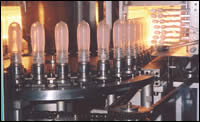
Container Corp. of Canada использует и продает установки для формования с раздувом и вытяжкой и пресс-формы своей собственной конструкции; все это производится в Китае. Во-вторых, источником потенциала является превосходная термостойкость полипропилена, которая позволяет выдерживать горячую расфасовку при температуре до 2050 F. Бутылки из ПЭТ могут подвергаться горячей расфасовке только при температуре до 160-1700 F без отверждения при нагревании. Здесь также нужны вакуумные панели для предотвращения оседания, когда температура горячей расфасовки превышает 1800 F. Для большинства применений ПЭТ с горячей расфасовкой требуется отверждение при нагревании, что увеличивает затраты на 20% из-за того, что нужны более толстые стенки и более медленное производство. Для бутылок из однослойного полипропилена не требуется отверждения при нагревании, и они могут использоваться на многих рынках с горячей расфасовкой пищевых продуктов, особенно, тогда, когда заполнение осуществляется при наибольших температурах горячей фасовки (от 1800 до 2050 F). Это открывает перспективы для барьерной и не барьерной упаковки соков, джемов, желе, маринадов, сальсы, а также соусов на основе томата. Имеется также и третья группа потенциальных рынков, где для использования бутылок из полипропилена и ПЭТ понадобится дополнительный газовый барьер. До тех пор, пока стоимость барьерного материала будет примерно одинакова для каждого из типов контейнеров, бутылки из барьерного ПОЛИПРОПИЛЕНА будут предпочтительнее в качестве замены стекла, за счет своего внутреннего ценового преимущества. Три дороги к производству Для преодоления прежних недостатков полипропилена, связанных с пропускной способностью, компании Bekum и CCC (которые проектируют и реализуют свои собственные установки) модифицировали оборудование для ПЭТ под полипропилена. Они рассматривают поточные линейные системы формования с раздувом и вытяжкой с повторным нагревом с количеством гнезд до восьми как рентабельные установки для производства средних по объему серий применений из полипропилена. “По умолчанию мы поставляет оборудование для производства бутылок из полипропилена,” – говорит Готтлиб, который рассказывает, что первоначально попытки CCC формовать бутылки из полипропилена, которые предпринимались шесть или семь лет назад, были отложены из-за отсутствия соответствующих установок и инструментария из коммерческих источников. В результате, CCC сама спроектировала патентованную поточную линю установок для SBM с повторным нагревом для работы с полипропилена. Установки компании, которые называются EnviroClear (и на которых можно работать также и с ПЭТ) выполнены партнером из Китая, и предлагаются с числом гнезд от двух до восьми. Стоимость с доставкой установки с четырьмя гнездами в США составляет $250,000. Установка производит 900 бутылок в час на одно гнездо, но для следующего поколения установок ожидается модернизация, которая даст производительность до 1100 бутылок в час. Вскоре будет представлена на рынок модель для изготовления банок с широким горлом. CCC предлагает произведенные в Китае преформы и инструментарий для SBM, имеющий до 32 гнезд, по ценам на 40% - 80% ниже, произведенных в стране. 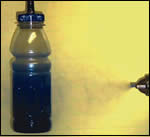
Барьерные покрытия Bairocade для бутылок из ПЭТ компании PPG в настоящее время адаптируются для использования с полипропилена. CCC говорит, что ключевое значение имеет оптимальная конструкция преформы. Её собственные преформы рассчитаны на растяжение на 50% больше, чем при работе с ПЭТ для того, чтобы повысить прозрачность. Недавно CCC начала поставлять преформы и оказывать услуги по созданию экспериментальных моделей бутылок. К числу применений полипропилена, которые компания ССС намерена представить в течение последующих месяцев, относятся: банки с широким горлом для салатных заправок, маринадов, и порошков, а также выдавливаемые контейнеры для шампуней, полоскателей для рта и лекарственных препаратов. Для увеличения прочности верхней и ободковой частей, ССС вводит азот в пространство над веществом заполнения после того, как фасовка завершится. Компания Bekum America оснащает свои установки для формования с раздувом и вытяжкой с повторным нагревом (такие как двухгнездные RBU-225) так, чтобы они могли переходить при производстве бутылок с работы на ПЭТ на работу с PP. Несколько лет тому назад, Bekum спроектировала свою первую полностью электрифицированную установку для SBM с повторным нагревом специально для работы с PP. У этой установки на шесть гнезд SB-6 номинальная мощность 7200 бутылок в час, что всего на 15% медленнее, чем при работе с ПЭТ при том же количестве гнезд. За другой подход к производству ратует Скотт Стил, вице-президент компании Plastic Technologies Inc. (PTI), которая проектирует и создает экспериментальные модели преформ из ПЭТ, инструменты и бутылки. Он утверждает, что самым лучшим способом получить преимущества от производства бутылок из полипропилена является их изготовление на высокопроизводительных ротационных установках для SBM с повторным нагреванием с постоянной производительностью в 1000 бутылок на гнездо в час. PTI имеет смоделированное на компьютере производство 24-граммовых бутылок из полипропилена на установке компании Sidel с такой скоростью, и в компании предсказывают, что средняя цена за единицу будет на 10¢ ниже, чем за бутылку из ПЭТ. Но при обычных скоростях производства бутылок из полипропилена (600 бутылок на гнездо в час), прогнозируемая цена за единицу будет больше, чем для бутылки из ПЭТ. По словам Стила, для оптимизации производительности бутылок из полипропилена необходимой строгий технологический контроль. Если выдувать бутылки при температуре слегка ниже температурного диапазона полипропилена, их нельзя будет правильно растягивать, из-за этого возникнет плохая прозрачность или разрыв преформ. Если выдувать бутылки из полипропилена при температуре, превышающей температурное окно, образуются корпуса, горлышки и основания с вуалью, а также создается плохое распределение материала в стенках и липкость бутылок, которое может повлечь за собой нарушение технологического процесса ниже по цепочке. По словам Стила, скорость производства 1000 бутылок на гнездо в час является экономической необходимостью. Для того, чтобы добиться такой скорости, PTI использует лабораторные исследования, а также свое программное обеспечение Virtual Prototyping для прогнозирования воздействия “быстро нагревающих” добавок, которые ускоряют поглощение тепла преформами из ПЭТ. PTI также осуществляет моделирование методик охлаждения воздуха и воды, которые в настоящее время используются для ускорения обработки бутылки из ПЭТ. Компания PTI установила, что эти технологии можно успешно переносить на производство бутылок из полипропилена, что сделает возможным достижение целевой скорости в техническом и экономическом аспектах. PPI работала с добавками быстрого нагревания в маточным смесях от компании Colormatrix. По словам коммерческого директора Colormatrix Дэвида Макбрайда, те же самые добавки, которые ускоряют нагревание преформ из ПЭТ так же эффективны и при изготовлении бутылок из полипропилена. ExxonMobil также осуществляла разработку экспериментальной модели и компьютерное моделирование производства бутылок из полипропилена на ротационных системах для SBM с повторным нагревом. В компании использовали модифицированные установки компании Sidel, специальную конструкцию преформ, а также полипропиленовую смолу со специально адаптированными свойствами, PP9505E1. Этот материал со скоростью течения расплава 30 обладает дымчатостью в 6% при 1 мм в толщину и модулем упругости при изгибе 166,000 ф. на кв. дюйм. У бутылок из полипропилена дымчатость составляет менее 2%.
|