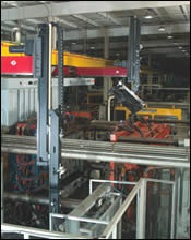
В области формования с множеством литьевых отверстий конструкционных пенопластов низкого давления по-прежнему распространена практика ручного извлечения деталей из пресс-формы. Но эта ситуация быстро меняется по мере того, как детали из пенопласта становятся все больше и все тяжелее. “На протяжении последних шести лет автоматизация была редкостью на нашем предприятии. Но изменения в области физической размерности, массы и формы деталей требуют применения автоматизации для того, чтобы не допускать телесных повреждений операторов”, - говорит Стюарт Хейден, менеджер предприятия в Джорджтауне, Кентукки, принадлежащего Orbis Corp. До недавнего времени предприятие было частью компании Linpac Materials Handling, крупного поставщика устройств для погрузки/разгрузки пластмассовых утилизированных сырьевых материалов, которая была приобретена Orbis. “Несколько лет тому назад наши самые тяжелые детали весили в среднем 70 фунтов, но сейчас чаще всего производят детали с массой 120 фунтов”, - поясняет Хэйден. “Также в настоящее время мы производим больше деталей, которые весят 140 или даже 150 фунтов”. 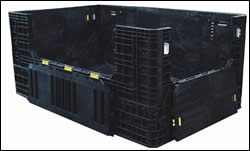 Формованные детали из конструкционных пенопластов с большей массой, такие как ящики из HDPE с компонентами весом до 150 фунтов, заставляют предприятия переходить на автоматизированную погрузку/разгрузку деталей. При большом количестве тяжелых деталей, которые выходят из установки после каждого цикла, можно обойтись погрузкой/разгрузкой сложных деталей с помощью ручного труда. Но все становится намного сложнее, когда в формы нужно также помещать вставки для каждого последующего цикла. “Ручные операции не только создают эргономические проблемы и проблемы в области обеспечения безопасности для работника, они могут также влиять на продолжительность цикла обработки детали”, - говорит Хейден. Пресс должен простаивать, пока рабочий не покинет участок формования, а из-за этого материал может дольше удерживаться в цилиндре, чем это необходимо. Количество деталей, формуемых одновременно, может даже сокращаться для того, чтобы ускорить ручное извлечение деталей. Пришествие автоматизации “Формовщики стремятся получить более стабильный производственный цикл, повысить производительность и оптимизировать каждый этап осуществляемых операций. Вот почему в области формования конструкционных пенопластов наблюдается устойчивая тенденция к внедрению автоматизации, особенно, на более крупных установках”, - говорит Эд Хьюнерберг, директор по формованию конструкционных пенопластов и промышленному выдувному формованию компании Uniloy Milacron, которая создала прессы, использующиеся на предприятиях Orbis. Хьюнерберг рассказывает, что компании, занимающиеся собственным формованием, которые работают на специально выделенных линиях для определенных продуктов, первыми начали использовать робототехнические устройства, особенно, по мере того, как детали у них начали становиться все тяжелее. Тем не менее, даже компании, осуществляющие формование по индивидуальным заказам на одной-двух установках, находят практические причины для того, чтобы рассмотреть вопрос об использовании робототехнических устройств. “У формовщика, работающего по индивидуальным заказам, как правило, эксплуатируются различные сочетания множеств пресс-форм на одной установке, гнезда для каждой серии устанавливаются в различное положение на установках с широкой плитой. У типичной 750-тонной установки SF с широкой плитой расстояние между поперечными планками 137 дюймов”, – говорит Хьюнерберг. Он также добавляет, что наличие робототехнического устройства позволяет формовщику создавать, сохранять и считывать программу, которая предназначена для того, чтобы доставать и подбирать детали, что позволяет сделать погрузку/разгрузку деталей более воспроизводимыми. 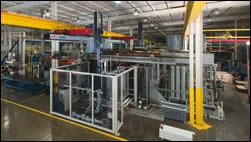 Два больших робототехнических устройства на одной балке позволяют Orbis оптимизировать работу на прессе, уменьшить продолжительность циклов, количество лома, а также продолжительность простоев, которые возникают из-за поломки деталей. Хьюнерберг говорит, что Uniloy разработала специальный разъем устройства связи с робототехническим устройством, который позволяет более эффективно осуществлять связь между роботом и прессом. “Еще несколько лет тому назад нельзя было и представить себе использования многоштырькового соединения для наших машин, а сейчас такое соединительное устройство установлено как стандартный элемент. Более половины всех прессов для конструкционных пенопластов, которые реализует Uniloy, подготавливается под использование средств автоматизации для извлечения деталей”, - говорит Хьюнерберг. Интерфейс настроен для конфигураций SPI или Euromap. Компания Linpac начала автоматизацию несколько лет тому назад с внедрения боковых робототехнических устройств. По словам Хейдена, боковые робототехнические устройства подходят для некоторых более простых применений, но более крупные детали лучше перемещать с использованием моделей с подвеской сверху. |