Прогресс современной деревообрабатывающей промышленности во многом обусловлен использованием недорогих связующих на основе формальдегида. Они на порядок дешевле альтернативных смол (эмульсии ПВА, эпоксидных) и при этом обеспечивают приемлемые показатели прочности. На сегодняшний день в мире сложились две системы обеспечения потребителей смолами: централизованной поставки смол предприятиями химической промышленности и приготовления смол самими деревообрабатывающими производствами. В России и странах СНГ используются обе системы. При этом крупные специализированные производители смол, которые также часто являются и поставщиками соответствующего исходного сырья, с целью расширения сбыта готовой продукции завышают цены на сырье и снижают цены на готовые смолы. Одновременно на малых производителей оказывается давление и со стороны природоохранных органов, контролирующих выбросы вредных компонентов в воздух и их содержание в сточных водах. Тем не менее отсутствие должного внимания со стороны крупных фирм-поставщиков к качеству производимых ими смол вынуждает малые предприятия всеми силами пытаться сохранить свои смоляные цехи. Типовой цех смол деревообрабатывающего предприятия выпускает карбамидоформальдегидную смолу для смежного с ним производства древесностружечных плит или фанеры. Основные виды сырья: 37%-ный формалин (раствор формальдегида в водно-метанольной среде), карбамид, а также хлористый аммоний (катализатор) и щелочь NaOH. Смолу изготовляют периодическим способом в реакторах (оборудованных мешалкой и рубашкой), где по определенному кислотно-температурному режиму проводят процесс поликонденсации исходных реагентов, после чего удаляют надсмольные воды (на стадии сушки) и осуществляют доконденсацию не прореагировавшего формальдегида карбамидом. Недостатки такой технологии хорошо известны: наличие сточных вод, потери формалина и метанола, значительная продолжительность процесса варки и сушки, большие расходы пара и электроэнергии, малый выход товарной смолы. Помимо этого, при приеме и хранении формалина в зимний период требуется постоянный подогрев емкостей паром. Часть формалина улетучивается, а еще большая его часть остается в виде параформа в цистернах и осаждается в емкостях. При изготовлении стандартной смолы КФ-МТ-15 образуется приблизительно 300 кг надсмольной воды на 1 т выработанной смолы. Типовое производство ДСП мощностью 100 тыс.м3 потребляет около 12 тыс.т смолы в год. Следовательно, предприятию ежегодно приходится сбрасывать в очистные сооружения более 3 тыс.т над- смольных вод, содержащих около 40 т формальдегида и свыше 300 т метанола. Таким образом, нагрузка на окружающую среду является неприемлемой. Исследовательские институты и отраслевые лаборатории уделяли большое внимание решению данной проблемы. Предлагались различные варианты утилизации надсмольных вод, в том числе их подача в сушилки, сжигание, связывание свободного формальдегида аммиаком или карбамидом, возвращение отходов изготовителю сырья на переработку и др. Ни один из перечисленных методов не нашел широкогоприменения из-за их низкой эффективности. Представляет интерес разработанная ЦНИИ фанеры смола КФ-НФП, которую производят без стадии сушки. Некоторые предприятия, особенно расположенные в черте города, были вынуждены перейти к использованию смолы КФ-НФП с целью решения проблемы стоков. Но при этом возникает другая проблема - повышенных объемов выброса вредных веществ, выделяющихся при прессовании. Ранее упомянутый типовой завод ДСП при использовании смолы КФ-НФП помимо формальдегида выбрасывает в атмосферу около 1 т метанола в день. При этом нарушаются не только общие экологические нормы, но и санитарно-гигиенические требования по предельно допустимым концентрациям (ПДК) вредных веществ в воздухе рабочей зоны. Уже многие годы на Западе широко применяют безотходную, экологически чистую технологию производства смол на основе формалинового концентрата, или форконцентрата - концентрированного раствора формальдегида, стабилизированного карбамидом. Основные достоинства технологии производства смолы из форконцентрата: • Полное отсутствие сточных вод и других отходов производства. • Вдвое увеличивается производительность оборудования. • В 5-6 раз уменьшается потребление пара и электроэнергии. • На 30% сокращаются расходы на транспортировку сырья. Форконцентрат можно хранить бесконечно долго в широком интервале температур: его свойства при этом не ухудшаются. Известны различные способы приготовления форконцентрата, но основными являются периодический (Batch Process) и непрерывный (Metal Oxide Process).При периодическом способе форконцентрат изготовляют на крупных химических предприятиях по упрощенной технологии варки карбамидоформальдегидной смолы. По заданному кислотно-температурному режиму в реакторе проводят процесс конденсации формалина и карбамида, а затем осуществляют сушку полученного конденсата до достижения заданного содержания в нем сухого вещества. Получаемый безметанольный продукт содержит в среднем 42-46% формальдегида и 23-27% карбамида, его можно хранить не менее полугода в широком интервале температур. Надсмольные воды, которые образуются в количестве 500-550 кг на 1 т форконцентрата, содержат в среднем по 6-8% формальдегида и метанола – эти воды используют в производстве формалина. Из полученного таким способом форконцентрата можно изготовлять многие марки смол без стадии сушки (кроме смол с высоким мольным отношением типа М-70). В производственных условиях описанный процесс был отработан в 1997 г. в Прибалтике. Из форконцентрата, изготовленного в Эстонии, литовское опытно-промышленное предприятие UAB “VIJOKA” произвело более 6 тыс.т смолы класса (по токсичности) Е1 для деревообрабатывающих фирм региона. На российском рынке также можно приобрести фор-концентраты, изготовленные по периодическому способу: ККФ-1, ККФ-2. Но из-за высоких цен на эти продукты и нестабильности их качества переход на безотходную технологию производства смол часто оказьпйется экономически нецелесообразным. Периодический способ приготовления форконцентрата не получил большого распространения - прежде всего из-за высокой себестоимости продукта. На Западе наиболее широко применяют непрерывный способ, основанный на разработанной в начале 50-х годов фирмой “Reichold Chemicals” (США) технологии получения формальдегида на металло-оксидном катализаторе в реакторах трубчатого типа. Его отличительная черта - полная конверсия метанола при прохождении через слой катализатора, что значительно повышает эффективность производства (в процессах, используемых в СНГ, в основном применяют серебряный катализатор, обеспечивающий только частичную конверсию метанола; при таких процессах требуется дополнительная стадия - отделения метанола от формалина и возвращения отделенного метанола в производство). Металло-оксидный процесс позволяет получать формалин концентрацией до 57%, а при использовании в качестве абсорбента раствора карбамида получается форконцентрат, содержащий 60% формальдегида и 25% карбамида. Расчет показывает, что себестоимость “металло-оксидного” форконцентрата составляет менее половины себестоимости концентрата, получаемого периодическим способом. Необходимо отметить, что уже более 20 лет в России и Украине - на двух небольших заводах по устаревшей технологии итальянской фирмы “Mont Edison” – производят форконцентрат с использованием металло-оксидного катализатора. Этот продукт в основном применяют на предприятиях азотной промышленности в качестве добавки к мочевине - для предотвращения ее слеживания (комкования).Он характеризуется высоким содержанием буферных солей и уроновых колец и поэтому малопригоден для применения в производстве быстро отверждаемых карбамидных смол класса Е1. В настоящее время некоторые предприятия азотной промышленности рассматривают возможность строительства современного (с использованием непрерывной технологии) производства форконцентрата. Однако стоимость типового производства мощностью 30 тыс. т/год (в пересчете на 37%-ный формалин) составляет свыше 4 млн.долл. США. Срок окупаемости такого строительства составит много лет. Таким образом, сегодня на российском рынке нет форконцентрата по такой цене, которая позволила бы цехам мол деревообрабатывающей промышленности совершить переход на безотходную технологию производства смол без значительного возрастания их себестоимости. Санкт-Петербургское российско-американское ЗАО “Безопасные технологии” предлагает принципиально новое решение проблемы перевода деревообрабатывающей промышленности на безотходную технологию варки смол - модульные установки по производству форконцентрата. Выпускаемые типовые установки мощностью 6 и 9 тыс.т форконцентрата в год (в пересчете на 37%-ный формалин) способны полностью обеспечить им крупное производство фанеры или ДСП. Оптимальное аппаратурное оформление технологического процесса и оригинальные технические решения компоновки оборудования позволили создать компактный и надежный модуль, удобный в эксплуатации. Модуль поставляют заказчику железнодорожным или автомобильным транспортом в собранном виде. Модульные установки размещают рядом с цехом смол на открытой площадке 3х3 м, подключают к источнику электроэнергии -и уже через несколько дней после доставки они готовы к работе. Технологический процесс производства форконцентрата на модульных установках основан на использовании новейших мировых достижений в области металло-оксидного катализа и межфазной абсорбции. Основное сырье для производства форконцентрата – метанол (метиловый спирт). Его поставляют в железнодорожных цистернах и хранят в специально оборудованных емкостях. В технологическом процессе синтеза форконцентрата метанол, проходя через испаритель, смешивается с потоком воздуха, эта смесь подается в реактор. В процессе окисления метанола кислородом воздуха - на железо-молибденовом оксидном катализаторе - происходит образование газообразного формальдегида. Насыщенный формальдегидом воздух охлаждается в рекуператоре, после чего эту смесь подают в абсорбционную колонну, где она поглощается раствором карбамида с образованием форконцентрата. Выходящий из колонны воздух, содержащий следы формальдегида, метанола и побочных продуктов реакции, перед выбросом в атмосферу подают в дожигателъ (каталитический конвертер), где происходит его полная очистка от загрязняющих веществ. Процесс полностью автоматизирован и управляется одним оператором. При реакции окисления метанола выделяется большое количество тепла, утилизируемое в виде пара. Получаемый пар давлением 10 атм можно использовать при синтезе смол, для обогрева помещений и емкостей, пропарочных бассейнов или подавать в общезаводской коллектор. 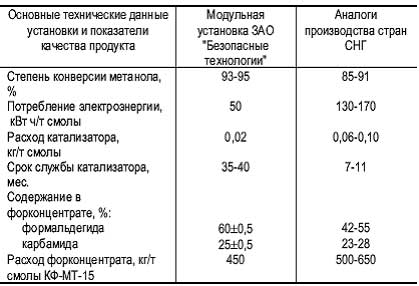 В табл. 1 приведены основные технические данные модульной установки, разработанной ЗАО “Безопасные технологии”, и ее аналогов, производимых в странах СНГ, а также показатели качества получаемого продукта. Синтез смол проводят периодическим способом на стандартном оборудовании. Основные отличия варки смолы на основе форконцентрата - отсутствие стадии сушки и проведение стадии поликонденсации (окисления) по более мягкому кислотно-щелочному режиму. Для достижения необходимого сухого остатка в реактор на стадии загрузки компонентов вводят расчетное количество воды, в том числе и при варке высокомольных смол типа М-70. В табл. 2 показаны величины удельного расхода компонентов для двух способов варки смолы КФ-МТ-15 (содержание сухого остатка в смоле - 67%, мольное отношение Ф/К = 1,10): из форконцентрата и формалина, а также величина показателя отгонки (удаления) воды на стадии сушки смолы. В деревообрабатывающих производствах образуется значительное количество технологических стоков (при мойке оборудования, помещений и др.). Стандартной практикой является их утилизация (с использованием очистных сооружений) или сжигание. Эти методы обычно сопряжены с большими расходами как на строительство и обслуживание очистных сооружений, так и на штрафы за превышение максимально допустимых экологических показателей. При наличии собственного производства форконцентрата упомянутые сточные воды используются при приготовлении раствора карбамида и добавляются при варке смолы, что на порядок повышает экологичность деревообрабатывающего производства. Небольшие (по сравнению с варкой смолы из формалина или привозного форконцентрата) величины удельного расхода компонентов при варке смол с использованием форконцентрата, получаемого на модульной установке, позволяют изготовить из 1 т форконцентрата UF-85 свыше 2 т смолы (см. табл. 2), себестоимость которой составит менее 1400 руб./т (что обусловлено низкой себестоимостью форконцентрата, получаемого на модульных установках). При этом себестоимость 1 т аналогичной смолы, изготовленной из привозного концентрата или формалина, - не менее 2600 руб. (при ценах на сырье по состоянию на 31.04.2000.). Таким образом, экономический эффект от внедрения модульной установки мощностью 6 тыс.т форконцентрата в год (в пересчете на 37%-ный формалин) составит около 10 млн.руб. С использованием форконцентрата синтез смол можно проводить как по традиционной технологии (без ухудшения качества смол), так и по специальной технологии, позволяющей полностью использовать преимущества форконцентрата и получать низкотоксичные смолы с пониженными расходными нормами. Применение специальных компьютерных программ облегчает расчет оптимальных величин удельного расхода компонентов на каждую варку (в частности, снижает продолжительность анализа исходных продуктов) и практически исключает зависимость качества смолы от качества сырья. В заключение отметим, что карбамидоформальдегидные смолы широко используются в деревообрабатывающей промышленности уже более 50 лет и их производство неуклонно растет в США, Канаде, Европе и особенно в странах Юго-Восточной Азии. Изготовление высококачественного форконцентрата UF-85 непосредственно на деревообрабатывающих предприятиях с помощью компактных модульных установок освобождает эти предприятия от “формалиновой” зависимости и открывает широкие возможности для обеспечения ими технико- экономического прогресса своих производств. Список литературы 1. Модульные установки безопасных технологий для деревообрабатывающих производств: [Просп.] / Компания CAL Polymers Inc., США, 2000. 2. ГОСТ 14231-88. Смолы карбамидоформальдегидные. Технические условия. - Введ. 01.07.89 до 01.07.94. 3. Теп-у Sellers. Публикации в журнале “Wood Technology, США, 1991-1999. 4. Panel products: applications and production trends, 2nd Edition. A special report from Wood Technology Magazine. США, 1996. 5. Материалы 5-й конф. PETE, Атланта, США. - 1998. 6. Прусак А.П. Перспективы производства малотоксичных смол с использованием карбамидоформальдегидных концентратов // Тез. докл. науч.-практ. семинара “Состояние и перспективы развития производства древесных плит” 15-16 марта 2000 г. - Балабаново, 2000. С. 24-27. С.И. Стомпель, кандидат химических наук, ЗАО “Безопасные технологии”, Д.А. Щедро, кандидат технических наук, “ЦНИИФ”
|