; 13 — вытяжной вентилятор; 14 — устройство для выгрузки готовой продукции; 15 — оставшиеся скардовины металла. При воздушно-сухой технологии шлаковый расплав сливают на дно шлаковой траншеи слоем высотой 0,2 м, где происходит его естественное охлаждение, сопровождающиеся саморассыпанием застывшего шлакового монолита в тонкодисперсный порошок. После этого обеспечивается возможность его сбора и сепарации [4,5]. Принципиальная возможность осуществления подобной технологии отрабатывалась на полупромышленной установке (рис. 2) производительностью 3 т/час. Шлаковый порошок собирали, перемещая заборное сопло, установленное на воздуховоде 2 и всю установку над слоем остывшего и распавшегося шлака 1 с помощью автомобильного подъемного крана 9. При этом шлаковый порошок попадал в пневмоклассификатор 6, где отделялись металлические включения и крупная фракция нераспавшегося шлака. Тонкодисперсная готовая шлаковая продукция осаждалась циклоном в бункере, разгрузка которого производилась периодически через шиберный затвор. Для создания разрежения в системе служил вентилятор 13. Обратная продувка фильтра осуществлялась нагнетательным вентилятором 4. Установка позволяла оставлять крупные металлические скардовины на дне шлаковой траншеи а мелкодисперсные частицы металла от-делялись в пневмоклассификаторе. Выделенный металл собирали с помощью магнитной шайбы и отправляли на переплавку. |